Chemical Workshop Aluminum Gantry Cranes for Hazardous Material Handling
Chemical Workshop Aluminum Gantry Cranes for Hazardous Material Handling. Chemical workshop aluminum gantry crane for sale 1 ton, 2 ton, 3 ton, 5 ton for handling implementing hazardous material handling in workshops.
Chemical workshops play a crucial role in various industries, from manufacturing to research and development. Within these environments, the handling of hazardous materials is a daily occurrence, posing significant risks to both personnel and the surrounding environment. It's imperative for businesses operating in chemical workshops to prioritize safety measures to mitigate these risks effectively.
Chemical workshops are dynamic environments where a wide range of hazardous materials, including corrosive liquids, flammable gases, and toxic substances, are processed, stored, and transported. From small-scale laboratories to large-scale manufacturing plants, these facilities handle chemicals at various stages of production, posing inherent risks to workers, equipment, and the environment.
Safety measures are paramount in chemical workshops to protect personnel, prevent accidents, and minimize the impact of hazardous material spills or releases. Without adequate safety protocols in place, chemical handling activities can lead to severe injuries, environmental contamination, and costly damage to infrastructure. By implementing robust safety measures, businesses can ensure the well-being of their employees and safeguard the surrounding community from potential harm.
Material Handling Risks and Challenges in Chemical Workshops
Chemical workshops present unique risks and challenges due to the nature of the materials being handled and the complexities of the processes involved. To effectively mitigate these risks, it's essential to understand the various hazards associated with chemical handling and to adhere to regulatory compliance and safety standards.
Hazards Associated with Handling Chemicals
Chemicals pose a range of hazards, including toxicity, flammability, reactivity, and corrosiveness. Exposure to these substances can lead to health effects such as skin irritation, respiratory problems, and chemical burns. Additionally, improper handling or storage of chemicals can result in fires, explosions, and environmental contamination. It's crucial for personnel working in chemical workshops to be aware of these hazards and to take appropriate precautions to minimize risks.
Regulatory Compliance and Safety Standards in Chemical Workshops
Government agencies and regulatory bodies have established stringent safety standards and regulations to ensure the safe handling, storage, and disposal of hazardous chemicals. Compliance with these standards is mandatory for chemical workshops to prevent accidents and protect both workers and the environment. Key regulations include OSHA's Hazard Communication Standard (HCS), which requires employers to provide information and training on hazardous chemicals, as well as guidelines from organizations such as the National Fire Protection Association (NFPA) and the Environmental Protection Agency (EPA).
Role of Aluminum Gantry Cranes in Chemical Workshop Safety
Aluminum gantry cranes play a vital role in promoting safety and efficiency in chemical workshops where hazardous materials are handled. These versatile lifting solutions offer several benefits and customization options tailored to the unique challenges of working with hazardous chemicals.
Benefits of Using Aluminum Gantry Cranes for Hazardous Material Handling
Aluminum gantry cranes offer numerous advantages that contribute to safer and more efficient material handling in chemical workshops. Their lightweight yet durable construction makes them ideal for use in corrosive environments, where traditional steel cranes may be prone to rust and degradation. Additionally, aluminum gantry cranes are non-sparking and non-conductive, reducing the risk of ignition when handling flammable or reactive chemicals. Their portability and ease of assembly allow for flexible deployment in various areas of the workshop, enabling workers to safely lift and move hazardous materials without the need for fixed lifting equipment.
Customization Options to Enhance Safety and Efficiency
To further enhance safety and efficiency, aluminum gantry cranes can be customized with various features and accessories. Adjustable height and span options allow for precise positioning of loads, minimizing the risk of spills or accidents during lifting operations. Specialized lifting attachments, such as chemical-resistant slings or vacuum lifters, can be incorporated to safely handle containers of hazardous materials without compromising worker safety. Additionally, safety features such as overload protection systems and emergency stop buttons can be integrated to ensure compliance with safety regulations and provide added peace of mind for operators.
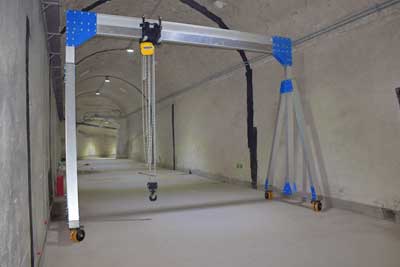
LT1: Aluminum Gantry Crane with Fixed Span and Height
- Capacity up to 5 tons.
- Span up to 4 meters.
- Max. height up to 5 meters
Get Fixed Span & Fixed Hight Aluminum Alloy Gantry Crane Price
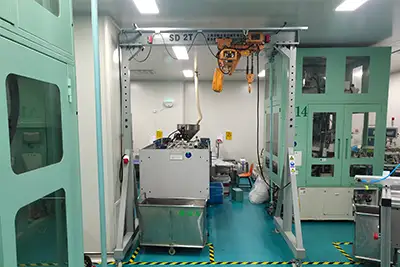
lT 2 Height Adjustable Aluminum Gantry Cranes
- Capacity up to 5 tons.
- Span up to 4 meters.
- Max. height up to 5 meters
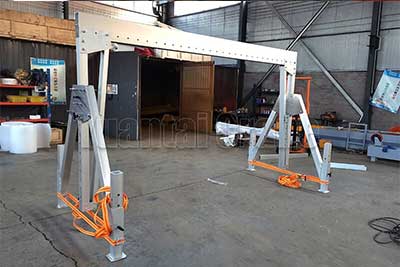
LT3: Fixed Aluminum Gantry Crane with Adjustable Span and Height
- Capacity up to 2 tons.
- Span up to 4 meters.
- Max. height up to 4 meters
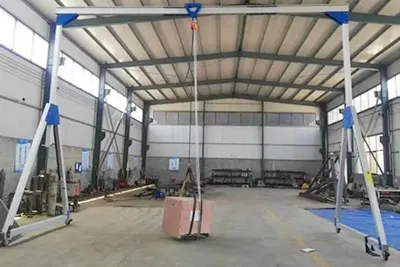
lT4 Simple Gantry Cranes with adjustable Height & Span
- Capacity up to 2 tons.
- Span up to 4 meters.
- Max. height up to 4 meters
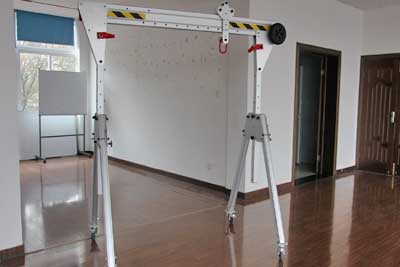
LT5:Foldable Aluminum Gantry Crane with Adjustable Span and Height
- Capacity up to 3 tons.
- Span up to 4 meters.
- Max. lifting height is no more than 6 meters
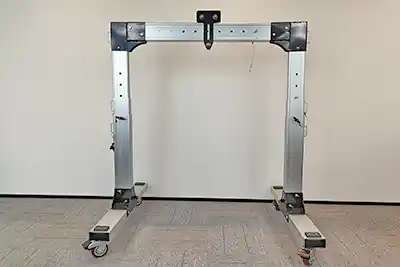
LT6 Ajustable Gantry Crane with Telescoping Height and Span T Frame Gantry Cranes
- Capacity up to 2 tons.
- Span up to 4 meters.
- Max. lifting height is no more than 4 meters
Case Studies: Successful Implementation of Aluminum Gantry Cranes
Aluminum gantry cranes have been successfully implemented in various settings within the chemical industry, contributing to improved safety and efficiency in handling hazardous materials.
Chemical Manufacturing Plants
In chemical manufacturing plants, aluminum gantry cranes are essential for lifting and moving raw materials, intermediate products, and finished goods throughout the production process. These cranes are customized to meet the specific requirements of chemical processes, including adjustable height and span features to accommodate varying container sizes and configurations. By integrating aluminum gantry cranes into their operations, chemical manufacturing plants have improved workplace safety, reduced manual handling risks, and enhanced overall productivity.
Laboratory Facilities
Laboratory facilities rely on aluminum gantry cranes for safe and precise handling of hazardous chemicals, delicate equipment, and sensitive samples. These cranes are customized with specialized lifting attachments and safety features to meet the stringent requirements of laboratory environments. With aluminum gantry cranes in place, laboratories can minimize the risk of spills, contamination, and workplace accidents, ensuring the integrity of experiments and research activities.
Storage and Distribution Centers for Hazardous Materials
Storage and distribution centers for hazardous materials utilize aluminum gantry cranes to facilitate the loading and unloading of containers, drums, and barrels. These cranes are equipped with features such as corrosion-resistant materials and anti-sparking components to mitigate the risks associated with handling flammable or reactive substances. By employing aluminum gantry cranes, storage and distribution centers can streamline material handling operations, reduce manual labor requirements, and enhance overall safety compliance.
Through these case studies, it is evident that aluminum gantry cranes play a crucial role in promoting safety and efficiency across various segments of the chemical industry, from manufacturing plants to laboratory facilities and storage centers.
Safety Measures and Best Practices
Ensuring the safe operation of aluminum gantry cranes in chemical workshops requires adherence to strict safety measures and best practices.
Training and Certification Requirements for Operators
Operators of aluminum gantry cranes in chemical workshops must undergo comprehensive training and obtain proper certification to operate the equipment safely. Training programs should cover crane operation, load handling techniques, hazard identification, and emergency procedures. Additionally, operators should receive specialized training on handling hazardous materials and understanding chemical properties to mitigate risks effectively.
Routine Maintenance and Inspection Procedures
Regular maintenance and inspection are essential for keeping aluminum gantry cranes in optimal condition and preventing equipment failures. Routine maintenance tasks include lubrication of moving parts, inspection of structural components for signs of wear or corrosion, and testing of safety features such as emergency stop buttons and overload protection systems. By adhering to a structured maintenance schedule, chemical workshops can identify potential issues early and address them before they escalate into safety hazards.
Emergency Response Protocols for Chemical Spills or Accidents
Chemical workshops must have well-defined emergency response protocols in place to handle incidents such as chemical spills or accidents involving aluminum gantry cranes. These protocols should outline procedures for evacuating personnel, containing spills, and notifying appropriate authorities. Additionally, workers should be trained in the proper use of personal protective equipment (PPE) and emergency response equipment, such as spill containment kits and fire extinguishers. Regular drills and simulations can help ensure that personnel are prepared to respond effectively to emergencies and minimize the impact on safety and the environment.
By implementing comprehensive safety measures and best practices, chemical workshops can mitigate risks associated with aluminum gantry crane operations and create a safer working environment for employees and the surrounding community.
Cost Considerations and Return on Investment
When implementing aluminum gantry cranes in chemical workshops, it's crucial to consider both the initial investment and the long-term savings associated with safety and compliance.
Initial Investment vs. Long-Term Savings
While the initial investment in aluminum gantry cranes may seem significant, it's essential to consider the long-term savings they can offer. By enhancing safety and efficiency in hazardous material handling, gantry cranes help minimize the risk of accidents, injuries, and costly downtime. Additionally, their durability and low maintenance requirements contribute to long-term cost savings compared to alternative lifting solutions. Businesses should weigh the upfront costs against the potential savings and benefits over the crane's lifespan to make an informed investment decision.
When evaluating the initial investment versus long-term savings associated with aluminum gantry cranes, it's crucial to consider several key factors:
- Safety and Risk Mitigation: Aluminum gantry cranes are equipped with safety features that help prevent accidents and injuries in chemical workshops. By minimizing the risk of mishaps during material handling tasks, these cranes contribute to a safer work environment. This reduction in workplace accidents can lead to substantial cost savings by avoiding potential liabilities, medical expenses, and production disruptions resulting from injuries or property damage.
- Operational Efficiency: Gantry cranes streamline material handling processes in chemical workshops, resulting in increased productivity and efficiency. Their precise lifting capabilities and customizable features enable workers to handle hazardous materials with greater accuracy and speed. As a result, businesses can optimize workflow and throughput, ultimately leading to cost savings through improved operational efficiency.
- Durability and Low Maintenance: Aluminum gantry cranes are renowned for their durability and low maintenance requirements. Unlike traditional lifting equipment that may require frequent repairs or replacements, gantry cranes are designed to withstand harsh chemical environments and heavy-duty use. The reduced need for maintenance and repairs translates to lower operational costs and fewer disruptions to workflow, resulting in long-term savings over the crane's lifespan.
- Compliance and Regulatory Costs: Non-compliance with safety regulations in chemical workshops can result in significant financial penalties and reputational damage. Investing in aluminum gantry cranes that meet industry standards and regulatory requirements helps mitigate compliance risks and associated costs. By adhering to safety regulations and implementing reliable lifting solutions, businesses can avoid fines, legal expenses, and potential business interruptions.
- Total Cost of Ownership: When assessing the total cost of ownership, it's essential to consider not only the upfront purchase price of the gantry crane but also the ongoing operational costs and potential savings over its lifetime. Calculating the return on investment (ROI) involves analyzing the tangible and intangible benefits of gantry crane ownership, including improved safety, efficiency gains, reduced downtime, and enhanced workplace morale.
In conclusion, while the initial investment in aluminum gantry cranes may represent a significant upfront cost, the long-term savings and benefits they offer far outweigh the initial expenditure. By enhancing safety, efficiency, and compliance in chemical workshops, gantry cranes contribute to cost savings, productivity gains, and a safer work environment, making them a worthwhile investment for businesses seeking to optimize their operations.
Cost of Non-Compliance with Safety Regulations
Non-compliance with safety regulations in chemical workshops can result in severe financial penalties, legal liabilities, and reputational damage. Implementing aluminum gantry cranes with robust safety features and adherence to regulatory standards helps mitigate these risks and avoid costly fines or lawsuits. Furthermore, prioritizing safety and compliance demonstrates a commitment to employee well-being and environmental stewardship, which can enhance the organization's reputation and competitiveness in the industry. Businesses should factor in the potential costs of non-compliance when evaluating the investment in gantry cranes and prioritize safety as a core business value.
Non-compliance with safety regulations in chemical workshops can have significant financial repercussions and pose serious risks to both personnel and the environment. Here's a closer look at the potential costs of non-compliance with safety regulations:
- Financial Penalties: Regulatory agencies impose substantial fines on businesses found to be in violation of safety regulations. These penalties can vary depending on the severity of the violation and may range from hundreds to thousands of dollars per incident. Repeat violations or egregious offenses can result in even steeper fines, placing a considerable financial burden on the organization.
- Legal Liabilities: In addition to fines, non-compliance with safety regulations can expose businesses to legal liabilities and lawsuits. If an accident or injury occurs due to safety violations, affected individuals may pursue legal action against the company for negligence. Legal fees, settlements, and damages awarded in court can amount to significant financial losses and tarnish the company's reputation.
- Reputational Damage: Public perception plays a crucial role in the success of any business. Incidents of non-compliance with safety regulations can damage the company's reputation and erode trust among customers, partners, and stakeholders. Negative publicity resulting from safety violations can lead to decreased sales, loss of contracts, and challenges in attracting and retaining talent.
- Operational Disruptions: Regulatory violations may trigger investigations, audits, or enforcement actions by regulatory agencies, disrupting normal business operations. Compliance-related activities, such as remediation efforts, audits, and mandatory training, require time, resources, and management attention, diverting focus away from core business activities and impacting productivity.
- Environmental Impact: Non-compliance with safety regulations can also have environmental consequences, such as chemical spills, leaks, or emissions. These incidents pose risks to ecosystems, water sources, and public health, potentially resulting in cleanup costs, remediation efforts, and regulatory sanctions.
In summary, the costs of non-compliance with safety regulations extend beyond financial penalties to include legal liabilities, reputational damage, operational disruptions, and environmental impact. Investing in aluminum gantry cranes with robust safety features and adherence to regulatory standards is essential for mitigating these risks and safeguarding the well-being of employees, the environment, and the organization's bottom line. Prioritizing safety as a core business value demonstrates a commitment to compliance, risk management, and responsible corporate citizenship.
By considering both the initial investment and the long-term savings associated with safety and compliance, chemical workshops can make strategic decisions regarding the implementation of aluminum gantry cranes and ensure a safe and efficient working environment for employees.
Conclusion
In this blog, we've explored the critical role of aluminum gantry cranes in enhancing safety and efficiency in chemical workshops. We discussed the risks and challenges associated with handling hazardous materials, the benefits of using gantry cranes, and successful case studies showcasing their implementation. Additionally, we highlighted safety measures, cost considerations, and the importance of compliance with regulations.
Safety should always be a top priority in chemical workshops, where the handling of hazardous materials poses significant risks to both personnel and the environment. Implementing aluminum gantry cranes with customized safety features helps mitigate these risks, safeguarding employees, facilities, and the surrounding community. By prioritizing safety, chemical workshops can create a culture of responsibility and accountability, promoting a safer working environment for all.
Recommendations for Implementing Aluminum Gantry Cranes
For chemical workshops considering the implementation of aluminum gantry cranes, several recommendations can ensure a successful and safe integration:
Conduct a thorough risk assessment to identify potential hazards and safety requirements.
Select gantry cranes with customizable features tailored to the specific needs and challenges of chemical handling.
Provide comprehensive training for operators on safe crane operation, maintenance procedures, and emergency protocols.
Establish regular maintenance and inspection schedules to ensure the continued safety and reliability of gantry cranes.
Stay informed about regulatory changes and industry best practices to maintain compliance and mitigate risks effectively.
By following these recommendations and prioritizing safety at every stage, chemical workshops can leverage aluminum gantry cranes to enhance operational efficiency, protect personnel and assets, and promote a culture of safety and responsibility.