Top 5 Crane Features Every Concrete Manufacturing Plant Needs
In the concrete manufacturing industry, cranes are essential for the efficient movement of heavy materials, from raw components to finished products. Cranes are used to lift, transport, and position large concrete elements such as molds, beams, panels, and blocks. Without reliable cranes, these tasks would be difficult to manage and would slow down production.
Cranes play a vital role in improving the efficiency, safety, and productivity of concrete plants. By enabling quick and precise handling of heavy materials, cranes help streamline operations, reduce downtime, and prevent accidents. For example, having a crane with sufficient lifting capacity ensures that heavy materials are moved safely without causing damage, while advanced control systems allow for more accurate positioning and lifting, reducing the chance of costly mistakes.
This article will focus on the top five crane features every concrete manufacturing plant should consider. By understanding these key features, plant managers can make more informed decisions when selecting cranes that not only improve overall plant operations but also enhance worker safety and boost long-term productivity.
Box girder gantry crane for heavy concrete components handling
Crane Feature 1: High Lifting Capacity
In concrete manufacturing, the ability to lift and move heavy components is essential for smooth operations. Concrete products, such as pre-cast panels, beams, molds, and blocks, can be extremely heavy. Without cranes with the right lifting capacity, these materials would be difficult to move efficiently, and manual handling would be impractical and unsafe.
Importance of Lifting Heavy Concrete Components
The primary role of cranes in concrete plants is to handle large, bulky, and heavy concrete components. Whether moving raw materials into molds, transferring finished products, or adjusting parts on the production line, the crane must be able to handle the weight without compromising safety or performance. Heavy lifting is particularly critical in plants that manufacture large-scale concrete structures like beams, walls, or slabs, where every movement needs to be accurate and reliable.
Common Lifting Capacities for Concrete Plants
The lifting capacity needed will depend on the specific tasks and materials handled in the plant. Some of the most common lifting capacities for cranes used in concrete manufacturing are:
- 10 tons: Often used for handling smaller concrete elements or lighter molds.
- 20 tons: Suitable for handling medium-sized concrete components, such as smaller pre-cast panels, beams, or aggregates.
- 50 tons and above: For larger operations, cranes with lifting capacities of 50 tons or more are used to handle heavy concrete slabs, full-size pre-cast walls, or large molds. These cranes are typically used in plants that produce large-scale infrastructure elements like bridge beams or multi-story building panels.
How High Lifting Capacity Impacts Plant Operations
A crane's high lifting capacity impacts plant operations in several ways:
- Increased Efficiency: With the ability to lift and move heavier components, cranes can speed up production processes. This reduces the need for manual labor and lowers handling time for each item.
- Safety: Cranes designed for heavy loads reduce the risk of accidents. By eliminating the need for manual lifting, the potential for worker injury is significantly reduced.
- Operational Flexibility: Cranes with higher lifting capacities can handle a wide variety of materials, from small molds to large, complex concrete elements. This gives the plant flexibility to tackle a broader range of projects without needing specialized equipment for each task.
Considerations for Selecting the Right Lifting Capacity for Your Plant
When selecting a crane, it's important to match the lifting capacity to the specific needs of the plant. Here are some key considerations:
- Size and Weight of Concrete Products: Assess the weight and size of the components most commonly produced in your plant. If your plant focuses on smaller products, a crane with a lower lifting capacity may be sufficient. For larger, heavier products, a more powerful crane will be necessary.
- Production Volume: High-volume plants may benefit from cranes with higher lifting capacities to keep operations running smoothly and quickly. This is especially true if multiple lifts are required during each production cycle.
- Future Growth and Expansion: Consider the future needs of your plant. If you're planning to increase production or add new product lines, investing in a crane with a higher lifting capacity might be worthwhile to accommodate future demands.
- Safety Regulations: Ensure that the crane's lifting capacity meets or exceeds safety standards and regulations in your region. Using an undersized crane for heavy lifting can lead to equipment failure or safety hazards.
Selecting the right lifting capacity is essential to maintaining efficient operations while also ensuring the safety of workers and equipment.
Crane Feature 2: Durability and Corrosion Resistance
Concrete manufacturing plants are demanding environments that place significant stress on equipment. Cranes used in these plants must be able to withstand harsh conditions, including exposure to dust, chemicals, moisture, and extreme temperatures. Without the right materials and construction, cranes can quickly degrade, resulting in costly repairs, reduced performance, and even safety hazards.
The Challenging Environment of Concrete Manufacturing Plants
Concrete plants are characterized by a highly abrasive and corrosive environment. Dust from the mixing and grinding of materials, exposure to wet concrete, and the presence of chemicals used in the production process all contribute to wear and tear on equipment. Additionally, cranes in these environments are often exposed to moisture from rain, humidity, or splashes from wet concrete, which accelerates the degradation of metal components.
These challenges make it essential to choose cranes that can endure constant exposure to such conditions without compromising their integrity or reliability.
Impact of Dust, Chemicals, and Moisture on Crane Components
The harsh environment of a concrete manufacturing plant can cause several problems for crane components:
- Dust and Abrasive Particles: Concrete dust and fine particles can accumulate on crane parts, particularly moving components like joints, pulleys, and gears. This can cause friction, leading to wear and tear, and ultimately reducing the lifespan of the crane.
- Chemicals and Corrosive Substances: Certain chemicals used in concrete manufacturing, such as curing agents or additives, can be highly corrosive to metal parts. Prolonged exposure to these chemicals can lead to rust and corrosion, which weakens the crane’s structure and reduces its load-bearing capacity.
- Moisture and Humidity: Constant exposure to moisture from concrete or the surrounding environment can cause rust on metal surfaces, leading to corrosion. Over time, moisture can also infiltrate into crane electrical systems, causing malfunctions or short-circuits.
Benefits of Corrosion-Resistant Materials and Coatings
To combat these issues, modern cranes are often built with corrosion-resistant materials and coatings that extend the life of the equipment and ensure optimal performance. Some of the key benefits include:
- Extended Equipment Lifespan: Cranes designed with rust-resistant materials like galvanized steel or coated with anti-corrosion coatings last much longer, reducing the frequency and cost of replacements.
- Reduced Maintenance Costs: Corrosion-resistant cranes require less frequent maintenance and repairs, resulting in lower operating costs over time.
- Improved Safety: Corrosion can compromise the structural integrity of a crane, leading to unsafe working conditions. Using corrosion-resistant materials ensures that cranes remain stable and reliable, reducing the risk of accidents due to material degradation.
Common corrosion-resistant features found in cranes include:
- Epoxy coatings: Provide an additional protective layer on crane components.
- Stainless steel parts: Highly resistant to rust and corrosion.
- Galvanized components: Metal parts coated with a protective layer of zinc to prevent rusting.
Choosing Cranes Built for Long-Lasting Performance in Harsh Environments
When selecting a crane for a concrete manufacturing plant, durability and corrosion resistance should be top priorities. Here are key considerations to ensure long-lasting performance in harsh environments:
- Material Selection: Choose cranes that are constructed from materials known for their durability and resistance to corrosion, such as stainless steel, galvanized steel, or high-quality alloys.
- Coatings and Finishes: Ensure that critical parts of the crane, such as the boom, girders, and wheels, are treated with corrosion-resistant coatings or finishes.
- Sealed Components: Look for cranes that have sealed electrical components and gearboxes, which protect internal systems from moisture and chemical exposure.
- Regular Maintenance: Even with corrosion-resistant features, regular maintenance and inspections are still necessary to ensure the crane remains in good working condition. This includes checking for early signs of corrosion, cleaning dust and debris from moving parts, and lubricating components to prevent wear.
Investing in a crane built for durability and corrosion resistance ensures that your plant will run more smoothly with fewer disruptions. It also minimizes long-term costs by reducing the need for repairs and replacements, all while ensuring safe, efficient operations in a challenging environment.
Crane Feature 3: Precision and Control
In concrete manufacturing, precision and control are essential for the safe and efficient handling of heavy concrete components. Cranes are not only responsible for lifting but also for carefully positioning large, often fragile, concrete elements into molds or structures. A crane that offers high precision reduces the risk of errors that could result in material damage, delays, and safety hazards.
Need for Accurate and Precise Lifting Operations
Concrete manufacturing involves handling large, heavy, and sometimes delicate components. Whether it's positioning a pre-cast concrete panel into place or lifting a mold to pour fresh concrete, the ability to lift and place materials with accuracy is crucial. Cranes with precise control ensure that each operation is performed smoothly, preventing errors such as misaligned placements, tipping, or damage to concrete products.
Inaccurate lifting or handling can lead to costly product damage, additional labor to correct errors, and even delays in production schedules. The need for precision is particularly important in operations where the margin for error is small, such as placing intricate molds or aligning large concrete sections that need to meet exact specifications.
Role of Advanced Control Systems
Modern cranes are equipped with advanced control systems that significantly enhance their precision and handling capabilities. Some key technologies that improve crane control include:
- Variable Speed Drives: These allow for smooth and precise movement of the crane, providing operators with better control over the speed of lifts and positioning. Variable speed drives are especially beneficial for fine-tuning the placement of large, heavy, or awkwardly shaped concrete components.
- Load Sensors: These sensors continuously monitor the load being lifted and provide real-time feedback to the operator, ensuring that the crane is not overloaded. By maintaining optimal load limits, load sensors help avoid damage to both the crane and the concrete components, improving safety and operational efficiency.
- Positioning Systems: Some cranes are equipped with advanced positioning technology that allows for ultra-precise movements, ensuring that concrete components are placed exactly where needed. This technology minimizes human error and speeds up the overall lifting process.
How Precision Improves Safety and Reduces Material Damage
Crane precision directly impacts both safety and the integrity of materials being handled. Some of the key benefits include:
- Enhanced Safety: Accurate positioning reduces the risk of crane instability, minimizing the chances of tipping, swinging, or dropping heavy loads. This is crucial in environments where the materials being lifted are both heavy and delicate, as incorrect positioning could lead to accidents or injuries.
- Material Protection: By lifting and placing materials with greater precision, cranes can avoid rough handling that could lead to cracks, chips, or other types of damage to concrete components. This is especially important when working with expensive or fragile materials, as even small mistakes can result in costly repairs or replacements.
- Reduced Downtime: Precision control ensures smoother, quicker lifts, which ultimately improves the overall workflow. Accurate lifting reduces delays and interruptions in production caused by the need to reposition loads or correct mistakes.
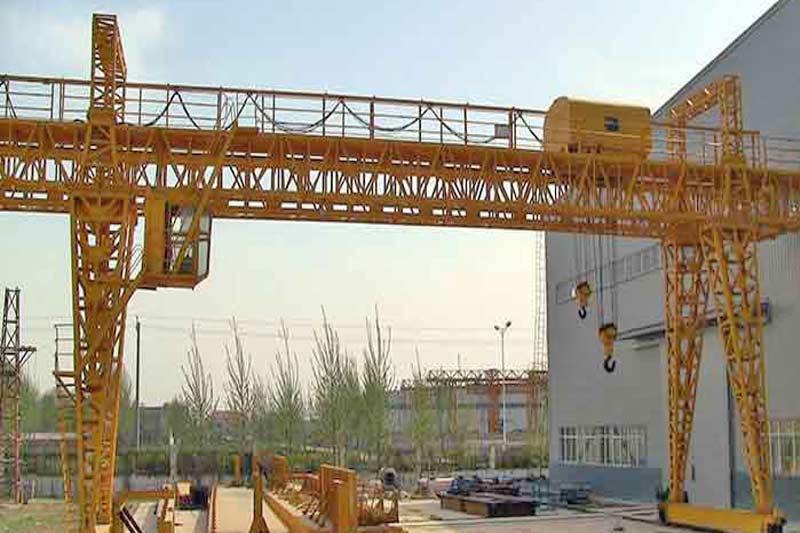
Technological Innovations That Enhance Crane Control and Positioning
Recent technological advancements have revolutionized how cranes operate, offering significant improvements in precision and overall control. Some of the latest innovations include:
- Anti-Sway Systems: These systems prevent the load from swinging or swaying during lifting or movement. Anti-sway technology helps to maintain the stability of the crane and load, especially when lifting large, heavy, or unbalanced concrete components.
- Automatic Load Balancing: Some modern cranes have automatic load-balancing features that adjust the crane's position in real-time to maintain equilibrium. This ensures that the load is evenly distributed, preventing tipping and improving control during lifts.
- GPS and Remote Control: Some cranes now feature GPS systems that allow operators to position loads with high accuracy by simply following mapped out coordinates. Additionally, cranes can be operated remotely, which reduces the risk to operators and allows for more precise control, especially in complex lifts or tight spaces.
- Integrated Safety Systems: Advanced safety features, such as overload protection, motion sensors, and real-time data monitoring, help prevent accidents and errors. These systems continuously assess the status of the crane and the load, alerting operators to potential problems before they escalate.
By integrating these advanced control systems, modern cranes can offer unmatched precision, resulting in smoother, safer, and more efficient operations. For concrete manufacturing plants, investing in cranes with superior precision not only enhances safety but also increases productivity by reducing material waste and operational errors.
Crane Feature 4: Customizable Reach and Height
In concrete manufacturing, flexibility is key to maintaining an efficient and versatile operation. The ability to adapt crane reach and lifting height to suit various tasks and environments within a facility is essential for maximizing productivity. Customizable cranes allow for more dynamic operation, enabling concrete plants to tackle a wider range of tasks and accommodate different production needs without requiring multiple cranes or specialized equipment.
Flexibility Required in Concrete Manufacturing Facilities
Concrete manufacturing plants typically have a variety of lifting requirements depending on the size and type of product being produced. From lifting molds to moving finished concrete elements, different tasks demand different crane configurations. Customizable reach and height allow cranes to be adapted to the unique demands of each task. This flexibility is especially important in large plants with multiple production lines, high ceilings, or specific spatial constraints.
Having a crane that can adjust to various tasks means fewer delays when moving between tasks, reducing the need to switch between different cranes or reconfigure the layout of the plant. This ability ensures smoother operations, saving time and increasing overall productivity.
Adjustable Spans and Lifting Heights for Different Tasks
Customizable cranes can be equipped with adjustable spans and lifting heights to suit a wide range of activities:
- Adjustable Spans: Cranes with customizable spans can adapt to different building layouts or specific production areas, allowing for efficient movement of materials across wide or narrow spaces. For example, cranes with adjustable spans are ideal for plants that have multiple production lines, allowing operators to use the same crane for multiple tasks without having to move equipment or materials around the facility.
- Variable Lifting Heights: Cranes that can adjust their lifting height offer significant flexibility, enabling them to handle both small and large concrete components in areas with varying ceiling heights. For instance, taller cranes are needed when lifting pre-cast concrete panels or beams to higher levels, while shorter cranes are ideal for ground-level tasks, like moving molds or smaller concrete pieces.
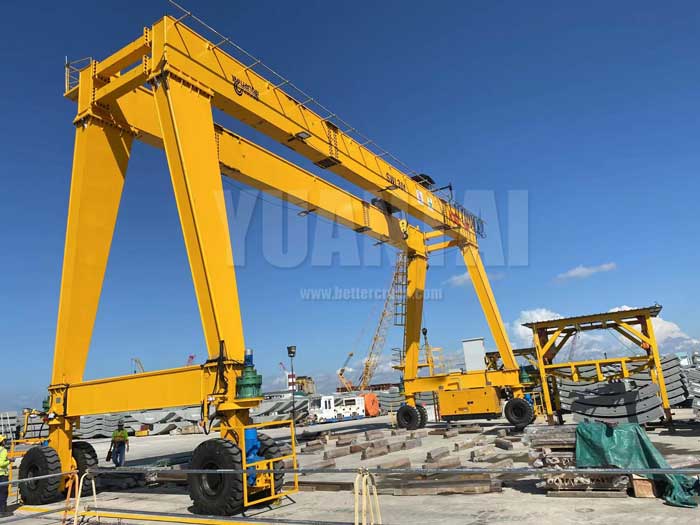
Benefits of Cranes That Can Be Tailored to Specific Tasks or Areas
The ability to customize a crane’s reach and height for specific tasks offers several key benefits:
- Optimized Workflow: By tailoring the crane’s reach and lifting height to the specific needs of the job, plants can maintain a more streamlined workflow, minimizing delays and reducing the time spent repositioning cranes or equipment.
- Increased Efficiency: Customizable cranes allow operators to work within tighter spaces or access difficult-to-reach areas, improving efficiency and reducing the time needed for manual labor or reconfiguring the plant layout. This flexibility also reduces the need for multiple cranes with different reach capabilities.
- Cost-Effectiveness: Investing in a crane that can be customized for various tasks saves money in the long run. Rather than purchasing separate cranes for different applications or reconfiguring equipment constantly, a single customizable crane can handle a broad range of operations, reducing the need for additional equipment and maximizing the value of the initial investment.
- Space Utilization: Customizable cranes allow for more effective use of available space, especially in plants with limited room for large, permanent cranes or infrastructure. Adjustable cranes help navigate tight or cluttered spaces, ensuring that production lines and storage areas remain optimized.
Examples of Customized Crane Features in Large Plants
In large concrete manufacturing plants, customized cranes are essential to meet specific operational needs. Some examples of customized crane features include:
- Telescopic Arms: These cranes feature extendable arms that allow operators to increase or decrease the reach depending on the task. This is particularly useful for working across wide production floors or lifting materials over obstacles.
- Modular Cranes: These cranes can be assembled with additional sections to adjust their span or lifting height. This modularity allows the crane to be adapted as production needs change or when working on different sections of a plant.
- Adjustable Trolleys: Cranes with adjustable trolleys offer flexibility in positioning the load precisely within a defined range. This is ideal for moving heavy concrete elements into molds or aligning pre-cast components with precision.
- High Lifting Gantries: Cranes that feature adjustable gantries can handle materials at various heights, ensuring that plant operations can continue smoothly even when dealing with tall structures or multiple levels within the manufacturing space.
By incorporating customizable reach and height, concrete plants can significantly enhance their operational efficiency, reduce equipment costs, and ensure that their cranes are adaptable to the unique needs of their production lines.
Crane Feature 5: Safety Features
Safety is a paramount concern in concrete manufacturing plants due to the heavy materials being handled and the complex operations taking place. Cranes, being integral to these processes, must be equipped with advanced safety features to protect both the operators and the equipment. A crane that prioritizes safety not only minimizes the risk of accidents but also ensures compliance with industry regulations and boosts overall operational efficiency.
Safety as a Top Priority in Concrete Plants
Concrete plants are high-risk environments, with heavy concrete elements, large machinery, and often limited space for maneuvering. The safe handling of materials is critical to preventing workplace injuries and equipment damage. Given the potential hazards associated with lifting heavy loads and working in confined spaces, cranes must be designed with safety features that reduce risks.
In addition to safety during lifting operations, cranes must also contribute to creating a safe working environment by reducing the likelihood of accidents that could endanger workers or cause costly downtime. Cranes with built-in safety systems can make a significant difference in protecting both personnel and equipment in concrete manufacturing facilities.
Crane Safety Systems: Overload Protection, Emergency Stop, Anti-Collision Systems
Several safety features play a critical role in preventing accidents and ensuring the crane operates within its safe limits. Some essential safety systems include:
- Overload Protection: One of the most important safety features of a crane is overload protection. This system automatically monitors the weight of the load being lifted and ensures that it does not exceed the crane’s rated capacity. If the load exceeds the safe limit, the system activates alarms or halts the operation to prevent damage to the crane and avoid accidents.
- Emergency Stop Function: Cranes should have emergency stop buttons easily accessible to the operator. This safety feature allows the crane to be halted immediately in case of any malfunction, dangerous situation, or if a worker is in the vicinity of the crane’s movement path. Quick shutdown capabilities are essential to prevent injuries and limit damage during emergencies.
- Anti-Collision Systems: In plants where cranes operate in close proximity to other machinery, personnel, and infrastructure, anti-collision systems are crucial. These systems help prevent accidents by detecting objects or other moving cranes in the crane’s path and automatically slowing down or stopping the crane to avoid collisions. Anti-collision features improve the safety of operations, especially in busy or high-risk areas of the plant.
The Role of Operator Training and Safety Protocols
Even the best crane safety features cannot prevent accidents if operators are not adequately trained. Proper operator training is essential to ensure that workers understand how to use the crane safely and efficiently.
- Comprehensive Training: Operators must undergo thorough training to understand crane operation, safety features, and emergency procedures. Training should cover topics such as load assessment, safe operating speeds, proper lifting techniques, and how to handle hazardous situations, such as crane malfunctions or unexpected movements.
- Safety Protocols: In addition to operator training, plants must implement safety protocols that govern crane operation. These protocols should include guidelines on crane maintenance, regular safety checks, and procedures for emergency situations. Ensuring that workers follow these protocols is essential for creating a culture of safety within the plant.
- Regular Safety Audits: Ongoing safety audits and inspections are essential for identifying potential hazards before they lead to accidents. Regular crane inspections ensure that safety systems are functioning correctly and that the crane remains in good working order.
Importance of Safety Certifications and Compliance with Industry Standards
Safety certifications and compliance with industry standards are crucial for ensuring that cranes meet safety regulations and operate reliably. Some key aspects include:
- Industry Standards Compliance: Cranes must comply with local and international safety standards, such as those set by organizations like OSHA (Occupational Safety and Health Administration), ISO (International Organization for Standardization), and the CE (Conformité Européenne) mark in Europe. Compliance with these standards ensures that the crane meets the necessary safety requirements and that the plant adheres to industry best practices.
- Certification of Safety Features: Manufacturers of cranes often provide certifications for safety features such as overload protection, anti-collision systems, and emergency stop mechanisms. These certifications assure plant operators that the equipment meets high safety standards, reducing the likelihood of mechanical failure or human error.
- Insurance and Liability: Compliance with safety standards and certifications is not only important for operational safety but also for reducing liability risks. Insurance companies often require that cranes and other equipment meet specific safety criteria to cover potential accidents or damages. Adhering to these requirements can protect both the workers and the business.
In summary, incorporating advanced safety features into cranes is essential for reducing risks in concrete manufacturing plants. Features such as overload protection, emergency stop systems, and anti-collision technology enhance safety by minimizing hazards during crane operations. In addition to the equipment itself, ensuring that operators are well-trained and that the plant complies with safety regulations creates a safer and more efficient working environment. Safety features not only protect employees but also contribute to the overall success and productivity of the plant.
Conclusion
In concrete manufacturing plants, selecting the right crane features is vital for ensuring smooth operations, maintaining safety, and boosting overall productivity. The five key crane features—high lifting capacity, durability and corrosion resistance, precision and control, customizable reach and height, and advanced safety features—are essential for handling the heavy lifting demands of the industry while minimizing risks.
Recap of the Five Key Crane Features for Concrete Manufacturing Plants
- High Lifting Capacity: Ensures cranes can handle heavy concrete components, such as panels and beams, without overloading.
- Durability and Corrosion Resistance: Protects cranes from wear and tear caused by harsh working environments, ensuring long-term performance.
- Precision and Control: Offers accurate and efficient lifting operations, minimizing material damage and enhancing safety.
- Customizable Reach and Height: Provides flexibility to adapt the crane to various tasks and space constraints within the plant.
- Advanced Safety Features: Ensures the protection of workers and equipment through overload protection, anti-collision systems, and proper training.
How Selecting the Right Crane Features Can Improve Efficiency, Safety, and Longevity
By choosing cranes equipped with these essential features, concrete manufacturing plants can achieve:
- Increased Efficiency: Optimized lifting capacities, precision, and flexibility reduce downtime and streamline operations, enabling quicker production cycles.
- Enhanced Safety: Safety systems like overload protection and anti-collision technology mitigate risks, ensuring a safe working environment for operators and workers.
- Longer Equipment Lifespan: Durable, corrosion-resistant cranes are built to withstand the demanding conditions of concrete production, reducing maintenance costs and extending service life.
Investing in quality cranes with the right features is crucial for the long-term success of concrete manufacturing plants. These cranes not only improve daily operational efficiency and safety but also contribute to the plant’s ability to scale production and meet market demands. By prioritizing durability, precision, and safety, plants can avoid costly downtime, improve worker productivity, and ensure they stay competitive in an increasingly demanding industry. The right crane is an investment in the future of the plant, supporting both immediate and long-term operational goals.