Advanced Materials and Coatings for C Hooks for Your Needs
Advanced materials and coatings for C Hooks for your needs. Explore cutting-edge materials and coatings for C hooks, enhancing durability, strength, and efficiency in material handling across various industries.
C Hooks Construction: Explore Cutting-Edge Materials and Coatings for C Hooks
C hooks might seem like a small component in the grand machinery of industries, but their significance is immeasurable. Found in various sectors from manufacturing to logistics, C hooks play a crucial role in lifting and transporting heavy loads. However, what keeps these hooks reliable and durable amidst rigorous operations? The answer lies in the materials and coatings used in their design.
C hooks are versatile tools utilized across multiple industries, including automotive, construction, and warehousing. Their distinctive C-shaped design allows for efficient handling of loads, making them indispensable in material handling processes. Whether it's moving steel coils in a manufacturing plant or transferring goods in a distribution center, C hooks ensure smooth and safe operations.
But why are materials and coatings so vital in the design of C hooks? The answer is simple yet profound: durability and performance. The materials used in constructing C hooks determine their strength, weight-bearing capacity, and resistance to wear and tear. Meanwhile, coatings provide additional protection against corrosion, abrasion, and other forms of damage, extending the lifespan of the hooks and enhancing their efficiency.
In the following, the following main questions will be talked about:
- What are the different types of advanced materials suitable for C hooks, and how do they compare in terms of strength, durability, and cost?
- What are the common types of coatings used in C hook design, and how do they contribute to enhancing performance and longevity?
- What are the challenges and limitations associated with the adoption of advanced materials and coatings in C hook manufacturing, and how can these be mitigated?
- What are the potential future directions and innovations in this field, and how might they reshape the landscape of material handling technology?
By answering these questions, we hope to provide actionable insights that empower industry professionals to make informed decisions regarding the selection, design, and maintenance of C hooks. Ultimately, our goal is to contribute to the development of more robust, efficient, and sustainable material handling solutions that drive productivity and profitability across diverse industrial sectors.
Advanced Materials for C Hooks:
Advanced materials refer to substances engineered at the molecular or atomic level to exhibit superior properties compared to traditional materials. These materials often possess exceptional strength, durability, lightweight nature, and resistance to harsh environmental conditions. Advanced materials are designed to meet the evolving demands of modern industries, offering enhanced performance and efficiency in various applications.
Types of Advanced Materials Suitable for C Hooks:
High-Strength Alloys: High-strength alloys are engineered metallic materials that combine multiple elements to achieve remarkable mechanical properties. These alloys exhibit exceptional tensile strength, hardness, and fatigue resistance, making them ideal for applications requiring heavy-duty performance. Common examples include stainless steels, titanium alloys, and nickel-based superalloys. High-strength alloys offer the advantage of withstanding high loads while maintaining structural integrity, making them well-suited for C hook applications in heavy industries such as steel manufacturing and shipbuilding.
Composite Materials: Composite materials are composed of two or more distinct constituents with complementary properties, combined to create a synergistic material with superior performance characteristics. These materials often consist of a reinforcing phase (such as fibers or particles) embedded in a matrix material (such as polymers or metals). Composite materials offer exceptional strength-to-weight ratios, corrosion resistance, and tailored mechanical properties, making them suitable for lightweight and high-strength applications. In the context of C hooks, composite materials offer the advantage of reduced weight without compromising strength, resulting in enhanced lifting capacity and energy efficiency.
Nanomaterials: Nanomaterials are engineered substances with dimensions on the nanometer scale, offering unique properties and functionalities attributed to their nanoscale architecture. These materials include nanoparticles, nanotubes, nanocomposites, and nanocoatings, among others. Nanomaterials exhibit enhanced mechanical, electrical, thermal, and optical properties compared to their bulk counterparts, making them highly desirable for various industrial applications. In the realm of C hooks, nanomaterials can be employed to enhance strength, wear resistance, and corrosion protection through innovative surface modifications and reinforcements.
Advantages of Using Advanced Materials in C Hooks:
The utilization of advanced materials in C hook design offers several significant advantages:
- Enhanced Strength and Durability: Advanced materials provide superior mechanical properties, including higher tensile strength, hardness, and fatigue resistance, ensuring reliable performance under demanding operational conditions.
- Lightweight Design: Advanced materials enable the construction of lightweight C hooks without compromising load-bearing capacity, resulting in reduced energy consumption and operational costs.
- Corrosion and Wear Resistance: Many advanced materials offer inherent resistance to corrosion, oxidation, and wear, prolonging the service life of C hooks and minimizing maintenance requirements.
- Tailored Properties: Advanced materials can be engineered to meet specific application requirements, allowing for the customization of C hook designs to optimize performance and efficiency.
- Sustainability: Some advanced materials offer eco-friendly alternatives to traditional materials, contributing to sustainable manufacturing practices and environmental stewardship.
By leveraging the unique properties of advanced materials, manufacturers can develop C hooks that deliver unparalleled performance, reliability, and longevity, thereby enhancing productivity and safety in material handling operations across various industries.
Coatings for C Hooks:
Coatings play a critical role in enhancing the performance and longevity of C hooks by providing an additional layer of protection against various forms of damage. These coatings act as a barrier between the hook's surface and external elements, mitigating corrosion, abrasion, and thermal degradation. By preserving the integrity of the hook's material and preventing surface deterioration, coatings contribute to prolonged service life, reduced maintenance requirements, and improved operational efficiency.
Common Types of Coatings Used for C Hooks:
- Corrosion-Resistant Coatings: Corrosion-resistant coatings are designed to protect C hooks from degradation caused by exposure to corrosive environments, such as moisture, chemicals, and salts. These coatings typically consist of zinc-rich primers, epoxy coatings, or specialized polymer blends that form a durable barrier against corrosive agents. By inhibiting the formation of rust and corrosion on the hook's surface, corrosion-resistant coatings help maintain structural integrity and prevent premature failure.
- Abrasion-Resistant Coatings: Abrasion-resistant coatings are formulated to withstand the mechanical wear and tear experienced by C hooks during handling and lifting operations. These coatings are commonly composed of hard particles, such as ceramics or tungsten carbide, dispersed within a tough resin matrix. By enhancing the hook's surface hardness and toughness, abrasion-resistant coatings reduce friction, minimize surface damage, and extend the service life of the hook in abrasive environments.
- Thermal Barrier Coatings: Thermal barrier coatings are applied to C hooks operating in high-temperature environments to protect them from heat-induced degradation and thermal stress. These coatings typically consist of ceramic-based materials that provide insulation against extreme temperatures while maintaining structural stability. By reducing heat transfer to the hook's substrate, thermal barrier coatings prevent thermal fatigue, oxidation, and thermal shock, thereby enhancing the hook's performance and reliability in elevated temperature conditions.
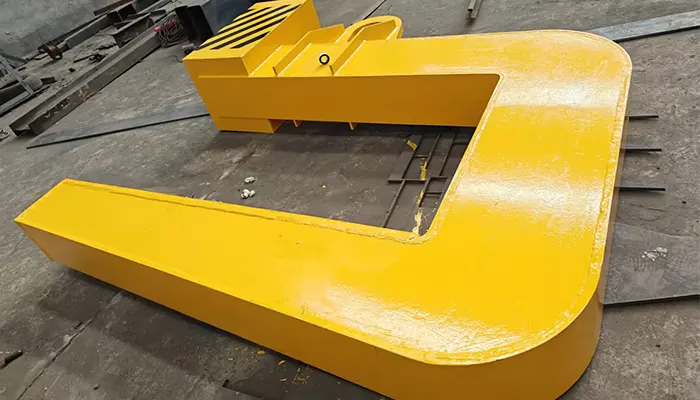
Benefits of Coating Application in C Hooks:
The application of coatings offers several notable benefits for C hooks:
- Increased Service Life: Coatings provide a protective barrier against corrosion, abrasion, and thermal damage, prolonging the operational lifespan of C hooks and reducing the frequency of replacements.
- Enhanced Performance: Coatings improve the hook's resistance to environmental factors and mechanical stresses, ensuring consistent performance and reliability in challenging operating conditions.
- Reduced Maintenance Costs: By minimizing surface degradation and wear, coatings reduce the need for maintenance interventions such as repairs and replacements, resulting in lower overall maintenance costs.
- Improved Safety: Coatings help maintain the structural integrity of C hooks, reducing the risk of sudden failures or accidents during lifting and material handling operations.
- Environmental Protection: Coatings mitigate the environmental impact of C hook operations by preventing the release of harmful substances such as corrosion products and abrasive particles into the surrounding environment.
Overall, the application of coatings plays a vital role in optimizing the performance, durability, and safety of C hooks, contributing to efficient and sustainable material handling practices across various industries.
Challenges and Limitations:
Cost Considerations:
One of the primary challenges associated with the adoption of advanced materials and coatings for C hooks is the cost consideration. Advanced materials often come at a higher price point compared to traditional materials, reflecting the research, development, and production expenses involved in their manufacturing. Similarly, specialized coatings designed to offer enhanced protection and performance can contribute to the overall cost of C hook fabrication. Balancing the benefits of improved durability and performance against the upfront investment required poses a significant financial consideration for manufacturers and end-users alike. Moreover, cost considerations extend beyond initial procurement to encompass maintenance, repair, and replacement expenses over the lifecycle of C hooks, necessitating a comprehensive cost-benefit analysis to justify investment decisions.
Compatibility Issues with Existing Equipment:
Another challenge in the adoption of advanced materials and coatings for C hooks pertains to compatibility issues with existing equipment and infrastructure. C hooks are often integrated into complex material handling systems comprising various components and machinery. Introducing new materials or coatings may pose compatibility challenges, such as differences in thermal expansion coefficients, mechanical properties, or surface characteristics. Incompatibilities between the C hook and other equipment can lead to operational inefficiencies, increased wear and tear, and potential safety risks. Addressing compatibility issues requires thorough engineering analysis, customization of components, and coordination with equipment suppliers to ensure seamless integration and optimal performance within existing systems.
Environmental and Regulatory Concerns:
Environmental and regulatory concerns present additional challenges in the adoption of advanced materials and coatings for C hooks. Many advanced materials and coatings contain chemicals or compounds that may pose environmental risks during manufacturing, application, use, or disposal. Compliance with environmental regulations, such as restrictions on hazardous substances or emissions, imposes stringent requirements on material selection, production processes, and waste management practices. Furthermore, concerns regarding the ecological footprint of advanced materials, including resource depletion, energy consumption, and waste generation, necessitate sustainability considerations in material sourcing and manufacturing practices. Balancing performance requirements with environmental stewardship entails implementing environmentally friendly alternatives, adopting cleaner production technologies, and promoting circular economy principles to minimize the environmental impact of C hook operations.
Addressing these challenges and limitations requires a collaborative effort among stakeholders, including manufacturers, suppliers, regulators, and end-users, to develop innovative solutions, mitigate risks, and promote sustainable practices in material handling operations. By overcoming these obstacles, the adoption of advanced materials and coatings can unlock significant benefits in terms of performance, efficiency, and environmental responsibility, driving positive outcomes for businesses and society alike.
Case Studies and Examples:
Successful Implementation of Advanced Materials and Coatings in C Hooks:
Case Study: Aerospace Industry
In the aerospace industry, C hooks are utilized for handling and transporting aircraft components, such as wings and fuselage sections, during manufacturing and assembly processes. To enhance efficiency and safety, leading aerospace manufacturers have implemented advanced materials such as carbon fiber composites for C hook construction. These lightweight yet durable materials offer significant weight savings without compromising strength or structural integrity. Additionally, specialized coatings, including thermal barrier coatings, are applied to C hooks to protect against heat-induced damage during high-temperature processes like curing or bonding. The successful implementation of advanced materials and coatings in aerospace C hooks has resulted in improved handling capabilities, reduced energy consumption, and enhanced worker safety.
Case Study: Automotive Industry
In the automotive industry, C hooks are essential for lifting and transporting heavy components, such as engine blocks and chassis assemblies, along the production line. To meet the demands of modern automotive manufacturing, leading carmakers have adopted high-strength alloys and advanced coatings for their C hooks. By utilizing materials such as high-strength steel alloys and ceramic-based coatings, automotive manufacturers have achieved significant improvements in load-bearing capacity, corrosion resistance, and longevity. These advanced materials and coatings enable C hooks to withstand the rigors of high-volume production environments while maintaining optimal performance and reliability.
Performance Comparison with Traditional Materials and Coatings:
Comparative Study: Steel vs. Composite C Hooks
A comparative study was conducted to evaluate the performance of traditional steel C hooks versus composite C hooks in a heavy industrial setting. The study examined factors such as weight, strength, corrosion resistance, and longevity. Results indicated that while steel C hooks offered high strength and durability, they were prone to corrosion and had a higher weight-to-load ratio. In contrast, composite C hooks demonstrated comparable strength with significantly lower weight, as well as superior corrosion resistance due to their non-metallic nature. The study concluded that composite materials and coatings offered a viable alternative to traditional steel for C hook applications, providing substantial benefits in terms of weight savings, corrosion protection, and operational efficiency.
Lessons Learned and Best Practices:
- Material Selection: Choose advanced materials and coatings based on specific application requirements, considering factors such as load capacity, environmental conditions, and operational constraints.
- Performance Testing: Conduct thorough performance testing and validation of C hooks using advanced materials and coatings to ensure compliance with industry standards and safety regulations.
- Lifecycle Cost Analysis: Perform comprehensive lifecycle cost analysis to evaluate the long-term economic benefits of adopting advanced materials and coatings, taking into account initial investment, maintenance costs, and operational savings.
- Continuous Improvement: Foster a culture of continuous improvement by monitoring performance metrics, soliciting feedback from end-users, and incorporating lessons learned into future designs and applications.
- Collaboration and Knowledge Sharing: Collaborate with industry partners, research institutions, and regulatory agencies to exchange best practices, share lessons learned, and promote innovation in C hook materials and coatings.
By leveraging successful case studies, conducting performance comparisons, and embracing lessons learned and best practices, manufacturers can optimize the selection, design, and implementation of advanced materials and coatings for C hooks, driving improvements in performance, efficiency, and sustainability across diverse industrial sectors.
Conclusion:
In summary, this exploration into advanced materials and coatings for C hooks has revealed several key findings:
- Advanced materials such as high-strength alloys, composite materials, and nanomaterials offer superior mechanical properties, lightweight design, and tailored functionalities suitable for C hook applications.
- Coatings play a crucial role in enhancing the performance and durability of C hooks by providing protection against corrosion, abrasion, and thermal damage.
- Challenges and limitations, including cost considerations, compatibility issues, and environmental concerns, must be addressed to facilitate the widespread adoption of advanced materials and coatings in C hook manufacturing.
The implications of these findings for the industry are significant. By embracing advanced materials and coatings, manufacturers can enhance the performance, efficiency, and sustainability of material handling operations across various sectors. Future research efforts should focus on addressing remaining challenges, advancing coating technologies, and exploring novel materials and manufacturing techniques to further optimize C hook design and performance. Collaboration among industry stakeholders, research institutions, and regulatory bodies is essential to drive innovation, facilitate technology transfer, and promote the adoption of best practices in C hook materials and coatings.
In conclusion, the advancements in C hook materials and coatings represent a paradigm shift in material handling technology, offering unprecedented opportunities for improving productivity, safety, and environmental sustainability. By harnessing the potential of advanced materials, coatings, and Industry 4.0 technologies, manufacturers can develop C hooks that are not only stronger, lighter, and more durable but also smarter, more adaptable, and environmentally friendly. As we continue to push the boundaries of innovation and collaboration, the significance of advancements in C hook materials and coatings will resonate far beyond the confines of industrial settings, shaping the future of material handling and transportation worldwide.