Overhead Cranes in Mexico's Automotive Manufacturing Plants
Driving Efficiency: Overhead Cranes in Mexico's Automotive Manufacturing Plants
Nestled in the heart of North America, Mexico has emerged as a powerhouse in the global automotive manufacturing landscape. With a robust industry that spans the production of vehicles, auto parts, and components, Mexico has become a key player in meeting the growing demands of the automotive market.
The Mexican automotive sector has witnessed unprecedented growth, attracting major global manufacturers to establish their production facilities within its borders. Renowned for its skilled labor force, strategic geographical location, and favorable trade agreements, Mexico has solidified its position as a premier destination for automotive manufacturing.
Significance of Overhead Cranes in Industrial Operations
Within the vast expanse of automotive manufacturing plants in Mexico, the role of overhead cranes is pivotal in driving operational efficiency. These towering mechanical giants are not just equipment; they are the unsung heroes that bear the weight of the industry's ambitions. The significance of overhead cranes lies in their multifaceted contributions to industrial operations:
- Streamlining Production Processes: Overhead cranes are instrumental in streamlining the intricate production processes within automotive plants. They facilitate the seamless movement of heavy materials and components, enhancing the overall flow of manufacturing activities.
- Handling Heavy Automotive Components: In an industry where precision and strength are paramount, overhead cranes excel at handling the heavy chassis, body components, and engines that form the backbone of automotive assembly. Their lifting capabilities make them indispensable for transporting these weighty elements with utmost precision.
- Enhancing Efficiency: Efficiency is the heartbeat of any successful manufacturing operation. Overhead cranes play a vital role in optimizing efficiency by expediting material handling, reducing downtime, and contributing to the timely completion of production cycles.
As we delve deeper into the intricate web of Mexico's automotive manufacturing landscape, it becomes evident that overhead cranes are more than mechanical marvels—they are the driving force behind the industry's ability to meet demands, ensure quality, and stay competitive on the global stage. In the subsequent sections, we will explore the industrial and geographical considerations that shape the usage of overhead cranes in Mexico and delve into the diverse types and applications that make these cranes indispensable in the automotive manufacturing realm.
Types and Applications of Overhead Cranes
Overview of Overhead Crane Types
In the intricate ballet of automotive manufacturing, overhead cranes are the choreographers, orchestrating the movement of heavy components with finesse and precision. These cranes come in various types, each designed to fulfill specific roles within the manufacturing environment. The key types of overhead cranes include:
- Bridge Cranes: Bridge cranes, also known as overhead traveling cranes, are the workhorses of manufacturing plants. They consist of parallel runways with a bridge spanning the gap. The hoist, which carries the lifting hook or other attachments, moves along the bridge, covering the entire length of the runway.
- Gantry Cranes: Gantry cranes operate on a similar principle to bridge cranes but are supported by legs that run on wheels or along a track on the ground. This design provides greater flexibility, allowing gantry cranes to traverse different areas of the manufacturing facility.
- Jib Cranes: Jib cranes are versatile and compact, featuring a horizontal boom (jib) that rotates on a vertical mast. These cranes are often used in areas where a full overhead crane system might be impractical. Jib cranes excel at precise material handling in localized spaces.
- Specialized Cranes: Specialized overhead cranes cater to unique requirements within the automotive manufacturing process. This category includes explosion-proof cranes for hazardous environments, foundry cranes for high-temperature applications, and magnetic cranes for lifting ferrous materials.
Specializations for Different Applications in Automotive Manufacturing
The automotive manufacturing process involves a diverse array of tasks, each demanding specific features from overhead cranes. Specialized overhead cranes play a crucial role in meeting these demands:
- Vehicle Assembly Line Cranes: Bridge cranes with high lifting capacities and precision controls are essential for moving large vehicle chassis and body components along the assembly line. These cranes ensure the seamless integration of various parts into the final product.
- Engine Manufacturing Cranes: Overhead cranes used in engine manufacturing require precision and adaptability. Jib cranes are often employed for tasks such as lifting and positioning engine components with accuracy.
- Transmission and Suspension Component Handling: Gantry cranes are well-suited for handling transmission and suspension components due to their ability to traverse different areas of the production floor. These cranes contribute to the efficient movement of critical parts.
- Material Handling in Parts Production: Specialized cranes, such as magnetic cranes, find application in parts production where the handling of ferrous materials is frequent. These cranes enhance efficiency by securely lifting and transporting materials with magnetic properties.
- Adaptable Solutions for Varied Manufacturing Processes: Overhead cranes with adaptability to various manufacturing processes are a cornerstone of automotive production. Their ability to handle different loads and tasks contributes to the versatility required in modern manufacturing environments.
Understanding the diverse types and applications of overhead cranes sheds light on the intricate choreography of automotive manufacturing. In the upcoming sections, we will explore how workshop and warehouse features are shaped by industrial and geographical environments, influencing the design and utilization of overhead crane systems in Mexico's automotive plants.
Overhead Crane Operation in Mexico
Typical Types of Overhead Cranes
Mexico's automotive manufacturing plants leverage a diverse range of overhead crane types, each strategically chosen to fulfill specific roles in the complex production processes. The typical types of overhead cranes found in these facilities include:
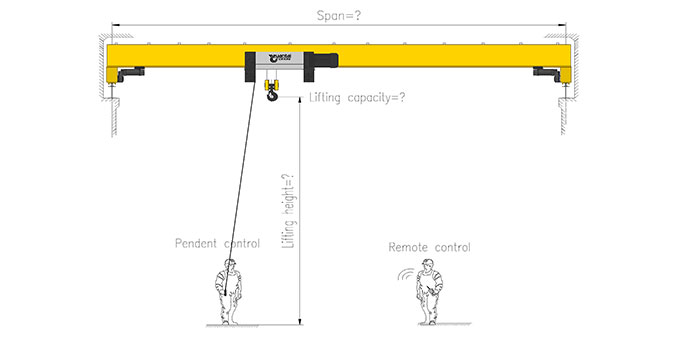
Bridge Cranes:
Features: High lifting capacities for heavy components.
Parallel runways with a bridge for extensive coverage.
Precision controls for accurate material placement.
Applications: Vehicle chassis and body component assembly.
Engine installation along assembly lines.
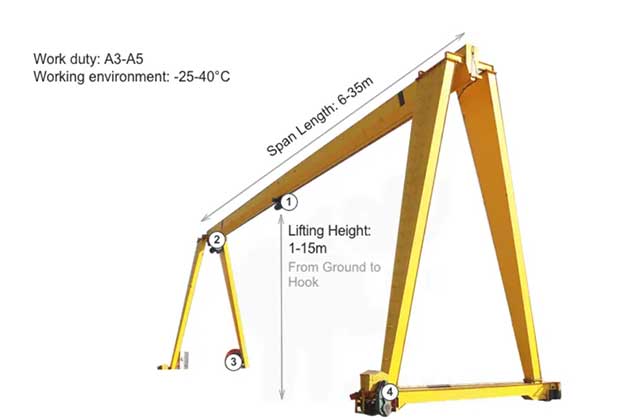
Gantry Cranes:
Features: Mobile support structure with wheels or tracks.
Ability to traverse different workstations.
Adaptability for various material handling tasks.
Applications: Efficient movement of components between different production areas.
Handling materials in storage and production zones.
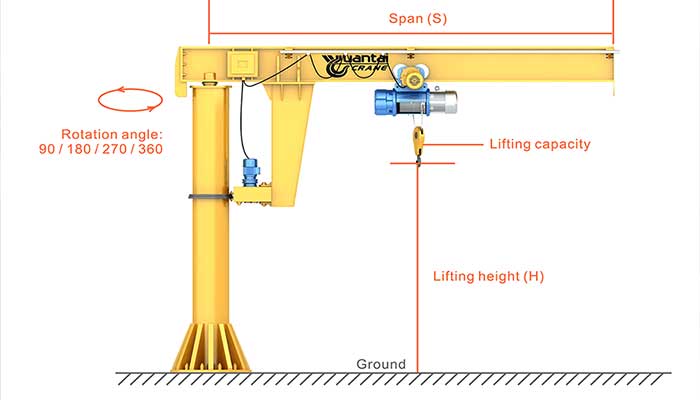
Jib Cranes:
Features: Horizontal boom (jib) rotating on a vertical mast.
Compact design for localized material handling.
Precise control for accurate positioning.
Applications: Lifting and positioning of engine components.
Support for intricate assembly tasks.
Overhead Crane Operation in Mexico
Features of Overhead Cranes
- Precision Controls: Overhead cranes in Mexico's automotive manufacturing plants boast advanced controls, enabling precise material placement. This is crucial for the intricate processes involved in vehicle assembly and component manufacturing.
- Anti-Collision Systems: Safety takes precedence, and these cranes are equipped with anti-collision systems. These features prevent accidents in the bustling production environments, ensuring a secure workplace for all personnel.
- Load Monitoring Capabilities: Overhead cranes come with sophisticated load monitoring capabilities. This allows for real-time tracking of load weights, contributing to safe load handling and preventing overloading incidents.
- IoT Integration: Embracing Industry 4.0, overhead cranes in Mexico leverage IoT integration. Real-time monitoring and data analytics enhance overall performance optimization, providing valuable insights into crane operations.
Applications in Automotive Manufacturing
- Vehicle Assembly Lines: Bridge cranes stand tall in the realm of vehicle assembly, playing a central role in moving large components along assembly lines. Their high capacity and precision controls are indispensable in ensuring the seamless assembly of complex automotive structures.
- Engine Manufacturing: Jib cranes shine in engine manufacturing, where precise positioning of heavy engine components is paramount. Their versatility makes them ideal for supporting various tasks within the engine production process.
- Material Handling: Gantry cranes, known for their efficiency, are the workhorses of material handling in automotive workshops and warehouses. They ensure swift and organized movement of materials, contributing to streamlined production processes.
Project Locations
- Assembly Lines: Overhead cranes find their stride on assembly lines, facilitating the sequential assembly of vehicle components. Their ability to cover expansive areas ensures a continuous and efficient production flow.
- Material Storage Areas: Gantry cranes take charge in material storage areas. Their adaptability and load-bearing capacity make them ideal for managing the storage and retrieval of materials, optimizing space and workflow.
- Workstations: Jib cranes are the unsung heroes at individual workstations. Their localized support enhances the efficiency of specific tasks, contributing to the overall productivity of the automotive manufacturing process.
Adaptability to Project Scale
- Large-Scale Assembly Plants: In large-scale assembly plants, the deployment of high-capacity bridge cranes is a common sight. These cranes provide extensive coverage, supporting the assembly of large and intricate automotive structures.
- Component Manufacturing Projects: For component manufacturing projects with unique requirements, adaptable gantry and jib cranes come into play. Their flexibility caters to project-specific needs, ensuring efficient and tailored material handling.
Workshop and Warehouse Features
Shaping of Workshop and Warehouse Environments
The workshop and warehouse environments in Mexico's automotive manufacturing plants are meticulously designed landscapes where efficiency, safety, and adaptability converge. These spaces serve as the canvas upon which the ballet of overhead cranes unfolds, shaping the very essence of manufacturing operations. The key elements that contribute to the shaping of workshop and warehouse environments include:
- Spatial Configuration: The layout of workshops and warehouses is strategically configured to accommodate the movement of materials, the assembly of components, and the storage of finished products. The spatial arrangement influences the placement and design of overhead crane systems.
- Workflow Optimization: Workshop and warehouse designs prioritize workflow optimization to ensure a seamless and efficient production process. Overhead cranes are integrated into these designs to enhance material handling capabilities and minimize bottlenecks.
- Flexibility and Adaptability: The automotive industry is dynamic, with changing production needs and evolving manufacturing processes. Workshop and warehouse environments are designed with flexibility and adaptability in mind, allowing for the integration of different types of overhead cranes based on evolving requirements.
Influence of Industrial and Geographical Factors
The influence of industrial and geographical factors on workshop and warehouse features is profound, shaping the utilization of overhead crane systems:
- Industrial Factors: The type of manufacturing processes, the scale of production, and the specific requirements of automotive components influence workshop features. For instance, large-scale assembly plants may have expansive workshops with multiple overhead crane systems, while smaller-scale workshops in component manufacturing may focus on precision and adaptability.
- Geographical Factors: The geographical location of automotive manufacturing plants introduces considerations related to climate, seismic activity, and available space. Workshops in regions with extreme weather conditions may require overhead cranes with special features to withstand environmental challenges. Additionally, seismic-prone areas may necessitate structural reinforcements for both workshops and crane systems.
- Integration with Local Infrastructure: The integration of workshops and warehouses with local infrastructure, including transportation networks, influences the logistics of material handling. Overhead cranes are strategically positioned to facilitate the smooth transition of materials from storage to production areas, aligning with the broader logistics framework.
- Adherence to Safety Regulations: Industrial and geographical factors also influence the adherence to safety regulations. Workshops and warehouses are designed to comply with local and international safety standards, ensuring a secure working environment for both personnel and the efficient operation of overhead crane systems.
Understanding the intricate interplay between workshop and warehouse features, industrial dynamics, and geographical considerations provides a holistic perspective on the utilization of overhead cranes in Mexico's automotive manufacturing plants. In the following sections, we will delve into the typical types, features, applications, and project locations of overhead cranes operated in Mexico, unraveling the crucial role they play in driving efficiency within this dynamic industrial landscape.
Industrial and Geographical Considerations
Automotive Manufacturing Landscape in Mexico
Mexico's automotive manufacturing landscape is a dynamic tapestry woven with the threads of innovation, collaboration, and strategic advantage. The country has positioned itself as a global hub for automotive production, attracting a diverse range of manufacturers from around the world. The key elements that define the automotive manufacturing landscape in Mexico include:
- Strategic Geographical Location: Nestled between the automotive markets of North America and South America, Mexico's geographical location is strategically advantageous. Proximity to the United States, one of the largest automotive markets globally, has facilitated efficient supply chain management and reduced transportation costs.
- Skilled Labor Force: The availability of a skilled and cost-effective labor force has been a driving force behind the success of Mexico's automotive industry. The workforce's expertise spans various aspects of automotive manufacturing, from assembly line operations to precision engineering.
- Favorable Trade Agreements: Mexico's participation in key trade agreements, such as the United States-Mexico-Canada Agreement (USMCA) and various free trade agreements, has created an environment conducive to cross-border collaboration. This has led to increased foreign direct investment and a flourishing network of automotive manufacturing facilities.
- Diverse Ecosystem of Suppliers: The automotive manufacturing landscape in Mexico is characterized by a diverse ecosystem of suppliers, ranging from Tier 1 suppliers providing major components to Tier 2 and Tier 3 suppliers offering specialized parts. This interconnected web ensures a streamlined supply chain for the industry.
Geographical Factors Influencing Overhead Crane Usage
The geographical factors that influence the usage of overhead cranes in Mexico's automotive manufacturing plants are intricately linked to the layout, size, and operational demands of the facilities. These factors include:
- Spatial Layout of Manufacturing Plants: The spatial layout of automotive manufacturing plants often dictates the need for overhead cranes. Plants with expansive layouts may require cranes with extended coverage to efficiently move materials across different sections of the facility.
- Distance from Storage and Production Areas: The distance between storage areas and production lines influences the choice of overhead cranes. Cranes are strategically positioned to minimize the time and effort required to transport heavy components from storage to the assembly line.
- Integration with Assembly Lines: Overhead cranes are integrated into the assembly line architecture to facilitate the smooth flow of production. Their placement is carefully planned to ensure minimal interference with other manufacturing processes.
- Adaptation to Local Climate: The local climate plays a role in determining the structural integrity and features of overhead cranes. Plants situated in regions with extreme temperatures or humidity levels may require specialized cranes designed to withstand environmental challenges.
Understanding these industrial and geographical considerations provides a foundational insight into the role of overhead cranes in Mexico's automotive manufacturing landscape. In the subsequent sections, we will explore the diverse types and applications of overhead cranes, shedding light on how these mechanical workhorses contribute to the efficiency and precision of automotive production.
User Guides and Best Practices
Before initiating operations, operators must conduct thorough pre-operation checks to ensure the crane's mechanical and electrical components are in optimal condition. This includes meticulous inspections of load-bearing elements such as hooks and ropes, focusing on identifying any signs of wear or damage that could compromise structural integrity. Additionally, operators need to verify the functionality of crucial safety devices, including limit switches and emergency stop buttons, ensuring a swift and effective response in unforeseen situations.
Regular inspections, conducted according to both manufacturer guidelines and industry standards, play a crucial role in proactive issue identification. This includes periodic inspections of critical components like brakes, gears, and electrical systems. Furthermore, load testing at regular intervals ensures the verification of the crane's lifting capacity, maintaining its safe and efficient operation over time.
Safe Operating Procedures
Emphasizing the use of precision controls is crucial to ensuring every movement is accurate and controlled, reducing the risk of accidents. Operators should be trained to gradually accelerate and decelerate, promoting smoother load handling and minimizing the likelihood of sudden jerks.
Strictly communicating and enforcing load capacity limits is paramount to prevent overloading, a potential cause of accidents. The implementation of real-time load monitoring systems provides operators with alerts on potential overloads, enabling immediate and informed responses.
Training operators on proper load positioning is essential to prevent swinging or unintended movements that could compromise safety. Stressing the importance of aligning the load directly under the hook during lifting ensures secure and precise material handling.
Load Handling Techniques
Instructing operators on the critical importance of load balancing for stable lifting, especially when dealing with irregularly shaped loads, enhances stability and ensures secure and controlled material handling. Utilizing spreader bars or multiple hooks for even weight distribution is a common practice in achieving this.
Encouraging smooth and controlled movements helps prevent sudden starts or stops, mitigating the risk of accidents. Operators should be trained to anticipate the load's behavior during lifting, movement, and lowering, creating a safer operational environment.
Maintenance and Inspection Schedule
Developing and adhering to a comprehensive routine maintenance schedule covering all overhead crane components is essential for long-term operational efficiency. Regular lubrication of moving parts reduces friction, minimizes wear, and extends the lifespan of critical components.
Conducting scheduled inspections by certified technicians is crucial for identifying potential issues and addressing them promptly. Detailed records of all maintenance activities, inspections, and repairs performed provide a comprehensive overview of the crane's condition and contribute to ongoing reliability.
Training Programs for Crane Operators
Implementing certification programs for crane operators ensures their skills align with industry standards and regulations. Combining theoretical and practical training components enhances operators' understanding of crane systems, contributing to their ability to operate equipment safely.
Providing ongoing education keeps operators informed about the latest advancements in crane technology and safety practices. Regular refresher courses reinforce safe operating procedures, fostering a culture of continuous improvement in crane operation skills.
Emergency Response and Safety Protocols
Training operators on immediate response procedures in emergencies is crucial for swift and effective action. Ensuring that emergency stop buttons are easily accessible and regularly tested maintains their functionality, contributing to a quick and controlled response.
Developing and communicating clear evacuation plans for crane operators and personnel in emergencies is essential. Regular drills ensure everyone is familiar with evacuation procedures, promoting a quick and orderly response and enhancing overall safety.
Establishing clear communication protocols between crane operators and ground personnel, utilizing standardized signals and communication devices, is vital. Efficient relay of instructions and warnings minimizes the risk of miscommunication, enhancing overall safety in crane operations.
Regulatory Compliance and Standards in Automotive Manufacturing
Overview of Relevant Safety Standards
- International Standards: An in-depth exploration of international safety standards, such as ISO 4301-1, is essential. ISO 4301-1 outlines general principles for crane design and classification, emphasizing the significance of adherence to these global standards. This ensures not only safety but also interoperability, promoting a unified and secure operational environment.
- Local Regulations: Examining local safety standards specific to the automotive manufacturing sector in Mexico is crucial. Understanding and complying with both international and local standards are fundamental for establishing and maintaining a safe working environment. This section provides insights into the nuances of safety requirements tailored to Mexico's industrial landscape.
Compliance with Mexican Industrial Safety Regulations
- Mexican Labor Law: Offering an overview of pertinent sections of the Mexican Labor Law related to industrial safety, with a specific focus on crane operation, helps emphasize the legal obligations of employers. Highlighting these obligations underscores the importance of providing a safe workplace environment for all personnel.
- National Institute of Occupational Safety and Health (INSST): Delving into guidelines and regulations set by INSST regarding the operation of industrial equipment, including overhead cranes, provides practical insights. This section underscores the significance of regular inspections and strict compliance with safety protocols outlined by authoritative bodies like INSST.
Certification and Inspection Requirements
- Certification Bodies: Identifying recognized certification bodies responsible for assessing and certifying overhead cranes in Mexico sheds light on the validation processes. Explanation of their role in ensuring that cranes meet safety and performance standards builds confidence in the reliability of certified equipment.
- Inspection Frequency: Outlining the recommended frequency of inspections is critical. Emphasis on routine inspections and more extensive periodic examinations helps stakeholders understand the importance of regular assessments. Factors influencing inspection intervals, such as usage intensity and environmental conditions, are discussed for a comprehensive understanding.
Documentation Requirements
Clarifying the documentation required for certification and inspection compliance is essential. Stressing the importance of maintaining accurate records of inspections, repairs, and maintenance activities is crucial for transparency and accountability. This section provides practical guidance on documentation practices.
In conclusion, the successful operation of overhead cranes in Mexico's automotive manufacturing plants requires a holistic approach that considers industrial, geographical, and regulatory factors. By prioritizing safety, selecting reliable suppliers, and embracing technological advancements, automotive manufacturers can drive efficiency and contribute to the overall success of the industry.