Overhead Cranes in Valve & Pump Assembly Plants 5 T, 10 T, 20 T
Precision overhead cranes in valve and pump assembly plants ensure component integrity, enhancing accuracy, efficiency & safety in handling delicate parts.
Precision Overhead Cranes in Valve and Pump Assembly Plants: Ensuring Component Integrity
In valve and pump assembly plants, precision is paramount. The integrity of each component must be maintained to ensure the final product's reliability and performance. Any misalignment or damage during the assembly process can lead to costly repairs and downtime. This is where overhead cranes play a crucial role.
Overhead cranes, designed to move heavy components with precision, are essential in these environments. They ensure that valve and pump components are handled carefully, reducing the risk of damage and improving overall efficiency. This blog will explore the different types of cranes used, the typical loads they handle, their applications, and the importance of precision handling in maintaining component integrity.
Types of Cranes Used FOR Valve And Pump Plants
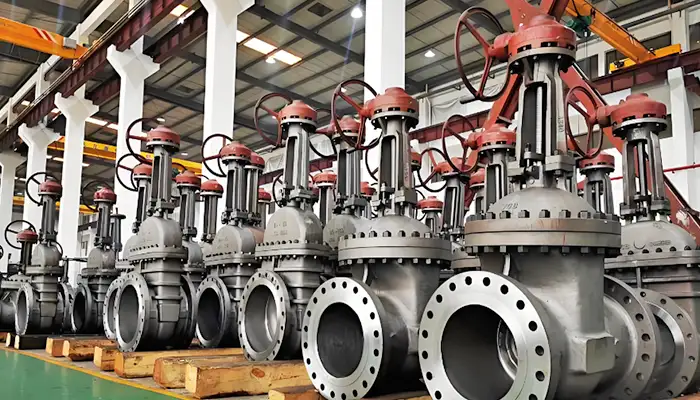
Single Girder Overhead Cranes
Single girder overhead cranes consist of a single bridge girder supported by two end trucks. They operate on a single rail or runway system, with the hoist and trolley moving along the bottom flange of the bridge girder. The design is straightforward, which makes these cranes a popular choice for various industrial applications, including valve and pump assembly plants.
Key design features include:
Single Bridge Girder: A single horizontal beam that spans the width of the work are
End Trucks: Located at each end of the girder, these trucks support the bridge and allow it to move along the runway.
Hoist and Trolley: The hoist lifts the load, and the trolley moves horizontally along the bridge girder.
Runway System: Rails mounted on the building's structure that allow the bridge and trolley to move across the work area.
Advantages and Disadvantages
Advantages:
Cost-Effective: Generally more affordable than double girder cranes due to simpler design and construction.
Lighter Structure: The lighter weight of the single girder reduces the load on the building structure, potentially lowering installation costs.
Ease of Installation: The simpler design allows for quicker and easier installation.
Versatility: Suitable for various lifting and moving tasks, making it a flexible option for different applications within assembly plants.
Disadvantages:
Lower Load Capacity: Single girder cranes typically have a lower load capacity compared to double girder cranes, limiting their use for very heavy loads.
Reduced Span: They generally cover shorter spans than double girder cranes, which may be a limitation in larger facilities.
Maintenance Access: Access to maintenance components like the hoist may be more challenging due to their placement beneath the girder.
Typical Applications in Assembly Plants
In valve and pump assembly plants, single girder overhead cranes are commonly used for tasks that require precision and moderate load capacities. Typical applications include:
Valve Component Assembly: These cranes are ideal for assembling various valve components, such as gate valves, ball valves, and butterfly valves. They provide the necessary precision to ensure each part fits together correctly.
Transporting Pump Parts: Single girder cranes are used to move pump components like impellers, casings, and shafts from one workstation to another, ensuring they are handled delicately to avoid damage.
Handling Motor Units: While motor units can be heavy, the moderate capacity of single girder cranes is often sufficient for lifting and positioning these components during assembly.
By utilizing single girder overhead cranes, assembly plants can achieve a balance of cost-efficiency, precision, and versatility, making them a valuable asset in maintaining the integrity of valve and pump components throughout the assembly process.
Jib Cranes
Jib cranes are a type of overhead crane that consists of a horizontal jib or boom that supports a moveable hoist. The jib is fixed to a wall or mounted on a floor pillar. These cranes can rotate either partially or fully, depending on their design, allowing them to cover a circular area within the work zone.
Key design features include:
Jib/Boom: The horizontal arm that supports the hoist and trolley. It can rotate around a central pivot point.
Pillar or Wall Mount: Jib cranes can be floor-mounted on a pillar or attached to a wall, providing flexibility in installation.
Hoist and Trolley: The hoist lifts the load, and the trolley moves along the length of the jib to position the load precisely.
Rotation Mechanism: Allows the jib to rotate around the mounting point. Rotation can range from 180 degrees to a full 360 degrees.
Advantages and Disadvantages
Advantages:
Flexibility: Jib cranes can be installed in various locations, either on the floor or on walls, making them adaptable to different workspace configurations.
Space Efficiency: They are ideal for small to medium-sized work areas where space is limited. Their ability to cover a circular area maximizes the usable workspace.
Ease of Use: Simple operation and control make jib cranes easy to use for lifting and moving tasks.
Cost-Effective: Generally less expensive than large overhead cranes, making them a cost-effective solution for specific lifting needs.
Disadvantages:
Limited Coverage: Jib cranes cover a smaller area compared to overhead cranes, which may limit their use in larger facilities.
Lower Load Capacity: Typically, jib cranes have a lower load capacity compared to single or double girder overhead cranes, restricting their use to lighter loads.
Rotation Constraints: The range of rotation might be limited based on the design, potentially limiting their flexibility in certain applications.
Typical Applications in Assembly Plants
In valve and pump assembly plants, jib cranes are used for tasks that require localized lifting and precise handling within a confined are Typical applications include:
Component Assembly: Jib cranes are used to assemble small to medium-sized components, such as valve parts or pump subassemblies. Their precise movement allows for careful handling of delicate parts.
Workstation Support: These cranes are often installed at individual workstations to assist workers in lifting and positioning parts, reducing manual handling and improving efficiency.
Maintenance and Repairs: Jib cranes are useful for maintenance tasks, allowing technicians to lift and move parts for repair or inspection without the need for larger, more cumbersome equipment.
Material Handling: They are employed to load and unload materials at specific points within the assembly plant, providing a flexible solution for moving parts within a localized are
Jib cranes offer a versatile and cost-effective solution for many lifting tasks in valve and pump assembly plants. Their ease of installation and operation, combined with their adaptability to different workspace configurations, make them an invaluable tool for maintaining precision and efficiency in the assembly process.
Typical Loads Handled
Valve Assemblies
Types of Valves
- Valve assemblies are critical components in many industrial applications, including those in the valve and pump assembly plants. Different types of valves are used depending on the specific requirements of the system they are integrated into. The main types include:
- Gate Valves: Gate valves use a gate or wedge that moves up and down to start or stop the flow of fluid. They are designed for fully open or fully closed service. Commonly used in pipelines where a straight-line flow and minimum restriction are desired. They are ideal for isolating sections of a pipeline or system.
- Ball Valves: Ball valves utilize a spherical ball with a hole through the middle. When the hole aligns with the flow direction, the valve is open; when turned 90 degrees, it is closed. Suitable for shut-off and control applications. They are widely used in industries that require tight sealing and reliability.
- Butterfly Valves: Butterfly valves have a disc that rotates to allow or restrict fluid flow. The disc is positioned in the center of the pipe and connected to an actuator on the outside. Ideal for applications that require quick shut-off and are often used in systems where space is limited and large valves are not feasible.
- Check Valves: Check valves allow fluid to flow in one direction only, preventing backflow. They typically have a hinged gate or a ball that moves to block reverse flow. Commonly used in pump systems to prevent reverse flow and protect equipment from damage.
- Globe Valves: Globe valves use a linear motion to throttle flow. The valve seat is parallel to the line of flow, and the disc moves perpendicular to the seat. Used for regulating flow in pipelines, especially where precise control is required.
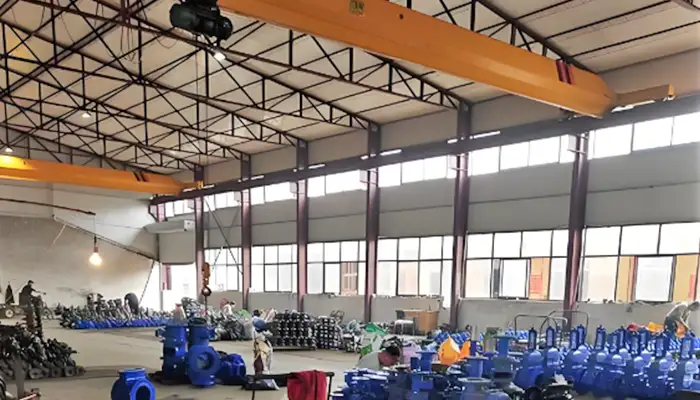
Importance of Precision Handling for Valve Assemblies
Precision handling of valve assemblies is crucial for several reasons:
- Ensuring Component Integrity:
Alignment: Proper alignment of valve components is essential to ensure a tight seal and prevent leaks. Overhead cranes and jib cranes provide the precision needed to position these components accurately.
Damage Prevention: Valve assemblies often include delicate parts such as seals and seats that can be easily damaged if not handled correctly. Precision cranes minimize the risk of dropping or misplacing parts. - Maintaining Performance and Reliability:
Flow Control: Valves are integral to controlling the flow of fluids in a system. Any misalignment or damage can result in poor performance, leading to inefficient operation or system failures.
Safety: Precision handling ensures that valves operate as intended, which is crucial for maintaining the safety of the overall system, especially in high-pressure or hazardous environments. - Quality Assurance:
Consistency: Using precision cranes ensures consistent handling practices across the assembly process, leading to uniform quality in valve assemblies.
Inspection and Testing: Precision cranes facilitate the accurate placement of valves for inspection and testing, ensuring that all parts meet the required specifications before installation. - Efficiency and Productivity:
Speed: Precision handling with cranes can speed up the assembly process by allowing quick and accurate placement of valve components.
Labor Reduction: Automated and precise crane operations reduce the need for manual handling, lowering labor costs and minimizing the risk of human error.
In summary, the careful handling of valve assemblies using precision overhead and jib cranes ensures that these critical components are assembled accurately and efficiently. This not only maintains the integrity and performance of the valves but also contributes to the overall reliability and safety of the systems in which they are used.
Pump Components
Types of Pumps
In valve and pump assembly plants, various types of pumps are assembled and handled. Each type of pump has specific components and assembly requirements:
- Centrifugal Pumps: Centrifugal pumps use a rotating impeller to move fluid through the pump and convert kinetic energy into hydrodynamic energy. The main components include the impeller, casing, shaft, and seals. These pumps are widely used in industries such as water treatment, chemical processing, and petroleum, where high flow rates and continuous operation are required.
- Positive Displacement Pumps: Positive displacement pumps move fluid by trapping a fixed amount and forcing it through the discharge pipe. Types include gear pumps, piston pumps, diaphragm pumps, and screw pumps. They are used in applications requiring precise flow control, such as chemical injection, hydraulics, and food processing.
- Submersible Pumps: Submersible pumps are designed to operate while fully submerged in the fluid they are pumping. Key components include a hermetically sealed motor, impeller, and diffuser. Commonly used in water and wastewater treatment, as well as in wells and underground applications.
- Vacuum Pumps: Vacuum pumps remove gas molecules from a sealed volume to create a partial vacuum. They include rotary vane pumps, diaphragm pumps, and liquid ring pumps. Used in industrial processes such as vacuum packaging, degassing, and laboratory research.
- Peristaltic Pumps: Peristaltic pumps use a rotating roller to compress and move fluid through a flexible tube. The main components include the rotor, rollers, and tubing. Ideal for handling corrosive or viscous fluids in industries like pharmaceuticals, food and beverage, and chemical processing.
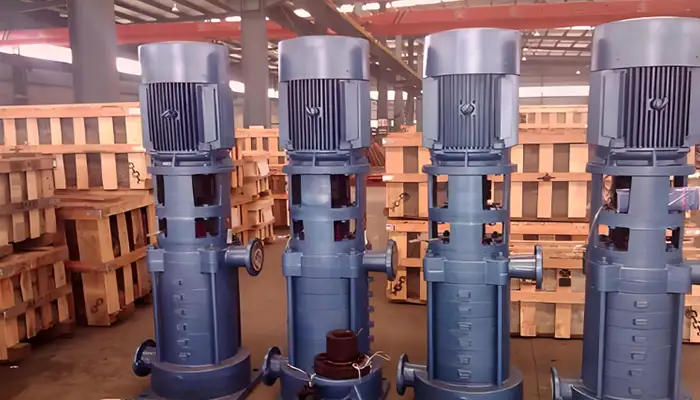
Precision Requirements for Handling Pump Components
Handling pump components with precision is crucial to ensure the performance and longevity of the pumps. Precision requirements include:
- Component Integrity:
Accurate Positioning: Components such as impellers, shafts, and seals must be precisely positioned during assembly to ensure proper alignment and function. Misalignment can cause inefficient operation or mechanical failure.
Damage Prevention: Pump components are often delicate and can be damaged if dropped or mishandled. Precision handling with cranes minimizes the risk of physical damage, such as dents or scratches that can affect performance. - Assembly Accuracy:
Tight Tolerances: Many pump components require assembly within tight tolerances to ensure optimal performance. Precision cranes enable accurate placement and assembly of parts, meeting these stringent requirements.
Consistent Quality: Consistent handling and assembly processes ensure that each pump produced meets quality standards, reducing the likelihood of defects and improving reliability. - Performance Optimization:
Flow Efficiency: The performance of pumps depends on the precise arrangement of components to achieve optimal flow rates and pressures. Precision handling ensures that components are assembled correctly to meet these performance criteri
Vibration and Noise Reduction: Properly aligned and assembled components reduce vibration and noise during operation, leading to quieter and more efficient pumps. - Safety and Reliability:
Sealing Integrity: Ensuring that seals and gaskets are correctly positioned prevents leaks and maintains the integrity of the pump system. This is particularly important in applications involving hazardous or corrosive fluids.
Operational Safety: Precision handling reduces the risk of assembly errors that could lead to pump failure, which can be dangerous and costly in industrial settings. - Efficiency and Productivity:
Speed of Assembly: Precision cranes allow for faster and more efficient assembly of pump components, reducing production time and increasing throughput.
Reduced Manual Labor: Automating the handling and assembly of pump components reduces the need for manual intervention, lowering labor costs and minimizing human error.
In conclusion, the precision handling of pump components using overhead and jib cranes is essential for ensuring the integrity, performance, and reliability of the pumps. By maintaining tight tolerances, preventing damage, and optimizing assembly processes, these cranes play a vital role in the efficient production of high-quality pumps for various industrial applications.
Motor Units
Types of Motors Used in Assembly Plants
In valve and pump assembly plants, various types of motors are used to drive pumps and other machinery.
Each type of motor has unique characteristics and applications:
- Induction Motors: Induction motors, also known as asynchronous motors, rely on electromagnetic induction to generate mechanical power. They consist of a stator, rotor, and a series of windings. Widely used due to their simplicity, robustness, and cost-effectiveness. They are common in pumps, fans, conveyors, and other industrial machinery.
- Synchronous Motors: Synchronous motors run at a speed directly proportional to the frequency of the supply current. They have a stator with windings and a rotor with a direct current (DC) supply. Employed where precise speed and position control are required, such as in high-precision pumps and compressors.
- Servo Motors: Servo motors provide precise control of angular position, speed, and torque. They consist of a motor coupled with a sensor for position feedback. Used in applications requiring high precision and rapid response, such as robotic arms, CNC machinery, and automated assembly lines.
- Stepper Motors: Stepper motors move in discrete steps, allowing for precise control of position without the need for feedback systems. They have multiple coils organized in phases. Common in applications requiring precise positioning and low-speed control, such as valve actuators and automated assembly equipment.
- Direct Current (DC) Motors: DC motors convert direct current electrical energy into mechanical energy. They consist of a stator, rotor, commutator, and brushes. Used where variable speed and high torque are needed, such as in electric drives, pumps, and hoists.
- Brushless DC (BLDC) Motors: BLDC motors use electronic commutation instead of brushes and a commutator. They consist of a stator with windings and a rotor with permanent magnets. Preferred in applications requiring high efficiency, low maintenance, and precise control, such as in fans, pumps, and electric vehicles.
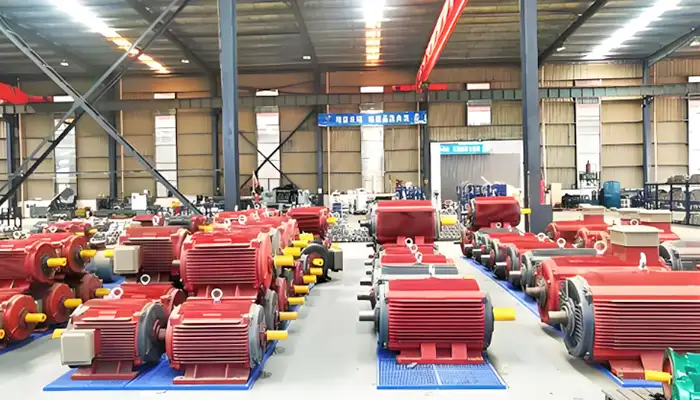
Handling Requirements and Challenges
Handling motor units in assembly plants requires precision and care to ensure their performance and longevity. Key handling requirements and challenges include:
- Weight and Size:
Heavy Components: Motors, especially large industrial ones, can be heavy and bulky. Precision cranes are essential for lifting and positioning these units without causing damage.
Compact Design: Some motors, while not as heavy, are compact and require careful handling to avoid damaging their intricate components. - Alignment and Positioning:
Precise Alignment: Motors must be aligned accurately during assembly to ensure proper functioning. Misalignment can cause excessive wear, vibration, and noise, leading to premature failure.
Mounting Challenges: Installing motors in tight or awkward spaces requires precise control to ensure they are securely and correctly mounted. - Damage Prevention:
Sensitive Components: Motors have delicate components, such as windings and bearings, that can be easily damaged if dropped or mishandled. Precision cranes reduce the risk of physical damage during handling.
Protection from Contaminants: Ensuring motors are handled in a clean environment prevents the ingress of dust, moisture, and other contaminants that can affect performance. - Electrical Safety:
Safe Handling Practices: Electrical motors need to be handled with care to prevent electrical hazards. Proper grounding and insulation must be maintained during handling and installation.
Avoiding Static Discharge: Static discharge can damage electronic components within motors, particularly for brushless and servo motors. Proper grounding and handling techniques are essential. - Efficiency and Productivity:
Speed of Installation: Precision cranes enable faster and more efficient installation of motor units, reducing downtime and increasing productivity in the assembly process.
Consistency: Automated and precise handling ensures consistent installation quality, reducing the likelihood of errors and rework. - Integration with Other Components:
Interfacing with Drives and Controllers: Motors often need to be precisely positioned to interface correctly with drives, controllers, and other system components.
Cable Management: Proper handling includes managing and protecting cables and connectors to ensure reliable electrical connections. - Safety Considerations:
Operator Safety: Using precision cranes reduces the physical strain on workers and minimizes the risk of injury during the handling of heavy and cumbersome motor units.
Equipment Safety: Ensuring motors are handled correctly prevents damage to the motors themselves and other equipment within the assembly plant.
In conclusion, the precise handling of motor units using overhead and jib cranes is essential to ensure their correct installation, alignment, and integration within valve and pump assembly plants. By addressing the unique challenges associated with motor handling, these cranes help maintain the performance, safety, and efficiency of the assembly process.
Typical Overhead Bridge Crane Applications
Assembling and Transporting Valve Components
Steps in Valve Assembly Requiring Crane Use
Valve assembly is a meticulous process that often necessitates the use of overhead bridge cranes at various stages. Here are the typical steps where crane assistance is vital:
- Component Handling:
Incoming Materials: Cranes are used to unload incoming valve components from trucks or storage areas and transport them to the assembly are
Storage and Retrieval: Cranes assist in storing components in designated areas within the assembly plant and retrieving them as needed for assembly. - Assembly Process:
Subassembly Handling: Components such as valve bodies, stems, discs, and actuators are lifted and positioned for subassembly.
Final Assembly: Cranes aid in lifting and aligning components during the final assembly stage, ensuring precise fitting and alignment of parts.
Testing and Inspection: After assembly, cranes may be used to transport assembled valves to testing stations for pressure testing, leak testing, and quality inspection.
Ensuring Precision During Assembly
Precision is paramount in valve assembly to ensure proper functioning and reliability of the final product. Here's how overhead bridge cranes contribute to maintaining precision:
- Accurate Positioning:
Cranes equipped with precision controls allow operators to position valve components with accuracy, ensuring proper alignment and fit.
Adjustable speed controls enable operators to maneuver components slowly and precisely into place, minimizing the risk of errors. - Gentle Handling:
Overhead bridge cranes provide smooth and controlled lifting and lowering motions, reducing the likelihood of damage to delicate valve components.
Soft start and stop features prevent sudden movements that could dislodge or damage components during handling. - Accessibility:
Cranes with flexible configurations can reach components in confined spaces or at elevated heights, facilitating assembly in areas that may be challenging to access manually.
The ability to rotate or move along multiple axes allows operators to position components optimally for assembly, even in complex assemblies.
Case Studies/Examples of Crane Use in Valve Assembly
Case Study 1: Precision Valve Manufacturing Company
Challenge: A valve manufacturer needed to improve the efficiency and accuracy of their valve assembly process to meet increasing demand while maintaining high quality.
Solution: The company implemented overhead bridge cranes with precision controls and custom-designed lifting attachments to handle valve components with precision and care.
Result: With the new crane system in place, the company achieved significant improvements in assembly speed, accuracy, and product quality. They also reported a reduction in assembly errors and rework, leading to higher customer satisfaction and increased profitability.
Case Study 2: Valve Assembly Line Optimization
Challenge: An assembly plant faced bottlenecks and inefficiencies in their valve assembly line due to manual handling of heavy components and limited workspace.
Solution: The plant invested in overhead bridge cranes with extended reach and load capacity to handle larger valve components and streamline assembly processes.
Result: The crane system enabled smoother material flow and faster assembly cycles, reducing idle time and increasing overall productivity. Operators reported improved ergonomics and reduced physical strain, leading to a safer and more comfortable working environment.
In conclusion, overhead bridge cranes play a critical role in assembling and transporting valve components in assembly plants. By providing precise positioning, gentle handling, and improved accessibility, these cranes contribute to the efficiency, accuracy, and quality of the valve assembly process. Case studies demonstrate the tangible benefits of crane use in optimizing assembly operations and achieving better overall performance.
Precision Handling of Pump Parts During Assembly
Key Stages in Pump Assembly Involving Cranes
Pump assembly is a complex process that often relies on overhead bridge cranes for precise handling of components. Here are the key stages where crane assistance is crucial:
- Component Preparation:
Incoming Material Handling: Cranes are used to unload raw materials and transport them to the assembly area, ensuring timely availability of components.
Pre-Assembly Inspection: Components are lifted and positioned for inspection to ensure they meet quality standards before assembly begins. - Subassembly and Final Assembly:
Subassembly Handling: Cranes assist in lifting and positioning subcomponents such as impellers, casings, shafts, and bearings for pre-assembly.
Final Assembly: During final assembly, cranes are used to carefully position major components and align them precisely to ensure proper fit and functionality. - Testing and Quality Assurance:
Pressure Testing: Assembled pumps may undergo pressure testing to ensure they can withstand operating conditions. Cranes are used to transport pumps to testing stations and handle them during testing procedures.
Quality Inspection: Cranes aid in moving pumps to inspection areas where technicians can conduct detailed quality checks before final approval for shipment.
Techniques for Maintaining Component Integrity
Maintaining component integrity during pump assembly is crucial for ensuring the performance and reliability of the finished product. Here are some techniques employed with overhead bridge cranes:
- Careful Handling:
Gentle Lift and Lowering: Cranes equipped with precision controls allow for smooth and controlled lifting and lowering motions, minimizing the risk of damage to sensitive components.
Balanced Load Distribution: Properly distributing the load across lifting attachments or spreader bars helps prevent stress concentrations on individual components, reducing the risk of distortion or damage. - Precision Positioning:
Accurate Alignment: Cranes with precise positioning capabilities enable operators to align components accurately during assembly, ensuring proper fit and alignment.
Slow and Steady Movements: Adjustable speed controls allow operators to maneuver components slowly and precisely into place, reducing the likelihood of errors or misalignment. - Operator Training:
Proper Training: Operators undergo training to familiarize themselves with crane operation techniques and safety protocols, ensuring they handle components with care and precision.
Continuous Improvement: Ongoing training and feedback mechanisms help operators refine their skills and adapt to changing assembly requirements, improving overall efficiency and component integrity.
Case Studies/Examples of Crane Use in Pump Assembly
Case Study 1: Pump Manufacturing Facility
Challenge: A pump manufacturer faced challenges in maintaining consistent product quality and meeting production deadlines due to manual handling errors and inefficiencies.
Solution: The facility invested in overhead bridge cranes equipped with precision controls and customized lifting attachments tailored to their specific pump components.
Result: With the new crane system in place, the manufacturer achieved significant improvements in assembly accuracy, reducing errors and rework. The cranes also increased productivity by streamlining material flow and reducing idle time between assembly stages.
Case Study 2: Pump Assembly Line Optimization
Challenge: An assembly plant struggled with bottlenecks and congestion in their pump assembly line, leading to delays and increased production costs.
Solution: The plant implemented overhead bridge cranes with extended reach and load capacity to handle larger pump components and improve material flow.
Result: The crane system enabled smoother assembly processes and reduced handling times, allowing the plant to meet increased demand without compromising on quality. Operators reported improved ergonomics and reduced physical strain, leading to a safer and more efficient work environment.
In conclusion, precision handling of pump parts during assembly is essential for ensuring product quality and performance. Overhead bridge cranes play a vital role in facilitating this process by providing accurate positioning, gentle handling, and efficient material flow. Case studies demonstrate the tangible benefits of crane use in optimizing pump assembly operations and achieving better overall performance.
Typical Tonnages Used
Overview of Tonnage Requirements
Factors Determining Crane Tonnage
The tonnage requirements for overhead cranes in valve and pump assembly plants depend on various factors, including:
- Load Weight:
The primary factor influencing crane tonnage is the weight of the heaviest loads to be lifted and moved within the assembly plant.
Cranes must have sufficient capacity to handle the maximum anticipated load weight, including any safety margins. - Load Distribution:
The distribution of loads across the crane's span affects the overall tonnage requirements.
Uneven load distribution may require higher tonnage capacity to ensure stability and safety during lifting and moving operations. - Lifting Height:
The vertical distance over which loads need to be lifted and lowered impacts the crane's capacity requirements.
Cranes with higher lifting heights may require higher tonnage capacities to maintain safe and efficient operation. - Duty Cycle:
The frequency and duration of crane operation, known as the duty cycle, influence tonnage requirements.
Cranes operating continuously or handling heavy loads frequently may require higher tonnage capacities to withstand sustained use. - Environmental Conditions:
Factors such as wind loads, seismic activity, and temperature variations can affect crane performance and tonnage requirements.
Cranes operating in harsh environments or outdoor settings may require additional tonnage capacity to ensure stability and safety.
Common Tonnages for Valve and Pump Assembly
5 to 10 Tons
Typical Applications and Examples:
Valve Component Assembly: Cranes with 5 to 10-ton capacities are commonly used for lifting and positioning valve components such as bodies, bonnets, and actuators during assembly.
Subassembly Handling: These cranes assist in the subassembly of pump components, including impellers, casings, and shafts, ensuring precise alignment and fit.
Material Handling: They are utilized for transporting materials such as steel plates, pipes, and fittings within the assembly plant, supporting various stages of valve and pump production.
10 to 20 Tons
Typical Applications and Examples:
Final Assembly: Cranes with 10 to 20-ton capacities play a vital role in the final assembly of large pump units, including lifting and positioning assembled pumps onto bases or skids.
Heavy Component Handling: These cranes are used for handling heavy components such as motor units, gearboxes, and base plates during pump assembly, ensuring safe and efficient operations.
Testing and Inspection: They assist in moving fully assembled pumps to testing areas for performance testing, pressure testing, and quality inspection before shipment.
Custom and Specialized Tonnages
Situations Requiring Custom Tonnage Solutions
- Heavy-Duty Applications: Specialized applications in valve and pump assembly plants may require cranes with custom tonnage capacities exceeding 20 tons to handle exceptionally heavy loads or oversized components.
- Precise Weight Distribution: Some assembly operations may require cranes with custom tonnage capacities to ensure precise weight distribution and balance during lifting and positioning of irregularly shaped or unbalanced loads.
- Unique Facility Layouts: Cranes with custom tonnage capacities may be required to accommodate unique facility layouts, such as overhead obstacles or restricted headroom, where standard crane configurations are not suitable.
Examples of Custom Crane Applications
- Large-scale Pump Manufacturing: In facilities producing large-scale pumps for industrial applications, custom overhead cranes with tonnage capacities exceeding 20 tons may be installed to handle oversized components and assemblies.
- Specialized Testing Facilities: Testing facilities equipped with custom cranes may require specialized tonnage capacities to support the testing of exceptionally large or heavy pump units under various operating conditions.
- Automated Assembly Lines: Automated assembly lines incorporating robotic systems may utilize custom cranes with tailored tonnage capacities to support robotic handling of components and assemblies with precision and efficiency.
In conclusion, while standard tonnage capacities ranging from 5 to 20 tons are commonly used in valve and pump assembly plants for various lifting and handling tasks, specialized applications may require custom crane solutions tailored to specific requirements. Custom tonnage capacities address unique challenges and ensure the safe and efficient handling of components throughout the assembly process.
Ensuring Component Integrity
Precision Handling Techniques
Best Practices for Crane Operators
- Load Assessment: Crane operators should thoroughly assess the weight, size, and distribution of the load before lifting to ensure it falls within the crane's capacity limits.
- Smooth Movements: Operators should use smooth, controlled movements when lifting, lowering, and maneuvering loads to minimize jolts and vibrations that could damage delicate components.
- Proper Rigging: Using appropriate rigging equipment and techniques, such as slings, spreader bars, and lifting attachments, ensures even weight distribution and prevents load shifting during lifting operations.
- Communication: Effective communication between crane operators and ground personnel is essential for safe and efficient lifting operations. Clear hand signals or two-way radios should be used to coordinate movements.
- Continuous Monitoring: Operators should continuously monitor the load and crane operation throughout the lifting process, being vigilant for any signs of instability or mechanical issues.
Training and Certification Requirements
- Operator Training: Crane operators should undergo comprehensive training programs covering crane operation techniques, load handling procedures, safety protocols, and emergency response procedures.
- Certification: Operators must obtain proper certification from recognized authorities or regulatory bodies to demonstrate their competence in operating overhead cranes safely and efficiently.
- Ongoing Education: Continuous education and refresher courses help crane operators stay up-to-date with the latest industry standards, best practices, and technological advancements.
Safety Measures
Safety Protocols for Crane Operations
- Pre-Operational Checks: Before each use, operators should conduct pre-operational checks to inspect the crane's condition, including hoists, brakes, hooks, and safety devices.
- Clear Work Zones: Establishing clear work zones around crane operations helps prevent unauthorized personnel from entering hazardous areas and reduces the risk of accidents.
- Emergency Procedures: Operators should be familiar with emergency procedures, including how to safely lower a load in the event of a power failure or equipment malfunction.
Regular Maintenance and Inspections
- Scheduled Inspections: Routine inspections of overhead cranes by qualified technicians are essential to identify and address any mechanical issues or signs of wear and tear before they escalate into safety hazards.
- Maintenance Programs: Implementing regular maintenance programs, including lubrication, adjustments, and component replacements, helps ensure the crane's continued reliability and safety.
- Documentation: Maintaining detailed records of maintenance activities, inspections, and repairs provides a history of crane performance and compliance with regulatory requirements.
Technological Advancements
Automation and Control Systems
- Remote Monitoring: Advanced control systems allow operators to remotely monitor crane performance, load status, and operating conditions in real-time, enhancing safety and efficiency.
- Collision Avoidance Systems: Automated collision avoidance systems use sensors and algorithms to detect obstacles and prevent collisions, reducing the risk of accidents during crane operations.
Innovations in Crane Design for Improved Precision
- Variable Frequency Drives (VFDs): VFDs provide precise control over crane movements, allowing operators to adjust lifting speeds and accelerations to match load requirements and improve handling precision.
- Load Sensing Technology: Load sensing systems provide feedback to crane operators about the weight and balance of the load, enabling them to make informed decisions and adjustments during lifting operations.
- Advanced Positioning Systems: Cranes equipped with GPS, laser guidance, or camera systems offer enhanced positioning accuracy, allowing for more precise placement of loads and reducing the risk of errors.
In summary, ensuring component integrity during crane operations in valve and pump assembly plants requires a combination of precision handling techniques, stringent safety measures, and leveraging technological advancements. By implementing best practices, providing comprehensive training, adhering to safety protocols, and embracing innovative technologies, operators can enhance efficiency, productivity, and safety in crane operations while safeguarding the integrity of critical components.
Case Studies and Real-World Examples
In this section, we'll delve into detailed case studies and real-world examples of successful implementations of overhead cranes in valve and pump assembly plants. These examples provide valuable insights into the challenges faced, solutions implemented, lessons learned, and best practices observed.
Case Study 1: Precision Valve Manufacturing Plant
Challenges:
A precision valve manufacturing plant experienced bottlenecks and quality issues due to manual handling errors and inefficient material flow.
The plant struggled to meet production deadlines and maintain consistent product quality, leading to customer dissatisfaction.
Solution:
The plant invested in overhead bridge cranes equipped with precision controls and customized lifting attachments tailored to valve components.
They implemented automated material handling systems to streamline material flow and reduce handling time between assembly stages.
Comprehensive operator training programs were conducted to ensure operators were proficient in crane operation techniques and safety protocols.
Results:
With the new crane system and automated material handling in place, the plant achieved significant improvements in production efficiency and product quality.
Assembly times were reduced, and error rates decreased, leading to higher throughput and improved on-time delivery performance.
Employee morale improved as operators reported reduced physical strain and increased job satisfaction due to the improved working environment.
Lessons Learned:
Investing in automation and precision handling technology can yield substantial improvements in production efficiency and product quality.
Comprehensive operator training is essential to maximize the benefits of crane systems and ensure safe and efficient operation.
Continuous improvement and adaptation to changing production requirements are crucial for sustaining success in the long term.
Case Study 2: Pump Assembly Line Optimization
Challenges:
An assembly plant faced challenges with congested assembly lines and inefficient material flow, leading to production delays and increased costs.
Manual handling of heavy pump components resulted in safety hazards and ergonomic issues for operators.
Solution:
The plant implemented overhead bridge cranes with extended reach and custom lifting attachments to handle heavy pump components with precision.
They redesigned the assembly layout to optimize material flow and minimize bottlenecks, incorporating dedicated staging areas for crane operations.
Safety protocols and ergonomic improvements were introduced, including anti-fatigue mats, ergonomic workstations, and lift-assist devices.
Results:
The new crane system and optimized assembly layout improved material flow and reduced congestion on the assembly lines, resulting in shorter lead times and increased productivity.
Safety incidents decreased, and operator satisfaction improved as ergonomic improvements reduced physical strain and fatigue.
The plant achieved cost savings through reduced downtime, lower scrap rates, and improved resource utilization.
Lessons Learned:
Customized crane solutions tailored to specific application requirements are essential for optimizing material handling and assembly processes.
Ergonomic improvements and safety enhancements contribute to a safer and more productive working environment, leading to higher employee satisfaction and retention.
Continuous monitoring and evaluation of production metrics are necessary to identify areas for further improvement and maintain operational excellence.
Best Practices:
- Prioritize safety in all crane operations, ensuring compliance with regulatory standards and implementing additional safety measures as needed.
Invest in comprehensive training programs for crane operators to ensure proficiency in crane operation techniques, safety protocols, and emergency response procedures.
Regularly evaluate production processes and performance metrics to identify opportunities for improvement and implement continuous improvement initiatives.
Collaborate closely with crane manufacturers and suppliers to develop customized solutions tailored to specific application requirements and production challenges.
In conclusion, successful implementations of overhead cranes in valve and pump assembly plants demonstrate the significant benefits of precision handling technology, automation, and ergonomic improvements. By investing in advanced crane systems, optimizing assembly layouts, and prioritizing safety and employee training, manufacturers can achieve substantial improvements in production efficiency, product quality, and employee satisfaction.
Conclusion
In conclusion, the implementation of precision overhead cranes in valve and pump assembly plants plays a crucial role in ensuring component integrity, improving production efficiency, and maintaining high product quality. Throughout this exploration, several key points have emerged:
Recap of Key Points:
- Precision Handling Techniques: Employing precision handling techniques, such as accurate load assessment, smooth movements, and proper rigging, is essential for preventing damage to delicate components during crane operations.
- Safety Measures: Adhering to strict safety protocols, conducting regular maintenance and inspections, and providing comprehensive operator training are critical for ensuring safe and efficient crane operations in assembly plants.
- Technological Advancements: Leveraging technological advancements, including automation and control systems, load sensing technology, and advanced positioning systems, enhances crane precision and efficiency, leading to improved assembly processes.
Future Trends in Crane Technology for Assembly Plants:
- Integration of IoT and Data Analytics: The integration of Internet of Things (IoT) devices and data analytics capabilities into crane systems enables real-time monitoring, predictive maintenance, and performance optimization, paving the way for smarter and more efficient assembly processes.
- Advancements in Robotics: The integration of robotic systems with overhead cranes enables automated material handling, assembly, and quality inspection, further enhancing production efficiency and precision in assembly plants.
- Enhanced Safety Features: Continued advancements in safety technology, such as automated collision avoidance systems, improved operator interfaces, and enhanced ergonomic designs, contribute to safer working environments and reduced risk of accidents.
Final Thoughts on Ensuring Component Integrity Through Precision Crane Use:
Precision overhead cranes are indispensable tools for ensuring component integrity in valve and pump assembly plants. By implementing best practices, adhering to safety measures, and embracing technological advancements, manufacturers can achieve:
- Improved Product Quality: Precision handling techniques and advanced crane technology contribute to higher product quality and reduced defect rates, enhancing customer satisfaction and brand reputation.
- Increased Production Efficiency: Optimized material flow, reduced downtime, and streamlined assembly processes result in higher throughput and improved production efficiency, enabling manufacturers to meet increasing demand and stay competitive in the market.
- Enhanced Workplace Safety: Prioritizing safety in crane operations creates safer working environments, reduces the risk of accidents and injuries, and fosters a culture of safety and accountability among employees.
In essence, precision overhead cranes serve as catalysts for innovation and excellence in valve and pump assembly, driving continuous improvement and ensuring the integrity of critical components throughout the production process. As technology continues to evolve and industry standards evolve, manufacturers must remain vigilant in adopting new practices and embracing emerging trends to stay at the forefront of the industry and deliver superior products to customers.