Maximize Your Overhead Workshop Cranes Lifespan
What are the general lifting span of your workshop overhead cranes ? How to maximize your crane's durability ? Custom workshop cranes available. Check now.
Maximize Your Overhead Workshop Cranes Lifespan
The workshop activities is often orchestrated by the precision and strength of overhead and gantry cranes. These industrial workhorses have evolved over time, adapting to the dynamic needs of workshop environments. From the early days of manual operation to the integration of cutting-edge technology, the journey of industrial cranes mirrors the progress of manufacturing and assembly processes.
In the heart of every workshop, the durability of cranes becomes a critical factor that influences both productivity and safety. Unlike one-size-fits-all approaches, workshops demand tailored strategies to ensure cranes withstand the unique challenges posed by diverse tasks, load specifications, and operational conditions. Recognizing this necessity is fundamental to fostering longevity and efficiency in crane operations.
Working Duty Classes in Workshops
Workshops are dynamic spaces with varying demands, ranging from light-duty tasks to heavy-duty operations. This section explores the significance of aligning working duty classes with the specific requirements of workshops, ensuring that the chosen crane is robust enough to handle the workload without being overengineered.
Delving deeper, we examine each working duty class (A1~A3, A4~A5, A6~A7, A8) and their adaptability to workshop operational conditions. Understanding how these classes correlate with the intensity of use and load capacities is pivotal for making informed decisions when selecting cranes for workshop applications.
Workshops are diverse environments, and no two are exactly alike. From assembly lines to maintenance bays, the conditions vary significantly. This section highlights the need for adaptations in crane selection and design to accommodate the unique challenges posed by different workshop settings.
Design Life Considerations for Types of Workshop Cranes
Manual Operated Industrial Workshop Cranes
- Overview of Manual Workshop Cranes:Manual operated industrial workshop cranes are designed for precision and controlled lifting in smaller workshop environments. These cranes are characterized by their manual operation, providing a hands-on approach for specific lifting tasks.
- Total Working Cycle: 3.2×10^4 to 6.3×10^4 cycles
- Usage Frequency: Rarely used, typically reserved for sporadic manual handling tasks where precision is crucial.
- Industrial Applications: Well-suited for workshops with occasional lightweight lifting requirements. Commonly used for precise lifting of materials or products.
- Usage Scenario: Brought into operation only when manual control and precision are essential for specific tasks.
- Design Life: 30 years
Overhead Cranes for Workshop Assembly:
- Overview of Workshop Assembly Cranes:Cranes specifically designed for workshop assembly play a crucial role in manufacturing and assembly processes. They facilitate the lifting and positioning of components during the assembly of machinery or products.
- Total Working Cycle: 6.3×10^4 to 1.25×10^5 cycles
- Usage Frequency: Less frequently used, deployed during assembly phases where precision and controlled lifting are essential.
- Industrial Applications: Ideal for workshops involved in manufacturing and assembly tasks, lifting and placing components during the assembly process.
- Usage Scenario: Brought into operation during assembly phases, providing reliable and controlled lifting for manufacturing tasks.
- Design Life: 25 years
This format can be applied to the remaining types of industrial workshop cranes as well, providing a structured and consistent presentation of information for each crane type.
Industrial Workshop Cranes for Power Stations
- Overview of Power Station Workshop Cranes:Cranes designed for power stations play a crucial role in the maintenance and installation of heavy equipment within power generation facilities. These cranes are engineered to handle the specific demands of lifting heavy machinery and components in power station environments.
- Total Working Cycle: 3.2×10^4 to 6.3×10^4 cycles
- Usage Frequency: Rarely used, typically brought into action for specific maintenance tasks and installations within power stations.
- Industrial Applications: Well-suited for lifting heavy machinery and components during maintenance and installation activities within power generation facilities.
- Usage Scenario: Deployed for specific tasks such as equipment maintenance and installations, ensuring precise and controlled lifting in power station environments.
- Design Life: 30 years
Industrial Workshop Cranes for Maintenance
Overview of Maintenance Workshop Cranes:Cranes tailored for maintenance tasks are essential in various industrial settings where lifting and replacing components during maintenance operations are common requirements. These cranes are designed to provide reliable and controlled lifting for maintenance activities.
- Total Working Cycle: 3.2×10^4 to 6.3×10^4 cycles
- Usage Frequency: Less frequently used, brought into operation when maintenance activities are required within industrial facilities.
- Industrial Applications: Specifically designed for lifting and replacing components during maintenance operations, ensuring precise and controlled handling.
- Usage Scenario: Deployed for tasks such as equipment maintenance, providing the necessary lifting capabilities for efficient and safe maintenance procedures.
- Design Life: 25 years
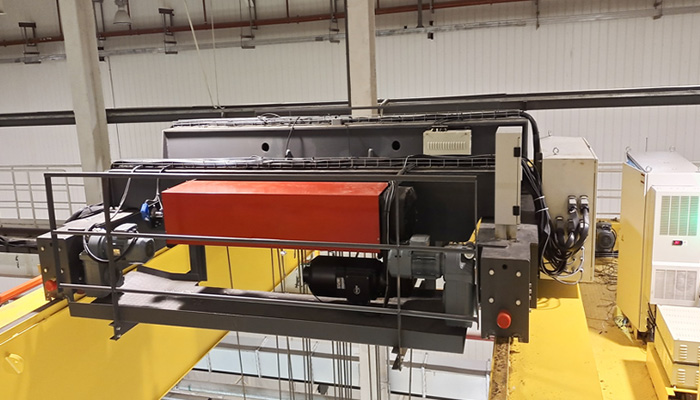
Electric Hoist Cranes Workshop Cranes
Overview of Electric Hoist Workshop Cranes:Electric hoist workshop cranes are versatile solutions suitable for a wide range of workshop applications. They are equipped with electric hoists for efficient material handling within the workshop environment.
- Total Working Cycle: 6.3×10^4 to 1.25×10^5 cycles
- Usage Frequency: Less frequently used, deployed for general material handling tasks within workshops.
- Industrial Applications: Versatile and well-suited for various workshop applications, providing efficient and controlled material handling.
- Usage Scenario: Brought into operation for general material handling tasks, offering reliable and electrically powered lifting capabilities.
- Design Life: 25 years
Workshop Cranes (Including Electric Hoist Cranes) - Infrequent Light-Duty Use:
- Overview of Infrequent Light-Duty Workshop Cranes:This category of workshop cranes, including electric hoist cranes, is designed for occasional light-duty tasks where precision and controlled lifting are necessary. They are suitable for workshops with intermittent lifting needs.
- Total Working Cycle: 1.25×10^5 to 2.5×10^5 cycles
- Usage Frequency: Infrequent light-duty use, deployed for specific tasks with lighter loads within workshops.
- Industrial Applications: Designed for workshops with occasional light-duty lifting requirements, providing controlled and precise lifting.
- Usage Scenario: Brought into operation for specific tasks that demand precision with lighter loads, ensuring reliable and efficient material handling.
- Design Life: 25 years
Workshop Cranes (Including Electric Hoist Cranes) - Infrequent Medium-Duty Use:
- Overview of Infrequent Medium-Duty Workshop Cranes:This category encompasses workshop cranes, including electric hoist cranes, designed for occasional medium-duty tasks. They are suitable for workshops with intermittent lifting needs involving moderately heavy loads.
- Total Working Cycle: 2.5×10^5 to 5×10^5 cycles
- Usage Frequency: Infrequent medium-duty use, deployed for specific tasks with moderately heavy loads within workshops.
- Industrial Applications: Tailored for workshops with occasional medium-duty lifting requirements, offering controlled and precise lifting for moderately heavy loads.
- Usage Scenario: Brought into operation for specific tasks demanding precision with moderately heavy loads, ensuring reliable and efficient material handling.
- Design Life: 25 years
Hook Cranes for Freight Yard (Including Electric Hoist Cranes for Freight Yard):
- Overview of Hook Cranes for Freight Yard:This category of cranes, including electric hoist cranes, is specialized for material handling in freight yards. They are designed to efficiently lift and transport heavy loads in the dynamic environment of a freight yard.
- Total Working Cycle: 1.25×10^5 to 2.5×10^5 cycles
- Usage Frequency: Less frequently used, deployed for specific tasks involving the lifting and transport of heavy loads in freight yards.
- Industrial Applications: Tailored for freight yards, offering efficient material handling capabilities for heavier loads.
- Usage Scenario: Brought into operation for specific tasks within freight yards, ensuring reliable and controlled lifting for heavy loads.
- Design Life: 25 years
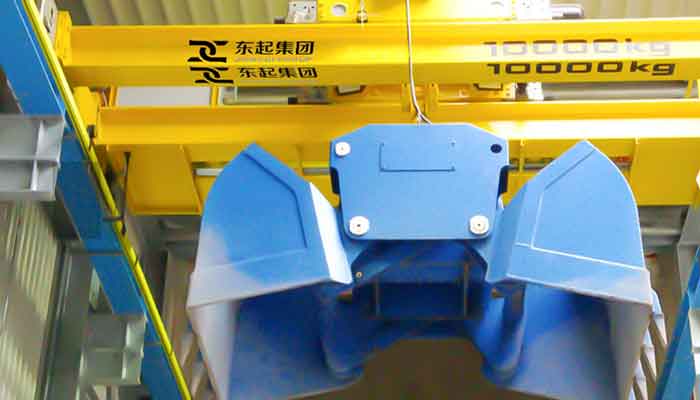
grab bucket workshop overhead cranes
Cargo Yard Grab Cranes or Electromagnetic Cranes:
- Overview of Cargo Yard Grab Cranes or Electromagnetic Cranes:This category of cranes is specifically designed for handling materials in cargo yards, utilizing grab mechanisms or electromagnetic systems for efficient and controlled material handling.
- Total Working Cycle: 2.5×10^5 to 5×10^5 cycles
- Usage Frequency: More frequent medium-duty use, deployed for regular material handling tasks in cargo yards.
- Industrial Applications: Suited for cargo yards where frequent medium-duty material handling is required, employing grab mechanisms or electromagnetic systems.
- Usage Scenario: Brought into operation regularly for material handling tasks in cargo yards, ensuring efficient and controlled lifting.
- Design Life: 20 years
Hook Crane for Waste Plant:
- Overview of Hook Crane for Waste Plant:Hook cranes designed for waste plants are crucial for the efficient handling and disposal of waste materials. These cranes are tailored to operate in waste plant environments, offering controlled lifting for waste management tasks.
- Total Working Cycle: 1.25×10^5 to 2.5×10^5 cycles
- Usage Frequency: Less frequently used, brought into operation for specific waste handling tasks in waste plants.
- Industrial Applications: Essential for waste management in waste plants, providing reliable and controlled lifting for waste disposal.
- Usage Scenario: Deployed for waste handling tasks, ensuring efficient and controlled lifting for waste management operations.
- Design Life: 25 years
Waste Plant Grab Crane or Electromagnetic Crane:
- Overview of Waste Plant Grab Crane or Electromagnetic Crane:This category of cranes, equipped with grab mechanisms or electromagnetic systems, is designed for more intricate waste handling tasks in waste plants, ensuring efficient and controlled material handling.
- Total Working Cycle: 2.5×10^5 to 5×10^5 cycles
- Usage Frequency: More frequent medium-duty use, employed for regular waste handling operations in waste plants.
- Industrial Applications: Suited for waste plants where frequent medium-duty material handling is required, utilizing grab mechanisms or electromagnetic systems.
- Usage Scenario: Regularly brought into operation for material handling tasks in waste plants, ensuring efficient and controlled lifting for waste management.
- Design Life: 20 years
These descriptions maintain a consistent format, offering detailed information about the specifications and applications of cranes in waste plant environments.
Container Handling Crane:
- Overview of Container Handling Crane:Container handling cranes play a vital role in efficiently managing and transporting containers within shipping yards and industrial facilities. These cranes are designed for more frequent medium-duty use, providing controlled and reliable lifting for container handling operations.
- Total Working Cycle: 2.5×10^5 to 5×10^5 cycles
- Usage Frequency: More frequent medium-duty use, employed for regular container handling tasks in shipping yards and industrial settings.
- Industrial Applications: Suited for locations where frequent medium-duty container handling is required, offering efficient and controlled lifting capabilities.
- Usage Scenario: Regularly brought into operation for container handling tasks, ensuring efficient and controlled lifting for shipping and storage operations.
- Design Life: 20 years
Shore Container Crane:
- Overview of Shore Container Crane:Shore container cranes are designed for heavy-duty container handling operations in maritime environments. These cranes are engineered to withstand the demands of more frequent heavy-duty use in loading and unloading containers from ships.
- Total Working Cycle: 5×10^5 to 1×10^6 cycles
- Usage Frequency: More frequent heavy-duty use, deployed for intense container handling operations in maritime settings.
- Industrial Applications: Specifically tailored for maritime environments, providing robust and controlled lifting for heavy-duty container handling.
- Usage Scenario: Regularly brought into operation for heavy-duty container handling tasks at shorelines, ensuring efficient and controlled lifting for maritime logistics.
- Design Life: 20 years
These descriptions follow a consistent format, offering detailed information about the specifications and applications of container handling cranes in different industrial settings.
Metallurgic Industrial Crane - Rolling Mill Roll Crane:
Overview of Rolling Mill Roll Crane:Rolling mill roll cranes are specialized industrial cranes used in metallurgical facilities for handling heavy rolls used in the rolling process. These cranes are designed for rare but essential use in metallurgical environments.
- Total Working Cycle: 6.3×10^4 to 1.25×10^5 cycles
- Usage Frequency: Rarely used, brought into operation for specific tasks related to the handling of rolling mill rolls.
- Industrial Applications: Crucial for metallurgical facilities, providing controlled lifting for heavy rolling mill rolls during production.
- Usage Scenario: Deployed for specific tasks involving the handling of rolling mill rolls, ensuring precise and controlled lifting.
- Design Life: 30 years
Metallurgic Workshop Crane - Scrap Charging Cranes:
- Overview of Scrap Charging Cranes:Scrap charging cranes are heavy-duty industrial cranes employed in metallurgical workshops for handling and charging scrap materials into furnaces. These cranes endure frequent heavy-duty use in demanding metallurgical processes.
- Total Working Cycle: 1×10^6 to 2×10^6 cycles
- Usage Frequency: Frequent heavy-duty use, employed regularly for the demanding task of charging scrap into metallurgical furnaces.
- Industrial Applications: Essential for metallurgical workshops, providing robust and controlled lifting for frequent heavy-duty scrap charging operations.
- Usage Scenario: Regularly brought into operation for charging scrap materials into furnaces, ensuring efficient and controlled lifting.
- Design Life: Generally 10~15 years, less than 20 years
These descriptions maintain a consistent format, offering detailed information about the specifications and applications of metallurgic cranes in different industrial settings.
Metallurgic Steel Mill Crane - Heating Furnace Crane:
- Overview of Heating Furnace Crane:Heating furnace cranes are crucial in steel mills, specifically designed for handling materials in the high-temperature environment of heating furnaces. These cranes endure frequent heavy-duty use in demanding metallurgical processes.
- Total Working Cycle: 1×10^6 to 2×10^6 cycles
- Usage Frequency: Frequent heavy-duty use, employed regularly for handling materials in the intense heat of steel mill heating furnaces.
- Industrial Applications: Essential for steel mills, providing robust and controlled lifting for frequent heavy-duty operations in heating furnaces.
- Usage Scenario: Regularly brought into operation for handling materials in the high-temperature environment of heating furnaces, ensuring efficient and controlled lifting.
- Design Life: Generally 10~15 years, less than 20 years
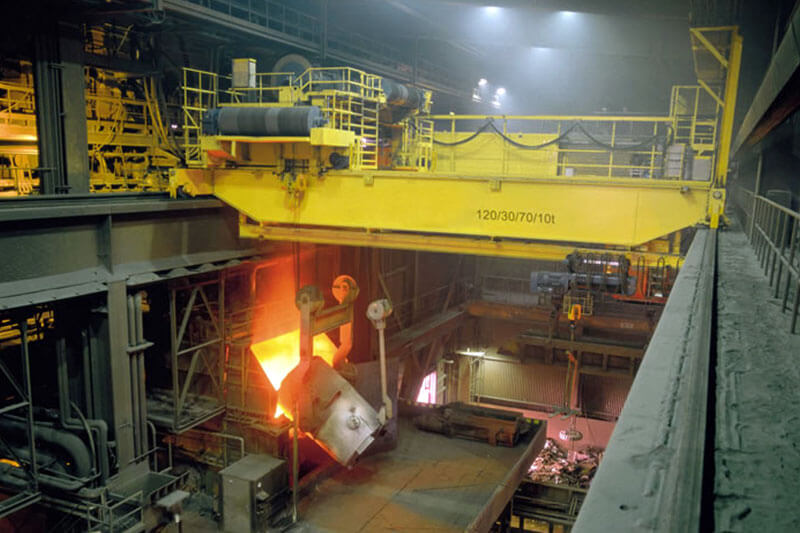
steel mill workshop ladle cranes
Metallurgic Furnace Crane - Front of Furnace Molten Iron Casting Hoisting Crane:
- Overview of Front of Furnace Molten Iron Casting Hoisting Crane:These cranes are specialized for the intricate task of hoisting and casting molten iron at the front of metallurgical furnaces. They are designed for more frequent heavy-duty use, ensuring precise and controlled handling of molten materials.
- Total Working Cycle: 5×10^5 to 2×10^6 cycles
- Usage Frequency: More frequent heavy-duty use, employed regularly for the delicate task of hoisting and casting molten iron at the front of metallurgical furnaces.
- Industrial Applications: Tailored for metallurgical processes, providing controlled and precise lifting for handling molten iron.
- Usage Scenario: Regularly brought into operation for the intricate task of hoisting and casting molten iron, ensuring efficient and controlled material handling.
- Design Life: 20 years
These descriptions maintain a consistent format, offering detailed information about the specifications and applications of metallurgic cranes in different industrial settings.
Metallurgic Ladle Crane - Back of Furnace Steel Pouring Casting Hoisting Crane:
- Overview of Back of Furnace Steel Pouring Casting Hoisting Crane:Ladle cranes designed for the back of metallurgical furnaces are specialized for the critical task of pouring and casting molten steel. These cranes endure more frequent heavy-duty use, providing precise and controlled lifting for steel casting operations.
- Total Working Cycle: 1.25×10^5 to 5×10^5 cycles
- Usage Frequency: More frequent heavy-duty use, employed regularly for the critical task of pouring and casting molten steel at the back of metallurgical furnaces.
- Industrial Applications: Crucial for metallurgical processes, providing controlled and precise lifting for frequent heavy-duty steel pouring and casting operations.
- Usage Scenario: Regularly brought into operation for the intricate task of pouring and casting molten steel, ensuring efficient and controlled material handling.
- Design Life: 20 years
Metallurgic Slab Crane - Slab Handling Crane:
- Overview of Slab Handling Crane:Slab handling cranes play a crucial role in metallurgical facilities, specifically designed for the handling of heavy slabs. These cranes endure more frequent heavy-duty use, providing efficient and controlled lifting for slab handling operations.
- Total Working Cycle: 5×10^5 to 1×10^6 cycles
- Usage Frequency: More frequent heavy-duty use, employed regularly for the handling of heavy slabs in metallurgical facilities.
- Industrial Applications: Essential for metallurgical processes, providing robust and controlled lifting for frequent heavy-duty slab handling operations.
- Usage Scenario: Regularly brought into operation for the handling of heavy slabs, ensuring efficient and controlled material handling.
- Design Life: 20 years
These descriptions maintain a consistent format, offering detailed information about the specifications and applications of metallurgic cranes in different industrial settings.
Metallurgic Heavy Duty Crane - Special Hoisting Crane on the Metallurgical Process Line:
- Overview of Special Hoisting Crane on the Metallurgical Process Line:This heavy-duty crane is designed for specialized lifting tasks within the metallurgical process line, enduring frequent heavy-duty use. It provides robust and controlled lifting for demanding metallurgical operations.
- Total Working Cycle: 1×10^6 to 2×10^6 cycles
- Usage Frequency: Frequent heavy-duty use, employed for specialized lifting tasks within the metallurgical process line.
- Industrial Applications: Crucial for metallurgical processes, providing specialized and controlled lifting for frequent heavy-duty operations within the process line.
- Usage Scenario: Regularly brought into operation for specialized lifting tasks, ensuring efficient and controlled material handling within the metallurgical process.
- Design Life: Generally 10~15 years, less than 20 years
Metallurgic Crane - Hoisting Crane for External Use in the Metallurgical Process Line:
- Overview of Hoisting Crane for External Use in the Metallurgical Process Line:This crane is tailored for external lifting tasks within the metallurgical process line, enduring more frequent medium-duty use. It offers controlled and efficient lifting for external operations in metallurgical facilities.
- Total Working Cycle: 5×10^5 to 1×10^6 cycles
- Usage Frequency: More frequent medium-duty use, employed for external lifting tasks within the metallurgical process line.
- Industrial Applications: Essential for metallurgical processes, providing controlled and efficient lifting for frequent medium-duty external operations.
- Usage Scenario: Regularly brought into operation for external lifting tasks, ensuring efficient and controlled material handling within the metallurgical process line.
- Design Life: 20 years
These descriptions maintain a consistent format, offering detailed information about the specifications and applications of metallurgic cranes in different industrial settings.
Hoisting Crane for Foundry Workshop:
- Overview of Hoisting Crane for Foundry Workshop:This crane is specifically designed for lifting tasks within foundry workshops, with a focus on enduring infrequent medium-duty use. It provides efficient and controlled lifting for various applications in foundry operations.
- Total Working Cycle: 1.25×10^5 to 2.5×10^5 cycles
- Usage Frequency: Infrequent medium-duty use, employed for lifting tasks within foundry workshops.
- Industrial Applications: Essential for foundry operations, providing controlled and efficient lifting for various medium-duty applications.
- Usage Scenario: Brought into operation for lifting tasks within foundry workshops, ensuring efficient and controlled material handling.
- Design Life: 25 years
Forging Crane:
- Overview of Forging Crane:Forging cranes are crucial in industrial settings, designed for the frequent heavy-duty lifting requirements of forging operations. These cranes provide robust and controlled lifting for the demanding tasks associated with the forging process.
- Total Working Cycle: 5×10^5 to 1×10^6 cycles
- Usage Frequency: More frequent heavy-duty use, employed for lifting heavy loads in forging operations.
- Industrial Applications: Crucial for forging processes, providing controlled and efficient lifting for various heavy-duty applications.
- Usage Scenario: Regularly brought into operation for heavy-duty lifting tasks in forging operations, ensuring efficient and controlled material handling.
- Design Life: 20 years
Quenching Crane:
- Overview of Quenching Crane:Quenching cranes are tailored for lifting tasks in quenching processes, enduring more frequent medium-duty use. They provide efficient and controlled lifting for materials undergoing quenching operations.
- Total Working Cycle: 2.5×10^5 to 5×10^5 cycles
- Usage Frequency: More frequent medium-duty use, employed for lifting tasks in quenching processes.
- Industrial Applications: Essential for quenching operations, providing controlled and efficient lifting for various medium-duty applications.
- Usage Scenario: Regularly brought into operation for lifting tasks in quenching processes, ensuring efficient and controlled material handling.
- Design Life: 20 years
These descriptions maintain a consistent format, offering detailed information about the specifications and applications of various industrial cranes in different workshop environments.
Factors Tailored to Workshop Crane Durability
Material Quality for Workshop-Specific Applications
Importance of Specialized Steel Requirements:
- Workshop cranes face unique stressors, necessitating the use of high-quality steel with specific characteristics.
- Understanding the critical role of materials in ensuring the longevity of workshop cranes.
Bearings and Electrical Components Customization:
- Customizing bearings and electrical components to withstand the varying demands of workshop operations.
- Tailoring these components to resist wear and tear associated with workshop environments.
Design and Engineering for Workshop Challenges
Considerations for Load Capacity Alignment with Workshop Tasks:
- Delving into the meticulous process of aligning crane load capacities with the specific tasks performed in workshops.
- Balancing the need for strength with the efficiency required for various workshop operations.
Structural Integrity and Fatigue Resistance:
- Exploring the significance of structural integrity in the face of continuous usage.
- Strategies for enhancing fatigue resistance, considering the cyclical nature of workshop crane operations.
Maintenance Practices Customized for Workshops
Importance of Workshop Lubrication Best Practices:
- Recognizing the specific lubrication needs of workshop cranes to ensure smooth operation and prevent premature wear.
- Implementing a tailored lubrication schedule that aligns with workshop usage patterns.
Workshop-Focused Inspection and Timely Repairs:
- Emphasizing the need for frequent inspections designed to identify potential issues early on.
- The importance of timely repairs to address wear and tear, preventing minor issues from escalating.
Operational Conditions in Workshop Environments
Workshop Weather Considerations:
- Acknowledging the impact of workshop-specific weather conditions on crane performance.
- Strategies for mitigating risks associated with temperature variations and humidity.
Addressing Corrosion in Workshop Atmospheres:
- Understanding the corrosive elements present in workshop environments.
- Implementing preventive measures, such as coatings, to combat corrosion and extend crane lifespan.
Load Capacity and Usage in Workshop Settings
Workshop Load Specifications:
- Defining load specifications based on the diverse range of materials and components handled in workshops.
- The importance of adhering to specified load capacities to prevent structural strain.
Mitigating Overloading Risks in Workshops:
- Educating operators and workshop personnel on the dangers of overloading.
- Implementing measures, such as load testing, to ensure compliance with load capacity guidelines.
Upgrades and Retrofits Tailored for Workshops
Technological Advancements Aligned with Workshop Needs:
- Integrating technology to enhance efficiency in workshop crane operations.
- Evaluating and adopting advancements that align with the specific demands of workshops.
Safety Additions Addressing Workshop Challenges:
- Identifying and implementing safety features tailored to workshop environments.
- Enhancing the overall safety of workshop crane operations through strategic retrofits.
Manufacturer Reputation in the Context of Workshop Usage
Choosing Manufacturers with Workshop Expertise:
- Evaluating manufacturers based on their understanding of workshop-specific requirements.
- Selecting partners with a proven track record of delivering reliable workshop crane solutions.
Workshop Performance Track Record:
- Analyzing the historical performance of crane models in workshop settings.
- Leveraging past experiences and success stories to inform future workshop crane investments.
Workshop-Centric Strategies for Maximizing Crane Durability
Customized Maintenance Programs for Workshops
Workshop-Specific Lubrication and Inspection Schedules:
- Designing maintenance programs tailored to the unique needs of workshop cranes.
- Establishing regular lubrication schedules that align with the frequency of crane usage in workshops.
Efficient Workshop Repairs and Replacements:
- Streamlining repair and replacement processes to minimize downtime in workshops.
- Developing protocols for swift and effective repairs, ensuring optimal crane functionality.
Load Capacity Guidelines Tailored to Workshop Requirements
Workshop Load Testing Protocols:
- Instituting rigorous load testing procedures to validate and adjust load capacities.
- Ensuring compliance with safety standards and preventing overloading risks.
Overloading Prevention Measures in Workshop Operations:
- Educating workshop personnel on the consequences of overloading.
- Implementing preventive measures, including real-time monitoring, to avert overloading incidents.
Workshop-Oriented Upgrades and Modernization
Implementing Technology for Workshop Efficiency:
- Embracing the latest technological advancements relevant to workshop operations.
- Introducing automation and smart features to enhance efficiency and precision in crane tasks.
Retrofitting to Enhance Safety and Workflow in Workshops:
- Assessing the need for retrofits to address evolving workshop safety standards.
- Enhancing workflow efficiency through strategic retrofitting initiatives.
Environmental Considerations in Workshop Context
Workshop Corrosion Protection Strategies:
- Implementing protective coatings specifically designed for workshop conditions.
- Periodically assessing and reapplying coatings to combat corrosion and extend crane lifespan.
Climate Control Solutions for Workshops:
- Exploring climate-controlled environments to shield cranes from extreme temperature variations.
- Installing ventilation and dehumidification systems to maintain optimal conditions for crane components.
Insights from Actual Service Life Statistics in Workshop Environments
Analysis of Light to Medium-duty Cranes in Workshops
Statistical Patterns and Observations:
- Examining data to identify trends and patterns in the service life of light to medium-duty cranes in workshop environments.
- Drawing insights from real-world scenarios to inform decision-making for future crane investments.
Workshop-Centric Average Lifespan: Real-world Benchmarks:
- Establishing benchmarks for the average lifespan of cranes in workshops based on statistical analysis.
- Providing a reference point for workshop operators to gauge the expected durability of their crane investments.
The following section delves into the criteria and considerations for deciding when a workshop crane needs to be retired or scrapped.
Decision-Making for Workshop Crane Retirement
Workshop Criteria for Overhauls and Repairs
Balancing Overhauls in Workshop Budgets:
- Developing cost-effective strategies for overhauls without compromising on safety and efficiency.
- Establishing a balance between maintenance budgets and the necessity for periodic overhauls.
Evaluating Structural Integrity in Workshop Context:
- Implementing thorough structural assessments to gauge the integrity of workshop cranes.
- Employing non-destructive testing methods to identify potential issues and structural weaknesses.
Performance Metrics Unique to Workshop Requirements
Aligning Crane Performance with Workshop Operations:
- Identifying key performance metrics that directly impact workshop productivity.
- Customizing performance evaluations to align with the specific tasks and demands of workshop operations.
Addressing Obsolescence in Workshop Technology:
- Keeping abreast of technological advancements and evaluating the relevance of existing crane technology in workshops.
- Planning for upgrades or replacements when technology becomes obsolete, ensuring continued efficiency.
Corrosion Management and Scrapping Decisions in Workshops
Workshop-Specific Corrosion Assessments:
- Conducting regular corrosion assessments with a focus on workshop-specific factors.
- Implementing proactive measures to manage corrosion and extend the usable life of workshop cranes.
Safe Practices for Decommissioning Cranes in Workshops:
- Establishing safe and environmentally responsible procedures for decommissioning workshop cranes.
- Adhering to regulatory standards and ensuring proper disposal or recycling of retired crane components.
In conclusion, to optimize the durability and lifecycle management of overhead and gantry cranes in workshops is a nuanced and dynamic process. By aligning strategies with the unique demands of workshop environments, stakeholders can not only extend the lifespan of their cranes but also elevate overall operational efficiency and safety. Crafting resilience is not a one-size-fits-all endeavor; it's a strategic and adaptive approach tailored to the beating heart of industrial innovation—the workshop.