Explosion-Proof Standards: ATEX, IECEx, GB Comparison
Overview of Explosion-Proof Standards
Explosion-proof standards are a set of safety guidelines designed to protect equipment used in hazardous environments, like steel mills or chemical plants, from explosions. These standards ensure that machinery, such as overhead cranes, can safely operate in areas with explosive gases, vapors, or dust.
For industrial cranes, explosion-proof standards determine how equipment is built, tested, and maintained to prevent ignition. These standards are critical because any failure in the equipment could lead to catastrophic accidents, injuries, or damage.
Why Comparing ATEX, IECEx, and GB Standards is Crucial for Buyers
When it comes to choosing the right explosion-proof crane, understanding different standards is key. The three main sets of standards—ATEX, IECEx, and GB—are all designed to keep equipment safe, but they come from different parts of the world and have their own unique requirements.
Here’s why comparing them matters:
- Global Applicability: If you’re buying cranes for a facility in Europe, you’ll need ATEX certification. For operations in other regions, IECEx might be more suitable. If you’re based in China, then you’ll need to meet China’s GB standards.
- Safety Compliance: Choosing the right standard means meeting local safety laws and regulations. Not complying could result in fines, shutdowns, or worse—accidents.
- Ensuring Reliability: Different standards might focus on different aspects of safety. Comparing them lets you choose the right fit for your specific needs, ensuring your equipment is reliable and compliant with safety guidelines.
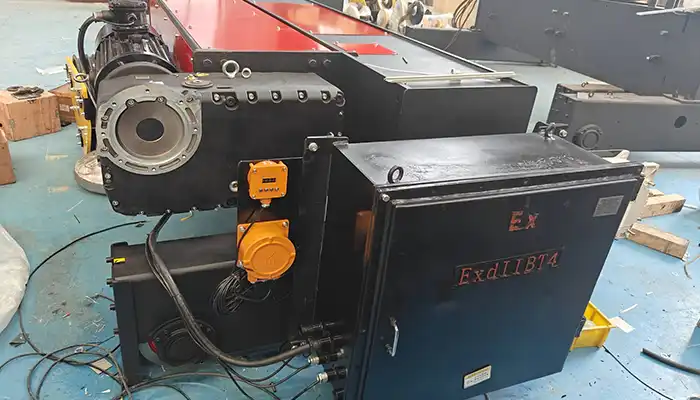
Explosion-Proof Standards
What Does "Explosion-Proof" Mean in the Context of Cranes and Other Heavy Equipment?
"Explosion-proof" refers to equipment designed to operate safely in hazardous environments where there is a risk of an explosion. In the context of cranes and other heavy equipment, it means that the crane is built to contain any sparks, heat, or electrical faults that might cause an explosion.
For example, when a crane operates in areas with flammable gases or dust, such as a chemical plant or steel mill, there’s a chance of an ignition. Explosion-proof cranes are specifically designed so that if any electrical components malfunction, the explosion will be contained within the equipment. This prevents sparks from reaching the hazardous atmosphere around it.
Role of Explosion-Proof Standards in Ensuring Safety in Hazardous Environments
In places like steel mills, chemical plants, and mines, hazardous materials—such as gases, vapors, or dust—are often present. These environments are highly volatile, meaning any small spark or electrical malfunction could trigger an explosion. That’s where explosion-proof standards come in. They guide manufacturers in designing equipment that minimizes these risks.
Here’s how explosion-proof standards play a crucial role:
- Protecting Workers: Explosion-proof equipment keeps workers safe by reducing the chances of ignition in dangerous areas. By ensuring that cranes and other machinery are built to strict safety standards, they help prevent accidents that could cause injuries or fatalities.
- Preventing Equipment Damage: Explosion-proof standards also help protect the machinery itself. When cranes meet these standards, they are built to withstand the harsh conditions of explosive environments, reducing the risk of costly damage or breakdowns.
- Ensuring Compliance: Following explosion-proof standards is not just about safety—it’s also about compliance with local regulations. In many countries, it’s a legal requirement for equipment used in hazardous areas to meet specific explosion-proof standards. This helps companies avoid fines and legal issues.
By ensuring that cranes and other heavy equipment meet these standards, companies can maintain a safe and compliant working environment.
ATEX Standards
Definition and Scope:
Origin and Application in the European Union (EU)
ATEX (ATmosphères EXplosibles) is a European standard for equipment used in explosive atmospheres. It was developed by the EU to ensure safety in industries where explosive gases, vapors, or dust are present. The ATEX directive provides a framework for equipment manufacturers and employers to follow, ensuring that machinery can operate safely in hazardous environments.
ATEX applies to a wide range of industries, including chemical processing, oil and gas, mining, and steel mills. Any equipment or system used in these environments must meet ATEX standards to prevent accidents caused by explosions.
Classification of Equipment and Zones
ATEX standards classify hazardous environments based on the likelihood of explosive atmospheres. The classification is divided into two main parts:
Zones for Gases (Zone 0, 1, 2):
- Zone 0: An area where an explosive atmosphere is continuously present or present for long periods.
- Zone 1: An area where an explosive atmosphere is likely to occur in normal operation.
- Zone 2: An area where an explosive atmosphere is not likely to occur under normal operation but may exist for a short time.
Zones for Dust (Zone 20, 21, 22):
- Zone 20: A place where combustible dust is present in the air continuously or for long periods.
- Zone 21: A place where combustible dust is likely to be present under normal operating conditions.
- Zone 22: A place where combustible dust is not likely to occur, but may be present for a short time.
The equipment used in these zones must be designed and tested accordingly.
Key Requirements:
Equipment Category Classification
ATEX classifies equipment into three categories, based on the level of protection needed:
- Category 1: Equipment that can be used in Zone 0 (high protection level).
- Category 2: Equipment that can be used in Zone 1 (moderate protection level).
- Category 3: Equipment suitable for use in Zone 2 (low protection level).
This classification helps manufacturers design equipment with the appropriate level of safety for the specific zone it will be used in.
Protection Levels (Ex e, Ex d, etc.)
ATEX uses different protection levels to define how equipment will prevent explosions. Some common types of protection include:
- Ex e: Increased safety – This protection level ensures that electrical parts don’t overheat or spark under normal operating conditions.
- Ex d: Flameproof – This protection level is designed to contain any explosion inside the equipment and prevent it from igniting the surrounding atmosphere.
- Ex i: Intrinsic safety – This method limits the electrical energy in the equipment to prevent sparks or heat that could cause an explosion.
- Ex m: Encapsulation – The equipment is completely sealed to prevent dust or gas from entering and causing ignition.
Each protection level is suited for specific types of explosive environments, depending on the nature of the risk.
Certification Process:
Involvement of Notified Bodies
To comply with ATEX, manufacturers must work with Notified Bodies, which are independent organizations authorized by the EU. These bodies assess the equipment and ensure it meets all ATEX requirements. The role of a Notified Body includes:
- Evaluating the design and construction of the equipment.
- Testing the equipment in real-world conditions.
- Issuing certificates confirming compliance with ATEX standards.
Without this certification, equipment cannot be legally sold or used in explosive atmospheres in the EU.
Documentation and Testing
Once the equipment passes testing, manufacturers must provide documentation that proves compliance with ATEX standards. This includes:
- Technical documentation: Detailed descriptions of the design, function, and safety features of the equipment.
- Risk assessments: Identifying potential hazards and how they are mitigated.
- Test results: Showing how the equipment was tested to meet the safety requirements.
This documentation must be available for inspection by regulatory bodies and customers to ensure that the equipment is safe to use in hazardous environments.
IECEx Standards
Definition and Scope:
International Certification System for Explosion Protection (Origin and Reach)
IECEx (International Electrotechnical Commission Explosive Atmospheres) is a global certification system for explosion protection, developed by the International Electrotechnical Commission (IEC). Its purpose is to ensure the safety of electrical and mechanical equipment in environments where there is a risk of explosion, such as chemical plants, oil refineries, and mines.
The IECEx system is recognized internationally, making it easier for manufacturers and buyers to comply with global standards. Unlike regional standards like ATEX, IECEx aims for worldwide standardization, ensuring that equipment meets consistent safety requirements no matter where it is used.
Key Features of IECEx
- Global Reach: IECEx operates internationally, making it the preferred standard for equipment used in explosive environments across borders.
- Cross-Border Compatibility: Because many countries adopt IECEx standards, equipment certified under IECEx can be used in various regions without the need for additional testing or re-certification.
- Unified Approach: IECEx provides a single set of standards that apply to both equipment and personnel working in hazardous areas, streamlining certification processes.
Key Requirements:
Equipment Types and Protection Techniques
IECEx categorizes equipment based on the protection techniques used to ensure safety in explosive atmospheres. Some common protection methods include:
- Flameproof (Ex d): Equipment designed to contain any explosion within the enclosure.
- Intrinsic Safety (Ex i): Limits the energy in electrical circuits to prevent sparks or heat that could cause an explosion.
- Increased Safety (Ex e): Equipment designed to prevent sparks and overheating under normal operating conditions.
- Dust Protection (Ex t): Protection against dust explosions, often using sealed enclosures.
These protection methods ensure that equipment remains safe under different operational conditions, depending on the type of explosive risk in the area.
Global Standardization and Cross-Border Compatibility
One of the key advantages of IECEx is its focus on global standardization. Many countries and regions—including the Middle East, Asia, and Australia—recognize IECEx certification. This makes it easier for manufacturers to sell equipment across international markets without needing separate certifications for each country.
For buyers, this means that IECEx-certified equipment can be used in multiple locations without worrying about local variations in safety regulations.
Certification Process:
IECEx Certification for Equipment and Personnel
To achieve IECEx certification, both equipment and personnel must be tested and evaluated:
- Equipment Certification: Manufacturers must submit their equipment for testing and assessment by an IECEx-certified test laboratory. The equipment is checked for compliance with the relevant protection techniques and safety requirements.
- Personnel Certification: IECEx also certifies personnel working in hazardous environments, ensuring that workers have the necessary skills and knowledge to operate and maintain explosion-proof equipment safely.
International Mutual Recognition of Certifications
One of the biggest benefits of IECEx is the mutual recognition of certifications. Once equipment is certified by an IECEx-approved organization, it can be accepted in any country that is part of the IECEx system. This eliminates the need for additional testing or certification, saving time and costs for manufacturers.
For example, a crane manufacturer in Europe can export IECEx-certified equipment to Australia, the Middle East, or other regions, and the equipment will be accepted without further verification, as long as it meets the IECEx standards.
European style explosion proof overhead crane double girder 3 ton to 80 ton for industrial hazardrous environment and applications.
China’s GB Standards
Definition and Scope:
Overview of GB Standards for Explosion-Proof Equipment in China
China’s GB (Guobiao) standards are national standards for industrial equipment, including explosion-proof machinery used in hazardous environments. These standards are similar to ATEX and IECEx but are tailored to meet the specific needs and regulations in China. The GB standards cover a wide range of industries, from mining to petrochemical plants, ensuring that equipment used in explosive atmospheres is designed, tested, and maintained to prevent ignition.
China’s GB standards are mandatory for all equipment used in explosive atmospheres within the country, and they play a significant role in ensuring safety for workers and minimizing accidents in high-risk environments.
Scope and Regulatory Authorities Involved
The State Administration for Market Regulation (SAMR) is the primary regulatory body overseeing the implementation of GB standards. SAMR monitors compliance with the GB explosion-proof standards and is responsible for testing, certification, and enforcement across various industries. Other organizations, such as the China National Center for Explosion Protection and Electrical Apparatus (CNCEPA), are involved in testing and certification processes.
These authorities ensure that manufacturers and operators comply with the required safety measures, making sure that equipment is safe for use in explosive atmospheres.
Key Requirements:
Chinese Equipment Classification System (Zones, Protection Methods)
China’s GB standards classify explosive environments into zones, similar to ATEX and IECEx, to determine the level of protection needed for equipment. The classification is based on the likelihood of an explosive atmosphere:
Zones for Gases:
- Zone 0: An area where explosive gas is present continuously or for long periods.
- Zone 1: An area where explosive gas is likely to occur under normal operating conditions.
- Zone 2: An area where explosive gas is not likely to occur, but may be present for short periods.
Zones for Dust:
- Zone 20: An area where combustible dust is present continuously or for long periods.
- Zone 21: An area where combustible dust is likely to be present under normal conditions.
- Zone 22: An area where combustible dust is unlikely to be present, but may be present for short periods.
The protection methods in China’s GB standards include flameproof (Ex d), intrinsic safety (Ex i), and increased safety (Ex e), among others. These methods ensure that equipment is built to prevent ignition in these specific environments.
Specific Features of Chinese Explosion-Proof Equipment
Chinese explosion-proof equipment is designed to meet the strict requirements of the GB standards, ensuring it performs reliably in hazardous conditions. Some of the specific features include:
- Stronger Construction: Chinese explosion-proof equipment often has reinforced enclosures and components to withstand the harshest conditions found in high-risk environments.
- Adaptation to Local Conditions: GB standards account for specific environmental and operational conditions in China, such as high humidity and temperature variations in certain regions.
- High-Level Protection: Equipment certified under GB standards is built to the highest protection levels, ensuring that it can operate safely even in the most explosive atmospheres.
Certification Process:
China’s State Administration for Market Regulation (SAMR) Oversight
The SAMR is responsible for ensuring that all explosion-proof equipment in China complies with GB standards. Manufacturers must submit their products to SAMR-approved test labs for evaluation. These labs assess the equipment to ensure it meets all necessary safety requirements before it can be sold and used in China.
The SAMR also oversees the certification of manufacturing facilities to ensure that they maintain consistent quality control and adhere to safety standards.
Testing, Marking, and Inspection Procedures
To comply with GB standards, explosion-proof equipment must undergo rigorous testing, which includes:
- Electrical and Mechanical Testing: Ensuring that all electrical components and mechanical parts meet the required safety thresholds.
- Explosion Tests: Simulating explosive conditions to ensure that the equipment can withstand and contain an explosion if it occurs.
- Marking: Once the equipment is certified, it is marked with the appropriate certification symbols to indicate compliance with the GB standards. This marking ensures that the equipment is recognized as safe for use in hazardous environments.
- Regular Inspections: After certification, ongoing inspections are required to ensure that the equipment continues to meet the GB standards throughout its operational life.
In summary, China’s GB standards provide comprehensive guidelines for explosion-proof equipment, ensuring that machinery used in hazardous environments is built to strict safety standards. Compliance with these regulations helps minimize risks and ensures a safe working environment.
Key Differences and Similarities Between ATEX, IECEx, and GB Standards
Scope and Global Reach:
Regional Focus vs. International Applicability
- ATEX: ATEX is a European Union (EU) standard specifically designed for explosive atmospheres within the EU. While it’s mainly recognized in Europe, many countries outside the EU may also use ATEX-certified equipment due to its reputation for high safety standards.
- IECEx: IECEx is a globally recognized certification system that ensures compatibility across countries and regions. It aims to provide a unified approach to explosion protection, and its standards are accepted in multiple international markets, including the Middle East, Asia, and Australia.
- GB: China’s GB standards are primarily focused on the Chinese market, with mandatory certification for equipment used in explosive environments within China. However, some international companies that do business in China may be required to follow GB standards as well.
In short, ATEX is regionally focused (EU), IECEx is internationally applicable, and GB is centered around China, with varying degrees of cross-border recognition.
Certifications and Compliance:
Regulatory Bodies and Approval Processes
- ATEX: In the EU, ATEX equipment certification is overseen by Notified Bodies, which are independent organizations authorized to assess and certify equipment for compliance with ATEX standards. The European Commission provides oversight of the directive’s implementation.
- IECEx: IECEx certification is managed by IECEx-approved certification bodies and recognized testing laboratories across the world. Equipment must undergo rigorous testing and meet IECEx standards before it can be certified.
- GB: China’s State Administration for Market Regulation (SAMR) is responsible for overseeing the certification and approval processes for explosion-proof equipment within China. SAMR ensures that products meet the required GB standards before they can be marketed.
In terms of approval processes, ATEX and IECEx are handled by independent, third-party organizations, while GB is overseen by a central governmental body in China.
Equipment Classification and Protection Techniques:
Variations in Protection Methods (Flameproof, Intrinsic Safety, etc.)
While all three standards classify equipment based on the risk levels of explosive atmospheres, the terminology and classification can vary slightly:
- ATEX: ATEX uses categories to classify equipment based on zones (e.g., Zone 0, 1, 2 for gases and Zone 20, 21, 22 for dust). Protection techniques include Ex d (flameproof), Ex e (increased safety), Ex i (intrinsic safety), and more.
- IECEx: Similar to ATEX, IECEx also uses zone classifications (e.g., Zone 0, 1, 2 for gases and Zone 20, 21, 22 for dust) and has protection methods like Ex d, Ex e, Ex i, and Ex m (encapsulation).
- GB: China’s GB standards also classify hazardous areas into zones (e.g., Zone 0, 1, 2 for gases and Zone 20, 21, 22 for dust) but might also include Ex n (non-sparking) protection in some cases. Protection methods are similar, such as flameproof (Ex d) and intrinsic safety (Ex i), with a focus on local environmental conditions.
The main differences lie in the classification specifics, with GB standards sometimes introducing local variations, and ATEX and IECEx focusing more on globally standardized terms.
Testing and Inspection Procedures:
Differences in Standards for Testing and Quality Assurance
- ATEX: Testing for ATEX certification involves rigorous evaluation of the equipment’s design, safety mechanisms, and performance under hazardous conditions. Notified Bodies conduct these tests, including assessments of materials, electrical components, and mechanical integrity.
- IECEx: IECEx follows a similar approach to ATEX but has more standardized global processes in place. Testing must be performed by IECEx-approved testing laboratories, and a full evaluation of equipment and personnel safety is required. The certification also extends to personnel working in explosive atmospheres, ensuring they are trained and competent.
- GB: GB standards require extensive local testing and inspection by authorized labs in China. The process involves both electrical and mechanical testing, as well as explosion simulations to ensure the equipment can withstand extreme conditions. In China, SAMR directly oversees the testing and approval process.
Overall, ATEX and IECEx focus on rigorous third-party testing, while GB also uses government-controlled oversight, which could impact the speed and consistency of approval in comparison to the other two.
In conclusion, while ATEX, IECEx, and GB standards all aim to ensure the safety of equipment in explosive atmospheres, they differ in their geographic focus, regulatory bodies, equipment classifications, and testing procedures. The key is understanding which standard applies to your equipment based on where it will be used and ensuring full compliance with the relevant regulations to maintain safety and legal conformity.
Comparative table outlining the key aspects of ATEX, IECEx, and China’s GB Standards for explosion-proof equipment:
Aspect | ATEX Standards | IECEx Standards | China’s GB Standards |
---|---|---|---|
Scope | European Union (EU) | International (Global) | China (Domestic) |
Geographic Focus | EU, with some international recognition | International, widely recognized in multiple regions | Primarily China, with some international recognition |
Regulatory Authority | European Commission, Notified Bodies | IECEx-approved Certification Bodies | State Administration for Market Regulation (SAMR) |
Equipment Classification | Zones (0, 1, 2 for gases; 20, 21, 22 for dust) | Zones (0, 1, 2 for gases; 20, 21, 22 for dust) | Zones (0, 1, 2 for gases; 20, 21, 22 for dust) |
Protection Methods | Flameproof (Ex d), Intrinsic Safety (Ex i), Increased Safety (Ex e), Others | Flameproof (Ex d), Intrinsic Safety (Ex i), Increased Safety (Ex e), Others | Flameproof (Ex d), Intrinsic Safety (Ex i), Others |
Certification Process | Tested by Notified Bodies, CE marking required | Tested by IECEx-approved labs, IECEx marking | SAMR oversight, testing by local certified labs |
Testing Procedures | Electrical and mechanical testing, explosion simulations | Electrical and mechanical testing, explosion simulations | Electrical, mechanical testing, explosion simulations |
Mutual Recognition | Recognized within the EU and some international markets | International mutual recognition | Primarily within China, with some international recognition |
Personnel Certification | No personnel certification required | Personnel certification (IECEx Certified Personnel) | No personnel certification required |
Validity and Renewals | Valid in the EU and other recognized regions | Valid worldwide where IECEx is recognized | Valid in China, with no automatic international recognition |
Marking | Ex marking, zone classification (e.g., Ex II 2 G) | Ex marking, zone classification (e.g., Ex d IIC T4) | Ex marking, zone classification (e.g., Ex d IIC T4) |
This table highlights the key differences and similarities between ATEX, IECEx, and China’s GB Standards, helping you compare their geographic reach, certification processes, and testing procedures.
VII. Which Standard is Best for Your Crane Needs?
Choosing the right explosion-proof standard for your crane is crucial to ensure safety, compliance, and optimal performance in hazardous environments. Here are the key considerations crane buyers should take into account:
Considerations for Crane Buyers in Hazardous Environments:
Location of Operation (EU, China, or Other International Regions)
- If your crane will operate in the EU: You will likely need to comply with ATEX standards. ATEX is the mandatory standard for explosive atmospheres in the EU, and it ensures that equipment meets strict safety guidelines for use in hazardous environments like steel mills, chemical plants, and mines.
- If your crane is for China: GB standards are the regulatory requirement. These standards are enforced by the State Administration for Market Regulation (SAMR) and are mandatory for any equipment used in explosive atmospheres within China.
- For International Operations (Outside EU and China): If you’re operating in multiple countries, or in regions that do not have strict local regulations, IECEx could be the most practical option. It provides internationally recognized certification that is accepted in a wide range of countries, including Australia, the Middle East, and many parts of Asia.
Compatibility with Local and International Safety Regulations
- It’s important to consider whether your equipment will be used solely in one country or region, or if it will be deployed in multiple regions across the globe.
- ATEX and IECEx standards are compatible with many international regulations, making them suitable for multinational operations. However, GB standards are tailored to China, and using GB-certified equipment outside of China may present compatibility challenges.
- IECEx might offer the most flexibility if your operations span multiple countries with varying safety regulations, as it is globally recognized and promotes mutual certification acceptance.
Certification Costs and Lead Times
- ATEX and IECEx certifications typically involve a comprehensive testing and approval process. The costs associated with certification can vary depending on the complexity of the equipment, testing requirements, and the certification body.
- ATEX certification, being region-specific, might be more expensive in terms of time and cost if you’re operating outside of the EU due to additional compliance requirements.
- IECEx might offer more streamlined certification processes for global operations, reducing the need for separate certifications in each country.
- GB standards might be less expensive and faster for companies based in China since the certification process is localized, but it may be harder to obtain approval if you want to export the equipment outside of China.
How to Choose the Right Explosion-Proof Standard for Your Crane
Determine Your Primary Market
- If you’re operating within the EU, ATEX certification is the clear choice.
- For China-based operations, GB standards should be your focus.
- For global operations or when dealing with multiple regions, IECEx offers broader international acceptance.
Assess the Hazards in Your Work Environment
- Identify whether your crane will be used in areas with highly explosive gases or combustible dust. Each standard classifies zones (e.g., Zone 0, Zone 1, Zone 2), and understanding the specific hazards in your environment will guide your protection method choices (e.g., Ex d for flameproof, Ex i for intrinsic safety).
Evaluate Local Regulatory Requirements
- Make sure to research and comply with local regulations, especially if you’re exporting equipment. If you’re building cranes for international projects, using IECEx certification can ensure compatibility across borders without the need for multiple certifications.
Consider Budget and Lead Time
- For smaller operations or if you’re only operating in China, GB standards may be a cost-effective and efficient choice.
- For multinational companies or operations in high-risk environments, IECEx offers a more versatile and internationally recognized certification, albeit at potentially higher costs and longer lead times.
Conclusion
Key Takeaways for Crane Buyers:
- ATEX, IECEx, and GB standards are all designed to ensure safety for cranes used in explosive environments, but each has a different scope of application and geographic focus.
- ATEX is best for operations in the EU, while IECEx is ideal for global operations or regions with international trade. GB standards are the primary certification for China-based operations.
- It’s essential to choose the appropriate certification based on where your crane will operate, local regulatory requirements, and the nature of the explosive hazards.
Final Recommendations Based on Industry Needs and Operational Regions:
- For EU-based companies: Ensure that your crane complies with ATEX standards for seamless integration with local regulations.
- For operations in China: Stick to GB standards for compliance with national regulations and smoother approval processes.
- For international companies or multi-region operations: IECEx offers the best flexibility and global recognition, making it a good choice for businesses looking to ensure safety and compliance across borders.
By selecting the right explosion-proof standard for your crane, you ensure not only regulatory compliance but also the safety of your workers and the longevity of your equipment in hazardous environments.