Overhead Crane Load Capacities for Different Steelmaking Processes
Explore how overhead crane load capacities vary for steelmaking processes, ensuring optimal performance for loading, charging, and handling tasks.
Overview of Steelmaking Processes
Steelmaking involves melting down iron and adding other elements to create steel with specific properties. This process is vital because steel is incredibly strong and versatile, making it a cornerstone of modern infrastructure and manufacturing.Overhead cranes are like the heavy-duty forklifts of the steel industry, lifting and moving massive loads with ease. They handle everything from molten metal to heavy steel billets, ensuring that materials are transported efficiently within the steel plant. Imagine trying to manage all that heavy lifting by hand—it would be chaotic and dangerous!
Overhead cranes not only speed up the process but also keep everything running smoothly and safely. They’re equipped to handle extreme weights and tough conditions, which is crucial given the intense heat and heavy materials involved in steelmaking. So, if you’ve ever wondered how those giant steel beams get from one place to another in a plant, the answer is: thanks to these powerful cranes.
Basic Concepts of Overhead Crane Load Capacities
Definition and Significance
When we talk about the load capacity of an overhead crane, we're referring to the maximum weight the crane can safely lift and move. This capacity is crucial because it determines the types of materials and loads the crane can handle. Think of it as a crane's weight limit—just like a car has a maximum load it can carry, so does a crane. If you exceed this limit, you risk damaging the crane or, even worse, causing a serious accident.
Understanding load capacity is vital for ensuring that operations run smoothly and safely. It’s like knowing how much weight your truck can handle before you hit the road. Overloading a crane is not only dangerous but can also lead to costly repairs and downtime.
Factors Affecting Load Capacities
Factors that influence the load capacities of overhead cranes is crucial for safe and efficient operations.
Structural Design
The structural design of an overhead crane is fundamental to its load capacity. The design involves various components such as beams, supports, and joints, all of which need to be carefully engineered to handle the intended loads.
- Beam and Support Structure: Cranes are built with horizontal beams and vertical supports that must be robust enough to handle the weight of the load. The configuration of these structural elements affects how weight is distributed across the crane, impacting its overall stability.
- Load Distribution: A well-designed crane evenly distributes weight to prevent localized stress, which can lead to tipping or structural failure. For example, cranes with a double girder design offer better load distribution and stability compared to single girder cranes.
- Complexity of Design: The more complex the crane’s design, the more precise the engineering must be. Cranes used in high-load applications or extreme environments require intricate design considerations to ensure they meet load requirements without compromising safety.
Material Strength
The strength of the materials used in crane construction is crucial for its load-bearing capabilities.
- Quality of Materials: High-quality steel and other metals are used to ensure the crane can support heavy loads without deforming or failing. The material’s tensile strength, durability, and thickness are critical factors.
- Impact of Material Weakness: If the materials are not up to standard, the crane’s load capacity is reduced. Subpar materials can lead to bending, warping, or even catastrophic failure under heavy loads. Ensuring that materials meet industry standards is essential for maintaining safety and performance.
- Corrosion and Wear: Over time, materials can be affected by factors such as corrosion or wear, especially in harsh environments. Regular inspections and maintenance are needed to address these issues and prevent them from compromising the crane’s load capacity.
Safety Regulations
Compliance with safety regulations is not just a legal obligation; it’s a vital component of safe crane operation.
- Design and Maintenance Standards: Regulations dictate how cranes should be designed, maintained, and inspected. This includes requirements for load limits, structural integrity, and regular maintenance schedules to ensure the crane remains in safe working condition.
- Operator Training: Regulations also cover the training and certification of crane operators. Proper training ensures that operators understand how to handle loads safely and use the crane within its designed limits.
- Load Handling Practices: Adherence to safety regulations includes following best practices for load handling, such as not exceeding load limits and using appropriate rigging and attachments. This helps prevent accidents and ensures the crane performs as expected.
In summary, the load capacities of overhead cranes are influenced by several factors, including structural design, material strength, and adherence to safety regulations. A well-designed crane with high-quality materials and strict compliance with safety standards ensures safe and efficient operations. Balancing these elements helps maintain the crane’s load capacity and supports smooth, reliable performance in various industrial settings.
Steelmaking Processes and Their Specific Requirements
Basic Oxygen Steelmaking (BOS)
Typical Loads and Crane Capacities
In Basic Oxygen Steelmaking (BOS), overhead cranes are essential for handling several challenging loads due to the process's high temperature and weight requirements. Here’s a breakdown of the key loads and the corresponding crane capacities:
- Molten Metal: Molten metal in BOS can reach temperatures exceeding 1,600°C (2,912°F). This extreme heat, combined with the weight of the molten metal, necessitates cranes with robust load capacities and heat-resistant features. The high temperature makes handling molten metal particularly demanding, as the crane must resist heat damage while managing very heavy loads.
- Slag: Slag is a byproduct of the steelmaking process and is generally quite dense. Handling slag requires cranes that can deal with substantial weight and the abrasiveness of the slag material. Proper management of slag is crucial to ensure smooth operations and prevent any buildup that could impact productivity.
- Steel Billets: Steel billets are semi-finished products that are heavy and bulky. Cranes used in BOS facilities must accommodate the size and weight of these billets, ensuring they can be moved safely and efficiently from one stage of the process to another.
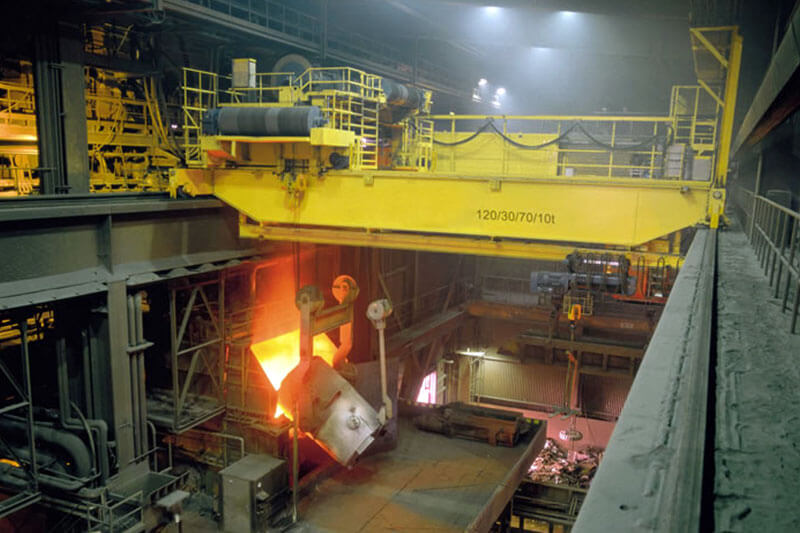
Crane Specifications
For handling the intense demands of BOS, cranes are designed with several key specifications to ensure they can operate safely and effectively:
- Load Capacities: Cranes used in BOS typically have load capacities ranging from 50 to 150 tons. This high capacity is necessary to manage the substantial weights involved in moving molten metal, slag, and steel billets. The cranes must be capable of lifting and transporting these heavy loads without compromising stability or safety.
- Structural Reinforcement: Due to the extreme conditions in BOS facilities, cranes are built with reinforced structures. This includes robust beams, supports, and joints designed to withstand both the weight of the loads and the high temperatures. The structural design is crucial for maintaining crane stability and preventing failures under heavy loads.
- Heat-Resistant Materials: Cranes in BOS are equipped with materials designed to resist high temperatures. This includes using specialized coatings and heat-resistant alloys to protect critical components from thermal damage. High-temperature resistant materials help prolong the crane’s lifespan and maintain operational efficiency.
- Specialized Cooling Systems: To manage the heat generated during BOS operations, cranes often feature cooling systems. These systems are essential for keeping the crane’s components at safe temperatures and preventing overheating, which could lead to mechanical failures or safety hazards.
In summary, overhead cranes in Basic Oxygen Steelmaking facilities are designed to handle extremely heavy and hot loads, with capacities typically ranging from 50 to 150 tons. Their specifications include reinforced structures, heat-resistant materials, and specialized cooling systems to ensure they perform effectively in the challenging conditions of the BOS process.
Electric Arc Furnace (EAF) Steelmaking
Typical Loads and Crane Capacities
In Electric Arc Furnace (EAF) steelmaking, overhead cranes are crucial for handling various heavy and high-temperature loads. Here’s a closer look at the typical loads and the necessary crane capacities:
- Scrap Metal: EAF operations frequently involve the handling of bulk scrap metal, which can be quite heavy. Cranes must be capable of managing large volumes of scrap metal efficiently, which often involves moving multiple tons of material at a time. This requires cranes with substantial load capacities and reliable hoisting systems.
- Molten Steel: The molten steel in EAF operations is similar to that in Basic Oxygen Steelmaking (BOS) in terms of temperature, reaching up to 1,600°C (2,912°F). Handling molten steel involves not only managing its weight but also dealing with its extreme heat. Cranes must be equipped to handle these high temperatures while maintaining safety and operational efficiency.
- Ladles: Ladles filled with molten steel are another critical load in EAF steelmaking. These ladles are extremely heavy and require precise control during handling. The weight of a filled ladle, combined with its high temperature, makes it essential for cranes to have precise control mechanisms and sturdy structural elements.
Crane Specifications
Crane specifications for EAF steelmaking are designed to meet the rigorous demands of handling high loads and intense conditions:
- Load Capacities: Cranes used in EAF facilities generally have load capacities ranging from 30 to 100 tons. This range is suitable for handling both the bulk scrap metal and the heavy ladles filled with molten steel. The cranes must be robust enough to manage these substantial weights consistently and safely.
- Durability and Strength: Given the intense operational environment of EAF steelmaking, cranes are built for high durability. They incorporate high-strength materials and reinforced structures to withstand both the weight and thermal stresses involved. This ensures the cranes can operate reliably over long periods without degradation.
- Advanced Cooling Systems: To cope with the extreme temperatures associated with molten steel, EAF cranes often feature advanced cooling systems. These systems help to keep the crane’s components at safe temperatures, preventing overheating and ensuring the crane remains functional and safe during high-temperature operations.
- High-Strength Materials: Cranes in EAF steelmaking are constructed using materials designed to resist high temperatures and physical stresses. This includes high-strength steel alloys and protective coatings that enhance the crane’s resilience against thermal and mechanical wear.
In summary, overhead cranes used in Electric Arc Furnace (EAF) steelmaking must be equipped to handle heavy and high-temperature loads, including bulk scrap metal, molten steel, and ladles. With load capacities typically ranging from 30 to 100 tons, these cranes are designed with durability, advanced cooling systems, and high-strength materials to ensure reliable performance in the demanding conditions of EAF operations.
Continuous Casting
Typical Loads and Crane Capacities
Continuous casting is a key process in steel manufacturing where molten steel is solidified into billets, slabs, and other semi-finished products. Here’s a breakdown of the typical loads and the corresponding crane capacities required for this process:
- Cast Billets and Slabs: In continuous casting, cast billets and slabs are solid steel products that can be quite heavy and large. Handling these items requires precision to avoid any damage during movement. The size and weight of these products necessitate cranes with substantial load capacities to manage them efficiently and safely.
- Semi-Finished Steel Products: Apart from billets and slabs, other semi-finished products might also be involved. These products vary in size and weight but generally require cranes capable of handling large, heavy loads. Proper management ensures that the products are moved smoothly from one part of the facility to another without any mishaps.
Crane Specifications
Cranes used in continuous casting operations need to be specifically designed to handle the heavy and solid products typical of this process. Here are the key specifications:
- Load Capacities: Cranes in continuous casting operations generally have load capacities ranging from 20 to 60 tons. This range is adequate for managing the substantial weights of cast billets and slabs. The crane’s capacity must be sufficient to handle these loads without compromising safety or performance.
- Precision Controls: Due to the need for careful handling of solid steel products, cranes are equipped with precise control systems. These controls allow for accurate positioning and movement of the heavy products, reducing the risk of damage and ensuring efficient operations.
- Robust Construction: Cranes in continuous casting are built with robust construction to withstand the demands of handling heavy, solid loads. This includes reinforced structural elements to ensure stability and durability under the stress of lifting and moving large products.
- Adjustable Lifting Mechanisms: Features such as adjustable lifting mechanisms are crucial for managing the varied sizes and weights of the products. These mechanisms allow the crane to adapt to different load dimensions, improving versatility and efficiency.
- Strong Hoists: The hoists used in continuous casting cranes must be strong and reliable. They are responsible for lifting and lowering the heavy products, so their strength and durability are essential for maintaining operational efficiency and safety.
In summary, cranes used in continuous casting operations must be equipped to handle heavy and large solid steel products like billets and slabs. With load capacities ranging from 20 to 60 tons, these cranes feature precise controls, robust construction, adjustable lifting mechanisms, and strong hoists to ensure effective and safe handling of substantial loads.
Induction Furnace Steelmaking
Typical Loads and Crane Capacities
In Induction Furnace (IF) steelmaking, overhead cranes are essential for managing molten metal and ladles. Here’s an overview of the typical loads and the crane capacities required:
- Molten Metal: The molten metal in Induction Furnace steelmaking is extremely hot, often reaching temperatures similar to those in other steelmaking processes. Handling molten metal involves managing both its high temperature and substantial weight. This requires cranes capable of safely lifting and transporting heavy and hot materials.
- Ladles: Ladles are used to transport and pour molten metal. They are very heavy when filled and require careful handling to avoid spillage and ensure accurate pouring. The weight of the ladles and the need for precise control during movement make the crane’s load capacity and control features critical.
Crane Specifications
Cranes used in Induction Furnace steelmaking are designed to handle the specific challenges of molten metal and ladle handling. Here are the key specifications:
- Load Capacities: Cranes in Induction Furnace operations typically have load capacities ranging from 20 to 70 tons. This range accommodates the weights of molten metal and ladles, ensuring that the crane can handle these substantial loads safely.
- Heat-Resistant Materials: To manage the extreme temperatures associated with molten metal, cranes are constructed with heat-resistant materials. This includes specialized coatings and alloys that protect the crane’s components from thermal damage, extending the crane’s operational life and maintaining safety.
- Robust Lifting Mechanisms: The lifting mechanisms of cranes used in Induction Furnace steelmaking need to be robust and reliable. They must be capable of handling heavy and hot ladles and molten metal without compromising performance. Strong hoists and durable lifting components are essential for effective operation.
- Thermal Shielding: Cranes often feature thermal shielding to protect critical components from the intense heat of molten metal. This shielding helps maintain the crane’s structural integrity and ensures safe operation in high-temperature environments.
- High-Capacity Hoists: High-capacity hoists are important for lifting and lowering heavy ladles and molten metal. These hoists need to be strong and dependable, providing the necessary lifting power while ensuring smooth and precise control of the loads.
In summary, Induction Furnace steelmaking requires cranes with load capacities ranging from 20 to 70 tons, designed to handle the heavy and hot loads of molten metal and ladles. Key features include heat-resistant materials, robust lifting mechanisms, thermal shielding, and high-capacity hoists, all crucial for safe and efficient operation in steelmaking facilities.
Specialized Overhead Cranes for Steelmaking
Heavy-Duty Cranes
Features and Benefits
Heavy-duty cranes are crucial in steelmaking due to the demanding nature of the tasks they handle. These cranes are engineered to meet the extreme challenges of the steelmaking environment, providing essential support in managing heavy loads and harsh conditions.
- Robust Design: Heavy-duty cranes are constructed with reinforced materials and robust structural components to manage the substantial weights involved in steelmaking. Whether it's molten metal, slag, or large steel billets, these cranes are designed to bear significant loads without compromising safety. Their solid construction ensures stability and prevents structural failures, even when lifting the heaviest of materials.
- Extreme Temperature Resistance: Steelmaking processes generate intense heat, making it essential for cranes to handle such conditions. Heavy-duty cranes are equipped with heat-resistant features, such as specialized coatings and cooling systems. These elements protect the crane from high temperatures, prevent overheating, and contribute to the crane’s extended lifespan. This capability ensures that cranes can operate effectively in the extreme temperatures typical of steelmaking environments.
- Enhanced Durability: Designed to endure continuous operation under strenuous conditions, heavy-duty cranes offer exceptional durability. Their robust build allows them to function reliably over long periods, reducing the frequency of maintenance and minimizing downtime. This durability is crucial in steelmaking facilities where operational efficiency and uptime are paramount.
In essence, heavy-duty cranes are the backbone of steelmaking operations. Their design, which includes reinforced materials and heat-resistant features, ensures they can handle the toughest tasks in harsh conditions. By providing reliable performance and maintaining safety, these cranes play a vital role in the efficient functioning of steelmaking facilities.
Double Girder Cranes
Advantages for Steelmaking Processes
Double girder cranes provide numerous benefits in steelmaking environments, thanks to their unique design and enhanced capabilities. Here’s a closer look at how they contribute to efficient and safe operations:
- Increased Load Capacity: The double girder design is a game-changer when it comes to lifting capacities. Unlike single girder cranes, double girder cranes can handle heavier and bulkier loads due to their robust structure. This makes them ideal for lifting large steel billets, molten metal ladles, and other substantial materials common in steelmaking. The increased load capacity ensures that even the heaviest tasks can be managed with ease, improving operational efficiency.
- Stability and Safety: One of the standout features of double girder cranes is their enhanced stability. The dual girder setup provides a more balanced distribution of weight, which significantly reduces the risk of tipping or swaying during operations. This stability is crucial when dealing with high temperatures and heavy loads in steelmaking processes. By minimizing movement and instability, these cranes enhance overall safety, protecting both the equipment and the operators.
- Smooth Operation: Precision is key in steelmaking, and double girder cranes excel in this area. Their design supports smoother and more precise control over lifting and lowering operations. This is particularly important when handling delicate or high-value materials that require careful management. The ability to control movements with greater accuracy helps prevent damage and ensures that materials are handled efficiently and safely.
In summary, double girder cranes offer substantial advantages in steelmaking. Their increased load capacity, stability, and smooth operation make them indispensable for managing heavy and precise lifting tasks. These features contribute to improved efficiency, safety, and precision in steelmaking facilities.
Overhead Crane Systems with Specialized Attachments
Types of Attachments
Specialized attachments significantly enhance the versatility and efficiency of overhead cranes in steelmaking. These attachments are tailored to handle specific tasks and materials, optimizing the performance of cranes in demanding environments.
- Ladle Cranes: Ladle cranes are equipped with ladle attachments specifically designed for the safe and efficient handling of molten steel. These attachments are crucial for transporting molten metal between different stages of the steelmaking process. They ensure precise control and secure movement, minimizing the risk of spills and enhancing operational safety. Ladle cranes are essential in maintaining smooth workflow and preventing interruptions during high-temperature operations.
- Bucket Grabs: Bucket grabs are used to handle bulk materials like slag and scrap metal. These attachments are ideal for quickly and efficiently picking up large quantities of material, making them invaluable for managing byproducts and raw materials in steelmaking. Bucket grabs streamline the workflow by enabling fast, effective material handling, which helps in maintaining the pace of production and reducing downtime.
- Magnetic Chucks: Magnetic chucks are designed for lifting and transporting ferrous materials. They use powerful magnets to securely hold and move metal objects without the need for traditional hooks or slings. This attachment is particularly useful for handling metal scraps or components in a clean and efficient manner. Magnetic chucks enhance operational efficiency by reducing the time and effort required for securing and moving metal loads.
In summary, specialized attachments for overhead cranes in steelmaking, such as ladle cranes, bucket grabs, and magnetic chucks, play a vital role in improving handling efficiency and safety. By tailoring crane systems to specific tasks, these attachments help streamline operations, manage high-temperature materials, and handle bulk or ferrous materials effectively.
Impact on Load Handling
Specialized attachments for overhead cranes have a profound impact on load handling in steelmaking, significantly improving the overall efficiency and safety of operations.
- Improved Efficiency: Attachments such as ladles and bucket grabs streamline material handling processes by enabling faster and more precise operations. For example, ladle cranes are designed to handle the heavy, molten metal with speed and accuracy, minimizing the time spent on each load. Bucket grabs efficiently manage bulk materials like slag and scrap metal, speeding up their movement from one location to another. This increased efficiency helps reduce operational delays and maintain a steady workflow, which is crucial for meeting production targets in a steel plant.
- Enhanced Safety: Using the appropriate attachment for each type of material minimizes the risk of accidents and material damage. Ladle cranes are specifically designed to manage the high temperatures and substantial weights of molten metal, ensuring safe transport and handling. Similarly, bucket grabs and magnetic chucks help in handling materials securely and effectively, reducing the chances of spills or accidents. This focus on safety not only protects the equipment but also enhances the overall safety of the steelmaking environment, safeguarding both personnel and operations.
- Versatility: Specialized attachments provide a high degree of versatility, allowing a single crane to perform a range of tasks. This adaptability is crucial in steelmaking facilities, where the needs can vary widely. For instance, a crane equipped with both ladle attachments and bucket grabs can switch between handling molten metal and bulk materials, making it a flexible tool for different aspects of the production process. This versatility helps in optimizing the use of equipment and responding to the diverse demands of steelmaking operations.
In summary, specialized overhead cranes and their attachments are essential for managing the unique demands of steelmaking. They enhance capacity, stability, and efficiency, making them indispensable for ensuring smooth, safe, and effective operations in steelmaking facilities.
Safety Considerations
Load Testing and Inspection
Regular Maintenance and Safety Checks
Ensuring the safety of overhead cranes in steelmaking requires diligent load testing and regular inspections. Load testing involves verifying that the crane can handle its maximum rated capacity without any issues. This process helps identify any potential weaknesses or defects in the crane’s structure or lifting mechanisms before they become serious problems.
Regular inspections are equally crucial. They include checking for signs of wear and tear, ensuring that all components are functioning correctly, and replacing any parts that show signs of fatigue. For instance, frequent checks on the crane’s cables, hoists, and lifting hooks help prevent failures that could lead to accidents or downtime. Maintenance schedules should be strictly adhered to, and any issues should be addressed promptly to maintain the crane’s safety and reliability.
Operational Safety Measures
Training, Procedures, and Safety Protocols
Operational safety is paramount when dealing with the high loads and extreme conditions of steelmaking. Comprehensive training for crane operators is essential. Operators need to understand not only how to control the crane but also how to handle emergency situations and recognize safety hazards. Training programs should cover crane operation, load management, and emergency response procedures.
In addition to training, well-defined safety procedures and protocols must be in place. These include standard operating procedures for different types of loads and conditions, as well as protocols for routine and emergency maintenance. Regular safety drills and refresher courses help keep the team prepared and aware of best practices, ensuring a safer working environment.
Regulations and Standards
Compliance with Industry Standards and Regulations
Compliance with industry regulations and standards is crucial for ensuring the safety and legality of crane operations. Various organizations, such as the Occupational Safety and Health Administration (OSHA) and the International Organization for Standardization (ISO), set forth guidelines for crane design, operation, and maintenance.
For example, OSHA mandates regular inspections and load testing, while ISO standards provide detailed guidelines on crane design and safety features. Adhering to these regulations not only helps avoid legal issues but also ensures that cranes operate safely and efficiently. Compliance with industry standards is a sign of a commitment to safety and quality, crucial for maintaining trust and operational integrity in steelmaking facilities.
Conclusion
In this guide, we’ve explored the critical role of overhead cranes in steelmaking and their load capacities tailored to various steelmaking processes. From Basic Oxygen Steelmaking (BOS) to Electric Arc Furnace (EAF) and Continuous Casting, each process has specific crane requirements. Heavy-duty cranes are essential for handling high loads and extreme conditions, while double girder cranes provide enhanced stability and capacity. Specialized crane systems with attachments, such as ladle cranes and bucket grabs, further optimize load handling and efficiency.