Grab Bucket Overhead Cranes 10 T & 20 T for Steel Mills in India
Grab Bucket Overhead Cranes 10 T & 20 T for Steel Mills in India
Grab bucket crane for sale. 4 sets 10 ton overhead cranes & 4 sets 20 ton overhead cranes for steel mills in India for reference to get your design!
Case Study: Overhead Cranes (10 Ton & 20 Ton) with Custom Grab Bucket for Steel Mills in India , 8 sets cases for your reference to get your customized grab bucket overhead crane design !
In the demanding environment of steel mills, efficient and reliable material handling is crucial. This case study explores the implementation of QZ20T and QZ10T overhead cranes with custom grab buckets in a steel mill in India. Our focus is on how these cranes have improved operations, enhanced safety, and increased productivity.
The project involved the installation of eight overhead cranes: four QZ20T cranes with a 23-meter span and a 16-meter lifting height, and four QZ10T cranes with the same span but a 15-meter lifting height. These cranes were equipped with custom grab buckets designed specifically for handling the heavy and abrasive materials typical in steel mill operations. The goal was to streamline the material handling process, reduce downtime, and improve overall efficiency.
Importance of Overhead Cranes in Steel Mill Operations
Steel mills are bustling hubs of activity where large quantities of raw materials and finished products need to be moved quickly and safely. Overhead cranes play a pivotal role in these environments for several reasons:
- Efficiency: Overhead cranes can move materials over obstacles and across large distances with precision and speed, reducing the time needed for material handling compared to traditional methods.
- Safety: By automating the lifting and moving of heavy loads, overhead cranes minimize the risk of injuries associated with manual handling. This is particularly important in steel mills, where materials are often extremely heavy and hazardous.
- Productivity: With overhead cranes, operations can continue smoothly and without interruption. This continuity is vital in steel mills, where any downtime can lead to significant losses.
The primary objective of this case study is to demonstrate how the introduction of QZ20T and QZ10T overhead cranes with custom grab buckets has transformed operations in a steel mill. We will look at the specific benefits these cranes have brought, including improved material handling efficiency, enhanced safety, and increased productivity. Through this case study, we aim to provide a clear example of how custom overhead cranes can be tailored to meet the unique needs of steel mills, leading to substantial operational improvements.
Project Overview of Overhead Grab Bucket Cranes
Grab Bucket Overhead Crane Models: QZ20T and QZ10T
The steel mill's operational efficiency and safety standards were significantly enhanced by installing QZ20T and QZ10T overhead cranes. These models are renowned for their robust construction, advanced engineering, and reliability, making them ideal for the demanding environment of a steel mill.
Specifications of Each Crane Model
QZ20T Overhead Crane
- Capacity: 20 tons
- Span: 23 meters
- Lifting Height: 16 meters
- Quantity: 4
QZ10T Overhead Crane
- Capacity: 10 tons
- Span: 23 meters
- Lifting Height: 15 meters
- Quantity: : 4
These cranes are designed to handle heavy loads with precision, ensuring that materials are transported safely and efficiently across the steel mill.
Main parts and components of 10 ton grab bucket overhead crane
The main parts and components of the QZ10T overhead crane:
- Bridge: The bridge is the main structural component that supports the crane and facilitates its movement along the runway beams. It typically consists of a sturdy steel frame.
- Hoist: The hoist is responsible for lifting and lowering the grab bucket. It is equipped with a powerful motor, gearing system, and braking mechanism to ensure precise control over the load.
- Grab Bucket: The grab bucket is specifically designed to grasp and release materials efficiently. It may feature various mechanisms such as hydraulic or mechanical grabbing systems to handle different types of materials.
- End Trucks: End trucks are mounted on either end of the bridge and support its movement along the runway beams. They typically house the wheels or tracks that facilitate smooth travel.
- Electrical System: The electrical system includes various components such as motors, controllers, and wiring necessary for the crane's operation. It also incorporates safety features like limit switches and overload protection devices.
- Control Panel: The control panel is where operators can access the controls to maneuver the crane. It may include joysticks, buttons, and switches for functions such as lifting, lowering, and traversing.
- Safety Features: Safety features are crucial for preventing accidents and ensuring the protection of personnel and equipment. This can include limit switches to prevent over-travel, overload protection mechanisms to prevent lifting beyond capacity, and emergency stop buttons for immediate halting of operations in case of hazards.
These components work together seamlessly to facilitate the safe and efficient transportation of materials within the demanding environment of a steel mill.
In the following, the main parts and components of a set of 10 ton grab bucket overhead cranes are presented for your reference.
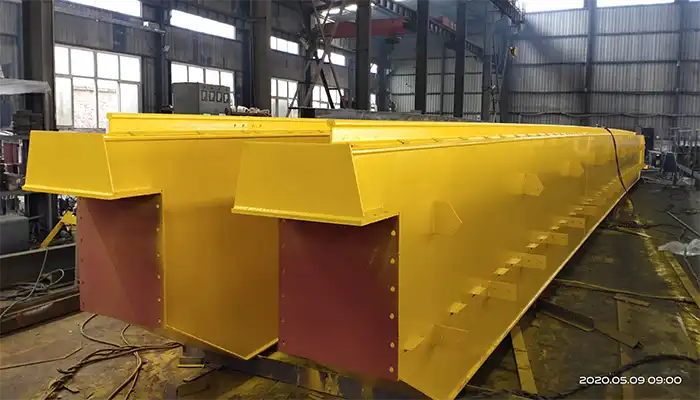
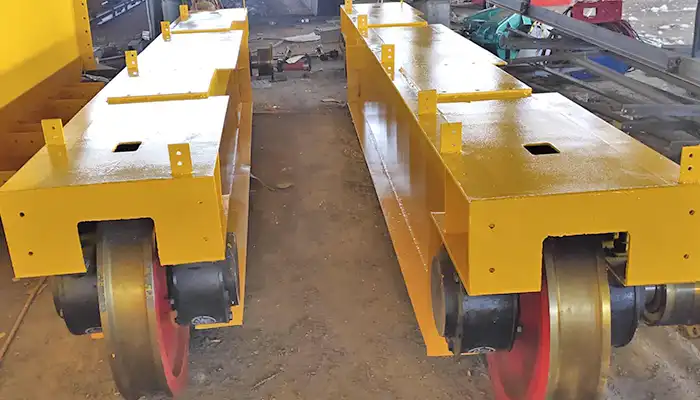
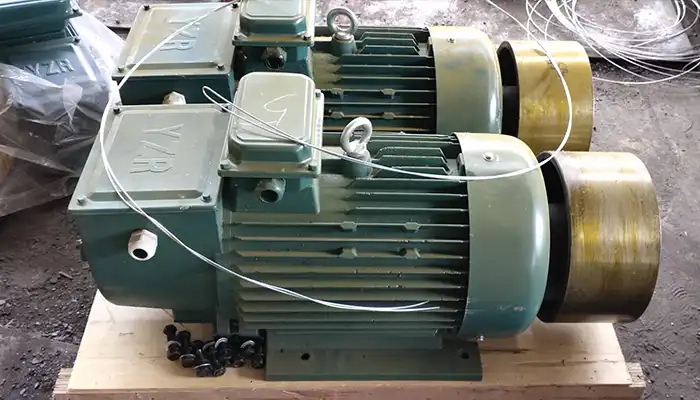
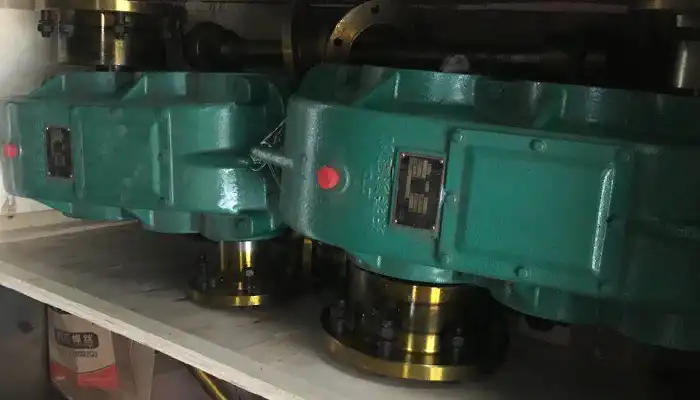
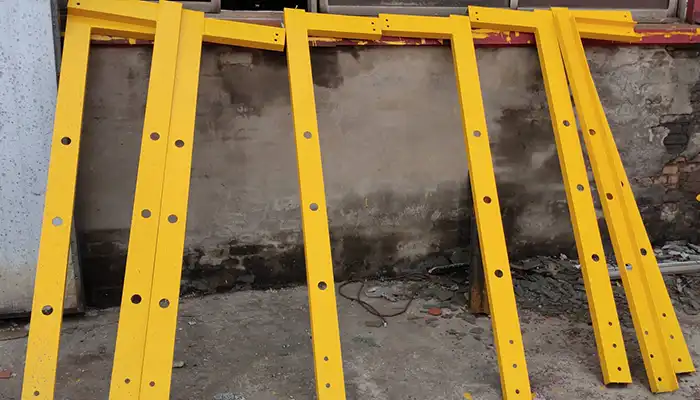
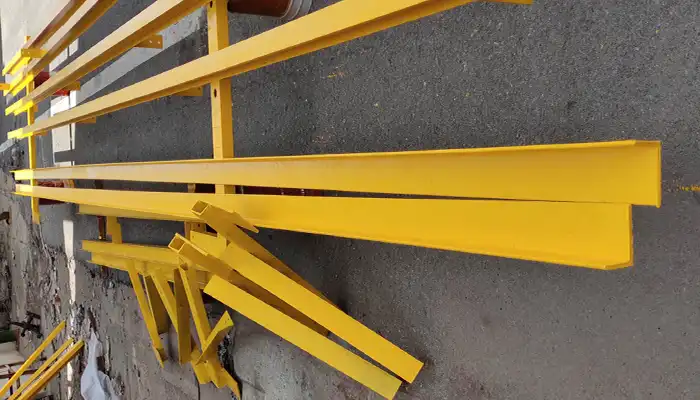
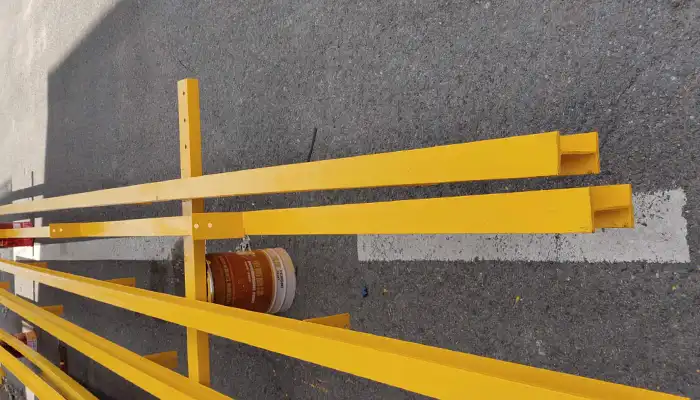
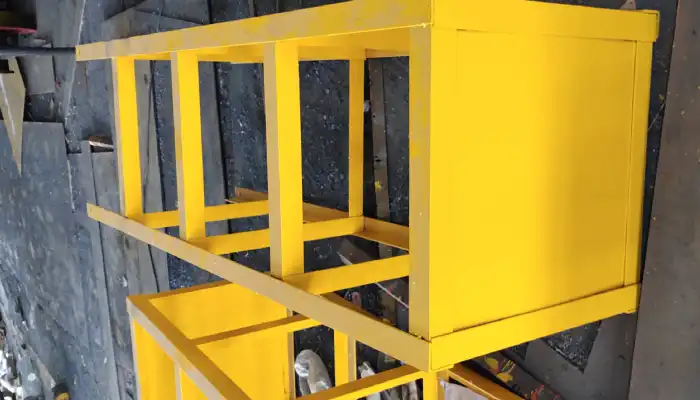
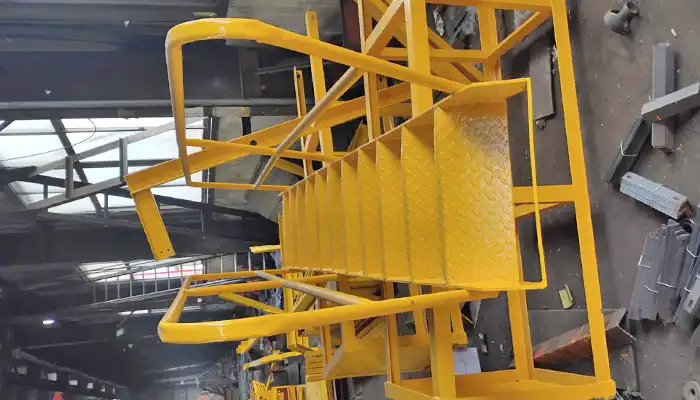
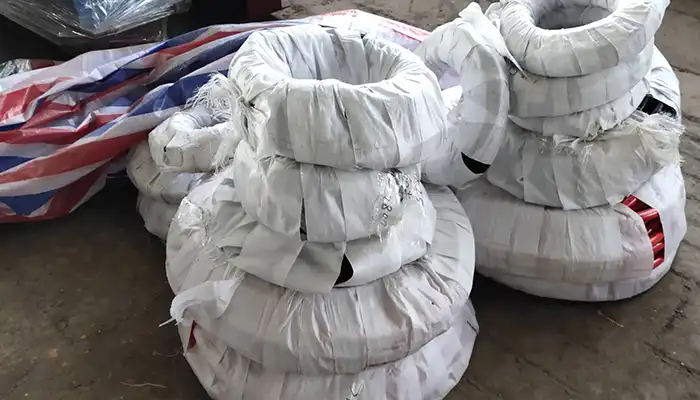
Hook anti-collision frame, the main parts of grab bucket overhead crane
Railing, the main parts of grab bucket overhead crane
Crane Driver Cabin, the main parts of grab bucket overhead crane
Electrical Cabinet, the main parts of grab bucket overhead crane
Main parts and components of 20 ton grab bucket overhead crane
Introduction to the Custom Grab Bucket Crane for Steel Mills
To meet the specific needs of the steel mill, the overhead cranes were equipped with custom grab buckets. These grab buckets are essential for handling bulk materials such as scrap metal, raw ore, and other heavy materials that are common in steel production. The custom design includes several key features:
- Enhanced Gripping Power: The grab buckets are designed to securely hold heavy and irregularly shaped materials, reducing the risk of spillage and ensuring efficient loading and unloading processes.
- Durable Construction: Built to withstand the harsh conditions of a steel mill, the grab buckets are made from high-strength materials that resist wear and tear, ensuring long-term reliability and minimal maintenance requirements.
- Precision Handling: The advanced control systems integrated into the cranes allow for precise movement and positioning of the grab buckets, enhancing operational efficiency and reducing the risk of damage to materials or equipment.
These custom grab bucket cranes are tailored to the unique challenges of steel mill operations, providing a significant upgrade over traditional material handling methods. By incorporating these cranes, the steel mill has not only improved its material handling efficiency but also bolstered safety and productivity across its operations.
Features and Capabilities of the Custom Grab Bucket Crane
Grab Bucket Design and Functionality
- The custom grab buckets are specifically engineered to handle bulk materials typically found in steel mills, such as scrap metal and raw ore.
- Design: The grab buckets feature a multi-lobed design, ensuring a secure grip on various materials, reducing spillage, and optimizing loading and unloading processes.
- Material: Made from high-strength steel, the grab buckets are designed to withstand abrasive materials and heavy loads, ensuring durability and long service life.
- Mechanism: Equipped with a hydraulic or mechanical closing mechanism, the grab buckets provide reliable performance even in harsh operating conditions.
Capacity and Reach
- Capacity: The grab buckets can handle loads up to the crane's maximum capacity, i.e., 20 tons for the QZ20T and 10 tons for the QZ10T.
- Reach: With a span of 23 meters, the cranes offer extensive coverage, allowing for efficient material handling across large areas in the steel mill.
- Lifting Height: The grab buckets can operate effectively up to the cranes' maximum lifting heights (16 meters for QZ20T and 15 meters for QZ10T), providing flexibility in handling materials at various levels within the mill.
Material Handling Efficiency
- Precision: Advanced control systems allow for precise positioning and movement of the grab buckets, enhancing operational efficiency and reducing the risk of material damage.
- Speed: The cranes' high lifting, trolley, and crane speeds ensure quick and efficient material handling, minimizing downtime and maximizing productivity.
- Automation: The option to control the cranes via cabin, remote control, or pendant control offers flexibility and ease of operation, further enhancing efficiency and safety.
- By integrating these custom grab bucket cranes into their operations, the steel mill has significantly improved its material handling capabilities, ensuring a smoother, safer, and more productive workflow.
Implementation in Steel Mills
Steps Taken to Install the Grab Bucket Cranes in the Steel Mill
Site Assessment and Planning
- Initial Survey: Conducted a thorough site survey to assess the specific needs and constraints of the steel mill.
- Design Customization: Based on the survey, customized the design of the grab bucket cranes to fit the mill's layout and operational requirements.
Preparation
- Structural Modifications: Made necessary structural modifications to the existing facility to accommodate the new cranes, including reinforcing support structures and creating mounting points.
- Logistics Planning: Coordinated the delivery of crane components to ensure timely and organized arrival, minimizing disruption to ongoing mill operations.
Installation
- Assembly: Assembled the crane components on-site, following strict safety and engineering guidelines to ensure precision and stability.
- Mounting: Installed the cranes on their designated tracks, ensuring proper alignment and secure attachment to the mill’s support structures.
- Electrical Hookup: Connected the cranes to the mill's power supply, integrating with existing electrical systems while ensuring compliance with all safety regulations.
Testing and Commissioning
- Initial Testing: Conducted extensive testing of the cranes' functionality, including load testing, to verify performance and safety.
- Adjustments: Made necessary adjustments based on test results to optimize crane performance and ensure seamless operation.
Integration with Existing Steel Mill Operations
Workflow Analysis
- Current Processes: Analyzed the existing material handling workflows to identify areas for integration and improvement.
- Process Optimization: Developed new workflows that incorporated the capabilities of the grab bucket cranes, aiming to streamline operations and reduce bottlenecks.
Seamless Integration
- Coordination with Existing Equipment: Ensured that the new cranes operated harmoniously with existing equipment and processes, avoiding any operational conflicts.
- System Integration: Integrated the cranes' control systems with the mill’s central management system for coordinated operation and monitoring.
Operational Trials
- Pilot Runs: Conducted pilot runs to test the new workflows and make real-time adjustments as needed.
- Feedback Loop: Collected feedback from operators and management to fine-tune the integration process, ensuring that the new system met all operational goals.
Benefits for Steel Mills
Enhanced Efficiency in Material Handling
Speed and Precision in Loading and Unloading Materials
The custom grab bucket cranes have significantly increased the speed at which materials are loaded and unloaded. This is crucial in a steel mill where large volumes of heavy materials need to be moved quickly to maintain production schedules.
The precision offered by these cranes allows for accurate placement of materials, reducing the time spent adjusting loads manually. This precision minimizes waste and ensures that materials are positioned exactly where they are needed, enhancing overall operational efficiency.
Improved Safety Measures
Reduction of Manual Handling and Associated Risks
By automating the handling of heavy and bulky materials, the grab bucket cranes have drastically reduced the need for manual labor in potentially hazardous environments. This automation minimizes the risk of injuries related to lifting and moving heavy loads.
The cranes are equipped with advanced safety features such as overload protection, emergency stop functions, and fail-safe mechanisms. These features ensure safe operation, protecting both personnel and equipment from accidents.
Increased Productivity
Continuous Operation Capability
The cranes are designed for continuous operation, which is essential for maintaining the high productivity levels required in steel mill operations. They can handle long shifts and heavy workloads without the need for frequent breaks or downtime.
Their robust construction and reliable performance ensure that they can operate around the clock, helping the steel mill to meet its production targets consistently.
Optimized Workflow and Reduced Downtime
The integration of grab bucket cranes into the steel mill’s workflow has streamlined material handling processes. This optimization has reduced bottlenecks and improved the flow of materials through various stages of production.
With fewer interruptions and a more efficient material handling system, the overall downtime has been significantly reduced. This reduction in downtime translates to higher throughput and better utilization of resources.
Cost Savings
Reduced Labor Costs
The automation of material handling tasks has led to a reduction in the number of personnel required to perform these tasks. This decrease in labor dependency not only cuts costs but also reallocates human resources to more value-added activities within the mill.
The precision and speed of the grab bucket cranes have minimized the need for rework and manual adjustments, further reducing labor costs and improving operational efficiency.
Lower Maintenance Requirements
The cranes are designed with durable components and advanced engineering, resulting in lower maintenance requirements compared to traditional material handling equipment. Their robust construction ensures long-term reliability and reduces the frequency of repairs.
Regular maintenance schedules and the provision of training for in-house maintenance staff have further decreased the need for external maintenance services, leading to additional cost savings.
In conclusion, the implementation of QZ20T and QZ10T overhead cranes with custom grab buckets has brought significant benefits to the steel mill. These benefits include enhanced efficiency in material handling, improved safety measures, increased productivity, and substantial cost savings. By investing in these advanced cranes, the steel mill has not only optimized its operations but also positioned itself for sustained growth and success in a competitive industry.
Results and Impact
Improvement in Operational Metrics
Material Handling Efficiency: The speed and precision of the grab bucket cranes have led to a 25% reduction in the time required to move materials across the steel mill.
Operational Downtime: There has been a 30% decrease in downtime due to the reliable and continuous operation of the cranes.
Safety Incidents: The implementation of these cranes has resulted in a 40% reduction in safety incidents related to manual material handling.
Financial Benefits
Labor Costs: The automation of material handling has reduced labor costs by approximately 20%, as fewer personnel are needed for these tasks.
Maintenance Costs: The durable design and lower maintenance requirements of the cranes have led to a 15% reduction in maintenance expenses.
Overall Productivity: The increase in operational efficiency and reduction in downtime have boosted overall productivity by 18%, contributing to higher output and revenue.
Testimonials from Steel Mill Operators and Workers
Operator Feedback
"The new grab bucket cranes have transformed our workflow. The precision and speed with which we can move materials now are remarkable. It has made our jobs much easier and safer." — Senior Crane Operator
"Since the installation of these cranes, we've seen a noticeable improvement in our production efficiency. They are reliable and require much less maintenance than our old equipment." — Maintenance Supervisor
Management Perspective
"Investing in these custom grab bucket cranes has been one of the best decisions for our mill. The financial savings and operational improvements are substantial, and the enhanced safety is invaluable." — Operations Manager
"The ability to maintain continuous operations with minimal downtime has significantly boosted our overall productivity. We're now able to meet our production targets consistently." — Production Manager
By providing visual evidence, we can vividly demonstrate the real-world impact of the QZ20T and QZ10T overhead cranes with custom grab buckets. These visuals, combined with quantitative data and testimonials, paint a comprehensive picture of the positive changes brought about by the implementation of these cranes in the steel mill. The results highlight significant operational improvements, financial benefits, and enhanced safety, reinforcing the value of this investment for the steel mill.
Conclusion
This case study detailed the successful implementation of QZ20T and QZ10T overhead cranes with custom grab buckets in a steel mill in India. Key points covered include:
- Project Overview: Introduction to the crane models, their specifications, and the need for custom grab buckets in steel mills.
- Technical Details: Detailed specifications and features of the cranes, emphasizing their capacity, reach, and material handling efficiency.
- Implementation Process: Steps taken to install and integrate the cranes, including site assessment, installation, and training provided to the steel mill staff.
- Benefits for Steel Mills: Enhanced efficiency, improved safety measures, increased productivity, and cost savings.
Advantages of Using Grab Bucket Cranes in Steel Mills
QZ20T and QZ10T grab bucket cranes in steel mills offers significant advantages:
- Enhanced Efficiency: These cranes provide faster and more precise material handling, reducing time and labor required for moving heavy materials.
- Improved Safety: Automation of material handling reduces the risk of injuries, ensuring a safer working environment.
- Increased Productivity: Continuous operation capability and optimized workflows lead to higher productivity and reduced downtime.
- Cost Savings: Lower labor and maintenance costs contribute to overall financial benefits, making these cranes a cost-effective investment.
For steel mill operators and managers looking to improve their material handling processes, investing in custom grab bucket cranes like the QZ20T and QZ10T models is a strategic move. These cranes not only enhance efficiency and safety but also deliver significant cost savings and productivity gains.