35 Ton Overhead Crane Steel Coil Handling in Steel Industrial Sector
35 Ton Overhead Crane Steel Coil Handling in Steel Industrial Sector.35 ton overhead crane for sale. Mastering efficiency & safety with 35 ton overhead cranes - A Comprehensive Guide for the Steel Industry. Design for you.
35 ton Overhead Crane Operation in Steel Industrial Sectors
Welcome to our comprehensive guide on the efficient and safe operation of 35 ton overhead cranes within the dynamic landscape of the steel industry. In this guide, we delve into the critical aspects of crane operation, offering valuable insights for crane buyers and operators navigating the intricate steel production processes.
The backbone of heavy-duty lifting in the steel industry, 35 ton overhead cranes are robust pieces of equipment designed for precision and strength. These cranes play a pivotal role in material handling, ensuring the seamless flow of raw materials, heavy machinery components, and finished products within steel facilities.
Efficient crane operation is not merely a luxury but a necessity in the steel industry. The scale and intricacy of steel production demand a reliable and well-operated lifting solution. Proper crane operation directly impacts productivity, safety, and the overall success of steel manufacturing processes. A misstep in crane operation can lead to costly delays, compromised safety, and potential damage to valuable equipment.This guide is tailored for two crucial groups within the steel industry: crane buyers and operators. For crane buyers, we provide insights into selecting the right 35 ton overhead crane based on the unique requirements of different workshops and facilities. Operators, on the other hand, will benefit from a deep dive into operational best practices, safety guidelines, and procedures specific to various phases of steel production.
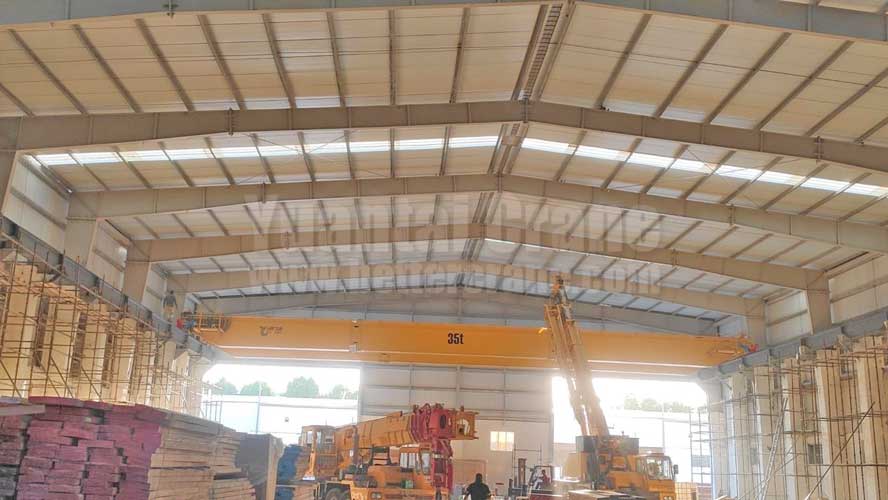
35 ton overhead crane for steel coil handling, custom 35 ton crane project for sale
Overview of Steel Production Processes
Steel production is a multifaceted process involving several stages, each demanding precise handling and movement of materials. From the extraction of raw materials to the delivery of finished products, the steel production journey comprises:
Mining and Extraction: Raw materials like iron ore and coal are extracted from mines.
Transportation: Materials are transported to steel plants using various means, emphasizing the need for efficient cranes in loading and unloading.
Processing: Raw materials undergo processing, with cranes assisting in the movement of heavy machinery and components.
Identification of Key Locations Within a Steel Facility
Understanding the layout of a steel facility is crucial for efficient crane operation. Key locations include:
Raw Material Storage: Cranes facilitate the movement of raw materials within storage areas.
Production Floors: Heavy machinery and components are lifted and positioned during the manufacturing process.
Finished Product Areas: Cranes play a vital role in handling and transporting finished steel products.
Overview of Raw Material Handling, Production, and Finished Product Areas
Raw Material Handling: Cranes are essential for unloading raw materials, transporting them to processing areas, and positioning them for further use.
Production Areas: Cranes assist in assembling and positioning heavy machinery components, ensuring a smooth manufacturing process.
Finished Product Areas: Efficient handling of finished steel products is critical for timely delivery, and cranes play a central role in this phase.
Crane Selection Considerations
Understanding Steel Industry Requirements- Load Capacity and Size Requirements:Determine the maximum weight and dimensions of loads to be lifted within the steel facility. Assess the size of the workspace to ensure the crane's span and lifting height align with operational needs.
- Operational Speed and Precision:Consider the required speed and precision for lifting and positioning tasks within different workshops or facilities. Evaluate the crane's control systems and features to meet specific operational speed and accuracy demands.
- Environmental Factors:Account for environmental conditions, such as temperature, humidity, and potential exposure to corrosive elements, to select a crane with suitable protection features.
Evaluating the Specific Needs of Different Workshops or Facilities
- Workshop Layout and Design:Analyze the layout of workshops or facilities to determine the optimal crane configuration for efficient material flow. - Consider factors such as aisle width, ceiling height, and potential obstacles that may impact crane movement.
- Frequency of Use:Assess the intensity of crane usage in different areas to determine the appropriate duty cycle and crane design for continuous or intermittent operation.
- Versatility and Adaptability:Evaluate the adaptability of the crane to various tasks within different workshops, ensuring it can handle diverse loads and operational scenarios.
Customization Options for 35 ton Overhead Cranes
- Specialized Attachments:Explore the availability of specialized attachments like magnets, hooks, or grabs to enhance the crane's versatility in handling different types of materials.
- Control Systems:Consider advanced control systems, such as radio remote controls or automation features, to improve efficiency and operator control during diverse operations.
- Safety Features:Opt for additional safety features, such as collision avoidance systems and overload protection, to enhance overall safety during crane operations.
- Adaptability to Future Needs:Select a crane model that allows for future modifications or upgrades to accommodate changes in production processes or facility layouts.
Understanding steel industry requirements, assessing workshop-specific needs, and exploring customization options are crucial steps in ensuring the chosen 35 ton overhead crane aligns perfectly with the demands of the steel production environment. In Part 4, we will delve into the critical aspect of safety guidelines, emphasizing the paramount importance of safe crane operations within the steel industry.
Safety Guidelines in Steel Industry Crane Operations
Importance of Safety in Steel Industry Crane Operations- Risk Mitigation:Highlight the potential risks associated with crane operations in the steel industry, emphasizing the need for proactive safety measures. Address common hazards, such as high loads, restricted visibility, and the presence of personnel in the work area.
- Safety Culture:Stress the importance of fostering a safety-centric culture within the steel facility, encouraging collaboration among all personnel to maintain a secure working environment.
Compliance with Industry Standards and Regulations
- OSHA and Industry Standards:Outline the key safety regulations set by the Occupational Safety and Health Administration (OSHA) and other relevant industry standards. Emphasize the legal obligations of the facility to adhere to these standards for safe crane operations.
- Certification Requirements:Discuss the necessity for operators to obtain proper certifications, ensuring they have undergone training programs that align with industry standards.
Pre-operation Safety Checks and Inspections
- Visual Inspections:Establish a routine for visual inspections to identify any visible signs of wear, damage, or irregularities in the crane structure, hoist, and components.
- Functional Testing:Conduct functional tests on critical components, including brakes, hoisting mechanisms, and emergency stop systems, to verify proper operation before each use.
- Load Testing:Periodically perform load testing to ensure the crane can safely handle its maximum rated load without compromising structural integrity.
- Documentation and Record-keeping:Stress the importance of maintaining detailed records of inspections, repairs, and maintenance activities to track the crane's performance over time.
- Emergency Preparedness:Develop and communicate emergency response plans, including procedures for addressing malfunctions, power outages, or other unexpected situations.
Preparation for Operation
Preparing the Crane for Operation in Different Workshops- Workspace Assessment:Evaluate the workspace in different workshops to ensure it is clear of obstacles and suitable for crane operations. Check for any changes in workshop layout or conditions that may affect crane movement.
- Equipment Readiness:Verify that the crane is in optimal working condition by conducting pre-operation checks on mechanical, electrical, and hydraulic systems.
Communication Protocols Between Crane Operators and Other Personnel
- Clear Communication Channels:Establish clear communication channels between crane operators and other personnel involved in the operation. Use standardized signals or communication devices to convey instructions effectively.
- Coordination with Ground Crew:Emphasize the importance of coordination with ground crew members during load movements to avoid collisions or accidents.
Load Calculation and Center of Gravity Considerations
- Load Capacity Assessment:Calculate the weight and dimensions of the load to ensure it falls within the crane's rated capacity. Consider factors such as load stability and potential shifts during lifting and movement.
- Center of Gravity Analysis:Determine the center of gravity for irregularly shaped or asymmetrical loads, ensuring proper load distribution during lifting operations. Highlight the impact of load positioning on crane stability and safe operation.
By prioritizing safety guidelines and implementing rigorous pre-operation checks, steel industry facilities can establish a secure environment for crane operations. In Part 5, we will explore the crucial procedures for different phases of steel production, focusing on raw material handling, production, and finished product areas.
Procedures for Different Steel Production Phases
Raw Material HandlingLifting and Transporting Raw Materials
- Material Identification:Implement a system for clearly identifying different types of raw materials to ensure proper handling and transportation.
- Load Attachment:Utilize appropriate attachments, such as hooks or grabs, to securely lift and transport raw materials without causing damage.
- Lifting Techniques:Train operators on the proper lifting techniques, considering the weight, shape, and dimensions of various raw materials.
- Load Balancing:Emphasize the importance of evenly distributing the load to maintain stability during lifting and transportation.
Maneuvering Around Storage Areas and Loading Zones
- Optimal Path Planning:Develop optimal paths for crane movement within storage areas and loading zones to minimize the risk of collisions and streamline operations.
- Clear Communication:Establish clear communication protocols between crane operators and ground personnel to coordinate movements in storage and loading areas.
- Speed Control:Emphasize the need for controlled and steady crane movements in confined spaces to prevent accidents and ensure precise material positioning.
- Emergency Protocols:Train operators on emergency procedures, including immediate stops and responses to unforeseen obstacles or hazards in storage and loading zones.
These procedures for raw material handling set the foundation for efficient and safe operations in the initial phases of steel production. In Part 7, we will delve into the intricacies of handling heavy machinery components during the manufacturing process within steel production facilities.
Procedures for Different Steel Production Phases
Steel Production
Handling and Positioning Heavy Machinery Components
- Machinery Identification:Implement a comprehensive labeling system for heavy machinery components to aid in easy identification during handling and positioning.
- Specialized Attachments:Use specialized crane attachments, such as spreader bars or lifting beams, to ensure secure and balanced handling of large and heavy machinery components.
- Precision Movements:Train crane operators on precise movements to accurately position machinery components, avoiding collisions with surrounding structures or equipment.
- Safety Measures:Enforce strict safety measures during the handling of heavy machinery, including the use of personnel barriers and warning signals to prevent accidents.
Efficient Movement During the Manufacturing Process
- Workflow Optimization:Collaborate with production planners to optimize the crane movement workflow during the manufacturing process, ensuring timely and seamless operations.
- Real-time Communication:Establish real-time communication channels between crane operators and production teams to adjust movements based on the progress of manufacturing tasks.
- Adaptability to Production Changes:Ensure that crane operations can adapt to changes in the production schedule or modifications to the manufacturing process without compromising efficiency.
- Integration with Other Systems:Explore opportunities for integrating crane operations with other manufacturing systems, such as automated conveyor systems, for a more streamlined production process.
- Continuous Monitoring:Implement monitoring systems to track the efficiency of crane movements during steel production, allowing for continuous improvement and optimization.
Efficiently handling and positioning heavy machinery components is crucial to the success of steel production. By optimizing movements during the manufacturing process, facilities can enhance overall productivity and maintain a safe working environment. In Part 8, we will explore the final phase of steel production, focusing on the careful handling of finished steel products within industrial facilities.
Procedures for Different Steel Production Phases
Finished Products
Careful Handling of Finished Steel Products
- Product Identification:Implement a robust identification system for finished steel products to ensure accurate and careful handling during crane operations.
- Gentle Lifting Techniques:Train operators in gentle lifting techniques, especially for delicate or finished products that may be susceptible to damage.
- Use of Cushioning Devices:Consider the use of cushioning devices or attachments to minimize shocks and vibrations during the lifting and movement of finished steel products.
- Avoidance of Abrasions:Emphasize the importance of avoiding abrasions or scratches on the surface of finished products by employing proper lifting and handling methods.
Loading and Unloading Finished Goods from Production Lines
- Efficient Loading Procedures:Develop standardized procedures for the efficient loading of finished steel products onto transport vehicles, ensuring timely delivery to storage or distribution areas.
- Unloading Protocols:Establish protocols for unloading finished goods from production lines, emphasizing precision to prevent damage and maintain product integrity.
- Coordination with Transportation Teams:Foster effective communication and coordination between crane operators and transportation teams to streamline loading and unloading processes.
- Quality Checks:Integrate quality checks into the loading and unloading procedures to identify and address any issues with finished products before they leave the production area.
- Safe Storage Protocols:Implement safe storage protocols for finished goods, considering factors such as weight distribution and stability to prevent accidents during storage.
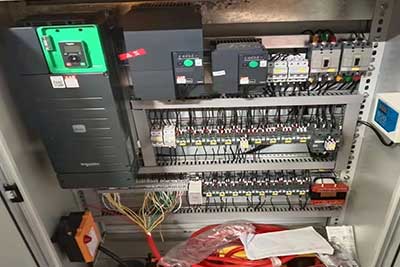
Electric control box of 35 ton, click to learn more 35 ton crane production picture and specifications for Qatar
Operational Best Practices
Proper Use of Crane Controls and Features
- Control System Familiarity:Ensure that crane operators are thoroughly familiar with the control systems specific to the 35 ton overhead crane model in use.
- Regular Training Sessions:Conduct regular training sessions to update operators on any new features or advancements in control technology.
- Emergency Shutdown Procedures:Train operators on emergency shutdown procedures to be employed in the event of malfunctions or safety concerns.
- Control Panel Ergonomics:Emphasize the ergonomic design of control panels, encouraging operators to maintain a comfortable and alert position during operation.
Techniques for Precise Positioning and Load Control
- Load Assessment:Prioritize accurate load assessment to determine weight, center of gravity, and potential shifts during movement.
- Slow and Controlled Movements:Encourage operators to execute slow and controlled movements, especially during critical phases such as positioning heavy machinery components or finished products.
- Use of Anti-Sway Systems:Implement anti-sway systems or features to minimize swinging of the load, ensuring precise positioning and reducing the risk of collisions.
- Continuous Monitoring:Train operators to continuously monitor load stability and make real-time adjustments to maintain control and prevent accidents.
- Positioning Markers:Utilize positioning markers on the floor or overhead to assist operators in achieving precise placement of loads.
Common Challenges and Troubleshooting Tips
- Power Failures:Establish procedures for safely lowering loads in the event of a power failure, preventing sudden drops or accidents.
- Overloading Situations:Train operators to recognize signs of overloading and to follow proper protocols for addressing these situations promptly.
- Mechanical Failures:Conduct regular inspections and maintenance to identify and address potential mechanical failures before they escalate.
- Communication Breakdowns:Implement redundant communication systems to address situations where standard communication channels may fail.
- Weather Considerations:Develop protocols for adverse weather conditions, such as high winds, to ensure safe crane operations.
By focusing on the proper use of controls, techniques for precise load control, and preparing for common challenges, crane operators can maximize efficiency while minimizing the risk of accidents or disruptions in steel production operations. In Part 10, we will explore the importance of routine maintenance and inspections, providing guidelines for ensuring the longevity and reliability of 35 ton overhead cranes in the steel industry.
Routine Maintenance and Inspections
Importance of Regular Maintenance for Crane Longevity- Enhanced Reliability:Emphasize the correlation between regular maintenance and the overall reliability of the 35 ton overhead crane, ensuring consistent and efficient performance.
- Extended Lifespan:Highlight how routine maintenance practices contribute to the extended lifespan of critical components, reducing the likelihood of costly replacements.
- Cost Savings:Showcase how investing in regular maintenance can lead to significant cost savings by preventing major breakdowns and associated downtime.
- Safety Assurance:Reinforce the connection between routine maintenance and safety, as well-maintained cranes are less prone to malfunctions or accidents.
Daily, Weekly, and Monthly Inspection Checklists
- Daily Inspections:Visual Checks:Inspect for any visible signs of wear, damage, or abnormalities in the crane structure, cables, and hooks. Verify the functionality of emergency stop buttons and other critical safety features.
- Operational Tests:Conduct operational tests to ensure smooth movements and responsiveness of controls. Check for any unusual sounds or vibrations during crane operation.
- Weekly Inspections:Lubrication:Verify that all moving parts are adequately lubricated, addressing any dry or worn-out components. Inspect the condition of wire ropes and lubricate them as needed.
- Electrical Components:Check electrical components, including wiring and connections, for signs of wear or damage. Ensure that electrical panels are clean and free from debris.
- Monthly Inspections:Load Testing:Perform load testing to confirm that the crane can handle its rated capacity without issues. Document load test results and compare them with previous records for consistency.
- Structural Inspections:Inspect the structural integrity of the crane, focusing on welds, bolts, and other connections. Address any signs of corrosion or rust to prevent structural degradation.
Addressing Minor Issues Before They Escalate
- Proactive Approach:Encourage a proactive mindset among crane operators and maintenance personnel to address minor issues promptly.
- Documentation:Maintain detailed records of daily, weekly, and monthly inspections, noting any minor issues identified and the actions taken to resolve them.
- Training Programs:Provide ongoing training to crane operators on identifying and reporting minor issues during routine inspections.
- Collaboration with Maintenance Teams:Foster collaboration between crane operators and maintenance teams to ensure seamless communication and quick resolution of identified issues.
- Root Cause Analysis:Conduct root cause analyses for recurring minor issues to identify and address underlying problems.
Training and Certification
Operator Training Programs and Certifications- Formal Training Programs:Develop and implement formal training programs for crane operators, covering both theoretical and practical aspects of crane operation. Ensure that training programs align with industry standards and regulations.
- Simulation Exercises:Incorporate simulation exercises to provide hands-on experience in a controlled environment, allowing operators to practice various scenarios without real-world risks.
- Certification Requirements:Establish clear certification requirements for crane operators, ensuring that they meet the necessary skill and knowledge standards. Encourage operators to pursue relevant certifications from accredited organizations.
- Regular Assessments:Conduct regular assessments to evaluate the proficiency of crane operators and identify areas for improvement. Provide constructive feedback and additional training based on assessment results.
Continuous Education on New Technologies and Safety Practices
- Stay Updated on Technological Advancements:Facilitate ongoing education on new technologies related to crane operation, ensuring that operators are familiar with the latest features and improvements. Encourage operators to attend workshops, webinars, or industry conferences to stay informed.
- Safety Workshops and Training:Organize regular safety workshops focusing on new safety practices, regulations, and industry trends. Integrate safety training into continuous education programs to reinforce the importance of a safety-first mindset.
- Adaptation to Industry Changes:Emphasize the need for operators to adapt to changes in industry standards, regulations, and best practices. Provide resources and support to help operators integrate new knowledge into their daily operations.
Ensuring a Skilled and Knowledgeable Workforce
- Skills Development Programs:Implement skills development programs that go beyond basic operation, addressing advanced techniques, problem-solving, and critical decision-making skills. Foster a culture of continuous improvement and learning.
- Cross-Training Initiatives:Encourage cross-training among operators to enhance versatility and adaptability to different crane models or specialized tasks. Ensure that operators are proficient in various aspects of steel production crane operations.
- Knowledge Sharing:Facilitate knowledge-sharing sessions where experienced operators can share insights, best practices, and lessons learned with newer team members. Create a collaborative environment that values the expertise of each team member.
- Mentorship Programs:Establish mentorship programs where experienced operators mentor and guide newer members, facilitating knowledge transfer and skill development.
By prioritizing comprehensive training programs, continuous education, and the development of a skilled workforce, steel facilities can ensure that their crane operators are well-prepared to navigate the evolving landscape of the industry. In Part 12, we will conclude our comprehensive guide by summarizing key points and offering encouragement for ongoing learning and improvement in 35 ton overhead crane operations within the steel industry.
Custom 35 Ton Overhead Crane for Steel Mill Plants
In this comprehensive guide, we've explored the intricate world of operating 35 ton overhead cranes within the challenging landscape of the steel industry. As we conclude this guide, it is crucial to reiterate the centrality of safe and efficient crane operation in the steel industry. The proper functioning of 35 ton overhead cranes is not only essential for productivity but is also paramount for the safety of personnel and the integrity of valuable equipment. Operators and stakeholders alike must prioritize adherence to safety guidelines, industry standards, and best practices to ensure a secure and thriving working environment.
In a rapidly evolving industry, the pursuit of knowledge and continuous improvement is key to staying ahead. We encourage crane operators, maintenance teams, and steel industry professionals to embrace ongoing learning, stay updated on technological advancements, and actively seek opportunities for skill development. By fostering a culture of improvement, the steel industry can navigate challenges, optimize operations, and set the stage for a successful future.
Related 35 ton cranes and hoists projects for your reference:
35 Ton Double Girder Hoist | Crab Hoist For Sale Egypt
35 ton builtup hoist for your applications
35 ton / 5 Ton Electric Hoist Trolley 2 Hooks for Bangladesh