What kinds of crane buffers are there? What are their characteristics?
Due to the high operating speed of the crane, in order to protect the crane and the building frame, when the crane collides with the end of the track (or with another crane) column, it must be ensured that the crane can stop relatively smoothly without causing a violent impact. This is a buffer The role of the device. The buffer is set at the position where the cart or the trolley collides with the blocking body. The buffer should also be set between the cranes running on the same track and between the two trolleys on the same crane.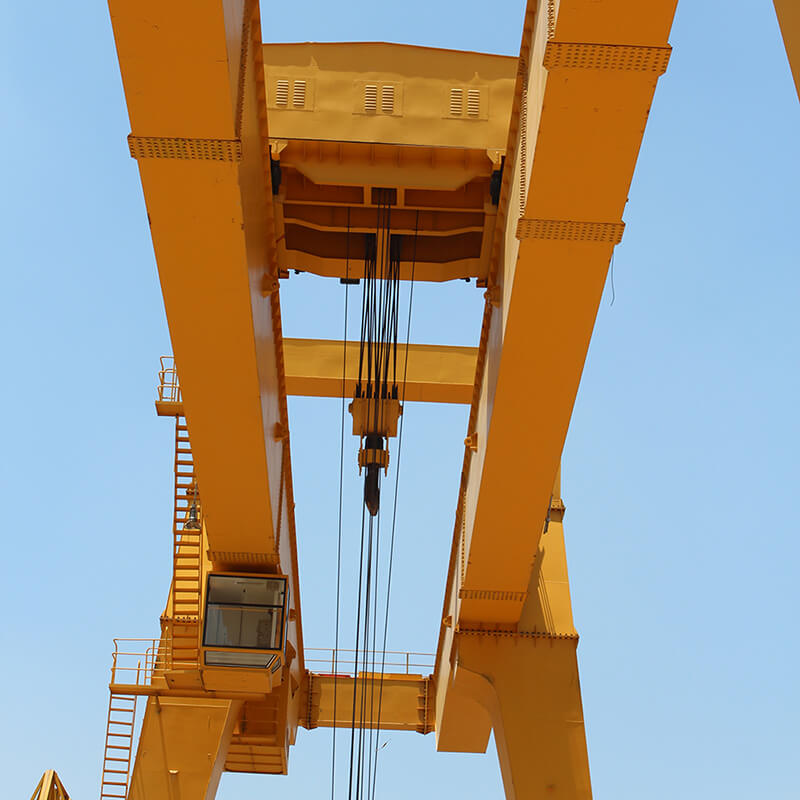
There are many types of crane buffers. Commonly used are spring buffers, rubber buffers, hydraulic buffers, and polyurethane foam plastic buffers.
①Spring bufferThe spring buffer is mainly composed of bumper, compression spring and shell spring parts. Figures 2-26 and 2-27 are the spring buffer of the big car and the spring buffer of the small car respectively.
The advantages of spring buffers are simple structure, reliable use, and can work normally at low temperatures. The outstanding shortcoming is that the back pressure is large, which causes rebound impact on the crane. The higher the running speed, the more serious the rebound phenomenon, so this kind of buffer can only be used on the crane with the running speed of 50-120m/min.
②Rubber buffer
The advantage of rubber buffer is low cost and no maintenance. The disadvantage is that the energy absorption is limited, and it is affected by the environment. The rubber is easy to age and has a low life. Therefore, it is only suitable for cranes with a speed of less than 50m/min, and the ambient temperature is in the range of -30-50 degrees.
③Hydraulic buffer
The hydraulic buffer is composed of ejector rod, working cavity and oil storage cavity. Its structure is shown in Figure 2-29.
The buffer fluid of the hydraulic buffer is kerosene with water or transformer oil. The buffer solution should be filtered when it is loaded, and no impurities should be mixed in. At the same time, it must be ensured that all the air is discharged.
The working principle of the hydraulic buffer is that when a collision occurs, the liquid in the working cavity flows into the oil storage cavity through numerous small holes in the cylinder liner, and the damping effect of the small holes absorbs the kinetic energy of the moving body and changes into the potential energy of the liquid. When the crane leaves, it returns to its original position under the action of the return spring, and the liquid flows back into the working chamber at the same time.
Hydraulic buffer can absorb large impact kinetic energy, and there is no rebound phenomenon, which is suitable for cranes with operating speeds greater than 120m/min. The disadvantage is that the structure is complicated and affected by temperature, sometimes causing oil leakage. In order to overcome these shortcomings, a granular working medium is designed to be steel balls. When the crane collides, the kinetic energy of the collision is absorbed by the working medium of the spring, and the original position is restored under the action of the spring after the collision. Practice has proved that this buffer has a smooth force curve and recoil force, which can stop the crane smoothly and reset slowly.
In addition, polyurethane foamed plastic buffers with simple structure and low cost have been used on cranes. Its appearance is shown in Figure 2-31. In the crane operating at a high speed of 120-160m/min, infrared reflectors, ultrasonic waves, excitation lines and other devices are also used to slow down and stop before collision to protect the crane from excessive impact.