Intelligent Features of New Advanced Electric Wire Rope Hoists
Electric Intelligent hoist and smart hoist for sale, advanced wire rope hoists, 1 to 20 ton for single girder crane, 3 to 80 ton for double girder crane.
Evolution of Intelligence in Electric Wire Rope Hoists
Introduction to Electric Wire Rope Hoists:
Electric wire rope hoists serve as indispensable components in material handling and lifting operations across various industries. These devices are designed to lift and move heavy loads efficiently, offering a practical solution for tasks that demand precision, safety, and reliability.
Definition and Purpose:
Electric wire rope hoists consist of a motor driven mechanism that utilizes a wire rope for lifting and lowering loads. They play a pivotal role in vertical and horizontal material movement within industrial settings. These hoists are employed in diverse applications, ranging from manufacturing and construction to warehousing and logistics.
Key Components and Functionality:
Electric wire rope hoists typically include essential components such as a motor, gearbox, drum, wire rope, and a lifting hook or attachment. The motor powers the mechanism, while the gearbox provides the necessary torque. The drum, equipped with the wire rope, facilitates the lifting and lowering of loads. The lifting hook or attachment ensures secure load handling.
Evolution of Hoist Technology:
Historical Overview:
The history of hoists traces back to ancient civilizations where manual hoisting systems were employed for lifting heavy objects. The industrial revolution marked a significant turning point, with the introduction of steam powered hoists, revolutionizing material handling in factories and construction sites.
Transition to Modern Electric Wire Rope Hoists:
Advancements in technology led to the development of electric wire rope hoists, marking a substantial leap forward in efficiency and precision. The transition from manual and steam powered systems to electric hoists brought about a paradigm shift in material handling practices.
Modern electric wire rope hoists leverage electric motors for enhanced control and efficiency. The integration of intelligent features has further elevated their capabilities, making them versatile tools in today's dynamic industrial landscape.
Smart electric hoist for single girder cranes, 1 ton to 20 ton
Need for Intelligent Features:
Electric wire rope hoists have evolved beyond their conventional counterparts, embracing a new era of intelligence to meet the growing demands of modern industrial operations. The incorporation of intelligent features has become a necessity, driven by the need to address challenges inherent in traditional hoist operations and fulfill the escalating requirements for efficiency and safety.
Challenges in Traditional Hoist Operations:
Traditional hoist operations, characterized by manual or basic mechanized systems, often encountered limitations that hindered optimal performance. Challenges included imprecise load positioning, potential overloading, and limited adaptability to varying operational conditions. These constraints not only affected operational efficiency but also posed safety concerns for both equipment and personnel.
Demands for Efficiency and Safety:
The contemporary industrial landscape demands heightened efficiency and safety in material handling processes. As industries strive for increased productivity, the need for hoists to perform with precision, speed, and adaptability has become paramount. Moreover, the emphasis on creating safer work environments necessitates advancements that mitigate the risk of accidents, collisions, and equipment damage.
Intelligent features in electric wire rope hoists emerge as a solution to bridge the gap between traditional operations and the evolving demands of modern industry. In the upcoming sections, we will explore a spectrum of intelligent features integrated into these hoists, examining how each addresses specific challenges and contributes to elevating both efficiency and safety in material handling.
Intelligent features of double girder smart hoist with capacity from 3 ton to 80 ton
Overview of Intelligent Features:
In the realm of material handling, the infusion of intelligence into electric wire rope hoists has revolutionized the way heavy loads are lifted and moved. This section provides a holistic overview of the intelligent features that define the modern era of hoist technology.
Definition of Intelligence in Hoists:
Intelligence in the context of electric wire rope hoists refers to the incorporation of advanced technologies that enable these machines to operate with enhanced precision, adaptability, and safety. These intelligent features go beyond traditional mechanisms, introducing a level of automation and control that optimizes performance in diverse industrial settings.
Integration of Advanced Technologies:
The intelligence in electric wire rope hoists is rooted in the integration of cutting edge technologies. These technologies work cohesively to address specific challenges and elevate the overall capabilities of the hoist. Some of the key advanced technologies integrated into modern hoists include:
- Extended Speed Range: Variable speed control for optimal performance. Catering to diverse operational requirements.
- Micro Speed: Precision in load handling through extremely controlled speeds.Ideal for delicate or sensitive loads requiring careful positioning.
- Slack Rope Prevention: Ensuring no slack or loose rope during operations. Preventing accidents or load instability caused by slack in the lifting mechanism.
- Inching: Control mechanism for making small, incremental movements. Fine tuning crane position with utmost precision.
- Restricted Load: Imposing limitations on maximum load capacity. Preventing overloading for safety and equipment longevity.
- Sway Control: Technology to minimize swinging or swaying of the load. Enhancing safety and precision, especially for heavy or sensitive loads.
- Load Floating: Maintaining a consistent load height regardless of variations in load weight. Critical for applications where maintaining constant height is crucial.
- Shock Load Prevention: Safety feature protecting the crane and load from sudden jolts or impacts. Absorbing and mitigating shocks for reduced risk of damage.
- Tandem Synchronization: Coordinated operation of multiple cranes for lifting larger loads. Ensuring synchronized movement and optimal lift capacity.
- Cranes in Tandem: Simultaneous operation of multiple cranes for heavy or oversized loads. Enhanced safety and load handling through synchronized movements.
- Synchronization: Continuously monitored synchronization, even with asymmetrical loads. Reducing accidents and enhancing operational benefits.
These intelligent features collectively contribute to elevating the performance, safety, and efficiency of electric wire rope hoists. In the subsequent sections, we will delve deeper into each feature, exploring their functionalities and the advantages they bring to material handling operations.
Unveiling the Intelligence: Exploring Key Features of Electric Wire Rope Hoists
Electric wire rope hoists have undergone a transformative evolution, becoming pioneers of intelligent features that redefine material handling capabilities. Let's delve into the key intelligent features that set modern hoists apart, each designed to address specific challenges and elevate operational efficiency and safety.
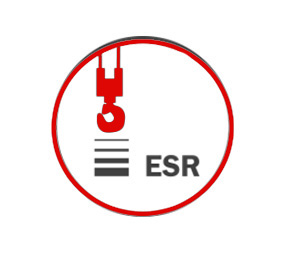
Extended Speed Range:
Explanation of Variable Speed Control:
The Extended Speed Range feature empowers hoists to operate within a versatile speed spectrum. Variable speed control allows for precise adjustments in the speed of crane movements, catering to diverse operational requirements. This feature ensures maximum performance at all times, offering flexibility in adapting to varying load conditions and tasks.
Benefits for Different Operational Requirements:
Higher productivity with optimized speed adjustments.
Time savings through faster hoisting speed, particularly advantageous when lifting smaller loads.
Enhanced adaptability to dynamic work environments, making the hoist a versatile tool in various industrial settings.
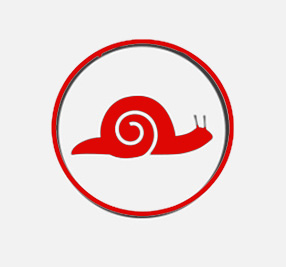
Micro Speed:
Precision in Load Handling:
Micro Speed is a testament to the hoist's ability to move at extremely slow and controlled speeds. This feature ensures precision in load handling, crucial for tasks that demand meticulous positioning. The hoist's capability to operate at micro speeds facilitates delicate handling of sensitive loads with unparalleled accuracy.
Applications for Delicate or Sensitive Loads:
Ideal for handling fragile or sensitive materials requiring careful positioning.
Ensures gentle and controlled movements, preventing any unintended impact on delicate loads.
Precision becomes paramount in applications such as precision manufacturing or laboratory environments.
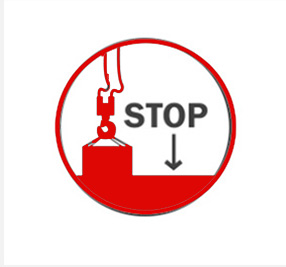
Slack Rope Prevention:
Importance in Safety:
Slack Rope Prevention is a safety feature that eliminates the presence of slack or loose rope during hoist operations. This feature is instrumental in preventing accidents and load instability caused by slack in the lifting mechanism. It ensures that the rope remains taut, contributing to a safer working environment.
Constant Tension Monitoring and Emergency Stop Functionality:
Continuous monitoring of rope tension to prevent slack.
Immediate activation of emergency stop functionality when slack is detected.
Safeguards against potential hazards, protecting both equipment and personnel.
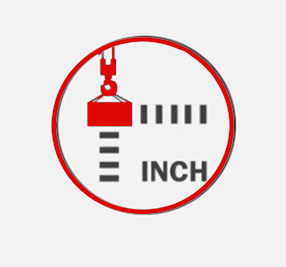
Inching:
Control Mechanism for Small Movements:
Inching is a control mechanism that empowers crane operators to make minute, incremental movements. This feature is particularly beneficial for fine tuning the crane's position with utmost precision. It allows operators to navigate tight spaces or align loads with unparalleled accuracy.
Benefits in Fine Tuning Crane Position:
Facilitates meticulous positioning of the crane.
Enables operators to navigate through intricate spaces with ease.
Ideal for applications requiring precision in load placement, ensuring optimal alignment.
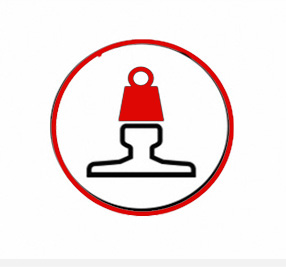
Restricted Load:
Protection Against Overloading:
The Restricted Load feature imposes limitations on the maximum load capacity the crane can handle. This preventative measure protects against overloading, ensuring that the crane operates within its specified limits. It contributes to safety and enhances the longevity of equipment components.
Contribution to Safety and Equipment Longevity:
Prevents overloading, reducing the risk of equipment strain or failure.
Ensures safe operations by adhering to specified load capacity limits.
Extends the service life of the crane and its components.
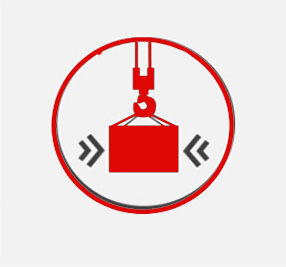
Sway Control:
Technology for Load Stability:
Sway Control is a technological advancement designed to minimize the swinging or swaying of the load during lifting or movement. This feature enhances safety and precision, especially when dealing with heavy or sensitive loads that are susceptible to unintended movements.
Applications in Heavy Load Handling:
Enhances stability during lifting and movement of heavy loads.
Minimizes the risk of load sway, ensuring controlled and secure operations.
Critical for applications where load stability is paramount, such as construction or heavy manufacturing.
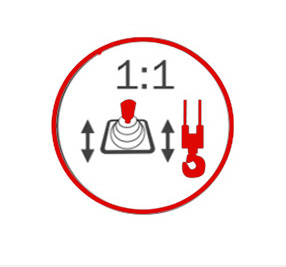
Load Floating:
Maintenance of Consistent Load Height:
Load Floating allows the crane to maintain a consistent load height regardless of variations in load weight. This feature is particularly useful in applications where maintaining a constant height is critical for the success of the operation.
Applications in Critical Load Operations:
Ensures a consistent load height, critical for precision applications.
Particularly useful when handling loads with varying weights consecutively.
Enhances overall operational efficiency and load stability.
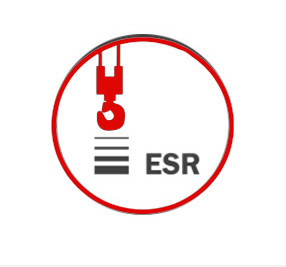
Shock Load Prevention:
Safety Feature Against Sudden Impacts:
Shock Load Prevention is a safety feature that protects the crane and the load from sudden jolts or impacts during lifting or movement. This feature absorbs and mitigates shocks, reducing the risk of equipment damage, structural strain, or load instability.
Measures for Equipment and Load Protection:
Real time monitoring detects sudden changes in load conditions.
Automatic adjustments to the lifting mechanism to absorb and reduce impact forces.
Protects against structural damage and ensures stable load handling.
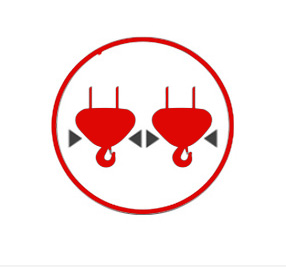
Tandem Synchronization:
Coordinated Operation of Multiple Cranes:
Tandem Synchronization facilitates the coordinated operation of multiple cranes working together. This technology ensures that two or more cranes move in sync, allowing for the lifting and movement of larger and more complex loads that may exceed the capacity of a single crane.
Lift Capacity Optimization and Efficiency:
Coordinated movement for stability and balance when lifting oversized loads.
Centralized control system for simultaneous operation of multiple synchronized cranes.
Load sharing mechanisms for even distribution of weight among synchronized cranes.
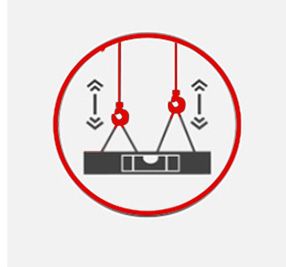
Cranes in Tandem:
Simultaneous Operation for Heavy Loads:
Cranes in Tandem specifically address the simultaneous operation of multiple cranes to lift and transport heavy or oversized loads. This feature allows multiple cranes to work together, often synchronized, to achieve a common lifting goal.
Enhanced Safety and Load Handling:
Simultaneous long travel and hoisting movements for heavy loads.
Synchronized lifting and lowering for optimal load control.
Improved safety through coordinated operations, reducing the risk of accidents.
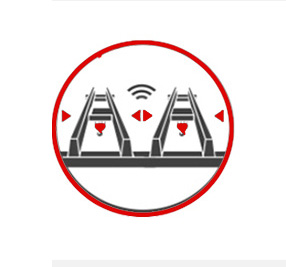
Synchronization:
Continuous Monitoring for Asymmetrical Loads:
Synchronization involves the continuous monitoring of crane movements, even with asymmetrical loads. This feature reduces the risk of accidents and enhances operational benefits by ensuring that the cranes operate in harmony, responding to load conditions in real time.
Accidents Reduction and Operational Benefits:
Real time adjustments to crane movements for load balance.
Reduction in the risk of accidents caused by asymmetrical loading.
Enhanced efficiency and safety through synchronized crane operations.
Conclusion:
The integration of intelligent features has propelled electric wire rope hoists into a realm of enhanced performance, safety, and adaptability. As we conclude this exploration of the intelligent features that define modern hoist technology, let's summarize the profound impact these advancements have on hoist performance and safety.
In conclusion, the infusion of intelligence into electric wire rope hoists represents a paradigm shift in material handling practices. These features collectively redefine the possibilities in the modern industrial landscape, offering not just improved performance but a safer and more adaptable solution for the challenges of heavy load handling. As industries continue to evolve, the intelligent features in electric wire rope hoists stand as a testament to innovation that prioritizes efficiency, precision, and, above all, the safety of personnel and equipment.