Unmanned 16-Ton Overhead Crane with Grab Buckets for Sand Silo
A 16-ton unmanned overhead crane automates sand silo filling in a nickel smelting plant, enhancing efficiency and reducing labor needs.
Executive Summary
Introduction to the Project
A nickel smelting plant in Gansu needed a more efficient way to handle bulk materials for its filling sand silo. The plant used three 16-ton overhead grab bucket cranes to transport materials. However, the harsh working conditions and labor shortages made manual operation increasingly difficult.
To solve these challenges, the company decided to upgrade to an unmanned crane system with 5G intelligent control. This transformation allowed for fully automated material handling, reducing the need for operators while improving efficiency and safety.
16 ton double girder overhead crane with grab bucket for bulk material handling
Key Objectives
The main goals of this upgrade were:
- Automation: Enable unmanned operation of the cranes.
- Efficiency: Improve material transport speed and reduce downtime.
- Cost Reduction: Minimize labor costs and lower long-term maintenance expenses.
- Safety Enhancement: Eliminate human exposure to dusty, high-risk environments.
Overview of the 5G-Based Intelligent Control System
The upgraded system introduced a 5G network to enable real-time communication between cranes and the control center. This allowed for:
- Precise Coordination: Cranes worked together efficiently, avoiding collisions and optimizing material flow.
- Remote Monitoring & Control: Supervisors could oversee operations from a control room, reducing the need for on-site staff.
- Smart Path Planning: The system adjusted crane movements based on workload, ensuring smooth operation even during peak production.
With these upgrades, the plant successfully transitioned to a fully automated, data-driven material handling system. This not only boosted productivity but also ensured stable and reliable operations in a challenging environment.
Background & Challenges
Company Profile
The project took place at a nickel smelting plant in Gansu, China. This facility processes large amounts of raw materials daily, requiring efficient and reliable handling systems. One critical step in the production process is filling the sand silo, where bulk materials are transported from storage pits to feeding points.
To handle this task, the plant relied on three 16-ton overhead grab bucket cranes. These cranes played a key role in keeping production running smoothly. However, manual operation presented several challenges, making it difficult to maintain efficiency and safety.
Existing Challenges
Harsh Working Conditions
- The environment was tough—high temperatures, constant dust, and heavy loads made operations difficult.
- Workers had to operate cranes in these conditions, increasing the risk of fatigue and errors.
Labor Shortages
- Hiring and retaining skilled crane operators was increasingly difficult.
- Many workers were unwilling to work in hazardous, high-dust environments.
- Labor costs continued to rise, making manual operation expensive.
Inefficiencies in Manual Operation
- Operators relied on experience rather than precise data, leading to inconsistent material handling.
- Crane coordination was a challenge—without automation, avoiding collisions and optimizing routes was difficult.
- Manual control often resulted in unnecessary energy consumption, increasing operating costs.
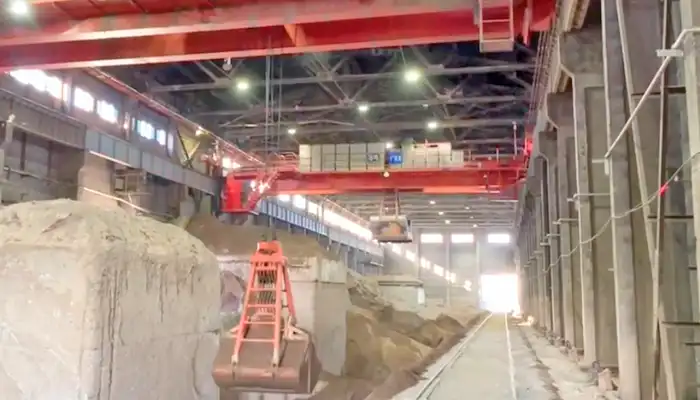
Clamshell grab bucket overhead crane 16 ton with intelligent control and automatic control
Need for an Unmanned Crane Solution
To address these issues, the company decided to upgrade to an intelligent, unmanned crane system. This transformation aimed to:
Reduce Labor Dependency
- Eliminate the need for on-site operators.
- Enable remote monitoring and automated control.
Improve Precision & Operational Consistency
- Use smart algorithms and sensors to optimize material handling.
- Ensure accurate and efficient movement, reducing waste and downtime.
Enhance Safety & Optimize Logistics
- Remove workers from dangerous environments, reducing accidents.
- Enable multi-crane coordination to improve efficiency and avoid collisions.
- Use real-time data and automation to adjust crane operations based on production demand.
With these goals in mind, the company moved forward with a 5G-based intelligent control system, transforming its material handling process.
Project Scope & Implementation
Crane Specifications
To improve efficiency and automate material handling, the plant upgraded its 16-ton overhead grab bucket cranes with advanced control systems. The project included:
- Multi-crane synchronized operation: All three cranes now work together, ensuring smooth material flow without collisions.
- Unmanned operation: The system eliminates the need for on-site operators, relying on automation for precise handling.
Technology Upgrades
Electrical Control System Overhaul
To improve performance and reliability, the cranes' electrical systems were completely upgraded. Key improvements included:
Thyristor switch drive for hoisting & grab control
- Replaced the old resistor-based system, reducing energy loss.
- Provided smoother and more efficient control over lifting and material grabbing.
VFD (Variable Frequency Drive) for bridge and trolley motion
- Allowed precise speed control, reducing mechanical stress.
- Improved energy efficiency and reduced wear and tear on components.
Siemens S7-1500 PLC for automation
- Enabled real-time logic control for crane movement.
- Allowed seamless integration with 5G and intelligent algorithms.
Integration of 5G Technology
A major part of the project was the adoption of 5G communication, ensuring faster and more reliable data transmission. This provided:
Real-time remote control and monitoring
- Operators could oversee crane operations from a control room, improving safety.
- Reduced human intervention, minimizing errors and inefficiencies.
Seamless communication between cranes for coordinated operation
- Cranes adjusted movements automatically to avoid collisions.
- Optimized material flow based on production needs, improving efficiency.
With these upgrades, the plant successfully transitioned to a fully automated, intelligent crane system, ensuring smoother operations, lower costs, and improved workplace safety.
Key Features & Functionalities
The unmanned 16-ton overhead grab bucket crane comes with several intelligent features that improve efficiency, safety, and precision. Below are the key functionalities that make this system a game-changer for the nickel smelting plant.
Real-Time Virtual Simulation & 3D Material Imaging
To improve monitoring and decision-making, the system provides a real-time digital representation of crane operations and material flow.
- Live visualization – The system creates a virtual model of the worksite, allowing remote operators to see crane movements and material positions in real time.
- Material tracking – It continuously tracks the location, volume, and distribution of bulk materials.
- Data analysis – The system collects and analyzes operational data, helping managers identify inefficiencies and optimize processes.
- Predictive insights – By studying trends, the system provides reports and recommendations, helping operators make informed decisions.
Multi-Crane Coordination & Optimized Path Planning
With multiple cranes working together, coordination and collision prevention are essential for smooth operations.
- Synchronized movement – The cranes communicate with each other to avoid collisions and work together efficiently.
- Workload distribution – The system assigns tasks to cranes based on production needs, ensuring no crane is overloaded or idle.
- Automatic adjustments – It dynamically changes the material placement strategy to optimize space and workflow.
- Peak-time efficiency – During high production periods, the system prioritizes speed and efficiency, preventing delays.
Anti-Sway & Load Stability System
A common issue with overhead cranes is load swinging, which can slow down operations and cause accidents. The new system reduces these risks by keeping loads stable.
- Automatic sway control – The system detects load weight and movement speed, adjusting crane actions to reduce swinging.
- Smooth lifting and lowering – It gradually accelerates and decelerates, preventing sudden movements that could damage materials.
- Adaptive speed control – Based on load size and travel distance, the crane automatically adjusts its motion for better efficiency.
- Improved safety – With reduced swinging, the risk of load spills and structural stress is significantly lower.
Advanced Radar-Based Material Recognition
In a dusty smelting environment, traditional sensors struggle to detect materials accurately. The upgraded system uses radar-based recognition to ensure precision.
- High-accuracy material detection – The radar system scans bulk materials, identifying them even in poor visibility conditions.
- Material classification – It distinguishes different materials and adjusts the grab bucket accordingly for better handling.
- Optimized sorting – The system ensures materials are placed in the right location, preventing misplacement and waste.
- Adaptive gripping force – The crane automatically adjusts the grip strength based on material density, reducing damage and improving efficiency.
Digital Operations & Predictive Maintenance System
A key improvement is the integration of digital monitoring and predictive maintenance, ensuring that cranes stay in top condition.
- Real-time condition monitoring – The system tracks motor performance, wire rope health, and overall crane condition.
- Early fault detection – Sensors detect wear and tear before breakdowns occur, allowing for timely maintenance.
- Automated diagnostics – When an issue arises, the system identifies the problem and suggests solutions, reducing downtime.
- Longer equipment lifespan – By performing preventive maintenance, the system extends the life of mechanical and electrical components.
Conclusion
With these intelligent features, the unmanned crane system has transformed material handling at the nickel smelting plant. It has:
- Increased efficiency by improving coordination and optimizing workflow.
- Reduced costs by cutting labor expenses and minimizing downtime.
- Enhanced safety by removing human exposure to harsh working conditions.
- Improved reliability with predictive maintenance and smart automation.
This fully automated system ensures stable, efficient, and intelligent operations, setting a new standard for industrial material handling.
Remote controlled overhead crane to ensure safety and efficiency
Project Results & Impact
The unmanned 16-ton grab bucket crane brought significant improvements in efficiency, cost savings, and safety. Below are the key results observed after implementation.
Operational Efficiency Gains
The shift to unmanned crane operation streamlined material handling and improved overall efficiency.
- Reduced labor costs – Eliminating the need for crane operators cut down labor expenses and solved the challenge of workforce shortages.
- Faster material handling – The automated system optimized movement paths, reducing cycle times and improving material transfer speed.
- Higher accuracy – The smart control system ensured precise material placement, minimizing rework and increasing overall productivity.
Cost Savings & ROI
By upgrading to an intelligent control system, the plant significantly reduced operational costs while maximizing returns.
- Saved nearly 1 million yuan – The project avoided expensive mechanical modifications by improving control systems and automation.
- Optimized logistics – Better material flow management reduced unnecessary movement and idle time, improving production efficiency.
- Reduced material waste – The radar-based recognition system ensured accurate handling, preventing material loss and misplacement.
- Lower maintenance costs – Predictive maintenance helped prevent breakdowns, reducing repair expenses and unexpected downtime.
Enhanced Safety & Reliability
The automated system removed human workers from dangerous environments and improved equipment performance.
- Eliminated manual operation risks – Workers no longer needed to operate cranes in a harsh, dusty, and high-temperature environment.
- Improved equipment lifespan – Smooth acceleration, anti-sway control, and predictive maintenance reduced mechanical wear and tear.
- Stable and reliable performance – Continuous system monitoring ensured consistent operation without unexpected failures.
With these improvements, the unmanned crane system has successfully enhanced efficiency, reduced costs, and created a safer work environment. This project demonstrates how intelligent automation can revolutionize material handling in heavy industries.
Conclusion & Future Prospects
The unmanned 16-ton grab bucket crane project has proven to be a major success, delivering significant improvements in efficiency, cost savings, and safety at the nickel smelting plant. The integration of 5G intelligent control and automation has transformed material handling, providing a more reliable, accurate, and safe operation.
Summary of Project Success and Long-Term Benefits
The project achieved all key objectives, including:
- Increased operational efficiency through unmanned operations and optimized material handling.
- Substantial cost savings, including nearly 1 million yuan saved in upgrades and reduced operational expenses.
- Enhanced safety by removing human operators from dangerous environments and preventing accidents.
- Improved reliability and equipment longevity thanks to predictive maintenance and smoother crane operation.
These benefits position the plant for continued growth and improvement, ensuring long-term success and sustainability.
Potential for Expansion to Other Processes
The success of this project opens the door for expanding the 5G intelligent crane system to other parts of the smelting plant. Future applications could include:
- Automating other material handling tasks in different areas of the plant, such as slag or ore transfer.
- Integrating the unmanned crane system into additional workshops, where similar challenges with harsh environments and labor shortages exist.
- Enhancing other crane operations with smart monitoring and predictive capabilities, leading to better overall plant performance.
Scalability and Replication in Similar Industries
The success of the unmanned crane system is not limited to the nickel smelting plant. The technology is highly scalable and replicable for industries that handle bulk materials, including:
- Steel mills, cement plants, and mining operations, where heavy material handling and harsh working conditions are common.
- Other manufacturing plants seeking to reduce labor costs and improve operational efficiency through automation.
- Ports and logistics facilities handling large quantities of bulk goods, where precision and coordination are crucial.
This project demonstrates that with the right technology, automation can be applied across a wide range of industries, helping to reduce costs, improve safety, and boost productivity.
The unmanned crane system at the nickel smelting plant is a successful example of how advanced automation and 5G technology can improve heavy industry operations. With its proven benefits and potential for expansion, this project sets the stage for future innovations and scalable solutions in material handling across various industries.