Advanced Double Hoist Overhead Cranes Meet Your Industrial Needs
Double Hoist Overhead Cranes: Revolutionizing Industrial Operations
In the world of industrial and construction settings, the evolution of machinery has been instrumental in enhancing productivity and efficiency. Among the many innovations, Double Hoist Overhead Cranes stand tall, representing a pinnacle in lifting and transporting heavy loads within these sectors.
Double Hoist Overhead Cranes, a marvel in engineering, are specialized cranes equipped with two hoists operating on a single bridge. Their primary function involves lifting and moving substantial loads with unparalleled precision and efficiency. Unlike conventional cranes, these innovative systems provide a higher level of flexibility and control in managing complex lifting tasks.
The significance of Double Hoist Overhead Cranes cannot be overstated in industrial and construction domains. These cranes have become indispensable due to their capability to handle heavier loads and perform intricate lifting operations with ease. Their presence significantly reduces manual labor and speeds up the process, ultimately resulting in cost-effectiveness and increased productivity.
When it comes to large-scale manufacturing plants, warehouses, or construction sites, these cranes play a pivotal role in streamlining operations. Their ability to handle diverse loads of varying shapes and sizes makes them versatile assets, catering to a wide array of industries.
Double Hoist Overhead Cranes have emerged as the backbone of numerous industrial and construction projects, revolutionizing the way heavy materials are handled and transported.
Double hoist overhead cranes for sale
Overview of Advanced Hoist and Crane Technologies
Hoist Technologies encompass a spectrum of cutting-edge mechanisms and systems integrated into machinery, specifically designed to lift, lower, and transport heavy loads efficiently and securely. In the context of Double Hoist Overhead Cranes, these technologies form the backbone of the crane's functionality, enabling precise and controlled movements crucial for various industrial and construction applications.
The evolution of hoist technologies has transitioned from traditional manual mechanisms to highly advanced automated systems, revolutionizing the capabilities and performance of overhead cranes.
Importance of Advanced Technologies in Overhead Cranes
The integration of advanced technologies in Double Hoist Overhead Cranes signifies a paradigm shift in the lifting and transportation industry. These innovations serve multiple purposes, primarily enhancing safety, precision, and efficiency in operations.
- Safety Enhancement:The incorporation of sophisticated sensors, monitoring systems, and fail-safes ensures a safer working environment. These technologies offer real-time data on load capacities, preventing overloading and averting potential accidents.
- Precision and Control:Advanced control mechanisms, such as Variable Frequency Drives (VFDs) and precision control systems, provide operators with unparalleled control over crane movements. This level of precision allows for delicate maneuvers even with heavy loads, reducing the margin of error and optimizing productivity.
- Efficiency and Productivity:The implementation of these technologies streamlines operations, reducing downtime and enhancing productivity. Intelligent load monitoring systems enable optimized load distribution, minimizing material handling time and maximizing efficiency.
- The significance of these advanced hoist technologies extends beyond mere efficiency gains. They redefine the capabilities of Double Hoist Overhead Cranes, setting new benchmarks for performance and reliability in industrial and construction settings.
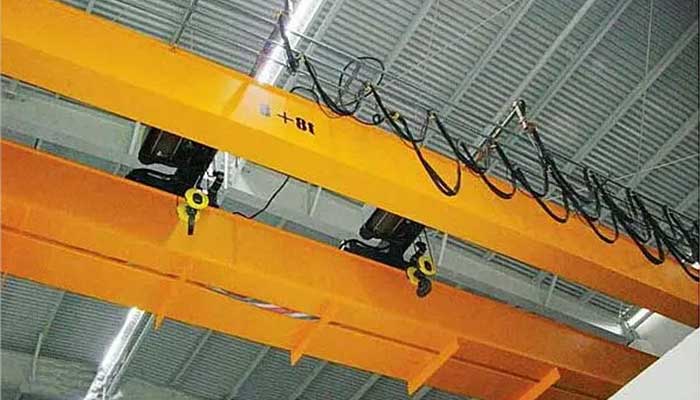
Advanced Hoist Technologies in Double Hoist Overhead Cranes
Variable Frequency Drives (VFDs)
Variable Frequency Drives (VFDs) are sophisticated control systems designed to regulate the speed and torque of an electric motor. They achieve this by adjusting the frequency and voltage of the electrical supply to the motor, allowing for precise control over its operation.
In Double Hoist Overhead Cranes, VFDs play a crucial role in optimizing the performance of the hoisting mechanism. They facilitate smooth and controlled acceleration and deceleration of the hoists, enabling operators to lift and lower loads with exceptional precision. VFDs adjust the speed of the hoists according to the load requirements, minimizing stress on the machinery and ensuring efficient operation.
Benefits and Advantages
- Enhanced Control and Precision:VFDs provide operators with fine-tuned control over the hoisting process, allowing for gradual and accurate movements, even when dealing with heavy loads. This precision significantly reduces the risk of load swing or sudden movements, enhancing safety and minimizing the potential for accidents.
- Energy Efficiency:By adjusting the motor's speed based on load demands, VFDs optimize energy consumption. They reduce the power drawn during lighter loads, leading to significant energy savings and contributing to a more sustainable operation.
- Extended Equipment Lifespan:The controlled acceleration and deceleration achieved through VFDs help mitigate wear and tear on the hoisting equipment. This results in reduced maintenance requirements and an extended lifespan of the crane components, ensuring long-term cost-effectiveness.
Variable Frequency Drives represent a cornerstone in the advancement of Double Hoist Overhead Cranes, enabling smoother and more efficient lifting operations while prioritizing safety and longevity.
Intelligent Load Monitoring Systems
Intelligent Load Monitoring Systems are advanced technologies integrated into Double Hoist Overhead Cranes to monitor and analyze the weight and stress on the lifting equipment in real-time. These systems employ sensors and data processing mechanisms to constantly assess the load being lifted and provide crucial information to operators.
In Double Hoist Overhead Cranes, Intelligent Load Monitoring Systems are seamlessly integrated into the hoisting mechanisms. They utilize load cells, strain gauges, or other sensor technologies installed on the crane's hook or lifting apparatus to measure the weight and stress distribution of the load. This data is then relayed to the operator, providing accurate information about the load being lifted.
Enhanced Safety and Efficiency
- Safety Enhancement:The real-time monitoring capabilities of these systems ensure that operators are aware of the load's weight and any potential overload situations. This allows for proactive measures to avoid hazardous conditions, preventing accidents and ensuring the safety of both personnel and equipment.
- Efficiency Improvement:Intelligent Load Monitoring Systems optimize the lifting process by providing precise information about load distribution. This data enables operators to adjust lifting techniques, distribute loads evenly, and minimize unnecessary maneuvers, thereby enhancing efficiency and reducing handling time.
- Preventative Maintenance:Continuous monitoring of load stresses allows for predictive maintenance. By identifying stress patterns, operators can address potential issues before they escalate, reducing downtime and extending the crane's lifespan.
Intelligent Load Monitoring Systems are a critical component in the arsenal of technologies enhancing the safety, efficiency, and longevity of Double Hoist Overhead Cranes.
Precision Control Mechanisms
Precision Control Mechanisms refer to sophisticated systems integrated into Double Hoist Overhead Cranes, offering precise and fine-tuned control over the crane's movements. These mechanisms typically involve advanced control interfaces and algorithms that regulate the crane's operations with exceptional accuracy.
Application in Double Hoist Overhead Cranes
In Double Hoist Overhead Cranes, Precision Control Mechanisms govern various aspects of crane functionality, including but not limited to:
- Hoist Movement:These mechanisms manage the acceleration, deceleration, and direction of the hoists with pinpoint accuracy, ensuring smooth and controlled lifting and lowering operations.
- Load Distribution:They enable operators to adjust load distribution between the hoists, allowing for balanced lifting and precise positioning of heavy loads.
- Collision Avoidance:Advanced control systems incorporate collision avoidance features, preventing accidental collisions between crane components or with obstacles within the operating environment.
Impact on Accuracy and Performance
- Enhanced Accuracy:Precision Control Mechanisms facilitate precise movements and positioning of loads, minimizing errors and ensuring that heavy materials are placed with utmost accuracy.
- Optimized Performance:The fine-tuned control over crane movements translates into enhanced performance. Operators can accomplish complex maneuvers efficiently, reducing operational time and increasing overall productivity.
- Minimized Wear and Tear:By enabling smoother and controlled operations, these mechanisms help reduce stress on crane components, prolonging their lifespan and minimizing maintenance requirements.
Precision Control Mechanisms represent a pinnacle of innovation in Double Hoist Overhead Cranes, elevating their capabilities and setting higher standards for accuracy and performance.
Advantages and Benefits of Integrated Hoist Technologies
Increased Efficiency in Operations
Integrated hoist technologies in Double Hoist Overhead Cranes significantly contribute to operational efficiency by:
- Reducing Downtime:Enhanced control mechanisms and load monitoring systems streamline operations, minimizing downtime associated with load adjustments and equipment malfunctions.
- Optimizing Workflows:Precision control mechanisms and Variable Frequency Drives (VFDs) enable smooth and precise movements, allowing for faster and more efficient completion of tasks.
- Minimizing Material Handling Time:Intelligent load monitoring systems facilitate optimal load distribution, reducing the time needed to handle and position heavy materials.
Enhanced Safety Measures
The incorporation of advanced hoist technologies prioritizes safety in various ways:
- Real-time Monitoring:Intelligent Load Monitoring Systems continuously monitor load stresses, allowing operators to prevent potential overloads and avoid unsafe operating conditions.
- Collision Avoidance Features:Precision Control Mechanisms often include collision avoidance features, minimizing the risk of accidents and ensuring a safer working environment.
- Improved Operator Awareness:Hoist technologies provide operators with real-time data and finer control, enhancing their ability to foresee and react to potential safety hazards.
Improved Precision and Control
Integrated hoist technologies offer unparalleled precision and control:
- Accurate Load Positioning:Precision Control Mechanisms enable precise movements and positioning of loads, reducing errors and improving overall accuracy.
- Fine-tuned Operations:Variable Frequency Drives (VFDs) and other control systems allow for gradual and controlled movements, minimizing load swing and ensuring smoother operations.
- Data-Driven Decision Making:Hoist technologies provide operators with crucial data insights, empowering them to make informed decisions for optimal load handling.
Cost-effectiveness and ROI
These technologies contribute to cost-effectiveness and a positive Return on Investment (ROI):
- Reduced Maintenance Costs:Precision control mechanisms and safety features help in minimizing wear and tear on equipment, reducing maintenance requirements and associated costs.
- Energy Efficiency:Variable Frequency Drives (VFDs) optimize energy consumption, leading to reduced power usage and operational costs.
- Increased Productivity:Enhanced efficiency and minimized downtime translate to increased productivity, resulting in improved ROI over the crane's lifecycle.
The integration of these hoist technologies in Double Hoist Overhead Cranes showcases their transformative impact, from bolstering safety measures to maximizing operational efficiency and cost-effectiveness.
Challenges and Considerations
Maintenance and Upkeep of Advanced Technologies
Maintaining and upkeeping advanced hoist technologies present certain challenges:
- Specialized Expertise:Handling and maintaining sophisticated systems like Variable Frequency Drives (VFDs) or Intelligent Load Monitoring Systems require specialized knowledge and training.
- Regular Maintenance:Ensuring consistent performance demands regular inspections and maintenance schedules for these high-tech components, adding complexity to routine upkeep.
- Cost of Repairs:In the event of malfunctions, repairing or replacing advanced components can be costly, impacting operational budgets.
Initial Investment and Implementation Challenges
Deploying advanced hoist technologies involves initial hurdles:
- High Initial Costs:The upfront investment for integrating these technologies into Double Hoist Overhead Cranes can be substantial, potentially posing financial constraints for businesses.
- Integration Complexity:Implementing these technologies seamlessly within existing crane systems may require significant modifications, causing temporary disruptions in operations.
- Decision-making Process:Selecting the right technologies amidst a plethora of options can be challenging, requiring thorough research and strategic decision-making.
Training and Skill Requirements for Operators
Adapting to new technologies requires investment in workforce development:
- Specialized Training:Operators need specific training to effectively operate and manage the advanced features of Double Hoist Overhead Cranes, necessitating additional training programs.
- Skill Enhancement:Ensuring that operators possess the skills to interpret and act upon the data provided by these technologies is crucial for maximizing their benefits.
- Transition Period:It may take time for operators to become proficient in handling these advanced systems, potentially affecting initial productivity.
Addressing these challenges involves a strategic approach, including investing in training programs, budgeting for maintenance, and careful planning during the implementation phase.
Case Studies or Examples
Applications of Double Hoist Overhead Cranes with integrated advanced hoist technologies span across various industries:
- Manufacturing Sector:In automotive manufacturing plants, Double Hoist Overhead Cranes equipped with Intelligent Load Monitoring Systems have revolutionized the assembly line. These cranes efficiently handle heavy car components, ensuring precise positioning and optimized workflows, enhancing overall productivity.
- Construction Industry:High-rise construction projects employ Double Hoist Overhead Cranes with Variable Frequency Drives (VFDs) and Precision Control Mechanisms. These technologies enable controlled lifting and placement of construction materials, contributing to the timely completion of projects while ensuring safety at great heights.
- Warehousing and Logistics:Logistics warehouses benefit from Double Hoist Overhead Cranes equipped with Advanced Control Systems. These cranes efficiently manage the movement of goods, maximizing storage space utilization and expediting the loading and unloading process.
Success Stories and Performance Enhancements
Several success stories highlight the performance enhancements achieved through the integration of advanced hoist technologies:
- Increased Throughput:Companies leveraging Double Hoist Overhead Cranes with VFDs and Intelligent Load Monitoring Systems report significant increases in throughput, allowing for more tasks to be completed within the same timeframe.
- Enhanced Safety Records:Success stories emphasize improved safety records attributed to the precision control mechanisms and real-time monitoring capabilities of these advanced technologies.
- Cost-efficiency and ROI:Businesses have experienced notable cost savings in maintenance and energy consumption while achieving a higher Return on Investment (ROI) due to increased operational efficiency.
These case studies underscore how the implementation of advanced hoist technologies in Double Hoist Overhead Cranes has led to tangible performance enhancements, ensuring safer, more efficient, and cost-effective operations.
Wrap it Up,
The integration of advanced hoist technologies, including Variable Frequency Drives (VFDs), Intelligent Load Monitoring Systems, and Precision Control Mechanisms, has redefined the capabilities of Double Hoist Overhead Cranes. These technologies offer precise control, enhanced safety measures, and increased operational efficiency, transforming the way heavy loads are lifted and handled in industrial and construction settings.
Benefits:
Enhanced Efficiency:Advanced technologies optimize operations, reduce downtime, and streamline workflows.
Safety Enhancement:Real-time monitoring and control mechanisms prioritize safety, preventing accidents and ensuring a secure working environment.
Precision and Control:These technologies enable precise movements and load management, improving overall accuracy and control.
Cost-effectiveness:While initially requiring investment, these technologies offer long-term cost savings and increased productivity.
Challenges:
Maintenance and Expertise:Ensuring proper maintenance and having specialized expertise for these technologies pose ongoing challenges.
Initial Investment:The high initial costs and complexities associated with integration can be barriers for some organizations.
Training Needs:Operator training and skill enhancement are essential for harnessing the full potential of these advanced systems.
This marks the beginning of a transformative era where Double Hoist Overhead Cranes, empowered by advanced hoist technologies, will continue to redefine the standards of lifting and handling heavy loads.