Automatic Gantry Crane Positioning with Flag and Encoder System
![automatic gantry crane positioning system]()
System Overview
The automatic rail mounted gantry crane positioning system is a critical component of automated gantry crane operations, responsible for precisely locating the gantry (truck) as it travels along its longitudinal rails. This system uses a hybrid approach combining physical reference markers (FLAG boards) and an absolute rotary encoder to achieve continuous, accurate, and reliable position tracking with built-in redundancy.
By leveraging both absolute and relative positioning technologies, the system ensures robust performance even in environments with dust, vibrations, or variable weather conditions—common in port or container yard applications.
Components and Working Principle
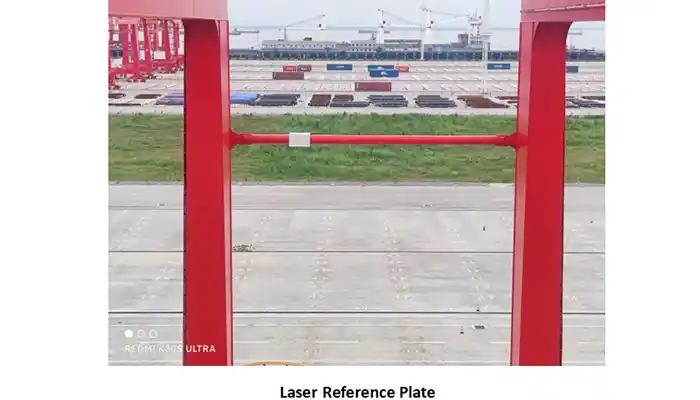
1. FLAG Boards (Positioning Plates):
FLAG boards are fixed, uniquely coded plates installed along the gantry's travel path on both sides of the runway beam. These plates contain encoded position data, typically in a barcode, QR, or reflective binary format. The data on each FLAG board corresponds to a specific absolute position along the track.
The FLAG boards are spaced at regular intervals (e.g., every few meters), acting as stationary reference points for the gantry’s position.
2. Reflector Sensors (FLAG Readers):
Mounted on both sides of the moving gantry, reflector sensors (such as optical or laser readers) are responsible for scanning the FLAG boards as the gantry passes by. These sensors capture the absolute location data embedded in the FLAG board and transmit it to the crane's control system.
This provides an externally verified absolute position, independent of cumulative mechanical errors.
3. Absolute Rotary Encoder:
Installed on the drive shaft or wheel assembly of the gantry, the absolute encoder continuously tracks motion by measuring the rotation of the gantry’s drive wheels. It translates rotational movement into linear distance and provides high-resolution position feedback.
Unlike incremental encoders, absolute encoders maintain position data even after power loss or system restart, offering a reliable reference for real-time motion control.
Operation and Positioning Logic
- As the gantry moves, the absolute encoder provides continuous position tracking based on wheel rotation.
- When the gantry passes a FLAG board, the sensor reads the board’s absolute position and compares it with the encoder’s calculated position.
- If the values align within the acceptable deviation range (±20 mm), the encoder value is considered accurate.
- If there is a discrepancy, the encoder reading is corrected or recalibrated using the FLAG board’s absolute position.
- This dual-input system allows for continuous tracking between FLAG boards and error correction whenever a FLAG board is encountered.
The result is a high-precision positioning system that is resilient to drift, encoder slip, or signal interruption.
Technical Specifications
- Positioning accuracy with respect to the actual gantry location: ≤ ±20 mm
- Encoder resolution: Typically 16-18 bits, offering high precision per revolution
- Sensor response time: Fast enough for high-speed gantry movements, with low latency scanning
- Environmental protection: Components can be rated IP65 or higher to withstand dust and moisture
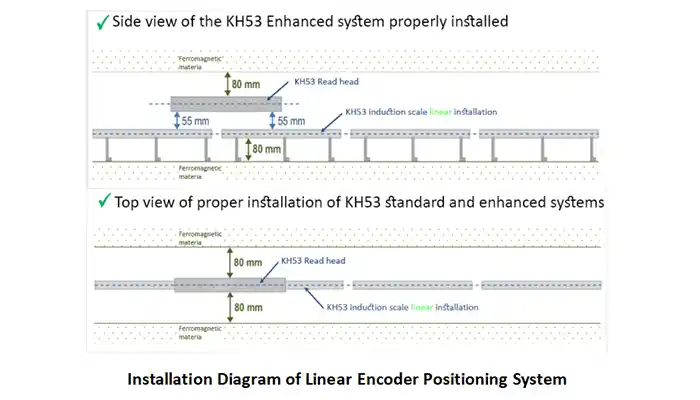
Installation and Layout
The typical installation includes:
- FLAG boards mounted at fixed intervals along both sides of the gantry rail path.
- FLAG readers or optical sensors installed on each side of the gantry, aligned with the FLAG boards.
- An absolute encoder mounted on the gantry’s drive mechanism (gearbox or wheel shaft).
- All sensors and encoders connected to the crane’s Equipment Control System (ECS) or Automatic Crane Control System (ACCS), where data is processed in real-time.
Diagrams often show the FLAG boards along the track, sensors on the gantry legs, and the encoder near the drive wheels, with cable routing toward the onboard control panel.
Integration with Control Systems
The gantry positioning system feeds real-time data to:
- ECS (Equipment Control System): For precise motion control, synchronization with the trolley and hoist, and travel limit enforcement.
- ACCS (Automatic Crane Control System): For automated operation, collision avoidance, and workflow optimization.
- ROCS (Remote Operation Control System): For operator visibility, remote overrides, and system diagnostics.
Data from the gantry positioning system is also used for:
- Automated container alignment
- Yard navigation and map updating
- Safety zone enforcement and obstacle avoidance
Key Benefits
- High-accuracy positioning (≤ ±20 mm) critical for automated handling of containers or heavy loads.
- Redundancy through dual sensing eliminates the risk of cumulative encoder error.
- Failsafe operation: The gantry can still self-correct using FLAG board references even if the encoder experiences slippage or drift.
- Robust performance: Suitable for long-distance gantry travel and outdoor operation.
If you want, I can also help visualize this with a technical drawing or assist in formatting it for use in a technical manual or sales brochure. Let me know how you'd like to proceed.