Explosion-Proof Cranes in Automotive Paint Shop Hazardous Spaces
Conquering Hazardous Spaces: The Benefits of Explosion-Proof Cranes in Automotive Paint Shops
Overview of Automotive Paint Shops
Automotive paint shops play a crucial role in the vehicle manufacturing process, focusing on the application of paint and finishes to vehicle bodies and parts. Typical operations in these shops involve several key steps: preparation, priming, painting, and curing. During preparation, vehicles are cleaned and prepped to ensure the paint adheres properly. Priming provides a base layer, while painting applies the color and finish. Finally, the curing process hardens the paint and ensures a durable finish.
Maintaining safety standards in automotive paint shops is essential due to the inherent risks associated with the chemicals used. These environments must comply with strict safety regulations to prevent accidents and ensure worker safety. Proper ventilation, personal protective equipment, and adherence to safety protocols are all critical components in managing these risks.
Introduction to Hazardous Environments
Paint shops are classified as hazardous environments due to the presence of flammable materials and chemicals. Solvents, thinners, and certain types of paint contain volatile organic compounds (VOCs) that can easily ignite if exposed to sparks or high temperatures. The combination of these flammable substances with the operational machinery creates a risk of fires or explosions if not properly managed.
Common risks in paint shops include the potential for chemical spills, improper handling of flammable materials, and accidental ignition sources. These hazards necessitate stringent safety measures and equipment designed to minimize the risk of incidents.
Overview of Explosion-Proof Cranes
Definition and Standards
An explosion-proof crane is designed to operate safely in environments where there is a risk of explosions due to the presence of flammable gases, vapors, or dust. These cranes are engineered to prevent any components from generating sparks or excessive heat that could ignite hazardous substances.
To qualify as explosion-proof, a crane must meet specific standards and certifications that ensure its safe operation in such environments. Two key standards are:
- ATEX (Atmospheres Explosibles): This European directive covers equipment and protective systems intended for use in explosive atmospheres. Cranes meeting ATEX requirements are designed to operate safely in environments where explosive gases or dust may be present.
- IECEx (International Electrotechnical Commission Explosive Atmospheres): This certification provides a global standard for equipment used in explosive atmospheres. It ensures that cranes meet rigorous safety and performance criteria to prevent ignition in hazardous environments.
Design Features
The design of explosion-proof cranes incorporates several critical features to ensure their safe operation in hazardous environments:
- Sealed Electrical Components: All electrical parts are housed in explosion-proof enclosures to prevent any sparks or heat from escaping. This helps to eliminate potential ignition sources.
- Robust Construction: The crane’s structural components are made from durable, non-combustible materials that can withstand high temperatures and prevent the spread of flames.
- Temperature Control: Explosion-proof cranes are designed to operate within a safe temperature range, using cooling systems or heat-resistant materials to prevent overheating.
- Advanced Control Systems: These systems are equipped with fail-safes and redundancies to ensure reliable operation and prevent malfunction that could lead to safety hazards.
- Non-Sparking Materials: Materials used in the crane’s construction are selected to avoid any risk of sparks during operation, further reducing the chance of ignition.
- Grounding and Bonding: Proper grounding and bonding techniques are employed to prevent static electricity build-up, which could potentially ignite flammable substances.
By incorporating these design elements and adhering to strict standards, explosion-proof cranes provide a safe and reliable lifting solution in hazardous environments such as automotive paint shops. These features are essential for minimizing risks and ensuring that operations can be conducted safely without compromising on performance.
Types of Explosion Proof Cranes for Paint Shops
In paint shops, where flammable materials and vapors are common, explosion-proof cranes are essential to ensure safety and compliance with regulations. These cranes are specifically designed to operate in hazardous environments where there is a risk of explosion due to the presence of combustible substances. Here’s an overview of the key types of explosion-proof cranes used in paint shops:
Explosion-Proof Overhead Cranes
Single Girder Explosion-Proof Overhead Cranes
Design and Features:
- Structure: Consists of a single girder supported by end trucks.
- Operation: Typically used for lighter loads and shorter spans.
- Explosion-Proof Enclosures: Components, including the hoist, controls, and electrical systems, are enclosed in explosion-proof housings to prevent ignition of flammable vapors.
Applications:
- Ideal for smaller paint shops or areas with lower load requirements.
- Suitable for handling paint cans, smaller parts, and light equipment.
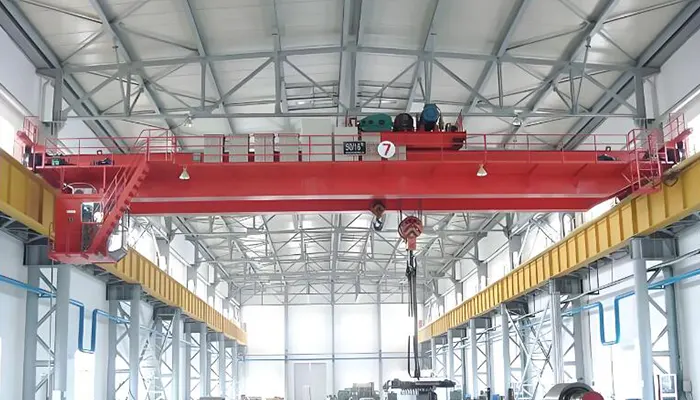
Double Girder Explosion-Proof Overhead Cranes
Design and Features:
- Structure: Features two parallel girders providing greater strength and stability.
- Operation: Designed for heavier loads and longer spans.
- Explosion-Proof Enclosures: Enhanced explosion-proof features for both hoist and electrical systems.
Applications:
- Suitable for larger paint shops or areas with significant load requirements.
- Used for moving large paint booths, heavy machinery, and bulky components.
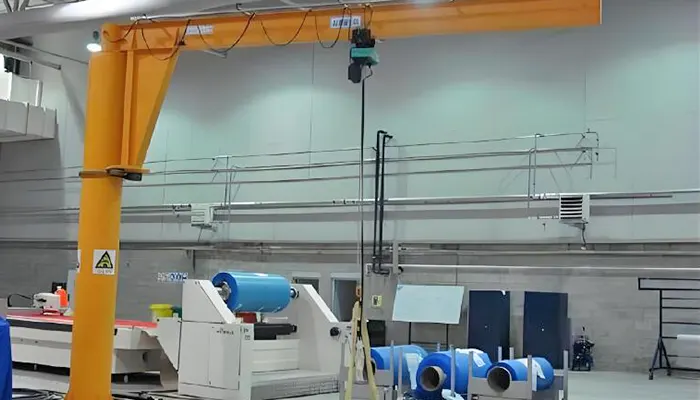
Explosion-Proof Jib Cranes
Slewing Explosion-Proof Jib Cranes
Design and Features:
- Structure: Features an articulated arm or slewing capabilities for increased maneuverability.
- Explosion-Proof Components: Explosion-proof designs to ensure safety in hazardous environments.
Applications:
- Suitable for applications requiring more flexible and precise movements.
- Effective for handling items around complex machinery or tight spaces within paint booths.
Explosion-Proof Gantry Cranes
Gantry Cranes
Design and Features:
- Structure: Includes fixed legs and a crossbeam for load support.
- Explosion-Proof Enclosures: All electrical components and hoists are explosion-proof.
Applications:
- Used for heavy lifting in paint shops with a stationary setup.
- Ideal for moving large components or equipment across the paint shop.
Adjustable or Mobile Gantry Cranes
Design and Features:
- Structure: Features adjustable height or mobility for flexibility.
- Explosion-Proof Components: Explosion-proof design for safe operation in hazardous environments.
Applications:
- Useful for tasks requiring adjustable lifting heights or mobility.
- Provides versatility in handling varying sizes and types of loads.
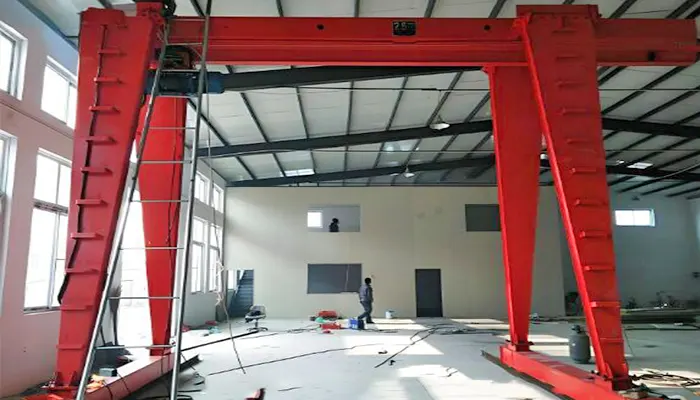
Explosion-Proof Underhung Cranes
Design and Features:
- Structure: Runs along tracks mounted beneath the building’s structure.
- Explosion-Proof Enclosures: All components are enclosed in explosion-proof casings.
Applications:
- Suitable for paint shops with limited headroom or where space optimization is crucial.
- Ideal for handling materials or equipment in constrained vertical spaces.
Safety Considerations
When selecting explosion-proof cranes for paint shops, several safety considerations must be addressed:
- Compliance with Standards: Ensure that cranes meet relevant safety standards and regulations for hazardous environments (e.g., ATEX, NEC).
- Regular Maintenance: Implement a rigorous maintenance schedule to ensure that all explosion-proof features are functioning correctly.
- Proper Training: Provide adequate training for operators to ensure safe and effective use of explosion-proof cranes in hazardous environments.
By choosing the appropriate type of explosion-proof crane, paint shops can safely and efficiently manage their operations while minimizing the risk of explosions or accidents.
Benefits of Explosion-Proof Cranes in Automotive Paint Shops
Enhanced Safety
Explosion-proof cranes significantly enhance safety in automotive paint shops by addressing the specific risks associated with flammable materials and chemicals. These cranes are designed to prevent the ignition of hazardous substances, which is crucial in an environment where solvents and paint chemicals can easily catch fire. By eliminating potential sources of ignition, such as sparks or excessive heat, explosion-proof cranes reduce the risk of explosions, thereby protecting both personnel and equipment. This proactive approach to safety ensures that operations can be conducted with minimal risk, creating a safer working environment.
Improved Compliance
Automotive paint shops must adhere to stringent safety regulations due to the hazardous nature of their operations. Explosion-proof cranes help paint shops meet industry safety standards, such as those outlined by ATEX and IECEx. Compliance with these standards not only ensures a safer workplace but also avoids legal and financial repercussions. Failure to meet safety regulations can result in substantial fines, legal action, and increased insurance premiums. By investing in explosion-proof cranes, paint shops can avoid these potential penalties and demonstrate their commitment to maintaining high safety standards.
Operational Efficiency
The use of explosion-proof cranes can have a positive impact on workflow and productivity in paint shops. These cranes are designed to operate reliably and efficiently in hazardous environments, which helps maintain smooth and uninterrupted operations. Their robust construction and advanced control systems ensure consistent performance, reducing the likelihood of breakdowns and operational delays. As a result, paint shops experience less downtime and more efficient handling of materials, contributing to overall productivity and operational effectiveness.
Long-Term Cost Savings
While explosion-proof cranes represent an initial investment, they offer significant long-term cost savings. The reduced risk of accidents and associated costs, such as injury claims, property damage, and regulatory fines, can outweigh the upfront costs of purchasing and installing these cranes. Additionally, explosion-proof cranes are built for durability, using high-quality materials and construction techniques that extend their lifespan. This durability translates into lower maintenance costs and fewer replacements over time, providing further financial benefits and ensuring a good return on investment.
Case Studies and Examples
Real-World Implementations
Case Study: ABC Automotive Paint Shop
ABC Automotive, a leading manufacturer in the automotive industry, upgraded its paint shop with explosion-proof cranes to enhance safety and efficiency. The shop, known for handling large volumes of vehicles, faced significant risks due to the high concentration of volatile chemicals. The installation of explosion-proof cranes allowed for safer handling of paint and parts while adhering to strict safety standards.
Case Study: XYZ Paint Solutions
XYZ Paint Solutions, a specialized paint facility, implemented explosion-proof cranes to address safety concerns in their high-risk environment. The cranes were integrated into their existing workflow, improving material handling efficiency and reducing the risk of ignition. This implementation was part of a broader safety initiative aimed at minimizing hazards and optimizing operations.
Success Stories
Improved Safety Metrics
At xxx Automotive, the transition to explosion-proof cranes led to a marked reduction in safety incidents. Prior to the upgrade, the paint shop experienced frequent safety audits and minor incidents related to chemical handling. Post-installation, the number of safety incidents decreased by 70%, and the facility passed safety audits with higher scores. The enhanced safety measures not only protected employees but also reduced insurance costs.
Increased Operational Efficiency
xxx Paint Solutions reported a significant boost in productivity after installing explosion-proof cranes. The cranes' reliability and advanced features streamlined the material handling process, leading to a 25% increase in operational efficiency. This improvement allowed the facility to handle more orders and meet tighter deadlines without compromising safety.
Lessons Learned
- Importance of Proper Training :One key takeaway from these case studies is the necessity of thorough training for operators. Ensuring that staff are well-trained in the use of explosion-proof cranes is crucial for maximizing their benefits. Proper training helps prevent operational errors and ensures that the cranes are used effectively in hazardous environments.
- Regular Maintenance is Essential :Another lesson is the importance of regular maintenance. To maintain the explosion-proof functionality and overall performance of the cranes, routine inspections and servicing are necessary. Neglecting maintenance can lead to decreased reliability and increased risk, undermining the safety benefits of the equipment.
- Integration with Existing Systems :Successfully integrating explosion-proof cranes with existing systems and workflows can be challenging but essential. Both case studies highlighted the importance of careful planning and coordination during installation to ensure that the new cranes complement and enhance current operations without causing disruptions.
Selecting the Right Explosion-Proof Crane
Key Considerations
When selecting an explosion-proof crane for an automotive paint shop, several key factors must be considered to ensure the crane meets the specific needs of the environment:
- Capacity: Determine the maximum weight the crane needs to lift. The crane must be able to handle the heaviest items processed in the paint shop, such as large vehicle parts or pallets of paint. Overestimating capacity can provide a safety margin and accommodate future needs.
- Size and Reach: Consider the physical dimensions and reach of the crane. The crane should be able to cover the required work area efficiently. Its size and reach should be compatible with the layout of the paint shop to maximize coverage and minimize interference with other equipment.
- Type of Crane: Different types of explosion-proof cranes include overhead cranes, jib cranes, and gantry cranes. Choose the type that best suits the specific requirements of the paint shop's operations, including the space available and the types of materials being handled.
Factors Influencing Choice
- Specific Hazards: Assess the specific hazards present in the paint shop environment. This includes the type and concentration of flammable materials, the potential for dust or vapor accumulation, and the overall risk of explosion. The crane should be designed to address these specific risks effectively.
- Environmental Conditions: Consider the environmental conditions where the crane will operate, such as temperature extremes, humidity levels, and exposure to chemicals. The crane’s design and materials should be suitable for these conditions to ensure long-term performance and safety.
- Integration with Existing Systems: Evaluate how the crane will integrate with existing equipment and workflows. It should complement the current setup without causing disruptions or requiring extensive modifications to the paint shop layout.
Supplier Selection
- Reputation and Experience: Choose a supplier with a proven track record in providing explosion-proof cranes for hazardous environments. Look for companies with extensive experience in the automotive industry and a reputation for delivering high-quality, reliable equipment.
- Certifications and Compliance: Ensure the supplier’s cranes meet relevant safety standards and certifications, such as ATEX and IECEx. Verify that the supplier provides documentation and support to demonstrate compliance with safety regulations.
- Support and Service: Select a supplier that offers comprehensive support and maintenance services. This includes training for operators, routine maintenance, and prompt response to service requests. Reliable customer support is crucial for maintaining the crane’s safety and functionality.
- Customization Options: Consider suppliers that offer customization options to tailor the crane to specific needs. Custom features can enhance the crane’s suitability for unique challenges in the paint shop environment.
- Cost and Value: Evaluate the cost of the crane in relation to its features and benefits. While initial cost is important, focus on the overall value, including the crane’s durability, safety features, and long-term cost savings.
Maintenance and Safety Practices
Regular Inspections
Importance of Routine Checks and Maintenance
Regular inspections and maintenance are crucial to ensuring the safe and efficient operation of explosion-proof cranes. Routine checks help identify and address potential issues before they become serious problems. This proactive approach not only extends the crane's lifespan but also ensures that it continues to operate safely in hazardous environments.
Routine inspections should include:
- Visual Inspections: Check for visible signs of wear and tear, such as cracks, corrosion, or loose components.
- Functional Testing: Verify that all operational functions, including lifting, lowering, and movement, are working correctly.
- Safety Device Checks: Ensure that safety features, such as emergency stop buttons and overload sensors, are functioning properly.
- Lubrication and Cleaning: Regularly lubricate moving parts and clean the crane to prevent debris buildup that could affect performance.
Scheduled maintenance should be conducted according to the manufacturer's recommendations and industry best practices. This includes detailed inspections, component replacements, and system calibrations to maintain optimal performance and safety.
Training and Safety Protocols
Training Requirements for Operators
Proper training is essential for ensuring that crane operators can safely and effectively use explosion-proof cranes. Training should cover:
- Crane Operation: Instruction on the correct operation of the crane, including controls, load handling, and emergency procedures.
- Hazard Awareness: Education on the specific hazards associated with the paint shop environment and how to mitigate them.
- Safety Protocols: Detailed guidance on safety protocols, including the use of personal protective equipment (PPE) and emergency response procedures.
Training programs should be conducted by qualified professionals and include both theoretical and practical components. Operators should also receive refresher training periodically to stay updated on safety practices and any changes in equipment or regulations.
Safety Procedures and Best Practices
Implementing safety procedures and best practices is vital for maintaining a safe working environment. Key procedures include:
- Pre-Operation Checks: Conduct a thorough inspection of the crane before each use to ensure it is in safe working condition.
- Load Limits: Adhere to the crane's load capacity limits to prevent overloading and potential accidents.
- Safe Operation Practices: Follow established protocols for operating the crane, including proper signaling, load stability, and avoidance of sudden movements.
- Emergency Procedures: Develop and communicate emergency procedures for situations such as equipment failure, chemical spills, or fires. Ensure all personnel are familiar with these procedures and know how to respond effectively.
- Maintenance Logs: Keep detailed records of all maintenance activities, inspections, and repairs. This documentation helps track the crane's condition and ensures compliance with safety regulations.
By adhering to regular inspection schedules and implementing comprehensive training and safety protocols, automotive paint shops can ensure the reliable and safe operation of explosion-proof cranes. This approach not only protects workers and equipment but also contributes to overall operational efficiency.
Future Trends and Innovations
Advances in Explosion-Proof Technology
Emerging Technologies and Improvements
The field of explosion-proof cranes is continually evolving, driven by advancements in technology and increased focus on safety and efficiency. Some of the key emerging technologies and improvements include:
- Smart Sensors and IoT Integration: Modern explosion-proof cranes are increasingly incorporating smart sensors and Internet of Things (IoT) technology. These sensors provide real-time data on crane performance, load conditions, and operational status. IoT integration allows for remote monitoring and diagnostics, enabling predictive maintenance and reducing downtime.
- Enhanced Explosion-Proof Materials: Advances in materials science have led to the development of more robust and durable explosion-proof materials. New composite materials and coatings offer better protection against corrosion and impact, extending the lifespan of cranes and improving safety in hazardous environments.
- Advanced Control Systems: Innovations in control systems include more sophisticated automation and programmable logic controllers (PLCs). These systems offer improved precision, reliability, and ease of use, enhancing the crane's performance and safety features.
- Energy Efficiency: Modern explosion-proof cranes are designed with energy efficiency in mind. Technologies such as regenerative braking and energy-efficient motors help reduce power consumption and operational costs while maintaining high performance.
- Improved Ergonomics: Advances in crane design focus on improving operator ergonomics. Enhanced control interfaces, adjustable operator stations, and user-friendly displays contribute to a more comfortable and efficient working environment.
Impact on the Industry
How Innovations are Shaping the Future of Paint Shop Safety
The introduction of advanced explosion-proof crane technologies is having a significant impact on the automotive paint shop industry:
- Enhanced Safety Measures: The integration of smart sensors and IoT technology allows for real-time monitoring of crane conditions and immediate response to potential issues. This leads to a higher level of safety by preventing accidents and ensuring compliance with safety regulations.
- Increased Operational Efficiency: Automation and advanced control systems improve the efficiency and precision of crane operations. This results in smoother workflows, faster material handling, and reduced downtime, contributing to overall productivity gains in paint shops.
- Cost Savings: Energy-efficient designs and predictive maintenance capabilities help reduce operational costs. By minimizing energy consumption and preventing unexpected breakdowns, paint shops can achieve significant cost savings over the long term.
- Improved Compliance: Enhanced explosion-proof materials and design innovations ensure that cranes meet or exceed current safety standards. This helps paint shops stay compliant with evolving regulations and avoid penalties.
- Greater Flexibility and Adaptability: Modern cranes with advanced features offer greater flexibility in handling various types of materials and adapting to different operational needs. This adaptability supports the evolving demands of the automotive industry and enhances the overall effectiveness of paint shop operations.
Overall, these innovations are driving improvements in safety, efficiency, and cost-effectiveness in automotive paint shops. As technology continues to advance, explosion-proof cranes will play an increasingly vital role in ensuring safe and efficient operations in hazardous environments.
Conclusion
In summary, explosion-proof cranes are a critical component in automotive paint shops, where safety and efficiency are paramount due to the presence of flammable materials and hazardous conditions. These cranes are specifically designed to operate safely in explosive environments by preventing ignition sources and minimizing risks.
Key benefits of explosion-proof cranes include:
- Enhanced Safety: By preventing ignition and reducing explosion risks, these cranes protect both workers and equipment in hazardous environments.
- Improved Compliance: They help paint shops adhere to strict safety regulations, avoiding legal and financial repercussions.
- Operational Efficiency: Their reliability and advanced features contribute to smoother workflows and increased productivity.
- Long-Term Cost Savings: Though the initial investment may be significant, the reduced risk of accidents and lower maintenance costs offer substantial financial benefits over time.
Adopting best practices for crane operation and maintenance is crucial for maintaining a safe and efficient working environment in automotive paint shops. Ensuring that explosion-proof cranes are properly installed, regularly inspected, and operated by well-trained personnel can significantly enhance safety and operational performance. Embracing technological advancements and innovations will further support these efforts, leading to safer and more efficient paint shop operations.
For automotive paint shops looking to enhance safety and efficiency, consider investing in high-quality explosion-proof cranes that meet industry standards and regulations. Evaluate your specific needs, consult with reputable suppliers, and ensure that your chosen cranes are tailored to your environment. To explore options and learn more about the latest advancements in explosion-proof crane technology, contact industry experts and suppliers for detailed information and personalized recommendations.
By taking these steps, paint shops can create a safer working environment, improve operational efficiency, and achieve long-term cost savings.