Customizing Under Running Bridge Cranes for Specialized Industrial Needs
Customizing under running bridge cranes transforms them to precisely fit unique industrial demands, optimizing efficiency and safety across diverse operational environments.
Overview of Under Running Bridge Cranes
Under running bridge cranes, also known as underhung cranes, are a type of overhead crane where the bridge is supported from the roof or ceiling structure rather than from the columns. This design allows the crane to run along the bottom flange of a runway beam, which is typically suspended from the ceiling or roof structure. Under running bridge cranes are known for their flexibility and space-saving design, making them an ideal solution for various industrial applications.
These cranes are used in environments where overhead space is limited or where it's essential to maximize floor space for other operations. They are commonly found in manufacturing plants, warehouses, and assembly lines, where they facilitate the efficient movement of materials and equipment. Their ability to operate in tighter spaces without the need for additional floor supports makes them particularly valuable in industries where space optimization is crucial.
Importance of Customization in Industrial Applications
While standard under running bridge cranes offer numerous advantages, customization is often necessary to meet the specific operational requirements of different industries. Each industry has unique challenges and demands, such as varying load capacities, environmental conditions, and integration with other machinery. Customizing under running bridge cranes ensures that these specific needs are met, enhancing operational efficiency and safety.
Customization can involve modifying the crane's design, adjusting its capacities, and incorporating special functionalities to handle unique tasks. For instance, a manufacturing plant might need a crane with a higher lifting capacity to handle heavy machinery, while a warehouse might require a crane with advanced control systems for precise handling of fragile goods. Customization not only improves the crane's performance but also ensures compliance with industry standards and regulations, thereby minimizing risks and downtime.
Under Running Bridge Cranes
Under running bridge cranes, also known as underhung cranes, are a type of overhead crane where the bridge is suspended from the bottom flange of the runway beams. These beams are typically supported by the roof or ceiling structure, eliminating the need for additional floor columns. This design provides several distinct advantages, particularly in facilities where floor space is at a premium or where ceiling height is limited.
Key components of an under running bridge crane include:
- Bridge: The horizontal beam that spans the width of the work area and supports the trolley and hoist.
- Trolley: The mechanism that moves along the bridge, carrying the hoist and enabling lateral movement.
- Hoist: The lifting device attached to the trolley, used for raising and lowering loads.
- Runway Beams: The beams along which the bridge travels, typically attached to the ceiling or roof structure.
- Control System: The interface used by operators to control the movement of the crane, which can include pendant controls, radio controls, or automated systems.
Under running bridge cranes can be designed to handle various capacities, from light loads in assembly lines to heavy machinery in manufacturing plants. Their design allows for greater flexibility in terms of placement and movement, as the crane operates below the runway beams, maximizing overhead clearance.
Common Applications in Various Industries
Under running bridge cranes are versatile and can be utilized across a wide range of industries due to their adaptability and efficient design. Some common applications include:
- Manufacturing: In manufacturing facilities, under running bridge cranes are used to transport raw materials, move components between workstations, and handle finished products. Their ability to navigate through tight spaces and work areas makes them ideal for assembly lines and production floors.
- Warehousing and Distribution: These cranes facilitate the movement of goods within warehouses, aiding in the loading and unloading of trucks, stacking of pallets, and placement of inventory on high shelves. Their design helps optimize storage space by reducing the need for floor supports.
- Automotive Industry: In automotive manufacturing and assembly plants, under running bridge cranes are used for lifting engines, car bodies, and other heavy components. They enable precise positioning and assembly, enhancing efficiency and safety.
- Aerospace: Aerospace facilities use under running bridge cranes to handle large, delicate components like wings, fuselages, and engines. The cranes’ precise control systems ensure safe and accurate movement of these valuable parts.
- Maintenance and Repair: In maintenance workshops and repair facilities, under running bridge cranes assist in lifting and maneuvering heavy machinery and equipment, making it easier for technicians to perform their tasks.
Benefits of Using Under Running Bridge Cranes
Under running bridge cranes offer numerous benefits that make them a preferred choice in various industrial applications:
- Space Efficiency: By being suspended from the ceiling or roof structure, under running bridge cranes free up valuable floor space, allowing for more efficient use of the facility’s layout. This is particularly beneficial in cramped or congested work environments.
- Flexibility: The design of under running bridge cranes allows them to operate in tighter spaces and navigate around obstacles, providing greater flexibility in movement and placement. They can be adapted to fit irregularly shaped buildings and customized to meet specific operational needs.
- Cost-Effectiveness: Installing under running bridge cranes can be more cost-effective than top running cranes, as they do not require additional floor supports or extensive structural modifications. This makes them an attractive option for businesses looking to improve their material handling capabilities without significant capital investment.
- Ease of Installation: Due to their simpler structural requirements, under running bridge cranes are easier and quicker to install compared to other types of cranes. This minimizes downtime and disruption to ongoing operations.
- Enhanced Safety: Modern under running bridge cranes are equipped with advanced safety features, such as overload protection, anti-collision systems, and precise control mechanisms. These features help prevent accidents and ensure safe operation, protecting both personnel and equipment.
- Improved Productivity: By streamlining material handling processes and reducing manual labor, under running bridge cranes enhance productivity. They allow for faster and more efficient movement of goods, components, and equipment, ultimately contributing to higher output and operational efficiency.
In summary, understanding the basic design, functionality, and benefits of under running bridge cranes highlights their versatility and value in various industrial settings. Their ability to optimize space, provide flexibility, and enhance productivity makes them an essential tool for businesses looking to improve their material handling operations.
The Need for Customization
Diverse Operational Requirements Across Industries
Industries have unique operational requirements that often necessitate customized solutions. Each sector, from manufacturing to warehousing to construction, encounters specific challenges and demands that standard equipment may not adequately address. For instance:
- Manufacturing: In manufacturing, processes can vary widely from one product to another. A facility producing heavy machinery parts will have different lifting and movement needs compared to one manufacturing consumer electronics. The former may require cranes with higher lifting capacities and robust structures, while the latter might need more precise control systems for handling delicate components.
- Warehousing and Logistics: Warehouses dealing with diverse inventory types, from bulk goods to fragile items, need cranes that can handle various weights and sizes efficiently. Customizing cranes to include features like specialized lifting attachments or adjustable lifting speeds can significantly improve handling efficiency and safety.
- Construction: Construction sites are dynamic environments with constantly changing needs. Cranes used here must be versatile enough to handle different materials, from heavy steel beams to precast concrete elements. Customizing cranes to meet the specific demands of each project can lead to more efficient and safer operations.
Limitations of Standard Cranes in Specialized Tasks
Standard cranes are designed to meet general requirements and may not be suitable for specialized tasks that require unique capabilities. Some limitations of standard cranes include:
- Fixed Capacities: Standard cranes come with predetermined lifting capacities that may not be adequate for all tasks. Industries requiring higher or variable load capacities need customized solutions.
- Limited Flexibility: Standard cranes may lack the flexibility to operate in irregularly shaped spaces or adapt to specific environmental conditions. For example, cranes in chemical plants may need corrosion-resistant materials, which standard models may not offer.
- Basic Control Systems: Standard cranes typically come with basic control systems that might not provide the precision or automation needed for certain applications. Industries like aerospace, which require highly accurate movements, benefit from advanced control systems that can be integrated into customized cranes.
- One-Size-Fits-All Design: The generic design of standard cranes often means they cannot cater to the particularities of different operational environments. This can lead to inefficiencies, increased wear and tear, and potential safety hazards.
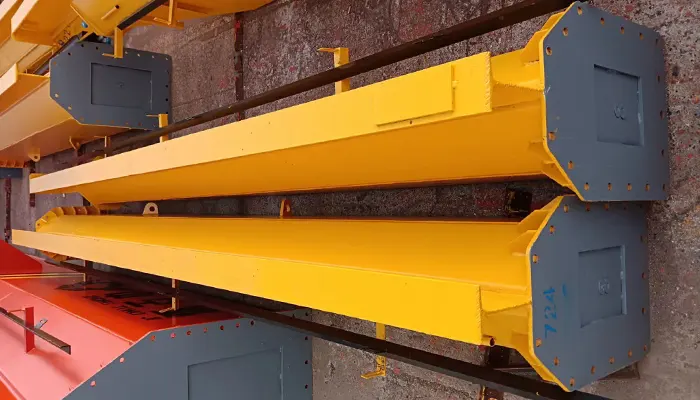
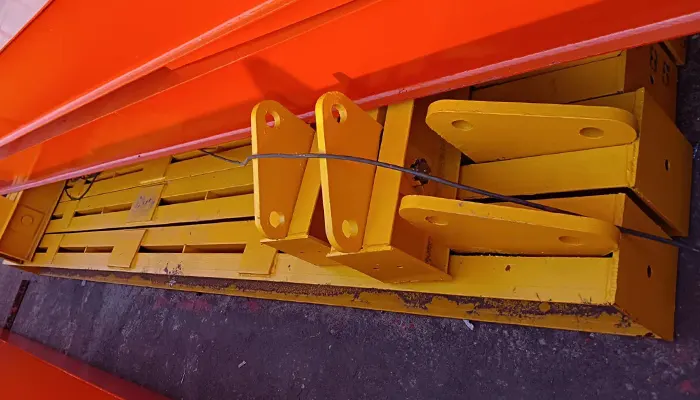
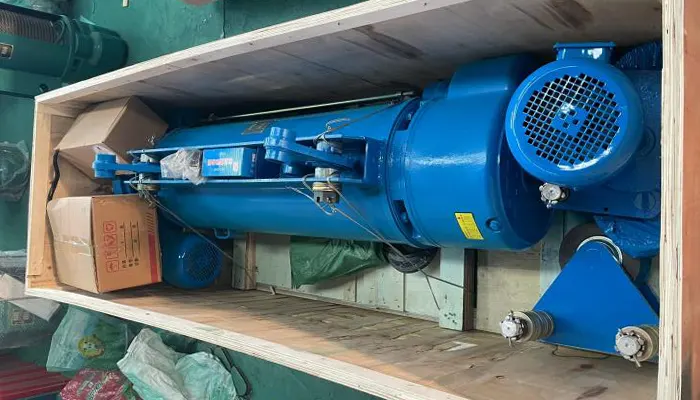
Under running bridge crane electric hoist
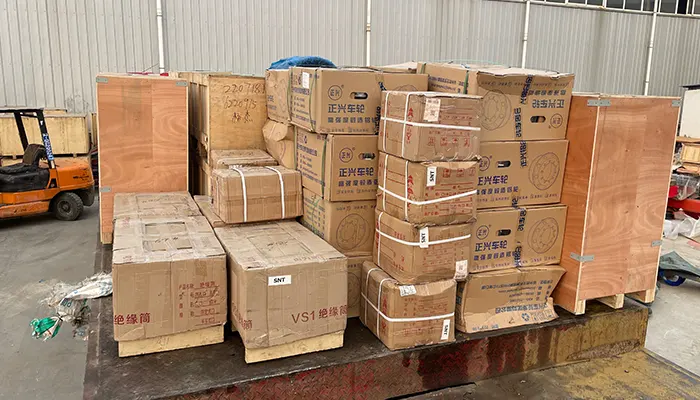
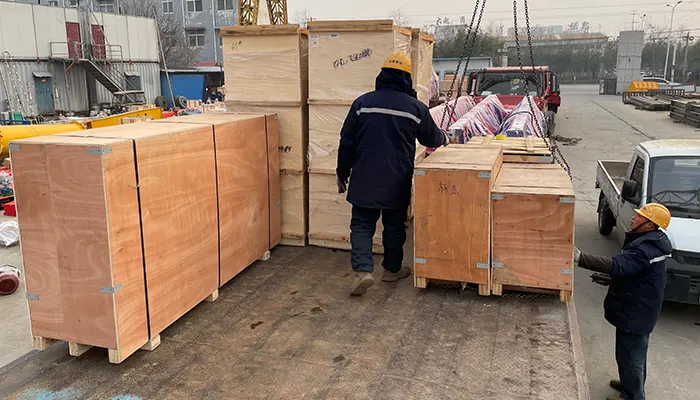
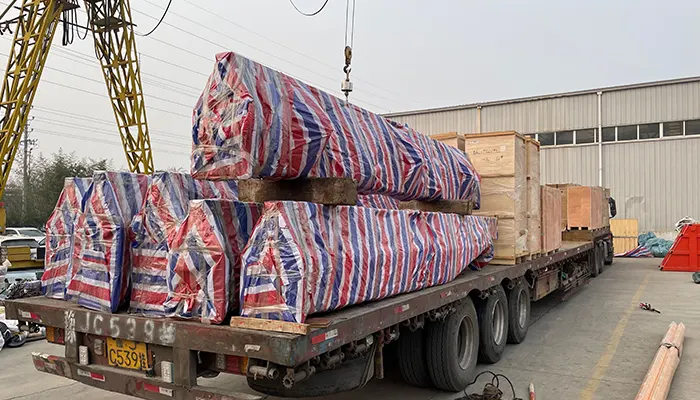
Advantages of Tailored Solutions
Customizing under running bridge cranes to meet specific operational requirements offers several significant advantages:
- Enhanced Efficiency: Tailored cranes are designed to match the exact needs of the operation, which can significantly enhance workflow efficiency. By addressing specific requirements, customized cranes reduce bottlenecks and streamline processes.
- Increased Safety: Custom solutions can include advanced safety features that are specific to the operational environment. This not only protects the workforce but also minimizes the risk of damaging expensive equipment and materials.
- Optimized Performance: Customizing a crane allows for optimization in terms of lifting capacities, control systems, and environmental adaptations. This leads to better performance and reliability in the intended application.
- Cost Savings: While the initial investment in a customized crane might be higher, the long-term benefits include reduced downtime, lower maintenance costs, and fewer operational disruptions. This results in overall cost savings and a better return on investment.
- Scalability: Custom cranes can be designed with future needs in mind, providing scalability as the business grows or as operational requirements change. This adaptability ensures the crane remains useful and relevant over a longer period.
- Improved Workflow Integration: Custom cranes can be integrated seamlessly into existing workflows and systems, ensuring a harmonious fit with other equipment and processes. This integration is crucial for maintaining continuous and efficient operations.
In conclusion, the need for customization in under running bridge cranes is driven by the diverse and specific operational requirements across various industries. While standard cranes provide general solutions, they often fall short in specialized tasks. Tailored solutions offer enhanced efficiency, safety, performance, and cost savings, making them an essential investment for industries aiming to optimize their material handling operations.
Customization Options
Design Features
Modifications to the Crane Structure
Customizing the structural design of under running bridge cranes is essential for meeting specific operational requirements and maximizing efficiency. Some key modifications include:
- Beam Design: Customizing the beam design can enhance the crane's load-bearing capacity and improve stability. For instance, beams can be reinforced or fabricated from high-strength materials to handle heavier loads or to span longer distances without sagging.
- Trolley Configuration: The trolley, which carries the hoist along the bridge, can be customized to include dual trolleys for improved load distribution or specialized trolleys designed for higher speeds and smoother operation. This customization is particularly useful in industries requiring rapid and precise material handling.
Customization for Specific Environments
Different industries operate in unique environments that can pose specific challenges. Customizing cranes to withstand these conditions ensures longevity and safety:
- Corrosion-Resistant Materials: In industries like chemical manufacturing or food processing, cranes are often exposed to corrosive substances. Using materials like stainless steel or applying protective coatings can prevent corrosion and extend the crane's lifespan.
- Explosion-Proof Designs: In environments where flammable gases or dust are present, such as in mining or petrochemical facilities, explosion-proof cranes are essential. These cranes are built with special enclosures and components to prevent sparks and contain explosions, ensuring safe operation in hazardous areas.
Capacities
Adjusting Lifting Capacities to Handle Unique Loads
One of the most critical aspects of customizing under running bridge cranes is adjusting their lifting capacities to handle specific load requirements. This involves:
- Enhanced Load Capacities: Custom cranes can be designed to lift much heavier loads than standard models, making them suitable for industries like heavy manufacturing and construction where large and heavy components are common.
- Variable Load Handling: In some industries, the weight and type of load can vary significantly. Custom cranes can be equipped with adjustable lifting capacities and smart load sensing technologies to accommodate these variations safely and efficiently.
Examples of Industries with Specialized Capacity Needs
- Heavy Manufacturing: Industries that produce large machinery or structural components require cranes with substantial lifting capacities. Custom cranes designed to handle these heavy loads ensure efficient and safe operation, preventing downtime and equipment damage.
- Aerospace: The aerospace industry often deals with large but delicate components, such as aircraft wings and fuselages. Custom cranes with precise control systems and high lifting capacities are essential to safely move these components during assembly and maintenance.
Functionalities
Enhanced Control Systems
Advanced control systems can significantly enhance the functionality and usability of under running bridge cranes:
- Remote Control: Implementing remote control systems allows operators to manage crane movements from a distance, enhancing safety and efficiency, especially in hazardous or hard-to-reach areas.
- Automated Operation: Automation technologies, including programmable logic controllers (PLCs) and sensor-based systems, enable cranes to perform repetitive tasks with minimal human intervention. This increases productivity and reduces the risk of human error.
Integration with Existing Systems
Integrating under running bridge cranes with other industrial systems can streamline operations and improve overall efficiency:
- Conveyor Belts: Custom cranes can be designed to work seamlessly with conveyor belts, enabling smooth and continuous material handling processes. This integration is vital in industries such as logistics and manufacturing, where efficient material flow is crucial.
- Robotic Arms: In high-tech manufacturing and assembly lines, integrating cranes with robotic arms can enhance precision and automation. This allows for complex tasks, such as assembling intricate components, to be performed more efficiently.
Special Lifting Attachments and Tools
Custom lifting attachments and tools can be designed to handle specific types of loads or to perform particular tasks:
- Specialized Hooks and Grabs: Different industries require different lifting attachments, such as magnetized hooks for metalworking, vacuum grabs for delicate materials, or special clamps for irregularly shaped objects.
- Custom Spreader Beams: For lifting long or awkwardly shaped loads, spreader beams can distribute the weight evenly and provide additional stability. These can be customized to match the exact dimensions and weight distribution needs of the load.
In conclusion, the customization options for under running bridge cranes are vast and varied, catering to the specific needs of different industries. By modifying design features, adjusting lifting capacities, and enhancing functionalities, businesses can ensure their cranes are perfectly suited to their operational requirements, leading to improved efficiency, safety, and productivity.
Application in Different Industrial Sectors
Manufacturing Industry
Description of Specific Customization Needs
In the manufacturing industry, processes vary widely, requiring cranes that can handle diverse tasks efficiently. Common needs include lifting heavy machinery, moving large components, and transporting delicate parts without damage. For instance, a facility producing automotive parts might need cranes that can manage both heavy engine blocks and lightweight, delicate components.
Example of a Customized Under Running Bridge Crane Solution
A manufacturing plant specializing in automotive parts required a crane that could handle both heavy and light loads with precision. The customized solution included:
- Dual Hoists: One hoist with a 10-ton capacity for heavy engine blocks and another with a 2-ton capacity for lighter components.
- Enhanced Control Systems: The crane featured advanced control systems, including a remote control for precision handling and automation capabilities for repetitive tasks.
- Specialized Hooks and Attachments: Custom hooks and clamps were designed to securely lift various components, preventing damage to delicate parts.
Impact on Operational Efficiency and Productivity
The customized crane solution significantly improved the plant's operational efficiency and productivity:
- Reduced Downtime: The dual hoists allowed for quick switching between different tasks without the need for additional equipment, reducing downtime.
- Increased Precision: The advanced control systems enabled precise handling, reducing the risk of damage and rework.
- Enhanced Safety: The specialized attachments ensured secure lifting, minimizing accidents and improving overall safety.
Mining Industry
Unique Environmental and Operational Challenges
The mining industry presents harsh environmental conditions, including dust, moisture, and extreme temperatures. Cranes used in this sector must be exceptionally durable and safe, capable of handling heavy loads like ore and mining equipment while operating reliably in these challenging conditions.
Custom Solutions Implemented
To address these challenges, a mining company implemented the following custom solutions:
- Durability Enhancements: The crane was constructed with corrosion-resistant materials and protective coatings to withstand the harsh environment.
- Explosion-Proof Design: Special enclosures and components were used to make the crane explosion-proof, essential for operations in areas with flammable gases and dust.
- Heavy-Duty Capacities: The crane was designed with a lifting capacity of 15 tons to handle large mining equipment and materials.
Benefits Realized
The custom crane provided numerous benefits to the mining operation:
- Improved Reliability: The durability enhancements ensured the crane operated reliably despite the harsh conditions, reducing maintenance needs and operational interruptions.
- Enhanced Safety: The explosion-proof design and heavy-duty capacities improved safety, minimizing the risk of accidents and equipment failure.
- Increased Productivity: The crane's ability to handle heavy loads efficiently boosted overall productivity, allowing for more efficient material handling and processing.
Construction Industry
Specific Project Requirements
Construction projects often involve diverse and changing requirements, such as lifting heavy materials, transporting equipment across the site, and operating in confined spaces. Cranes in this industry need to be highly adaptable and mobile.
Custom Crane Adaptations
A construction company working on high-rise buildings required a versatile crane capable of adjusting to various project needs. The customized crane included:
- Mobility Features: The crane was equipped with wheels and a track system to allow easy movement across the construction site.
- Adjustable Spans: The crane's span could be adjusted to fit different building dimensions, providing flexibility in handling materials.
- Advanced Control Systems: Remote control and automation features enabled precise placement of materials, crucial for high-rise construction.
Success Stories and Outcomes
The customized crane led to significant success on the construction site:
- Increased Flexibility: The mobility features and adjustable spans allowed the crane to adapt to different project stages and requirements, improving workflow.
- Enhanced Precision: The advanced control systems enabled precise material placement, reducing errors and rework.
- Improved Efficiency: The crane's versatility and ease of movement across the site streamlined operations, leading to faster project completion and reduced labor costs.
In conclusion, these case studies highlight the importance and impact of customizing under running bridge cranes for specific industrial needs. Tailored solutions address unique challenges and enhance operational efficiency, safety, and productivity across various industries.
Implementing Custom Solutions
Steps in the Customization Process
Implementing custom solutions for under running bridge cranes involves several critical steps to ensure that the final product meets the specific needs and challenges of the client’s operations. Here’s a detailed look at the process:
Initial Consultation and Needs Assessment:
- Meeting with the Client: The process begins with an in-depth meeting between the crane manufacturer and the client to understand their specific needs, challenges, and operational environment.
- Site Analysis: Conducting a thorough analysis of the client's site to assess spatial constraints, load requirements, environmental conditions, and integration needs with existing systems.
Design and Engineering:
- Concept Development: Based on the needs assessment, the engineering team develops a conceptual design for the customized crane, including structural modifications, control systems, and lifting attachments.
- Technical Specifications: Detailed technical specifications are prepared, outlining the materials, dimensions, capacities, and features of the customized crane.
Client Review and Feedback:
- Presentation of Design: The initial design and specifications are presented to the client for review. Feedback is solicited to ensure that all requirements are adequately addressed.
- Revisions and Final Approval: Necessary revisions are made based on client feedback. The final design is approved by the client before moving to the manufacturing stage.
Manufacturing and Assembly:
- Fabrication: The custom crane components are fabricated according to the approved design. This may involve specialized manufacturing processes to ensure durability and performance.
- Assembly: The crane is assembled, with particular attention to integrating custom features such as enhanced control systems, specialized lifting attachments, and structural modifications.
Testing and Quality Assurance:
- In-House Testing: Before delivery, the crane undergoes rigorous testing at the manufacturer’s facility to ensure it meets all specifications and performance standards.
- Client-Site Testing: Once installed at the client’s site, additional testing is conducted to confirm the crane’s functionality in its operational environment.
Installation and Training:
- Installation: The custom crane is installed at the client’s site by experienced technicians, ensuring proper setup and alignment with existing systems.
- Training: Comprehensive training is provided to the client’s personnel on the operation and maintenance of the custom crane, ensuring they can utilize it effectively and safely.
Collaboration Between Crane Manufacturers and Clients
Effective collaboration between crane manufacturers and clients is essential for successful customization. This partnership involves:
- Open Communication: Continuous communication throughout the process ensures that the client's needs are understood and met. Regular updates and feedback loops help in making timely adjustments.
- Expert Consultation: Manufacturers provide expert advice on the best solutions for the client’s specific challenges. This includes recommendations on materials, design features, and advanced technologies.
- Joint Problem-Solving: Collaborative problem-solving helps address any issues that arise during the design, manufacturing, or installation phases, ensuring a smooth implementation process.
Importance of Detailed Needs Assessment and Planning
A detailed needs assessment and meticulous planning are crucial for the success of custom crane solutions. Here’s why:
- Accurate Requirements Gathering: A thorough needs assessment ensures that all operational requirements, constraints, and goals are clearly understood and documented. This reduces the risk of overlooking critical aspects that could affect the crane’s performance.
- Tailored Solutions: Detailed planning allows for the design of solutions that are precisely tailored to the client’s needs, rather than relying on generic, off-the-shelf options that may not fully address specific challenges.
- Risk Mitigation: Identifying potential challenges and constraints during the planning phase helps mitigate risks. This includes addressing environmental factors, load variances, and integration with existing systems.
- Cost and Time Efficiency: Proper planning helps in creating a realistic timeline and budget for the project. It ensures that resources are allocated effectively, reducing the likelihood of delays and cost overruns.
- Enhanced Performance and Safety: A well-planned custom solution not only meets performance requirements but also adheres to safety standards and regulations, ensuring safe operation and long-term reliability.
In conclusion, implementing custom solutions for under running bridge cranes involves a comprehensive process of assessment, design, collaboration, and meticulous planning. This approach ensures that the final product is perfectly suited to the client’s specific needs, enhancing operational efficiency, safety, and overall productivity.
Considerations for Customization
Budget and Cost Implications
When customizing under running bridge cranes, it is essential to carefully consider the budget and cost implications:
- Initial Investment: Custom cranes typically require a higher initial investment compared to standard models due to the specialized design, materials, and manufacturing processes involved.
- Cost-Benefit Analysis: Conducting a thorough cost-benefit analysis helps justify the initial investment by highlighting long-term benefits such as increased efficiency, reduced downtime, and lower maintenance costs.
- Budget Planning: Establishing a clear budget early in the planning process ensures that all customization requirements are met without unexpected expenses. This involves detailed discussions with the crane manufacturer to understand the cost components.
- Funding Options: Exploring various funding options, such as leasing or financing, can help manage the financial impact of the initial investment while allowing the business to benefit from the customized crane.
Compliance with Industry Standards and Regulations
Ensuring that customized cranes comply with industry standards and regulations is critical for safety and operational efficiency:
- Local and International Standards: Custom cranes must adhere to local safety regulations and international standards, such as those set by the Occupational Safety and Health Administration (OSHA) or the International Organization for Standardization (ISO).
- Certification and Inspection: Custom cranes should undergo rigorous testing and certification processes to ensure compliance. This may involve third-party inspections and certifications from recognized bodies.
- Regulatory Updates: Staying informed about updates to regulations and standards is essential. Custom solutions should be designed with the flexibility to adapt to future regulatory changes.
Ensuring Future Scalability and Flexibility
Custom cranes should be designed with future scalability and flexibility in mind to accommodate changing operational needs:
- Modular Design: Incorporating a modular design allows for easy upgrades and modifications in the future. This ensures that the crane can adapt to new requirements without the need for a complete overhaul.
- Capacity for Expansion: Designing cranes with the potential for increased lifting capacity or extended spans can accommodate future growth and changes in production demands.
- Integration with New Technologies: Custom cranes should be compatible with emerging technologies and industry trends, such as automation and smart systems, to remain relevant and efficient over time.
Maintenance and Support for Custom Features
Proper maintenance and support are crucial for the longevity and optimal performance of custom cranes:
- Customized Maintenance Plans: Developing a maintenance plan tailored to the specific features and components of the custom crane ensures that it remains in peak condition. This includes regular inspections, preventive maintenance, and timely repairs.
- Manufacturer Support: Choosing a manufacturer that offers comprehensive support services, including technical assistance and spare parts availability, is vital. This support ensures quick resolution of any issues and minimizes downtime.
- Training for Maintenance Personnel: Providing specialized training for maintenance personnel on the unique aspects of the custom crane ensures they are equipped to handle routine maintenance and address any problems that arise.
- Documentation and Manuals: Comprehensive documentation and user manuals for the custom features of the crane are essential. These resources help operators and maintenance teams understand and manage the crane effectively.
In conclusion, customizing under running bridge cranes requires careful consideration of various factors to ensure successful implementation and long-term benefits. Addressing budget and cost implications, compliance with standards and regulations, future scalability and flexibility, and robust maintenance and support plans are essential steps in the customization process. By focusing on these considerations, businesses can achieve a tailored solution that enhances operational efficiency, safety, and productivity.
Conclusion
Customization of under running bridge cranes is crucial for meeting the diverse and specific needs of various industries. Standard cranes often fall short in addressing unique operational challenges, making tailored solutions essential for optimizing performance, safety, and efficiency. Custom cranes are designed to fit specific environments, handle unique loads, and integrate seamlessly with existing systems, ensuring they meet the exact requirements of different industrial applications.
Summary of Key Points Discussed
Throughout this article, we have explored several critical aspects of customizing under running bridge cranes:
- Understanding Under Running Bridge Cranes: We examined the basic design and functionality of these cranes, highlighting their common applications and inherent benefits.
- The Need for Customization: We discussed how diverse operational requirements and the limitations of standard cranes drive the need for tailored solutions.
- Customization Options: Detailed various customization options, including design features, lifting capacities, and enhanced functionalities to address specific industry needs.
- Case Studies: Provided real-world examples from the manufacturing, mining, and construction industries, showcasing the impact of custom crane solutions on operational efficiency and productivity.
- Implementing Custom Solutions: Outlined the steps in the customization process, emphasizing the importance of collaboration, detailed needs assessment, and meticulous planning.
- Considerations for Customization: Highlighted key considerations such as budget and cost implications, compliance with industry standards, future scalability, and maintenance and support for custom features.
Final Thoughts on the Benefits and Future of Custom Crane Solutions
Customized under running bridge cranes offer significant advantages over standard models, including:
- Enhanced Efficiency: Tailored solutions improve workflow and reduce downtime, leading to increased productivity.
- Improved Safety: Custom features such as explosion-proof designs and specialized lifting attachments ensure safe operation in challenging environments.
- Operational Flexibility: Custom cranes are designed to adapt to specific operational needs, providing flexibility to accommodate future changes and growth.
The future of custom crane solutions looks promising as industries continue to evolve and face new challenges. Advances in technology, such as automation and smart systems, will further enhance the capabilities and efficiency of custom cranes. As businesses increasingly recognize the value of tailored solutions, the demand for custom-designed under running bridge cranes is likely to grow, driving innovation and continuous improvement in this field.
In conclusion, the customization of under running bridge cranes is a strategic investment that delivers long-term benefits by addressing unique industrial needs, improving operational efficiency, and ensuring safety. By partnering with experienced manufacturers and focusing on detailed planning and implementation, businesses can achieve optimal solutions that support their specific goals and operational requirements.