Crane Quality ensures Crane Safety
Overview of Crane Quality Control & Supervision in overhead crane, gantry crane, jib crane production. Check Now.Yuantai Better Crane's quality control system focuses on the control process, incorporating the crane quality control philosophy into design, manufacture, testing, and all other processing activities. Yuantai Better Crane uses advanced testing equipment to oversee each step of the crane manufacturing process and ensure the quality of every hoist and crane product it produces.
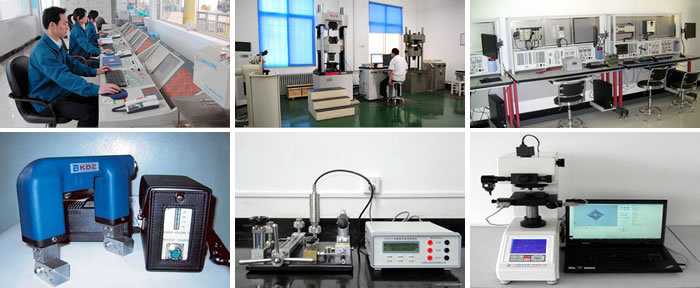
Testing equipment of Yuantai Better Crane
Yuantai Better Crane Quality control measures
Quality is the lifeblood of Yuantai Better Crane, and the pursuit of excellent hoist and crane quality is designed to meet customers' different material handling needs. Yuantai Better Crane uses the following crane inspection checklist and traditional quality assurance techniques to provide you with high-quality material handling equipment:
Crane quality control on steel structure
- The crane steel structure's quality is critical, and it will be tested for steel and welding quality. On the subject of steel quality. Before entering Yuantai Better Crane's store, all steel materials will be inspected by professional QC in terms of material, size, configuration, weight, and permissible variation. The national standards of GB/T 700-2006, GB/T 709-2006, GB/T3274-2007, and GB/T 1591-2008 are used to inspect Yuantai Better Crane.
- On crane welding quality. The welding technique specification and blueprint criteria apply to all weld groove form, size, and welding materials. By referring to the national standards GB/T 3323-2005, JB/T 10559-2006, and JB/T 6062-2007, the following tests are used to assure welding quality: appearance detection, nondestructive testing, radiographic testing, ultrasonic testing, penetration testing, magnetic particle testing, and so on.
Crane quality control on mechanism system
- On wheels. The wheels are guaranteed to be built of casting steel ZG340-640 or low alloy steel ZG-50iMn, with a hardening depth of 20mm. Casting steel ZG340-640 has a rolling surface hardness of 300-350HB, while ZG-50iMn has a rolling surface hardness of 420-480HB. Mechanical property, precision, and roughness are all monitored using the JB/T 6392-2008 national standard.
- On crane hooks, to be precise. The forging hooks will be inspected in accordance with GB/T10051-2010, which is categorized in terms of strength into M,P, S, T, and V. The top of the crane hook should be composed of DG20, DG20Mn, and DG34CrMo, and the shape of the crane hook should be DG20, DG20Mn, and DG34CrMo.
- On wire ropes. The wire ropes are crane-specific steel wire ropes that will be tested for technical requirements and mechanical properties in accordance with GB/T 20118-2006 and GB 8919-2006 standards.
Crane quality control on assembling
- On crane span. The stiffness and camber of the crane span must be inspected in accordance with national regulations, and the process inspection will be carried out using factory records as a guide.
- On painting. The painting surface must be shot peened to achieve grade Sa2 1/2, and the overall film thickness must be guaranteed to be around 75m105m. The adherence of the paint is checked according to GB/T 9286 class I.
- Loading testing on cranes. Crane bearing capacity and mechanism operation will be checked during the process, which will include static and dynamic loading tests.
Crane quality control and testing equipment
1) Radiographic Testing (RT). To test the discontinuity of materials and investigate the internal defect, X, Y, or neutron rays are used.
Radiographic Testing at Yuantai Crane Factory
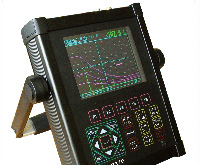
Ultrasonic Testing at Yuantai Crane Factory
2) Ultrasonic Testing (UT). Ultrasonic is a technique for detecting internal faults in metal materials such as pipe, plate, bar, and weld that is rapid, low-cost, and has a wide range of applications.
3) Penetration Testing (PT). Similar to ultrasonic testing, it is also used to discover interior faults in metal materials. Double testing ensures that the overhead lifting product is of the highest quality.
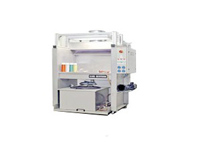
Penetration Testing at Yuantai Crane Factory
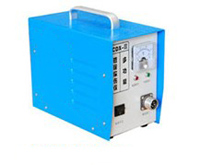
Magnetic Testing at Yuantai Crane Factory
4) Magnetic Testing (MT) is a type of testing that involves the use of magnets. To locate the discontinuity on the specimen surface and near surface, magnetic leakage and suitable tests are employed.
5) Coating evaluation. Coating thickness testers, adhesion testers, testers, and film girding instruments are used to assess coating quality in terms of film performance, mechanical properties (thickness, adhesion, gloss, etc.) and special properties (corrosion resistance, oil resistance, and acid resistance, for example).
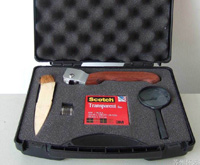
Coating evaluation at Yuantai Crane Factory
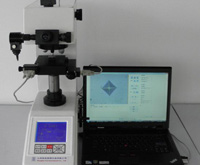
Testing the hardness of metals at Yuantai Crane Factory
Testing the hardness of metals. Static testing procedures such as HB, HRC, HV, and HL are routinely used to determine the resistance of metal materials.
Crane test and crane inspection for overhead crane commissioning and acceptance
Before being applied in to work, overhead cranes must be tested and certified qualified, as well as pass an acceptance inspection. Crane inspection and testing are required and vital for crane commissioning and acceptance, which is an essential technique for ensuring crane safety during operation and checking overhead crane manufacturing and installation quality.
In addition to crane commissioning and acceptance inspections, annual overhead crane inspections and loading tests are necessary. However, the crane test and crane inspection for overhead crane commission and acceptance will be detailed in the following sections.
Crane Inspection before Commissioning
Before commissioning a newly installed or overhauled overhead crane, we should assemble a team of skilled electricians, fitters, crane operators, and other technical personnel to thoroughly inspect the overhead crane. The following are the key contents of the crane inspection:
1) Before inspecting the overhead crane, turn off the power supply. Check and ensure the following in accordance with the crane drawings and technical requirements:
- All of the fasteners are tightened;
- The safety equipment and devices have been installed properly;
- The metal frame of the overhead crane is in good shape, and no deformation is detected.
- The wire rope on the pulley and drum is securely fastened.
2) Double-check that all rotating devices are properly placed and that they can revolve freely. Turn the wheel by hand to check the output shaft's movement and the revolving of the driving organization, ensuring that everything is in good working order and that nothing is stuck.
3) The overhead crane brake should be precise and consistent. Two brakes placed for the overhead crane's running mechanism should be consistent with each other.
4) All lubricating points should be lubricated with the needed lubricating oil according to the regulations and oil amount on reducer shall be within the prescribed scope.
5) Inspection of electrical equipment
- Using a megohmmeter, check the circuit system's insulation resistance.
- Ensure that all electrical equipment complies with the regulations.
- If the working line is correct, the controller is flexible and trustworthy in the situation of a disconnect power circuit.
- The electrical equipment should be in good working order, with special care paid to the electromagnet, limit switch, and emergency switch.
Crane Test Preparation before Commissioning
- Clean up the overhead crane test site and ensure sure no one who isn't supposed to be there is allowed in.
- Prepare a testing object that is 1.25 times the overhead crane's rated capacity. It is preferable to weigh it ahead of time.
- Using a steel wire rope or a belt to lift something.
- Steel line (Jean line), plumb, and measuring tool are some of the tools used to inspect bending.
- Equipment manager, engineer, technician, and operator should all be on the testing team.
Test employees should be aware of the commissioning objectives, requirements, and techniques, as well as the appropriate division of labor. An experienced operator should be assigned to the trial operation.
Overhead Crane Commissioning
The overhead crane operation test can begin after the inspection and preparation. The no-load test, static load test, and movement test are the three steps in the overhead crane operating test.
- No-load testing on overhead cranes
- The crane trolley travelling test, overhead crane travel test, and no-load hook test are the three sections of the overhead crane no-load test.
- Travel test for trolleys and hoists
- Start the overhead crane trolley/hoist and make it run back and forth along the track more than three times.
- Test the limit switch for sensitivity and dependability.
- The driven wheels must always be in contact with the rail; the distance between the positive wheel and the rail should not exceed 1mm.
- Test of crane travel
- Make the overhead crane run more than three times back and forth along the rail. Each time you run, you must cover at least 3 meters.
- The overhead crane's wheels must not become trapped on the rail.
- Hook test with no load
- Test the operation of hook more than three times to lift the empty hook up and down.
- Examine the braking system and the lifting limits.
- All traveling and lifting mechanisms must function in a stable manner, with no vibration or shock.
Overhead crane static load tests
- The no-load test must be qualified before the static load test.
- Place the crane at one end of the rail. The trolley/hoist raises the rated capacity and travels back and forth along the crane girder.
- Set the trolley to one end of the crane girder and unload the cargo.
- Placing a plumb in the center of the crane girder to check the initial bending degree. Come to the middle of the girder with the operating trolley/hoist, lift loads 1.25 times their rated capacity up to 100mm, and maintain this condition for 10 minutes on both sides of the girder.
- Then look at the bending degree once more.
- Then unload the capacity to see if the girder has changed permanently. This test should be repeated three times.
- After that, look at the ultimate bending degree, which should be greater than 0.8L/1000.
Place the trolley/hoist stop in the middle and raise the rated capacity to test the girder's downwarping resilience, which should not exceed L/700. The resilience downwarping for a single girder overhead crane should not exceed L/600.
Load tests on movement
- Lift loads that are 0.5, 0.7, 1, and 1.1 times the overhead crane's rated capacity.
- Make many trips with the trolley/hoist.
- Start the crane traveling mechanism and run the overhead crane many times if no problems are found.
- The lifting mechanism must work for 10-15 minutes, and the traveling mechanism must work for 20 minutes or 10 times.
- Ensure that the brake is operable, that the reducer is free of noise and vibration, that the temperature is normal, and that there is no oil escaping;
- Check to see if the lubrication system is working properly.
- Ensure that all limiters and safety devices are in working order, as well as that the electrical box is in good condition, that the temperature is normal, that there is no noise or vibration, and that the cable/line connections are not burned.