High-Capacity Grab Bucket Cranes for Metal Industry Operations
Efficient 10-50 ton grab bucket cranes for handling scrap, raw materials, and bulk loads in steel mills, foundries, and recycling plants.
High-Capacity Grab Bucket Cranes 10 Ton to 50 Ton for Metal Industry Operations":
Grab Bucket Crane
The metal industry handles large volumes of materials daily. Efficient material handling is essential to maintain smooth operations. From raw materials to finished products, the movement of goods needs to be fast and safe. Without the right equipment, productivity can suffer.
Cranes play a central role in managing these operations. They are used for lifting and moving materials throughout the facility. In large-scale operations, like steel mills and recycling plants, choosing the right crane is crucial for keeping everything on track.
Importance of High-Capacity Grab Bucket Cranes
- Heavy Material Handling: Grab bucket cranes can lift and move large volumes of materials with ease.
- Safety and Efficiency: They reduce manual labor and speed up the loading and unloading process.
- Reliability: Built to operate in tough environments, these cranes are durable and dependable.
High-capacity grab bucket cranes, ranging from 10 tons to 50 tons, are essential for the metal industry. Whether handling scrap metal, ores, or finished products, these cranes ensure the movement of heavy materials happens without delay. They offer the strength and reliability needed to keep operations running efficiently.
grab bucket crane for steel scrap handling
What Are High-Capacity Grab Bucket Cranes?
High-capacity grab bucket cranes are specialized lifting machines used to handle bulk materials in industries like metal processing. These cranes feature a "grab" bucket attached to the end of a lifting arm, designed to efficiently pick up and move large quantities of materials.
Working Principle of Grab Bucket Cranes
- Hydraulic or Electric Power: The crane is powered by hydraulic or electric systems that control both the lifting and the opening/closing of the grab bucket.
- Lifting and Grabbing: The crane’s hook lifts the grab bucket, which is designed to open and close around the material. The grab bucket then carries the material to the desired location.
- Control Mechanism: Operators control the crane through remote or onboard control panels to move the crane arm, open or close the grab bucket, and position the materials with precision.
Differences Between Grab Bucket Cranes and Other Cranes
- Bucket Mechanism: Unlike regular overhead cranes, grab bucket cranes have specialized buckets that can open and close to grab materials, making them ideal for handling bulk, loose materials like scrap metal, ores, or coal.
- Capacity and Reach: Grab bucket cranes are often used in applications that require lifting heavy, loose materials, unlike standard cranes, which may be more focused on lifting solid, pre-formed items.
- Customization: Grab bucket cranes can be fitted with different types of buckets (e.g., clamshell or orange peel) to suit specific materials, whereas other cranes may use hooks or slings.
Types of "Grab" Mechanisms
- Clamshell Grab: A bucket with two hinged parts that open and close like a clam shell. It’s ideal for handling materials like sand, gravel, or scrap metal.
- Orange Peel Grab: A bucket with multiple jaws that open and close like the peel of an orange. It’s commonly used for handling materials like scrap metal, coal, and other dense materials.
- Rotary Grab: A rotating grab that allows for better control when handling uneven loads. This is useful for unloading materials from ships or bulk storage areas.
Grab bucket cranes are designed to provide maximum control and efficiency when dealing with bulk materials, offering the flexibility needed for different materials and heavy-duty tasks.
Applications in the Metal Industry (10 Ton to 50 Ton Capacity Range)
High-capacity grab bucket cranes in the 10 ton to 50 ton capacity range are versatile machines used in various metal industry operations. These cranes are designed to handle heavy loads and perform efficiently in demanding environments.
Scrap Metal Handling
- Used in Scrap Yards: Grab bucket cranes are essential for moving large quantities of scrap metal in recycling plants and scrap yards.
- Loading and Unloading: These cranes efficiently load scrap metal onto trucks, railcars, or containers for further processing. They also unload bulk metal scrap from incoming shipments, improving operational flow.
- Precise Handling: The grab bucket allows for quick and accurate handling of scrap materials, reducing waste and increasing productivity.
Steel Mills
- Feeding Raw Materials: In steel mills, grab bucket cranes are used to move bulk raw materials like iron ore, coke, and limestone into furnaces for processing.
- Handling Finished Products: Once the metal is processed, these cranes are also responsible for moving molten metal, billets, or slabs from the furnaces to cooling areas or storage.
- Improved Efficiency: The high capacity of these cranes ensures that large volumes of materials are handled efficiently, keeping production schedules on track.
Foundries and Casting Operations
- Transporting Molten Metal: Grab bucket cranes are used to transport molten metal from furnaces to casting areas. The precision and reliability of these cranes are crucial when dealing with dangerous, high-temperature materials.
- Handling Metal Castings: After metal is poured into molds, these cranes assist in moving the finished castings to cooling or finishing areas for further processing.
- Safety and Control: The grab bucket design ensures that the handling of molten metal is secure and that any spills or accidents are minimized.
Bulk Material Handling
- Managing Raw Materials: Grab bucket cranes handle bulk materials like ores, coal, and slag in metal processing plants. They can load and unload materials from storage areas, ships, or railcars.
- Efficient Transportation: These cranes ensure that raw materials are moved efficiently throughout the plant, reducing downtime and speeding up production processes.
- Adaptability: Different grab types, such as clamshell or orange peel grabs, can be used to manage various material types, ensuring the crane is well-suited to the specific demands of the operation.
High-capacity grab bucket cranes in the 10 to 50 ton range are vital for various stages of metal processing. From handling scrap metal to transporting molten materials, these cranes offer the strength and flexibility needed for smooth, efficient operations.
Benefits of 10 Ton to 50 Ton Grab Bucket Cranes for Metal Operations
Grab bucket cranes in the 10 ton to 50 ton capacity range provide several key benefits to metal industry operations. Their robust design and versatile functionality help increase productivity while ensuring safety and cost-efficiency.
Enhanced Efficiency
- Faster Loading and Unloading: These cranes are specifically designed to handle large volumes of materials quickly. With their powerful grab mechanism, they can scoop up bulk materials in a single motion, reducing the time spent on each load.
- Improved Throughput: Faster material handling leads to better throughput, enabling the plant to process more materials in less time. This results in higher production rates and a more streamlined operation.
Cost-Effective Operations
- Reduced Equipment Needs: A 10 to 50 ton grab bucket crane can handle a wide range of tasks, reducing the need for additional cranes or machinery. This helps to lower overall equipment costs and maintenance expenses.
- Long-Term Savings: With a high lifting capacity and versatile use, these cranes can work continuously, minimizing downtime and reducing the need for frequent replacements or repairs.
Safety
- Reduced Manual Labor: Handling heavy materials manually can be dangerous, especially in high-temperature environments like steel mills. Grab bucket cranes reduce the need for manual labor, minimizing human error and the risk of injury.
- Improved Risk Management: With precise control over the grab bucket, operators can move heavy materials with great accuracy, reducing the likelihood of spills or accidents that can endanger workers.
Precision
- High-Level Control: These cranes allow for precise movements of the grab bucket, ensuring that materials are picked up, transported, and placed exactly where needed. This accuracy is essential when dealing with various materials like scrap metal, ores, or molten metal.
- Optimized Material Handling: The precise control means that operators can handle materials in a way that maximizes efficiency while preventing waste, damage, or misplacement of valuable resources.
Incorporating 10 ton to 50 ton grab bucket cranes into metal operations provides significant improvements in speed, safety, and cost-effectiveness. Their ability to handle bulk materials with precision and reliability makes them essential for smooth, high-capacity operations.
Design Features of 10 Ton to 50 Ton Grab Bucket Cranes
High-capacity grab bucket cranes are built with a variety of features to meet the demands of heavy-duty operations in the metal industry. These design elements ensure that the cranes can handle large volumes of material while maintaining safety, efficiency, and durability.
Load Capacity and Reach
- Tailored for Heavy Loads: These cranes are specifically designed to handle materials ranging from 10 tons to 50 tons. Their powerful lifting mechanisms ensure they can handle substantial loads with ease.
- Precise Reach and Span: The cranes are built with a carefully designed reach, allowing them to cover large areas and work in tight spaces. This makes them versatile, capable of moving materials across the entire plant or yard, even in areas with limited space.
Grab Bucket Types
- Clamshell Grab: This type of grab features two hinged parts that open and close like a shell. It is ideal for handling loose materials like scrap metal, sand, and gravel. The clamshell grab ensures a secure grip, preventing spillage during transport.
- Orange Peel Grab: This grab has multiple jaws that resemble the peel of an orange. It is often used for heavier, bulkier materials like scrap metal, coal, or heavy ores. The design allows for a more secure grasp, making it suitable for dense materials.
- Rotary Grab: Some cranes may also be equipped with rotary grabs that provide more control during material handling. This type is particularly useful when working with materials that require precise manipulation, such as molten metal.
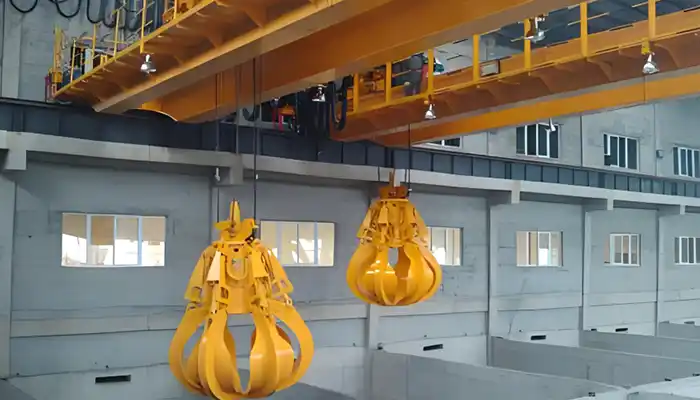
Robust Structure
- Heavy-Duty Construction: These cranes are built to withstand the harsh conditions of the metal industry. Whether in steel mills, foundries, or recycling plants, the crane’s structure is designed to handle heavy, abrasive, or even high-temperature materials.
- Durability: The materials used in the crane’s construction ensure that it can operate efficiently under continuous use. Reinforced components are made to resist wear and tear, even when exposed to extreme working conditions.
Lift Height and Rotation
- Lift Height: High-capacity grab bucket cranes are equipped with adjustable lift heights to accommodate different operational needs. Whether loading from low-ground areas or unloading from high trucks or ships, the crane’s lift height can be adjusted to provide optimal reach.
- Rotation: The crane’s arm and grab bucket can rotate, allowing for a full 360-degree range of movement. This rotation feature enhances flexibility, ensuring that materials can be placed exactly where needed, regardless of their position in the facility.
These design features make the 10 ton to 50 ton grab bucket cranes highly effective in metal industry operations. They offer precise control, robustness, and versatility, all while being built to endure the challenging environments of steel mills, foundries, and other heavy-duty settings.
Power and Control Systems
The performance and efficiency of 10 ton to 50 ton grab bucket cranes depend heavily on their power and control systems. These systems are designed to provide reliable operation, precision, and energy efficiency, making them ideal for high-demand metal industry environments.
Hydraulic and Electric Systems
- Hydraulic Power: Many high-capacity grab bucket cranes use hydraulic systems to control the movement of the crane arm and grab bucket. Hydraulic pumps provide the force needed to lift heavy loads and operate the grab mechanism. This system is known for its power and ability to handle large, heavy materials with ease.
- Electric Power: Electric motors are also commonly used in grab bucket cranes for their efficiency and precision. These motors drive the crane's lifting and rotating functions. Electric systems are often more energy-efficient and require less maintenance than hydraulic systems, making them an attractive option for many operations.
- Combined Systems: Some cranes combine both hydraulic and electric power to take advantage of the benefits of each system. This hybrid approach allows for greater lifting power and smoother, more precise operation.
Control Systems
- Precision Control: Modern grab bucket cranes feature advanced control systems that ensure smooth, accurate operation. Operators can adjust the crane’s movements with high precision, ensuring that materials are handled safely and efficiently. This includes controlling the grab bucket’s opening and closing, lift height, and arm positioning.
- Remote Controls: Many cranes are equipped with remote control systems, allowing operators to manage the crane from a safe distance. This is especially useful in environments where the crane is handling hazardous or high-temperature materials, like molten metal. Remote controls provide greater flexibility and improve safety by allowing operators to stay clear of dangerous zones.
- Automation: In some advanced systems, automation plays a role in controlling the crane's movements. Automated systems can handle routine tasks, such as loading or unloading materials, reducing the need for manual input. This not only increases efficiency but also minimizes human error, improving overall safety.
Energy Efficiency
- Energy-Saving Technologies: Modern grab bucket cranes are designed with energy efficiency in mind. Hydraulic systems are optimized to minimize energy loss, while electric systems are increasingly using variable frequency drives (VFDs) to adjust the motor’s speed based on demand. This ensures that power is used efficiently, reducing overall energy consumption.
- Regenerative Power: Some advanced cranes also feature regenerative braking systems that convert the crane's kinetic energy into electrical power. This energy can be reused within the system, reducing the overall energy requirements and lowering operating costs.
- Eco-Friendly Features: Many newer crane models are designed to meet environmental standards, using energy-efficient components and technologies that help reduce emissions and minimize the environmental impact of their operations.
The combination of hydraulic and electric power systems, alongside advanced control mechanisms, ensures that 10 ton to 50 ton grab bucket cranes operate smoothly, efficiently, and safely. Their energy-efficient designs contribute to lower operating costs while improving environmental sustainability in metal industry operations.
Customization and Adaptability
High-capacity grab bucket cranes are highly customizable to meet the specific needs of metal industry operations. Their flexibility allows them to be adapted for a variety of tasks, materials, and environments.
Tailoring Cranes to Specific Operational Needs
- Lifting Configurations: Cranes can be tailored to meet particular lifting requirements, such as adjusting the length of the arm or the lifting height to handle specific materials. This ensures that the crane can operate efficiently in different settings, from scrapyards to steel mills.
- Grab Sizes: Depending on the material being handled, the size of the grab bucket can be adjusted. Larger grabs are ideal for handling bulky scrap metal, while smaller grabs provide greater precision for handling lighter, more delicate materials.
Adjustments for Material Type
- Scrap Metal Grades: Different grades of scrap metal may require different grab types. For example, denser materials may require an orange peel grab, while lighter scrap may be handled with a clamshell grab. Customizing the crane's grab bucket ensures that the right tool is used for each material type.
- Ores and Raw Materials: Cranes can also be adapted for handling bulk ores, such as iron ore or coal. The design of the grab bucket can be modified to optimize for the density and texture of the materials, improving efficiency and preventing material loss.
- Molten Materials: Cranes working in foundries or steel mills may be equipped with special buckets or grabs designed for handling molten metal. These custom grabs are built to withstand high temperatures and maintain their shape under extreme heat.
Flexible Crane Configurations
- Adaptable to Plant Layouts: High-capacity grab bucket cranes can be configured to suit different plant layouts. Whether the crane is needed in a compact area or a large, open space, the crane can be customized for maximum reach and efficiency.
- Production Process Needs: The crane’s function can be adapted to fit various stages of production, from unloading raw materials to transporting finished products. Customization allows cranes to handle a wide range of tasks in different areas of the plant.
Case Studies
Real-world applications of high-capacity grab bucket cranes show their significant impact on efficiency, safety, and cost reduction in the metal industry. Below are two case studies that highlight the effectiveness of these cranes in different sectors.
Case Study 1: A Steel Mill Using a 30-Ton Grab Bucket Crane for Raw Material Loading
Challenges: The steel mill was facing delays in the loading and transport of raw materials, including iron ore and coal, into the furnace. The existing cranes were underperforming, leading to bottlenecks in the production process.
Solution: A 30-ton grab bucket crane was introduced to handle the heavy materials with a faster and more reliable system. The crane was equipped with a hydraulic power system and a large clamshell grab, designed specifically for bulk material handling.
Results:
- Efficiency Gains: The crane reduced the loading time by 40%, allowing for quicker turnaround times between shipments and improved furnace operation.
- Safety Improvements: By automating the material handling process, the crane reduced manual labor in hazardous areas, minimizing accidents and improving worker safety.
- Cost Reduction: The efficient operation of the crane led to a 15% reduction in operational costs, as the mill was able to increase throughput without additional labor or equipment investments.
Case Study 2: A Recycling Facility Leveraging a 15-Ton Grab Bucket Crane for Scrap Metal Handling
Challenges: The recycling facility was struggling with inefficient scrap metal handling. The existing cranes were not able to efficiently pick up materials from uneven piles or move large quantities of scrap quickly.
Solution: A 15-ton orange peel grab crane was installed to improve material handling. The crane's design included a high-precision control system and robust grab mechanism, perfect for sorting and lifting various types of scrap metal.
Results:
- Efficiency Gains: The crane reduced the time spent moving scrap metal by 30%, enabling faster unloading of incoming shipments and more efficient sorting of metal types.
- Safety Improvements: The crane's remote control system allowed operators to safely control the crane from a distance, eliminating the risks associated with working in close proximity to heavy, unstable scrap piles.
- Cost Reduction: The facility saw a 20% reduction in labor costs as the crane automated much of the scrap handling process. Furthermore, the crane's durability reduced maintenance costs, resulting in long-term savings.
These case studies demonstrate how high-capacity grab bucket cranes improve operational efficiency, enhance safety, and reduce costs in real-world applications across the metal industry.
Future Trends and Innovations
The future of high-capacity grab bucket cranes is shaped by technological advancements and evolving industry needs. Below are some of the key trends and innovations that are expected to define the next generation of cranes.
Automation and Smart Technology
- AI and Machine Learning: The integration of AI and machine learning into crane systems allows for real-time data analysis, predictive maintenance, and automated operation. AI-driven systems can optimize crane movements, reducing the need for manual input and enhancing efficiency.
- Remote Control and Automation: Remote control technology allows operators to manage cranes from a distance, enhancing safety in dangerous environments. Fully automated cranes may be capable of completing tasks without human intervention, further increasing productivity and safety.
- Smart Sensors: Advanced sensors can monitor the crane’s performance, providing real-time data to operators and predicting potential issues before they arise. These sensors also enable better precision in material handling, improving operational accuracy.
Eco-Friendly Designs
- Energy-Efficient Technologies: New cranes are designed to consume less energy, reducing their environmental footprint. The use of regenerative power systems and energy-efficient electric motors helps lower energy consumption and costs.
- Sustainable Manufacturing: Manufacturers are focusing on using recyclable materials in the construction of cranes and adopting environmentally friendly production practices. This not only reduces waste but also ensures that the cranes are more sustainable over their lifecycle.
- Zero-Emission Cranes: Some crane manufacturers are working toward developing electric-powered cranes with zero emissions. These cranes will help reduce air pollution in steel mills, foundries, and other industrial settings, contributing to a cleaner environment.
Increased Load Capacities
- Larger Cranes for Heavy-Duty Operations: As industries push for higher production rates, the demand for cranes with greater lifting capacities is increasing. Future trends indicate the development of cranes capable of lifting more than 50 tons, allowing for the handling of even heavier materials.
- Stronger Structures: Cranes with enhanced structural integrity will be able to handle extreme weights and operate in more demanding environments. These cranes will be built with stronger materials and reinforced components to withstand the stress of lifting larger loads.
- Customization for Specialized Tasks: As industries continue to evolve, cranes will be further customized to meet the specific needs of different materials and tasks, whether that be handling molten metal, hazardous waste, or bulk ores.
The future of high-capacity grab bucket cranes will be defined by innovations in automation, energy efficiency, and load capacity. These advancements will make cranes smarter, more sustainable, and capable of handling the increasing demands of the metal industry.
Conclusion
High-capacity grab bucket cranes with lifting capacities ranging from 10 tons to 50 tons play a pivotal role in the metal industry. They are essential for managing large-scale operations, enhancing efficiency, and improving material handling processes in steel mills, recycling facilities, foundries, and other metal processing plants.
Recap of the Importance of 10 Ton to 50 Ton Grab Bucket Cranes
These cranes are designed to meet the demanding needs of the metal industry, offering powerful lifting capabilities, precise control, and the ability to handle various materials, from scrap metal to molten metal. They enable smoother and faster operations, ensuring that metal production processes can be carried out without delay.
Summary of Benefits
- Efficiency: By reducing the time needed for material handling, these cranes increase overall plant throughput, improving the productivity of operations.
- Safety: Automated controls, remote operation, and high-precision handling reduce the need for manual labor in hazardous environments, significantly enhancing worker safety.
- Cost-Effectiveness: Their ability to lift heavy loads and handle large volumes of material with minimal maintenance requirements helps lower operational costs, making them an excellent long-term investment.
As the metal industry continues to grow and evolve, the demand for high-capacity cranes will only increase. These cranes are vital in managing complex and large-scale operations efficiently and safely. The continued development of advanced technologies, energy-efficient designs, and automation will further elevate the role of grab bucket cranes in the metal industry, helping businesses stay competitive and sustainable in an ever-changing market.