Overhead Crane with Two Hooks
Overhead crane with two hooks for sale. Custom single girder and double girder overhead crane with double hoists or built up hoist with two hooks for sale.
Overhead cranes equipped with two hooks stand as pivotal solutions within industrial settings, offering a robust means of material handling. These cranes, characterized by their unique ability to manage two separate loads simultaneously, hold a critical position in various industrial operations. The following sections delve into the multifaceted aspects associated with these sophisticated cranes, shedding light on their design, manufacturing, installation, operation, maintenance, and comparison between different types.
An overhead crane with two hooks, often known as a double-hook overhead crane, is a specialized lifting equipment system mounted on an elevated runway structure. Unlike standard cranes, these sophisticated systems feature two hoisting mechanisms, each equipped with its own hook, enabling the concurrent lifting and transport of two distinct loads within a single operational cycle. This distinctive feature significantly amplifies the efficiency and throughput of material handling processes in industries ranging from manufacturing and construction to warehousing and logistics.
The significance of overhead cranes with two hooks lies in their ability to streamline and expedite material handling operations. These cranes serve as indispensable assets across diverse industrial domains, catering to the needs of heavy-duty lifting, precise maneuvering, and simultaneous handling of multiple loads. Their versatility spans various applications, ranging from lifting bulky machinery components in manufacturing plants to facilitating the swift movement of goods in distribution centers and harbors.
The capability to handle two loads concurrently not only optimizes operational efficiency but also contributes to enhanced productivity, allowing industries to meet demanding production schedules and manage complex logistics with ease. Moreover, these cranes offer a heightened level of flexibility, adaptability, and safety in material handling operations, underscoring their indispensable role in modern industrial workflows.
Types of Overhead Cranes with Two Hooks
Overhead cranes with two hooks come in distinct configurations, each tailored to specific industrial needs, lifting capacities, and operational requirements. Let's explore the two primary types:
Double Girder Overhead Crane with Two Hooks:
Structural Design and Components:
- Incorporates two parallel girders for enhanced stability and strength.
- Utilizes heavy-duty components to withstand higher loads.
Lifting Capacities and Load Handling:
- Offers substantial lifting capacities suitable for heavy loads.
- Accommodates oversized materials with ease.
Applications in Heavy Industries:
- Finds prevalence in heavy industrial sectors such as steel mills, shipyards, and construction sites.
- Ideal for handling large machinery, bulky components, and heavy materials.
Single Girder Overhead Crane with Two Hooks:
Structure and Design Specifics:
- Features a single main girder offering a more compact design.
- Balances load handling capability with space efficiency.
Versatility and Applications:
- Suited for moderate lifting tasks in various industrial environments.
- Offers flexibility and adaptability in handling diverse materials and components.
Suitability for Moderate Lifting Tasks:
- Commonly employed in assembly lines, workshops, and warehouses with moderate lifting requirements.
- Provides an optimal solution for operations needing versatility and moderate lifting capabilities.
Both double girder and single girder overhead cranes with two hooks present unique advantages, serving different industrial demands and lifting requirements. The choice between the two types depends on specific operational needs, load capacities, and the intended application environment.
Comparative Analysis of Overhead Crane Types with Two Hooks
Lifting Capacities and Load Handling:
- Double Girder vs. Single Girder Cranes:
- Double Girder Cranes: Known for their robust construction, they excel in handling heavier loads, typically offering higher lifting capacities compared to single girder cranes.
- Single Girder Cranes: While featuring a more compact design, they accommodate moderate loads efficiently but might have lower lifting capacities compared to double girder cranes.
Structural Design and Stability:
- Stability in Double Girder Design vs. Space Efficiency in Single Girder:
- Double Girder Cranes: The use of two girders provides enhanced stability, making them suitable for heavy-duty lifting applications requiring greater structural integrity.
- Single Girder Cranes: Known for their space efficiency and versatility, they offer a more lightweight and economical solution but may sacrifice some stability.
- Strength and Durability Comparisons:
- Double Girder Cranes: Generally constructed with heavier and sturdier components, ensuring robustness and durability over the long term.
- Single Girder Cranes: Feature lighter structures, compromising slightly on overall strength but offering agility and adaptability in various settings.
Applications and Industrial Suitability:
Heavy Industry vs. Lighter Applications:
- Double Girder Cranes: Predominantly employed in heavy industrial sectors requiring the handling of massive and bulky loads, such as steel manufacturing, foundries, and shipyards.
- Single Girder Cranes: More adaptable across lighter applications like workshops, assembly lines, and warehouses with moderate lifting requirements.
Specific Use Cases for Each Type:
- Double Girder Cranes: Excel in scenarios demanding high lifting capacities and robust structural support, facilitating the handling of exceptionally heavy materials.
- Single Girder Cranes: Ideal for operations requiring moderate lifting capacities and versatility, where space constraints or lighter loads are prevalent.
Cost Considerations and Efficiency:
Initial Investment vs. Long-Term Benefits:
- Double Girder Cranes: Generally involve a higher initial investment due to their robust design but offer superior lifting capacities and durability, resulting in long-term efficiency.
- Single Girder Cranes: Economical initial investment with lower lifting capacities; however, they provide efficiency and adaptability in specific operational contexts, optimizing resources effectively.
Operational Efficiency and Maintenance Costs:
- Double Girder Cranes: While efficient in heavy lifting tasks, they might have higher maintenance costs due to their heavy-duty components and larger size.
- Single Girder Cranes: Offer cost-effective maintenance and operational efficiency, especially in applications with moderate lifting needs.
Double Hoists Overhead Crane with Two Hooks

- Description: This type of crane is equipped with two hoists and two hooks, allowing for independent lifting operations. It typically comprises a double-girder structure with two hoisting mechanisms installed for simultaneous or separate load handling.
- Functionality: The double hoists overhead crane with two hooks is designed to perform tasks where the simultaneous lifting of multiple loads or handling of intricate operations is required, providing enhanced versatility in industrial applications.
- Applications: Often utilized in scenarios demanding intricate load manipulation or simultaneous handling of different weights within a single operation, such as heavy machinery manufacturing or assembly lines.
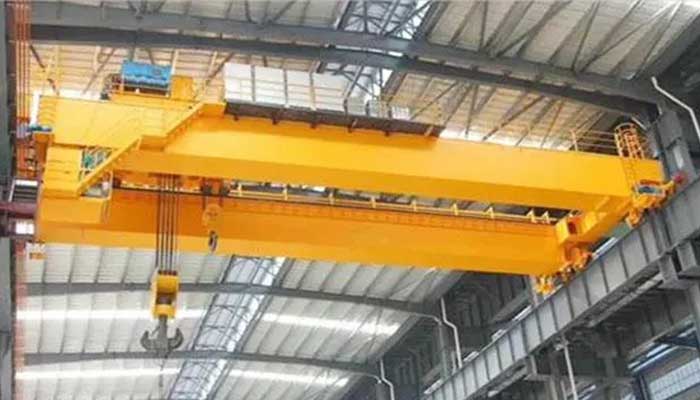
Builtup Hoists Overhead Crane with Two Hooks, Main Hook & Auxiliary Hook:
- Description: This crane features a primary (main) hook and an auxiliary hook, providing a versatile solution for lifting operations where varying load sizes or configurations are encountered. The main hook handles the primary load, while the auxiliary hook assists in managing additional or smaller loads simultaneously.
- Functionality: Builtup hoists overhead cranes with two hooks, comprising a single or double girder design, offer flexibility in handling diverse loads, allowing the main hook to manage heavier loads while the auxiliary hook supports supplementary or smaller loads.
- Applications: Commonly employed in settings where varying load sizes or multiple lifting operations are prevalent, such as shipyards, construction sites, or warehouses requiring flexible and efficient material handling solutions.
These types of overhead cranes with multiple hooks cater to specific industrial needs, providing enhanced versatility and adaptability for various lifting operations, making them valuable assets in industries requiring complex load handling.
Comparison: Double Hoists Overhead Crane vs. Builtup Hoists Overhead Crane with Two Hooks
Configuration:
Double Hoists Overhead Crane with Two Hooks:
- Equipped with two separate hoists and hooks.
- Allows for simultaneous or independent lifting operations.
- Suitable for handling multiple loads concurrently.
Builtup Hoists Overhead Crane with Two Hooks:
- Comprises a main hook and an auxiliary hook.
- Main hook manages primary loads, while the auxiliary hook assists with smaller or additional loads.
- Offers flexibility in handling diverse load sizes and configurations.
Load Handling Capability:
Double Hoists Overhead Crane with Two Hooks:
- Ideal for scenarios requiring simultaneous lifting of multiple heavy loads.
- Suited for heavy machinery manufacturing or assembly lines.
Builtup Hoists Overhead Crane with Two Hooks:
- Offers versatility in handling various load sizes simultaneously.
- Useful in situations where different load configurations or sizes are encountered.
Complexity and Versatility:
Double Hoists Overhead Crane with Two Hooks:
- Provides a more intricate and sophisticated lifting operation.
- Offers increased versatility in complex handling scenarios.
Builtup Hoists Overhead Crane with Two Hooks:
- Simpler setup with a main and auxiliary hook configuration.
- Offers adaptability in handling different loads efficiently.
Industrial Applications:
Double Hoists Overhead Crane with Two Hooks:
- Commonly used in heavy industries demanding intricate load manipulations.
- Suitable for operations requiring multiple heavy loads to be lifted simultaneously.
Builtup Hoists Overhead Crane with Two Hooks:
- Widely employed in settings with varying load sizes or multiple lifting requirements.
- Suitable for applications where different load configurations need to be managed efficiently.
Operational Flexibility:
Double Hoists Overhead Crane with Two Hooks:
- Offers enhanced flexibility for handling multiple heavy loads independently.
- Well-suited for demanding operations with intricate load requirements.
Builtup Hoists Overhead Crane with Two Hooks:
- Provides flexibility in managing various load sizes and configurations concurrently.
- Suitable for environments needing versatile material handling solutions.
Design Considerations for Crane Manufacturers
Designing overhead cranes with two hooks necessitates meticulous attention to various critical aspects ensuring optimal performance and safety. Here are essential design considerations for crane manufacturers:
Structural Design Specifications:
- Girder Configuration: Determining the appropriate girder type (single or double) based on load capacities, application requirements, and structural stability.
- Bridge Configuration: Designing the crane's bridge structure, considering span length, runway length, and ensuring proper alignment with the working area.
Material Selection for Components:
- High-Quality Construction Materials: Employing durable and high-strength materials such as high-grade steel for girders, main structural components, and critical parts to ensure longevity and reliability.
- Corrosion Resistance: Using materials resistant to environmental factors and corrosion for enhanced durability, especially in industrial settings with harsh conditions.
Load Capacity and Hook Arrangement:
- Determining Load Capacities: Calculating and defining the crane's maximum lifting capacities based on application requirements and ensuring adherence to safety standards.
- Optimal Hook Arrangement: Strategically placing the hooks to ensure balanced load distribution, avoiding tilting, and maintaining stability during lifting operations.
Safety Features Integration:
- Safety Devices and Systems: Incorporating safety features like overload protection, limit switches, emergency braking systems, and anti-collision mechanisms to prevent accidents and ensure operator and workplace safety.
- Redundancy Measures: Implementing redundant safety features and fail-safe mechanisms to mitigate risks and ensure operational safety even in case of component failure.
Compatibility with Lifting Requirements:
- Versatile Configurations: Designing the crane system to accommodate various lifting configurations, heights, and load types to cater to diverse operational needs.
- Precision Controls: Integrating control systems offering precise maneuverability, speed regulation, and accurate load positioning for efficient material handling.
Manufacturing Process for Crane Manufacturers
Manufacturing overhead cranes equipped with two hooks requires a systematic and precise process to ensure quality, safety, and reliability:
Fabrication of Structural Components:
- Girder Construction: Fabricating the girders, considering material specifications and structural design requirements, to ensure robustness and load-bearing capacity.
- Bridge and Trolley Components: Manufacturing the bridge, trolley, and other structural components with precision to meet design specifications and operational needs.
Hoist and Hook Assembly:
- Hoist Design and Assembly: Fabricating the hoisting mechanisms, including motors, drums, and wire ropes, with precision engineering to support the crane's lifting capacities.
- Hook Manufacturing: Crafting hooks to withstand designated loads, ensuring strength, durability, and compliance with safety standards.
Installation of Electrical Systems and Controls:
- Electrical Wiring and Components: Integrating electrical systems, including motors, controllers, limit switches, and sensors, ensuring proper connections and functionality.
- Control Panel Installation: Mounting and configuring the control panels to facilitate smooth operation and precise control of the crane functions.
Quality Assurance and Testing Procedures:
- Quality Checks: Implementing stringent quality control measures throughout the manufacturing process, including inspections of components, welds, and assemblies.
- Performance Testing: Conducting load tests, functionality checks, and operational simulations to ensure adherence to design specifications and safety standards.
Compliance with Safety Standards and Regulations:
- Regulatory Compliance: Ensuring that the crane design, manufacturing, and testing adhere to industry-specific safety standards, codes, and regulations.
- Certifications and Documentation: Obtaining necessary certifications and generating comprehensive documentation validating compliance with safety protocols.
Adhering to a meticulous manufacturing process that covers fabrication, assembly, electrical integration, rigorous quality checks, and compliance measures is essential for ensuring the production of reliable and safe overhead cranes with two hooks.
Installation Aspects for Crane Buyers
For buyers acquiring overhead cranes with two hooks, proper installation is crucial for safe and efficient operation:
Site Preparation and Structural Requirements:
- Foundation Readiness: Ensuring the installation site meets foundation requirements, such as load-bearing capacity and levelness, to support the crane's structure.
- Runway Assembly: Setting up the crane's runway structure, ensuring alignment, proper anchoring, and clearance according to the manufacturer's specifications.
Rigging and Assembly Procedures:
- Component Rigging: Rigging and positioning structural components, girders, trolleys, and hoisting mechanisms following assembly instructions and safety protocols.
- Hook Assembly: Installing and securing hooks, ensuring proper alignment and attachment to the hoisting mechanisms.
Electrical Connections and Power Supply:
- Electrical Installation: Connecting electrical components, including motors, controls, and sensors, following manufacturer guidelines and electrical codes.
- Power Requirements: Ensuring the availability of appropriate power supply configurations as specified by the crane's electrical requirements.
Calibration and Testing Before Operational Use:
- Calibration Procedures: Conducting calibration of controls, limit switches, and safety features to ensure accuracy and functionality.
- Pre-operational Testing: Performing comprehensive tests and trials to verify the crane's performance, safety features, and operational functions before active use.
Certification and Inspection Requirements:
- Certification Procedures: Verifying compliance with local regulations, obtaining necessary permits, and ensuring adherence to safety standards.
- Inspection and Approval: Scheduling inspections by qualified personnel to certify the crane's installation and operational readiness.
Proper adherence to installation procedures, including site preparation, rigging, electrical connections, calibration, and certification, is paramount to guarantee the safe and efficient functioning of overhead cranes with two hooks.
Operation and Safety Guidelines for Crane Buyers
Ensuring safe and efficient operation of overhead cranes with two hooks involves adherence to strict operational and safety protocols:
Operator Training and Certification:
- Comprehensive Training Programs: Providing thorough training sessions for crane operators covering operational controls, load handling, and safety procedures.
- Certification Requirements: Ensuring operators receive proper certification and licensing to operate the crane in compliance with industry standards.
Safe Operating Procedures:
- Standard Operating Protocols: Establishing and enforcing standard procedures for crane operation, including startup, maneuvering, and shutdown sequences.
- Load Handling Guidelines: Providing clear instructions on load handling techniques, weight limits, and proper load attachment methods.
Load Handling Practices and Limitations:
- Weight Capacity Awareness: Educating operators on the crane's load capacity limitations and the importance of adhering to specified weight limits.
- Balanced Load Handling: Emphasizing the significance of balanced load distribution and proper rigging techniques to avoid overloading or imbalance issues.
Emergency Protocols and Shutdown Procedures:
- Emergency Response Training: Conducting training sessions on emergency procedures, such as shutdown protocols, evacuation plans, and response to critical situations.
- Emergency Stop Controls: Ensuring operators are familiar with emergency stop mechanisms and procedures in case of unforeseen circumstances.
Periodic Safety Inspections and Audits:
- Scheduled Inspections: Conducting regular inspections by qualified personnel to assess the crane's condition, functionality, and adherence to safety standards.
- Safety Audits: Performing periodic safety audits to review operational practices, identify potential hazards, and implement necessary corrective actions.
Promoting a culture of safety and providing comprehensive training, operational guidelines, and safety protocols are paramount in ensuring the secure and efficient use of overhead cranes equipped with two hooks.
Maintenance Protocols for Crane Manufacturers and Buyers
Implementing robust maintenance procedures is essential to uphold the operational efficiency and safety of overhead cranes with two hooks:
Routine Maintenance Schedule and Tasks:
- Scheduled Maintenance Plans: Establishing a routine maintenance schedule outlining periodic inspections, checks, and servicing intervals for all crane components.
- Checklist for Tasks: Creating detailed checklists covering maintenance tasks such as inspections, adjustments, and preventive measures to ensure thoroughness.
Lubrication and Component Inspection:
- Lubrication Regimen: Implementing a comprehensive lubrication schedule for critical components, including wire ropes, bearings, gears, and tracks, to prevent wear and corrosion.
- Component Inspections: Conducting regular inspections to assess the condition of structural elements, electrical connections, and safety features for signs of wear or malfunction.
Repairs and Replacement Procedures:
- Prompt Repair Protocols: Establishing protocols for identifying and addressing potential issues promptly, with clear procedures for repairs or component replacements.
- Sourcing Quality Parts: Ensuring the procurement of genuine parts and components from authorized suppliers for repairs and replacements.
Record-Keeping of Maintenance Activities:
- Maintenance Logs: Maintaining detailed records of all maintenance activities, including dates, tasks performed, inspections, repairs, and replacements, for future reference and auditing purposes.
- Documentation Compliance: Ensuring adherence to regulatory documentation requirements for maintenance records and compliance verification.
Collaboration for Scheduled Downtime and Maintenance:
- Coordinated Downtime: Collaborating with operational teams to schedule planned downtime for maintenance, minimizing disruption to regular operations.
- Communication and Coordination: Establishing effective communication channels between maintenance personnel and operational staff for seamless coordination during maintenance periods.
Adhering to comprehensive maintenance protocols, including routine inspections, lubrication, repairs, and systematic record-keeping, ensures the longevity, reliability, and safety of overhead cranes with two hooks.
Performance Monitoring and Upgrades
Continuously monitoring and upgrading overhead cranes with two hooks is pivotal for maintaining optimal performance and incorporating technological advancements:
Monitoring Crane Performance Metrics:
- Data Collection and Analysis: Implementing systems to collect performance data related to load handling, operational efficiency, and safety metrics.
- Performance Metrics: Monitoring metrics such as load capacities, hoist speeds, downtime, and energy consumption to assess overall crane performance.
Identification of Potential Upgrades or Enhancements:
- Regular Assessments: Conducting regular assessments to identify areas for potential improvements, whether related to efficiency, safety, or technological advancements.
- Feedback from Operators: Seeking feedback from crane operators regarding operational challenges or areas where enhancements could be beneficial.
Technological Advancements and Retrofits:
- Upgrading Control Systems: Considering modernization of control systems, including adopting wireless controls or automation integration for improved precision and efficiency.
- Implementing Safety Innovations: Incorporating cutting-edge safety technologies like anti-collision systems or remote monitoring for enhanced workplace safety.
Collaboration for Crane Improvements and Innovations:
- Industry Collaboration: Engaging with industry peers, technical experts, and manufacturers to explore innovations and best practices for crane upgrades.
- Manufacturer-Buyer Collaboration: Encouraging collaboration between crane manufacturers and buyers to implement upgrades or retrofits aligned with specific operational needs.
Efficient performance monitoring and proactive identification of potential upgrades or enhancements, in conjunction with technological advancements and collaborative efforts, ensure that overhead cranes with two hooks remain at the forefront of operational efficiency and safety.