Integration of 40.5 Ton to 65 Ton RTGs in Railroad Systems
Overview of Multi-Modal Container Handling
Multi-modal transportation uses more than one type of transport—rail, road, and sea—to move goods from one place to another. This system allows each transport mode to do what it does best, helping goods travel faster and more efficiently.
- Rail: Moves goods over long distances on tracks.
- Road: Provides flexibility to transport goods to and from ports and rail terminals.
- Sea: Used for global shipping, connecting countries and ports.
Efficiency in container handling is key to this system. As containers are transferred between rail, road, and sea, they need to be moved quickly to avoid delays. Efficient handling increases speed, reduces costs, and boosts the capacity of transportation systems.
Introduction to Rubber-Tyred Gantry Cranes (RTGs)
Rubber-Tyred Gantry Cranes (RTGs) are mobile cranes used in container terminals to move containers between trucks, railcars, and ships. Their rubber tyres allow them to travel easily along the yard, making them very flexible.
- Capacity: RTGs typically lift between 40 and 65 tons.
- Use: These cranes handle standard containers, which can weigh between 2.5 tons (empty) and 30 tons (full).
- Function: RTGs can stack containers and move them across the terminal, helping to make better use of limited space and improving overall terminal efficiency.
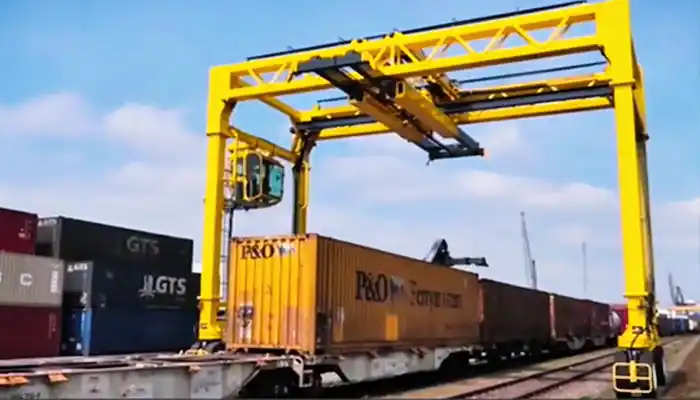
Role of RTGs in Multi-Modal Systems
Container Handling Efficiency
RTGs play a key role in making container transfers quick and smooth between different transport modes—railcars, trucks, and ships.
- Efficient Transfers: RTGs move containers between railcars, trucks, and ships without delays, speeding up the process.
- Handling Different Weights: With capacities ranging from 40 to 65 tons, RTGs can lift both light and heavy containers, ensuring flexibility in handling various types of cargo.
- Size Flexibility: RTGs can handle containers of different sizes, from standard 20-foot containers to larger 40-foot containers, making them versatile for different terminal needs.
This efficiency helps reduce waiting times and increases the flow of goods through the terminal, allowing quicker turnaround and better overall terminal performance.
Increased Operational Flexibility
RTGs are highly flexible and mobile, which is essential for terminals that need to adapt to different environments and operational needs.
- Mobility Within the Terminal: RTGs can move easily across the terminal, providing quick access to containers no matter where they are located. This mobility is especially useful in large terminals with complex layouts.
- Handling Limited Space: In terminals where space is limited, RTGs can efficiently move containers without the need for fixed tracks or complex infrastructure.
- Adaptability to Different Environments: Whether in a busy port, a rail yard, or an inland container depot, RTGs can adjust to varying environments and handle diverse cargo types.
This flexibility makes RTGs valuable in terminals with complex operations or those located in spaces with limited room for large cranes.
Integration with Other Logistics Equipment
Interaction with Terminal Tractors and Trucks
RTGs work closely with yard trucks and terminal tractors to move containers efficiently across the terminal.
- Coordinated Movement: RTGs lift and place containers onto trucks or railcars, while terminal tractors and yard trucks transport these containers to their next destination.
- Smooth Transfers: The coordination between RTGs and road transport vehicles ensures a quick and seamless transfer of containers, reducing delays and increasing terminal throughput.
- Efficient Workflow: As RTGs handle the lifting, yard trucks manage the movement, allowing for a constant flow of containers without bottlenecks.
This interaction helps improve the overall efficiency of container handling, ensuring that containers are quickly loaded, unloaded, and transported to their next stop.
Collaboration with Automated Guided Vehicles (AGVs)
RTGs also work well with Automated Guided Vehicles (AGVs), which are self-driving vehicles used to transport containers within the terminal.
- Seamless Movement: RTGs and AGVs work together to ensure containers are quickly and safely moved from one location to another. While RTGs handle the heavy lifting, AGVs manage the transport within the terminal.
- Automation Advantage: The combination of RTGs and AGVs creates an automated system that reduces human intervention, improves accuracy, and speeds up operations.
- Increased Efficiency: The use of both RTGs and AGVs reduces wait times, increases throughput, and improves container tracking, making the terminal more efficient and cost-effective.
This integration is especially beneficial in automated or semi-automated terminals, where the goal is to minimize human error and maximize operational speed.
Integration with Container Handling Systems (CHS)
RTGs can be linked with other container handling equipment, like reach stackers and ship-to-shore cranes, to create a fully integrated system.
- Coordinated Operations: RTGs work alongside reach stackers to stack containers in the yard and ship-to-shore cranes to load and unload containers from vessels.
- Optimized Workflow: By connecting RTGs with other equipment in the container handling system (CHS), terminals can optimize their workflows. Containers are moved between different equipment types in a smooth and efficient manner, reducing downtime.
- Advanced Coordination: The integration of RTGs with other handling equipment ensures that containers are transferred with minimal delays, allowing for better resource utilization and more streamlined operations.
This coordinated approach boosts terminal productivity, ensuring containers are handled quickly and accurately from arrival to departure.
Integration with Rail Systems
Container Transfer Between Rail and Terminal
RTGs play a critical role in transferring containers between railcars and terminal yards.
- Efficient Transfers: RTGs lift containers from railcars and place them onto trucks or stack them in the yard for storage. They are particularly effective in high-volume terminals where quick transfers are essential.
- Handling Heavy and Oversized Containers: With capacities ranging from 40 to 65 tons, RTGs can easily manage heavy and oversized containers, ensuring they are safely lifted and transported. This capacity is especially important for handling large containers often found in rail systems.
By facilitating these transfers, RTGs ensure a smooth and continuous flow of containers, reducing delays and improving overall terminal efficiency.
Synchronization with Rail Schedules
RTGs must align with rail schedules to ensure containers are loaded and unloaded promptly.
- Timing Coordination: RTGs are synchronized with train schedules to ensure timely container handling. This coordination allows containers to be transferred quickly from railcars to trucks or other transport modes without delays.
- Reducing Dwell Times: By aligning with rail schedules, RTGs help reduce the amount of time containers spend in the terminal (known as dwell time). Shorter dwell times mean faster turnaround, which leads to increased throughput.
- Improved Efficiency: This synchronization allows for smooth and timely operations, which is critical for maintaining high levels of efficiency in the terminal.
This coordination is essential for maintaining terminal productivity and ensuring that containers are swiftly moved to their next destination.
Safety and Security Considerations
RTGs are equipped with several safety features to ensure secure container handling within rail systems.
- Safety Protocols: RTGs follow strict safety protocols to ensure containers are safely lifted and moved. This includes checking load stability, using warning signals to prevent accidents, and ensuring proper securing of containers during handling.
- Load Stability: RTGs are designed to maintain load stability during operations. They feature anti-sway technology, which minimizes container movement during lifting and transportation, reducing the risk of accidents or damage.
- Secure Operations: RTGs also include safety measures such as emergency stops, overload detection, and safety interlocks to prevent mishandling and ensure that containers are moved securely.
These safety features help ensure that operations within rail systems are conducted with minimal risk, providing secure and efficient handling of containers.
Impact on Terminal and Operational Efficiency
Space Optimization
RTGs play a crucial role in maximizing container storage in terminals with limited space.
- Maximized Stacking Capacity: RTGs allow for high-density stacking of containers, enabling terminals to store more containers in a smaller are This capability is particularly valuable in crowded or urban locations where space is limited.
- Efficient Use of Available Space: By efficiently moving and stacking containers, RTGs help terminals make the most of the available space, reducing congestion and improving container flow.
This optimized use of space enables terminals to handle a higher volume of containers without expanding their physical footprint, increasing terminal efficiency.
Reducing Operational Costs
Modern RTGs are designed to be cost-effective, reducing both energy consumption and maintenance costs.
- Energy Efficiency: Newer RTG designs are more energy-efficient, using advanced power systems that reduce fuel consumption and lower operational costs. This makes RTGs more sustainable in the long term.
- Lower Maintenance Costs: RTGs with capacities of 40-65 tons are built to last longer, requiring less frequent maintenance. The durable design and fewer mechanical issues reduce the overall cost of repairs and downtime.
- Longer Service Life: With regular maintenance, modern RTGs can provide years of reliable service, offering terminals a solid return on investment.
By cutting energy costs and extending service life, RTGs help terminals reduce operational expenses while boosting performance.
Faster Turnaround Times
The efficiency of RTGs directly impacts how quickly containers are handled at terminals.
- Speed and Precision: RTGs handle containers quickly and accurately, ensuring that containers are transferred with minimal delay. The fast lifting and precise movements lead to quicker container handling times.
- Reduced Turnaround Time: Faster container handling reduces the time containers spend in the terminal, which in turn increases the throughput. This means more containers can be processed within a shorter time, leading to faster operations overall.
Faster turnaround times improve terminal flow, reduce congestion, and enhance productivity, contributing to the overall efficiency of the terminal’s operations.
Challenges and Considerations in Integration
Operational Complexity
Integrating RTGs into multi-modal systems can introduce operational challenges.
- Coordination Challenges: RTGs must work in harmony with other equipment like terminal tractors, Automated Guided Vehicles (AGVs), and rail systems. Coordinating these systems effectively can be complex, especially in terminals with diverse cargo types and transport modes.
- Advanced Terminal Management: To ensure smooth operation, modern terminal management systems (TMS) are needed. These systems help manage the coordination of RTGs with other equipment, monitor container movements, and optimize terminal workflows. Without such systems, delays and inefficiencies may arise.
Effective integration requires investment in both technology and staff training to keep operations running smoothly across various transport modes.
Environmental Factors
Environmental conditions can impact the performance of RTGs, especially in regions with extreme weather conditions.
- Weather Impact: Harsh weather conditions, such as high winds, heavy rain, or extreme temperatures, can affect the stability and efficiency of RTGs. These factors can slow down operations or require additional safety measures.
- Adapting RTGs: RTGs can be equipped with features to adapt to different weather conditions. For instance, wind sensors can detect strong gusts and automatically slow down operations to prevent accidents. Similarly, RTGs can be designed with corrosion-resistant materials to withstand humid or salty environments in coastal areas.
By tailoring RTGs to specific environmental conditions, terminals can ensure reliable performance and minimize the impact of adverse weather.
Safety and Risk Management
RTGs must be operated safely, especially in busy, multi-modal environments where risks are higher.
- Risk Mitigation: The operation of RTGs in areas with high traffic—such as rail yards and port terminals—can present safety risks. Ensuring safe operations requires proper risk management strategies, including safety protocols, operator training, and regular maintenance checks.
- Operator Safety: RTGs are equipped with features to protect operators, such as emergency stop buttons, load sensors, and anti-collision systems. These features reduce the likelihood of accidents and enhance overall safety during operations.
- Preventing Accidents: With multi-modal operations, the risk of accidents increases. It’s essential to implement safety measures such as warning signals, fencing around operating areas, and clear traffic lanes to ensure the safety of both operators and equipment.
Ensuring safety in the operation of RTGs is crucial to maintaining smooth, risk-free terminal operations and protecting personnel.
Conclusion
Recap of the Importance of RTGs in Multi-Modal Systems
Rubber-Tyred Gantry Cranes (RTGs) play a pivotal role in enhancing the efficiency of multi-modal railroad container handling systems. Their integration into terminals has brought several significant benefits:
- Improved Container Handling Efficiency: RTGs streamline the transfer of containers between railcars, trucks, and ships, ensuring smooth and fast operations across multiple transport modes.
- Increased Operational Flexibility: The mobility of RTGs within terminals allows for efficient operations in various environments, even in space-constrained or complex terminal layouts.
- Cost Savings and Higher Throughput: With their ability to increase throughput and reduce delays, RTGs contribute to reduced operational costs and enhanced terminal performance.
- Space Optimization: RTGs maximize stacking capacity, allowing terminals to handle a higher volume of containers in limited space.
In short, RTGs help create more efficient, flexible, and cost-effective container handling processes, leading to smoother operations across rail, road, and sea transport.
In conclusion, RTGs will continue to be a cornerstone in the integration of multi-modal railroad container handling systems, driving further improvements in terminal efficiency, cost-effectiveness, and sustainability. Their role in the future of global logistics is undeniable, shaping the way containers move across the world.