35 Ton Remote Control Overhead Crane, Custom Steel Mill Crane Qatar
35 Ton Remote Control Overhead Crane for Steel Coil Handling
The steel industry stands as a cornerstone of modern infrastructure and manufacturing, playing an indispensable role in constructing bridges, buildings, and machinery. However, at the heart of this industry lies an intricate challenge: efficient material handling within steel mills. With the colossal demand for steel production, the need for streamlined and effective handling solutions has never been more critical.
As steel coils constitute a fundamental component in steel manufacturing, their efficient movement and handling are paramount. Here enters the hero of our narrative – the Remote Control Overhead Crane specifically designed for Steel Coil Handling.
The Need for Remote Control Cranes
Traditional lifting equipment might suffice for general purposes, but when it comes to the specialized demands of steel coil handling, a paradigm shift is necessary. The sheer weight, shape, and delicacy of steel coils demand a more nuanced approach to material handling, prompting the need for purpose-built machinery.
Enter the QDX model crane, a pinnacle of innovation and engineering expertise, tailored precisely to meet the unique challenges posed by steel coil handling within the steel mill environment. Its design, manufacturing precision, and integrated technologies stand as a testament to addressing the industry-specific demands efficiently and effectively.
In the following, we'll delve deeper into the intricate facets of this revolutionary remote control double girder overhead crane design, exploring its design intricacies, manufacturing prowess, and seamless installation. Through this exploration, we aim to showcase our competence in steel mill crane design and manufacturing while highlighting the unique features that set the QDX model crane apart.
Custom Specification for Your Steel Coil Handling of the QDX Model Crane
- Lifting Capacity: The QDX model crane boasts an impressive lifting capacity of 35 tons, specifically engineered to effortlessly handle the substantial weight of steel coils. This high capacity ensures efficient movement and positioning of these heavy loads within the steel mill premises.
- Crane Span: With a crane span of 33 meters, this crane offers an extensive coverage area, enabling it to reach across vast sections of the steel mill. This wide span allows for increased flexibility in maneuvering and accessing various operational points within the facility.
- Lifting Height: The crane's lifting height of 7.7 meters ensures that steel coils can be elevated to desired levels, accommodating storage, loading, or unloading requirements seamlessly. This height provides the necessary vertical reach without compromising on stability or safety.
- Power Supply: Operating on a 380V 50Hz 3Phase power supply, the crane harnesses a robust and reliable energy source. This power configuration is ideal for sustaining the crane's performance, ensuring consistent and uninterrupted operations critical in the demanding steel mill environment.
- Crane Travelling Length: With a traveling length of 90 meters, the crane can traverse significant distances along the steel mill floor. This extensive coverage facilitates swift and precise transportation of steel coils from one point to another with minimal effort.
- Working Duty (M5): The crane's M5 working duty signifies its ability to handle heavy and intense operations continuously. It ensures the crane's durability and reliability under strenuous working conditions, characteristic of steel coil handling processes.
- Bearing Beam: Spanning 180 meters, the bearing beam provides structural support to the crane, ensuring stability and safe operation while lifting heavy loads. The design of this beam is crucial in distributing the load efficiently and preventing structural stress.
- Busbar System: Covering a length of 90 meters, the busbar system facilitates the transmission of power to the crane, ensuring smooth and efficient electrical operations throughout its operational range.
Explanation of Why These Specifications Are Crucial for Steel Coil Handling
The specifications outlined above are meticulously engineered to address the unique demands of steel coil handling within the steel mill environment. The intricate design considerations behind these specifications are paramount for several reasons:
- - Safety: The high lifting capacity, along with the crane's structural integrity, ensures safe handling of heavy steel coils, reducing the risk of accidents or mishaps.
- Efficiency: The extensive span and traveling length enable the crane to swiftly navigate the steel mill, optimizing operational efficiency by minimizing downtime and maximizing productivity.
- Reliability: The robust power supply, combined with the M5 working duty, ensures consistent and reliable performance, meeting the rigorous demands of continuous steel coil handling operations.
Each specification of the QDX model crane is purposefully tailored to enhance the efficiency, safety, and reliability of steel coil handling, setting a benchmark for specialized material handling equipment in the steel industry.
Crane Design for the Remote Control Overhead Cranes
Designing specialized cranes like the QDX model involves a meticulous process that amalgamates engineering expertise, industry insights, and innovative technologies. It commences with a comprehensive analysis of the operational requirements, considering factors such as load capacities, spatial constraints, safety standards, and environmental considerations specific to the steel mill.
The design process typically involves conceptualization, structural analysis, detailed engineering, prototyping, and rigorous testing phases. Each stage aims to refine the crane's design, ensuring optimal functionality and safety in handling the intended loads.
Specific Design Features Tailored for Steel Coil Handling
Structural Design for Heavy Lifting:
The QDX model crane's structural design is engineered to handle heavy lifting tasks efficiently. Reinforced steel components, coupled with precision engineering, provide the necessary strength and stability required for lifting and maneuvering hefty steel coils.
Safety Features for Coil Handling:
Safety remains a paramount concern in the design of the QDX model crane. Features like overload protection systems, anti-sway mechanisms, and emergency braking systems are integrated to m itigate risks associated with handling heavy loads, ensuring the safety of both the equipment and operators.
Wireless Remote Control Technology Integration:
An innovation at the heart of the QDX model crane is its seamless integration of wireless remote control technology. This advanced feature empowers operators with increased flexibility and precision in controlling the crane's movements while maintaining a safe distance from the load. The wireless remote control not only enhances operational efficiency but also ensures safer handling of steel coils by providing a clear line of sight for operators.
The incorporation of these design features in the QDX model crane signifies a thoughtful approach towards addressing the specific challenges posed by steel coil handling. By prioritizing structural robustness, safety, and technological advancements, the crane stands as a testament to cutting-edge design tailored explicitly for the demanding steel mill environment.
Manufacturing Process of Remote Control Overhead Crane 35 Ton
Insight into the Manufacturing Stages for the QDX Model Crane
The manufacturing of the QDX model crane is a comprehensive process that integrates precision engineering and state-of-the-art manufacturing techniques. It traverses several distinct stages, starting from the procurement of raw materials to the assembly and final testing of the crane.
- Design Translation: The meticulously crafted design specifications undergo translation into manufacturing blueprints and technical drawings. These serve as the guiding framework for the production stages.
- Material Procurement and Preparation: The selection of high-quality materials, including robust steel components and cutting-edge electrical systems, is paramount. Rigorous quality checks are conducted to ensure the integrity and reliability of the materials used in crafting the crane.
- Fabrication and Assembly: Skilled technicians and engineers adeptly fabricate and assemble the crane components according to the design specifications. Each part undergoes precision manufacturing processes to ensure accuracy and compatibility during assembly.
Installation of Control Systems: Integration of the advanced wireless remote control system is meticulously executed, ensuring seamless connectivity and flawless operation of the crane's controls.
Material Selection and Quality Control Measures
Material selection plays a pivotal role in determining the crane's durability, reliability, and operational efficiency. Only materials meeting stringent industry standards are employed in the construction of the QDX model crane. High-grade steel for structural components, durable electrical systems, and cutting-edge control mechanisms form the backbone of this crane's construction.
To maintain uncompromised quality, stringent quality control measures are implemented at every manufacturing stage. Comprehensive inspections, material testing, and adherence to industry-specific standards and regulations ensure that each component meets the highest quality benchmarks.
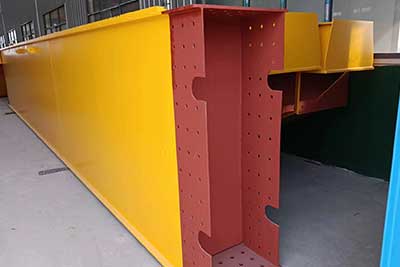
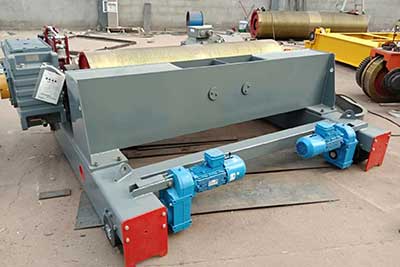
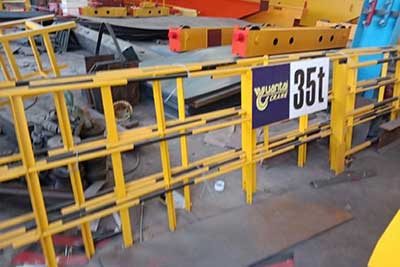
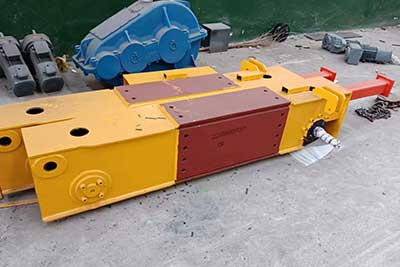
Click to chek more production pictures of 35 ton remote control overhead cranes for sale Qatar
Testing Procedures to Ensure Reliability and Safety
The QDX model crane undergoes a series of rigorous tests and inspections to guarantee its reliability and safety under real-world operating conditions. These tests encompass functionality checks, load testing, stress testing, and operational simulations to validate its performance.
Furthermore, safety protocols and compliance assessments are conducted to ensure that the crane adheres to industry safety standards. This includes verifying the efficacy of safety features, emergency systems, and wireless remote control functionalities.
The culmination of these manufacturing stages, meticulous material selection, and comprehensive testing procedures reinforces the reliability, durability, and safety of the QDX model crane, setting it apart as a pinnacle of engineering excellence tailored for steel coil handling in the most demanding industrial settings.
Installation and Integration
Challenges and Considerations During Installation
- The installation of the QDX model crane within a steel mill environment presents several unique challenges that require meticulous planning and execution. Challenges may include:
- Space Constraints: Maneuvering large crane components within confined spaces of the steel mill demands careful coordination and precision during installation.
- Safety Regulations: Adhering to strict safety protocols and ensuring compliance with industry standards while installing heavy machinery within an operational steel mill is crucial.
- Minimal Disruption: Minimizing disruptions to ongoing operations during the installation process to prevent downtime and maintain production efficiency.
Integration of the Crane into the Steel Mill Environment
Integrating the QDX model crane seamlessly into the steel mill environment involves a systematic approach to ensure optimal functionality and minimal disruption to operations. Key steps include:
- Site Preparation: Assessing the installation site to ensure it meets safety requirements and provides adequate structural support for the crane's assembly.
- Assembly and Rigging: Methodical assembly of the crane components using specialized rigging equipment and techniques to ensure precise alignment and structural integrity.
- Electrical Integration: Connecting the crane to the power supply and integrating the electrical systems, including the busbar system, to ensure seamless power transmission.
- Environmental Adaptation: Customizing the crane's settings and configurations to suit the specific operational needs and environmental conditions of the steel mill.
Testing and Calibration of the Wireless Remote Control System
- Post-installation, comprehensive testing and calibration of the wireless remote control system are imperative to guarantee flawless operation and safety. Steps involved include:
- Functional Testing: Verifying the functionality of all crane operations through the wireless remote control, ensuring precise control over movements and load handling.
- Range and Signal Testing: Conducting tests to ascertain the range and signal strength of the remote control system in various operational scenarios within the steel mill.
- Calibration: Fine-tuning the remote control system for optimal performance, including sensitivity adjustments and ensuring synchronization between control inputs and crane movements.
The meticulous installation, seamless integration, and rigorous testing and calibration of the wireless remote control system reinforce the QDX model crane's reliability, safety, and efficiency within the dynamic and demanding steel mill environment.
Our Expertise and Competence
Our company stands as a beacon of innovation and excellence in the design and manufacturing of specialized cranes for industrial applications. With decades of experience and a team of seasoned engineers and technicians, we have continually pushed the boundaries of crane technology to meet the evolving needs of various industries, including the demanding steel sector.
Our expertise lies in the ability to conceptualize, design, and deliver bespoke crane solutions tailored to the unique requirements of our clients. Through a meticulous blend of engineering acumen, cutting-edge technologies, and a deep understanding of industrial workflows, we have consistently delivered cranes that exceed expectations in performance, reliability, and safety.
The QDX model crane stands at the pinnacle of our innovative solutions. Its unique features and benefits include:
- - Precision Engineering: The crane's design is a result of meticulous engineering, ensuring optimal performance and durability in handling heavy steel coils.
- Advanced Safety Measures: Incorporation of cutting-edge safety features guarantees a secure operating environment, minimizing risks and ensuring the safety of both operators and equipment.
- Wireless Remote Control: The integration of a wireless remote control system provides operators with enhanced control and maneuverability, increasing efficiency and safety in material handling processes.
- Customizability: The QDX model crane can be customized to suit specific operational requirements, ensuring seamless integration into various steel mill environments.
The QDX model crane's advanced features and benefits not only enhance operational efficiency but also underscore our commitment to delivering top-tier solutions that redefine industry standards.