A Case Study on Single Girder Cranes 5 Ton in Low-Height Factory
Explore how custom single girder overhead cranes maximize efficiency in low-height factories, overcoming space constraints for optimal performance.
Low-height factories face unique challenges when it comes to selecting overhead cranes. The primary issue is fitting a crane into a factory with limited vertical space, which can restrict the lifting height and overall functionality of standard overhead cranes. These constraints make it crucial to find a crane solution that not only fits within the available space but also meets the operational needs of the factory. Standard cranes may not always be suitable due to their height or structural requirements, making customization a key consideration.
Single girder overhead cranes are often the preferred choice in such environments due to their simpler and more compact design compared to double girder cranes. However, even single girder cranes must be tailored to handle the specific limitations of low-height factories. This requires an understanding of various factors, such as the crane's lifting height, span, and overall dimensions, to ensure optimal performance and space utilization.
Factory Situation Analysis
Client Inquiry
The client approached us with a request to supply six 5-ton single girder overhead cranes for their manufacturing facility. Their requirement was driven by the need to enhance operational efficiency within their existing workshop setup. The cranes were intended for use across one of the factory spans, highlighting the need for precision in customization to meet both their lifting and spatial constraints.
Factory Constraints
The factory presented a significant challenge due to its low height. Specifically, the minimum height from the ground to the roof’s lowest point was 5175 mm. This limitation necessitated a careful evaluation of crane options to ensure they would fit within this restricted vertical space while still delivering the required performance.
Key Data Points
- Lifting Capacity:The lifting capacity defines the maximum weight the crane can handle. For this project, the cranes needed to have a lifting capacity of 5 tons to match the client’s operational needs.
- Lifting Height (H):Lifting height refers to the distance from the hook center to the ground. In this low-height factory, achieving an adequate lifting height was critical to ensure that the cranes could lift loads effectively without obstruction. The available space between the factory’s roof and the ground limited the maximum lifting height, influencing the design of the crane.
- Span (S):The span is the distance between the two runway tracks where the crane travels. It determines the width of the area that the crane can cover. For the client's workshop, the span needed to accommodate the layout and ensure the crane could reach all necessary work areas.
- Crane Traveling Length (L):This is the distance the crane can travel along the runway tracks. The length of crane travel impacts how effectively the crane can cover the entire working area. For this project, the crane was required to cover a running distance of approximately 50 to 60 meters, aligning with the factory’s operational requirements.
These key data points guided the selection and customization of the single girder overhead cranes, ensuring that they would meet the factory’s specific needs while accommodating the constraints of the low-height environment.
Solution Matching
Crane Types Considered
Single Girder Electric Overhead Traveling Cranes (EOT Cranes): These cranes are a common choice for various industrial applications. They feature an electric hoist that runs along a single girder, providing reliable lifting and traveling capabilities. However, the standard design may not always be ideal for low-height factories due to the height of the hoist and its components.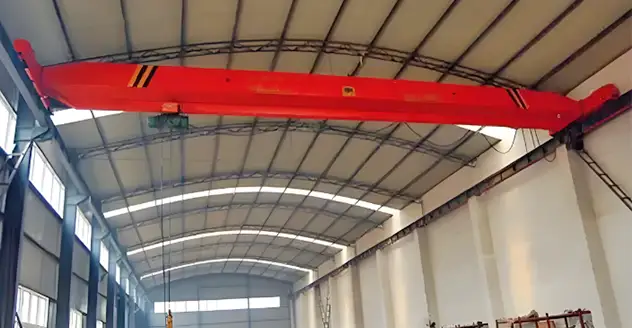
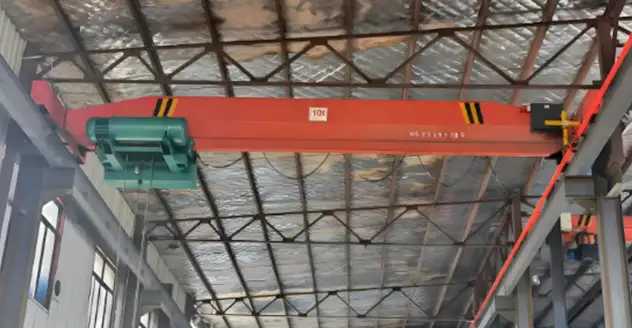
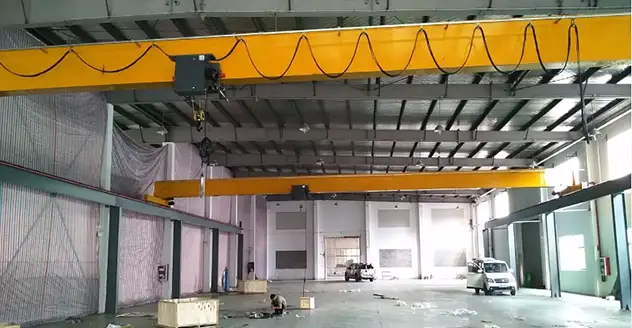
Customization Considerations
To address the client's specific requirements, detailed drawings and specifications were prepared for each crane type:
Single Girder Electric Overhead Traveling Cranes (EOT Cranes):
Specifications:- Lifting Capacity: 5 tons
- Span: 10.5 meters
- Lifting Height: 3135 mm
Customization: Adjustments included optimizing the hoist and bridge structure to fit within the factory’s height constraints while ensuring effective performance. Low Headroom Single Girder Overhead Cranes:
Specifications:- Lifting Capacity: 5 tons
- Span: 10.5 meters
- Lifting Height: 3645 mm
Customization: Focused on reducing the crane’s height through a low headroom hoist design, allowing more efficient use of the available vertical space. FEM/DIN Type Single Girder Overhead Cranes:
Specifications:- Lifting Capacity: 5 tons
- Span: 10.5 meters
- Lifting Height: 3817 mm
Customization: Included advanced design features to maximize lifting height and ensure compliance with high-performance standards. This crane type offered the highest lifting height among the options considered. The customization process involved analyzing the factory’s dimensions and constraints to determine the most suitable crane type. Each option was evaluated for its ability to fit within the limited vertical space while meeting the operational requirements of the workshop. This thorough assessment ensured that the selected crane design would provide optimal performance and efficiency in the low-height factory environment.
Scheme Analysis
Price Comparison
Single Girder EOT Cranes:
- Cost: $2700.00 per set
- Features: Basic design with standard hoisting mechanisms, suitable for factories with moderate height requirements.
- Pros: Cost-effective solution with straightforward design and installation.
- Cons: Limited headroom and height adjustments compared to other options.
- Cost: $3100.00 per set
- Features: Designed specifically for low-height spaces, providing better headroom and maximizing lifting height.
- Pros: Optimal for environments with restricted vertical space. Higher lifting height compared to standard EOT cranes.
- Cons: Higher initial cost compared to standard EOT cranes.
- Cost: $6000.00 per set
- Features: Advanced design adhering to European standards, offering the highest lifting height and enhanced performance.
- Pros: Superior construction, durability, and lifting capabilities, suitable for more demanding applications.
- Cons: Higher cost and potentially over-specified for some low-height environments.
Headroom Lifting Height Comparison for Electric Hoists
- CD Type Wire Rope Electric Hoist: 1120mm
- Low Headroom Type Wire Rope Electric Hoist: 802mm
- Euro-Type Wire Rope Electric Hoist: 630mm
The differences in headroom lifting height are due to the structural design variations:
- CD Type Hoist: Trolley wheels are positioned at the top of the hoist structure.
- Low Headroom and Euro-Type Hoists: Trolley wheels are positioned in the middle of the hoist structure.
The elevated trolley wheel placement in the CD type hoist allows the hoist body to rise above the main beam, thereby increasing the lifting height of the single girder overhead crane.
Lifting Height Comparison
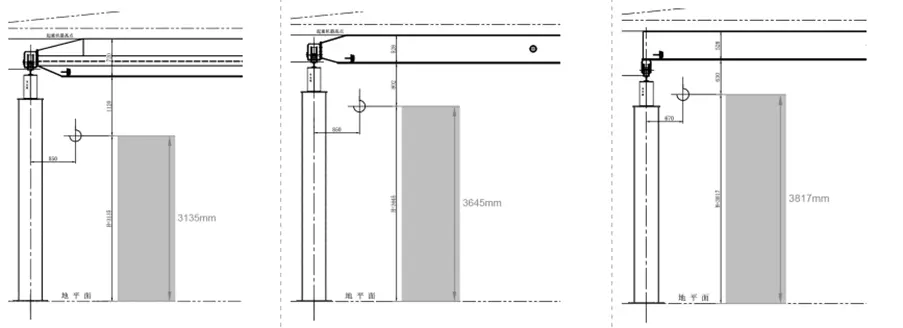
Single Girder EOT Crane:
- Lifting Height: 3135 mm
- Description: Provides a standard lifting height suitable for typical industrial needs but may be limiting for very low-height spaces.
Low Headroom Crane:
- Lifting Height: 3645 mm
- Description: Offers a greater lifting height within constrained vertical space, making it a better fit for low-height factories.
FEM/DIN Crane:
- Lifting Height: 3817 mm
- Description: Maximizes lifting height with advanced design features, ideal for environments where every millimeter of headroom counts.
Coverage and Operational Range
LD Single Girder EOT Cranes:
- Coverage: Typically designed to cover the span of the factory, with operational ranges extending to both extreme left and right positions.
- Operational Range: Adequate for general tasks but limited in terms of flexibility compared to low headroom or FEM/DIN designs.
Low Headroom LD Low Headroom Cranes:
- Coverage: Similar to EOT cranes but with enhanced operational range due to optimized headroom design.
- Operational Range: Allows for more efficient coverage of the workspace, especially in confined areas.
FEM/DIN Cranes:
- Coverage: Extensive coverage capabilities with robust design, suitable for handling larger or more complex operations.
- Operational Range: Provides the greatest flexibility and reach, accommodating a wide range of operational needs.
Post-Sale Maintenance Requirements
Single Girder EOT Cranes:
- Brake Inspection: Regular checks to ensure braking system functionality.
- Fault Code Display and Troubleshooting: Basic fault indicators for easier troubleshooting.
- Motor and Cable Management: Standard maintenance practices to ensure longevity.
Low Headroom Cranes:
- Brake Inspection: Similar maintenance needs as standard EOT cranes, with additional focus on compact design features.
- Fault Code Display and Troubleshooting: Enhanced diagnostic tools to address more complex issues related to headroom design.
- Motor and Cable Management: Requires careful management due to the compact design.
FEM/DIN Cranes:
- Brake Inspection: Comprehensive maintenance to ensure performance meets high standards.
- Fault Code Display and Troubleshooting: Advanced diagnostic systems for efficient troubleshooting and maintenance.
- Motor and Cable Management: High-quality management systems to maintain optimal performance in demanding environments.
This scheme analysis provides a detailed comparison of the crane types, focusing on their price, lifting height, operational range, and maintenance requirements. It helps in evaluating the most suitable option based on cost-effectiveness, operational needs, and long-term maintenance considerations.
Conclusion
Recommendation Summary
When selecting a crane for low-height factory environments, several key factors must be considered:
- Lifting Height: The low headroom single girder overhead crane provides the best lifting height among the options, making it suitable for factories with limited vertical space. With a lifting height of 3645 mm, it offers a significant improvement over standard EOT cranes and is more practical than FEM/DIN cranes for this particular application.
- Coverage and Operational Range: Low headroom cranes offer better coverage and operational flexibility in confined spaces compared to standard EOT cranes. They maximize the usable space within the factory, which is crucial for efficient operation in a low-height environment.
- Maintenance Requirements: Low headroom cranes, while more advanced, may require slightly more detailed maintenance compared to standard EOT cranes due to their compact design. However, the advanced diagnostic tools available make troubleshooting and maintenance manageable.
- Cost: While low headroom cranes are more expensive than standard EOT cranes, they provide better functionality and fit for low-height environments. Their cost is justified by the increased lifting height and operational efficiency they offer.
Client Decision
The client has chosen the low headroom single girder overhead cranes as the optimal solution for their factory. This decision is based on:
- Specific Needs: The factory's constraints require a crane that maximizes lifting height while fitting within the limited vertical space. The low headroom crane meets this requirement effectively.
- Cost vs. Benefit: Despite the higher initial cost, the benefits in terms of lifting height, operational range, and overall efficiency outweigh the additional expense.
- Future-Proofing: Investing in a crane with advanced features ensures long-term suitability and flexibility for the factory’s evolving needs.
By selecting the low headroom single girder overhead cranes, the client ensures that their operational requirements are met with the best possible solution for their unique environment.
Yuantai Crane Expertise
Customization Capabilities
Yuantai Crane stands out for its exceptional expertise in delivering customized overhead crane solutions. With extensive experience in designing and manufacturing cranes to meet specific factory needs, Yuantai Crane excels in providing tailored solutions that address various constraints and requirements.
Key Customization Features:
- Precision Engineering: Yuantai Crane leverages advanced engineering techniques to create cranes that fit precisely within limited vertical spaces. This ensures optimal performance and safety in challenging environments.
- Adaptability: The company offers a range of options, including low headroom designs and specialized hoisting mechanisms, to address unique operational needs and space limitations.
- Quality Assurance: Every crane is built with high-quality materials and adheres to rigorous safety standards, ensuring long-term reliability and performance.
- Expert Consultation: Yuantai Crane provides expert consultation to help clients choose the best crane type and specifications for their specific requirements, including lifting capacity, height, span, and more.
If you are facing challenges with overhead crane selection or need a customized solution for your factory’s unique constraints, contact Yuantai Crane today. Our team of experts is ready to assist you in designing and implementing the perfect crane system to meet your needs. Reach out to us for a consultation and discover how our tailored crane solutions can enhance your operational efficiency and address your specific requirements.