Overhead Crane 2 Ton for Engine Maintenance in Automotive Workshop
Overhead Crane 2 Ton for Engine Maintenance in Automotive Workshop
Overhead cranes designed for engine maintenance handle up to 2,000 kg, enhancing efficiency and safety in automotive workshops.Get your maintenance crane!
Overview of Engine Maintenance in Automotive Workshops
Importance of Efficient Engine Maintenance
In automotive workshops, efficient engine maintenance is crucial for ensuring vehicles operate smoothly and reliably. Regular maintenance and timely repairs help prevent breakdowns, extend the lifespan of engine components, and maintain vehicle performance. With engines becoming increasingly complex, the need for precise and safe handling of heavy engine parts has grown. Efficient engine maintenance minimizes downtime and enhances the productivity of automotive repair operations, making it essential for any workshop aiming to deliver high-quality service.
Role of Overhead Cranes in Automotive Repair
Overhead cranes play a pivotal role in automotive workshops by providing a safe and effective means to lift and maneuver heavy engine components. These cranes streamline the repair process, allowing technicians to handle large and cumbersome parts with ease. By using overhead cranes, workshops can improve operational efficiency, reduce physical strain on workers, and ensure precise placement of engine components during maintenance and assembly.
Purpose of Overhead Cranes in Engine Maintenance
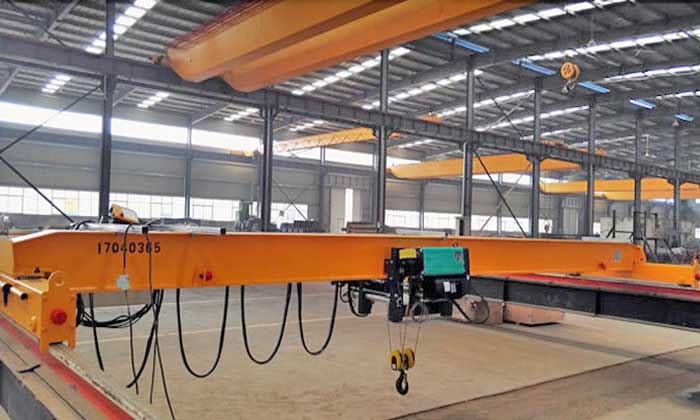
Benefits of Using Cranes for Heavy Engine Components
Overhead cranes are specifically designed to handle heavy engine components, which can weigh up to 2,000 kg. Their ability to lift and move such substantial loads significantly enhances the efficiency of engine maintenance tasks. The benefits include:
- Enhanced Safety: Reduces the risk of injury by eliminating the need for manual lifting of heavy parts.
- Improved Precision: Facilitates accurate placement and alignment of engine components.
- Increased Efficiency: Speeds up the maintenance process by allowing quick and easy repositioning of engine parts.
Overview of Load Handling Capabilities Up to 2,000 kg
Crane systems designed for automotive workshops can handle loads up to 2,000 kg, making them suitable for a wide range of engine components. This capability ensures that even the heaviest parts, such as engine blocks and transmissions, can be safely lifted and moved. Overhead cranes with this load capacity are equipped with robust hoists and lifting mechanisms to manage such heavy weights reliably, ensuring the smooth operation of maintenance tasks.
Key Features of Overhead Cranes for Engine Maintenance
Load Capacity and Strength
Typical Load Capacities for Engine Maintenance
Overhead cranes used in engine maintenance are designed to handle substantial loads, with typical capacities accommodating up to 2,000 kg. This load capacity is crucial for lifting and moving heavy engine components such as engine blocks, cylinder heads, and transmissions. Cranes with such capacities ensure that even the most cumbersome parts can be managed safely and efficiently, supporting the complex maintenance tasks in automotive workshops.
Design Considerations for Handling Up to 2,000 kg
To handle loads up to 2,000 kg, overhead cranes must be engineered with robust structural components and advanced lifting systems. Key design considerations include:
- Strengthened Hoisting Mechanisms: High-capacity hoists and winches are essential for lifting heavy components.
- Reinforced Structural Framework: The crane’s frame and supports need to be built with high-strength materials to bear the weight.
- Safety Features: Incorporating overload protection and stable base designs to prevent accidents and ensure safe lifting operations.
Span and Height Adjustments
Importance of Adjustable Spans and Heights
Adjustable spans and heights are critical features of overhead cranes, particularly in automotive workshops where space and component sizes vary. These adjustments allow the crane to be tailored to different workshop layouts and tasks, improving operational flexibility and efficiency.
- Span Adjustments: Allow the crane to cover a wider or narrower area, accommodating various workshop configurations and engine sizes.
- Height Adjustments: Enable the crane to reach different heights for lifting and positioning components, adapting to the specific requirements of engine maintenance tasks.
Custom Solutions for Workshop Dimensions
Customizing overhead cranes to fit specific workshop dimensions enhances their functionality and integration. Solutions include:
- Variable Span Options: Customizable spans that match the width of the workshop or the specific area of operation.
- Adjustable Lifting Heights: Tailored height adjustments to align with the height of engine components and maintenance stations.
- Compact Designs: Cranes designed to fit into smaller or constrained spaces while maintaining functionality and load capacity.
Material and Construction
Common Materials Used for Durability
Overhead cranes for engine maintenance are constructed from durable materials to withstand the demands of heavy lifting. Common materials include:
- Steel: Often used for the crane’s frame and structural components due to its high strength and durability.
- Alloy Materials: Employed for critical lifting parts and hoists to ensure reliability under heavy loads.
- Coatings and Treatments: Protective coatings are applied to prevent rust and wear, enhancing the crane's lifespan.
Features for Harsh Automotive Environments
Automotive workshops present challenging conditions, including exposure to oil, dirt, and other contaminants. Features designed to withstand these environments include:
- Corrosion-Resistant Finishes: Coatings and treatments to protect against rust and chemical damage.
- Sealed Bearings and Components: To prevent contamination from automotive fluids and debris.
- Durable Construction: Reinforced parts and high-quality materials to ensure the crane remains operational under harsh conditions.
Types of Overhead Cranes for Engine Maintenance
Single Girder Overhead Cranes
Advantages and Applications
Single girder overhead cranes are a popular choice for engine maintenance in automotive workshops due to their straightforward design and cost-effectiveness. These cranes feature a single main beam that supports the hoisting system, making them suitable for various tasks involving engine components.
- Cost-Effective: Generally less expensive than double girder cranes due to simpler construction.
- Compact Design: Ideal for workshops with limited space, providing efficient use of available overhead space.
- Ease of Installation: Simpler to install and maintain, making them a practical choice for many automotive repair environments.
Typical Load Handling Capabilities
Single girder cranes can handle moderate loads, typically up to 2,000 kg, which is sufficient for most engine maintenance tasks. They are designed to lift and move heavy engine parts efficiently, though their load capacity may be somewhat less than that of double girder cranes. This makes them suitable for standard engine maintenance needs in typical workshop settings.
Double Girder Overhead Cranes
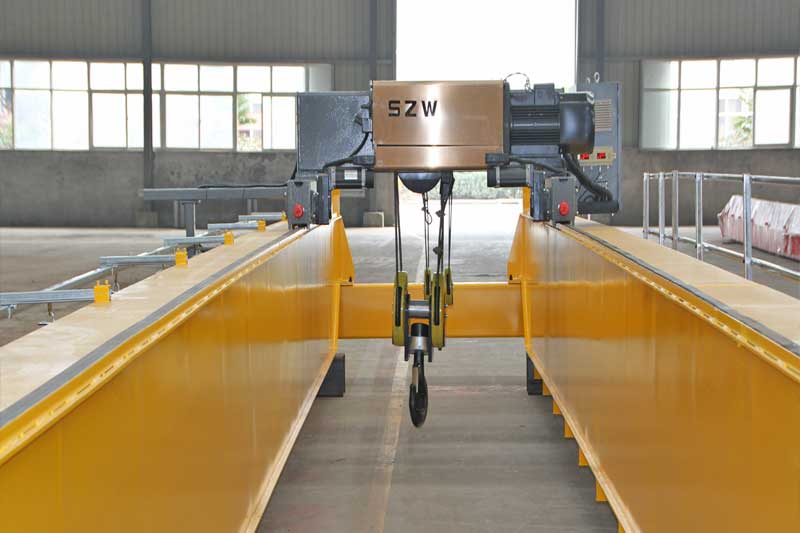
double girder overhead crane for heavy engine maintenance
Benefits for Heavy Engine Components
Double girder overhead cranes offer enhanced strength and stability, making them well-suited for handling heavy engine components. These cranes feature two main beams that support the hoisting system, providing greater load capacity and improved balance.
- Increased Capacity: Capable of handling heavier loads, often exceeding 2,000 kg, which is advantageous for large or complex engine components.
- Greater Stability: The dual girder design offers superior structural stability, reducing the risk of sway and improving precision during lifts.
- Enhanced Lifting Height: Typically allows for higher lifting heights, accommodating taller engine components and maintenance tasks.
Design Features for Increased Capacity
Double girder cranes are engineered with several design features to support their increased capacity:
- Reinforced Beams: Stronger main beams to support heavier loads.
- High-Capacity Hoists: Advanced hoisting mechanisms capable of handling greater weights.
- Robust Frame Construction: Enhanced structural integrity to ensure safe operation under heavy loads.
Jib Cranes
Applications in Confined Workshop Spaces
Jib cranes are particularly effective in confined workshop spaces where overhead clearance may be limited. Their design allows for flexible movement and precise positioning of engine components in tight areas.
- Space Efficiency: Ideal for workshops with limited overhead space, as they require less vertical clearance compared to traditional overhead cranes.
- Ease of Maneuverability: Allows for easy movement of engine parts in confined areas, improving accessibility and workflow.
- Cost-Effective Solution: Often more affordable than larger overhead crane systems, making them a practical choice for smaller or specialized maintenance tasks.
Flexibility and Load Handling Specifics
Jib cranes provide flexibility in load handling, allowing for a range of movements and adjustments:
- Rotational Movement: Offers 360-degree rotation within its reach, enabling precise placement of engine components.
- Adjustable Reach: Can be customized with different arm lengths to suit various engine sizes and workshop layouts.
- Load Handling: Typically supports lighter loads compared to overhead cranes, but still effective for handling most engine components within its capacity range.
Installation and Operation Considerations
Installation Requirements
Site Preparation and Space Considerations
Proper installation of overhead cranes for engine maintenance begins with careful site preparation and planning. Key considerations include:
- Workshop Layout: Ensure there is adequate overhead space and clearance for crane operation. Measure the workshop dimensions to determine the suitable crane type and span.
- Structural Support: Verify that the workshop’s structure can support the crane’s weight and operational forces. Reinforce or modify existing structures if needed.
- Accessibility: Plan for crane access routes for delivery, installation, and future maintenance. Clear pathways should be maintained to facilitate crane operation and movement of heavy components.
Professional Installation and Calibration
To ensure optimal performance and safety, professional installation and calibration are essential:
- Qualified Technicians: Employ experienced technicians to install the crane, as improper installation can lead to operational issues and safety hazards.
- Alignment and Calibration: Ensure that the crane is properly aligned and calibrated according to manufacturer specifications to guarantee accurate and smooth operation.
- Safety Inspections: Conduct thorough safety inspections post-installation to identify and address any potential issues before the crane is put into service.
Operational Best Practices
Safe Operating Procedures
Adhering to safe operating procedures is crucial for effective and accident-free crane operation:
- Operator Training: Ensure that all crane operators are trained and certified in safe crane operation techniques. Training should cover load handling, emergency procedures, and safety protocols.
- Load Limits: Never exceed the crane’s rated load capacity. Overloading can compromise the crane’s stability and safety.
- Pre-Operation Checks: Perform routine pre-operation checks to verify that all crane components are functioning correctly and that safety devices are in place.
Maintenance and Inspection Routines
Regular maintenance and inspections are vital to keep the crane in good working condition and to prevent unexpected failures:
- Routine Maintenance: Follow the manufacturer’s maintenance schedule, including lubrication, part replacements, and adjustments. Regular maintenance helps extend the crane’s lifespan and ensures reliable performance.
- Periodic Inspections: Conduct periodic inspections to assess the crane’s condition. Look for signs of wear, corrosion, or structural damage and address issues promptly.
- Record Keeping: Maintain detailed records of maintenance activities, inspections, and repairs to track the crane’s history and ensure compliance with safety regulations.
Case Studies and Examples
Automotive Workshops Using Overhead Cranes
Examples of Successful Implementations
Overhead cranes have been successfully integrated into various automotive workshops to enhance engine maintenance processes. Some notable examples include:
-
Example 1: Large Automotive Repair Facility
A major automotive repair facility implemented double girder overhead cranes to handle heavy engine blocks and transmissions. The cranes were equipped with high-capacity hoists and adjustable spans to accommodate the workshop’s layout and various engine sizes. The successful integration of these cranes improved the efficiency of engine removal and installation, reduced manual handling injuries, and allowed for quicker turnaround times on repairs. -
Example 2: Specialty Engine Maintenance Workshop
A specialty workshop focusing on high-performance engines used single girder overhead cranes with custom height adjustments. These cranes facilitated precise placement of delicate engine components and streamlined the assembly process. The customized cranes enabled the workshop to manage complex engine builds more efficiently, leading to enhanced productivity and reduced downtime.
Benefits Realized in Real-World Settings
The use of overhead cranes in automotive workshops has led to several tangible benefits:
- Enhanced Efficiency: Cranes enable faster and more accurate handling of engine components, reducing overall maintenance time.
- Improved Safety: Automated lifting reduces the risk of manual handling injuries and enhances worker safety.
- Increased Capacity: Workshops can handle a higher volume of maintenance tasks due to the efficiency and effectiveness of crane operations.
Comparative Analysis
Performance of Different Crane Types in Engine Maintenance
A comparative analysis of different crane types reveals how each performs in engine maintenance:
- Single Girder Overhead Cranes: Best suited for workshops with limited space and moderate load requirements. They provide cost-effective solutions but may have lower load capacities compared to double girder cranes.
- Double Girder Overhead Cranes: Ideal for handling heavier engine components and offering greater stability and lifting height. These cranes are more suitable for larger workshops with high-capacity needs.
- Jib Cranes: Excellent for confined spaces and precise positioning. While they may handle lighter loads compared to overhead cranes, their flexibility makes them valuable for specialized engine maintenance tasks.
Lessons Learned and Best Practices
From various case studies, several lessons and best practices have emerged:
- Customization is Key: Tailoring crane features to specific workshop needs ensures optimal performance and efficiency.
- Regular Maintenance is Essential: Consistent upkeep and inspections prevent downtime and maintain crane reliability.
- Operator Training: Investing in comprehensive training for crane operators improves safety and operational efficiency.
- Space Planning: Proper site preparation and crane placement are crucial for maximizing functionality and safety in the workshop environment.
Conclusion
Overhead cranes play a crucial role in automotive engine maintenance, providing significant advantages for handling heavy and complex engine components. Key features of these cranes include:
- Load Capacity: Cranes with capacities up to 2,000 kg effectively manage heavy engine parts, enhancing workshop efficiency.
- Adjustability: Features such as adjustable spans and heights ensure cranes can be customized to fit various workshop layouts and tasks.
- Material Durability: Constructed from high-strength materials, these cranes are designed to withstand harsh automotive environments and ensure long-term reliability.
The benefits of using overhead cranes in engine maintenance include improved operational efficiency, enhanced safety, and increased productivity. Selecting the appropriate crane type—whether single girder, double girder, or jib crane—based on specific workshop needs is essential for optimizing these benefits.
Importance of Choosing the Right Crane for Specific Needs
Choosing the right overhead crane is critical to meeting the unique demands of engine maintenance. The correct crane ensures:
- Optimal Performance: Tailoring crane features to specific tasks and workshop dimensions maximizes efficiency and safety.
- Enhanced Safety: Properly matched cranes help prevent accidents and reduce the risk of damage to both components and personnel.
- Cost-Effectiveness: Selecting the appropriate crane can lead to significant savings in terms of maintenance costs and operational downtime.
Potential Advancements in Crane Capabilities and Design
Future advancements are expected to further improve crane capabilities and design:
- Increased Load Capacities: Innovations in materials and engineering may enable cranes to handle even heavier loads with greater stability.
- Customizable Designs: More flexible and adaptable crane designs to meet a wider range of workshop environments and specific maintenance tasks.
- Eco-Friendly Solutions: Development of energy-efficient and environmentally friendly crane systems to reduce operational impact and costs.
As technology progresses, the future of overhead cranes will likely bring about significant enhancements in their functionality, safety, and efficiency, further benefiting automotive workshops and other industrial applications.