Coil handling Overhead Cranes 5 to15 tons in Automotive Body Shop
Coil handling Overhead Cranes 5 to15 Tons in Automotive Body Shop
5 ton to 15 ton overhead crane for automotive-grade Steel Coils handling to ensure precise manufacturing of automotive body components in automotive shop.
In automotive manufacturing, precision and efficiency are paramount. single girder and double girder overhead cranes, a cornerstone in material handling, play a pivotal role in streamlining operations within automotive body shops. These cranes are characterized by a single horizontal beam – the girder – and are meticulously designed to navigate heavy loads with finesse.
The heartbeat of any automotive body shop lies in its ability to seamlessly handle materials, especially when dealing with coils. Overhead cranes provide a sophisticated solution, allowing for precise movement and placement of materials throughout the manufacturing process. Their significance is underscored by the enhanced productivity, reduced labor intensity, and improved safety they bring to the intricate dance of automotive assembly.
Within the spectrum of overhead cranes, the 5 to 15 tons capacity range stands out as an ideal choice for automotive body shops engaged in coil handling. This range strikes a delicate balance between robust strength and intricate control, making it a go to solution for the demanding task of transporting and maneuvering heavy coils.
Overview of single girder and double girder overhead cranes
The single girder design, characterized by its singular horizontal beam, provides a host of benefits tailored to the demands of automotive body shops. The streamlined structure ensures a more straightforward and economical solution, without compromising on strength or precision. This design choice maximizes the crane's lifting capacity, making it an ideal companion for handling substantial loads within the confined spaces of a manufacturing facility.
Components of Overhead Cranes
- Girder: Serving as the backbone of the crane, the girder bears the weight of the entire system. Constructed from high strength steel, it provides the structural integrity needed to handle heavy loads while maintaining a lightweight and efficient profile.
- Hoist: The hoist is the workhorse of the crane, responsible for lifting, lowering, and positioning loads. In the context of automotive body shops, where precision is paramount, modern hoists are equipped with advanced features such as variable speed controls and precise positioning capabilities.
- End Trucks: Mounted on either end of the girder, end trucks house the wheels that facilitate horizontal movement along the crane's runway. The design of these end trucks is crucial, allowing for smooth and controlled traversing of the crane, ensuring precise placement of materials during the manufacturing process.
- Electrical Components: The electrical system of a single girder overhead crane is the nerve center of its operation. From control panels to sensors and safety mechanisms, these components work in harmony to provide operators with seamless control and ensure the safety of both personnel and materials being handled.
Advantages of Single Girder Cranes in Automotive Body Shops
- Lower Profile: The single girder design allows for a lower profile, making these cranes well suited for facilities with space constraints. This characteristic ensures optimal use of the available vertical space without compromising on performance.
- Ease of Installation: Single girder cranes are known for their relatively simple installation process. This minimizes downtime during setup, allowing automotive body shops to swiftly integrate these cranes into their operations and reap the benefits without prolonged disruptions.
- Cost Effectiveness: The economic advantages of single girder cranes make them an attractive choice for automotive body shops. With lower material and installation costs compared to their double girder counterparts, these cranes provide a compelling return on investment.
- Adaptability: Automotive body shops often require flexibility in their material handling equipment. Single girder cranes excel in adapting to various working environments, making them suitable for the dynamic demands of an automotive manufacturing facility.
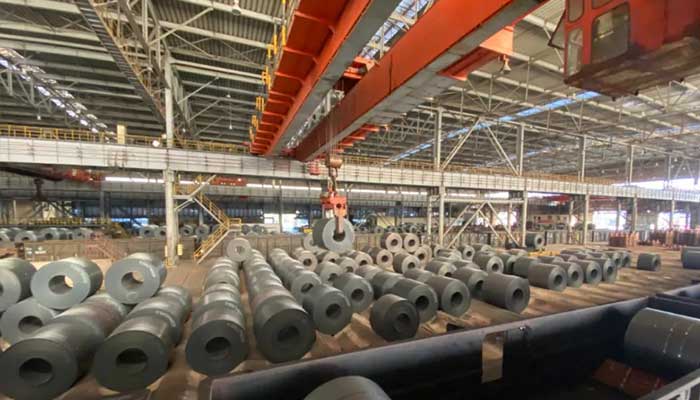
Significance of Coil Handling in Automotive Body Shops
In automotive manufacturing, coil handling refers to the process of transporting, manipulating, and positioning coiled materials – typically steel or aluminum coils – within a manufacturing facility. Coils, often weighing several tons, serve as fundamental raw materials in the creation of automotive components.
The importance of effective coil handling cannot be overstated in the realm of automotive manufacturing. Coils are the foundational building blocks for a variety of components, ranging from car body panels to intricate parts used in the assembly process. Efficient handling ensures a smooth workflow, aiding in timely production and maintaining the high standards expected in the automotive industry.
Challenges in Coil Handling Without Proper Equipment
The challenges inherent in coil handling become pronounced when proper equipment is lacking. Without the aid of specialized machinery, such as the 5 to 15 tons single girder and double girder overhead cranes we previously discussed, several challenges emerge:
- Safety Concerns: Manually handling heavy coils poses a significant risk to personnel. Accidents, injuries, and strain related issues become prevalent in the absence of proper material handling equipment.
- Inefficiency and Downtime: Manual handling not only jeopardizes safety but also leads to inefficiencies and increased downtime. The slow and labor intensive nature of manual coil handling hampers the overall production process, affecting timelines and output.
- Material Damage: Coils are sensitive materials, and mishandling can result in damage. Scratches, dents, or deformation of coils can compromise the quality of the final automotive components, leading to increased waste and additional costs.
- Limited Precision and Control: Precision is crucial in automotive manufacturing, and without specialized equipment, achieving accurate coil placement becomes challenging. This lack of control can hinder the manufacturing process and lead to errors in the assembly line.
- Reduced Productivity: The manual handling of coils is inherently slower compared to mechanized alternatives. This reduction in productivity not only impacts output but also affects the overall competitiveness of an automotive body shop in the industry.
Characteristics of 5 to 15 Tons single girder and double girder overhead cranes
Load Capacity Considerations
The 5 to 15 tons capacity range of single girder and double girder overhead cranes is meticulously engineered to address the specific demands of automotive body shops. This load capacity strikes an optimal balance, offering the strength needed for handling substantial coils while ensuring precise control over the material.
Span Length and Coverage
The span length and coverage of these cranes are designed with versatility in mind. The configuration allows them to efficiently cover the workspace within automotive body shops, providing seamless access to various manufacturing areas. This adaptability is essential for accommodating the dynamic layout of modern production facilities.
Hoisting Speed and Precision
Speed and precision are paramount in automotive manufacturing. The 5 to 15 tons single girder and double girder overhead cranes are equipped with advanced hoisting mechanisms that combine speed with accuracy. This ensures swift and precise positioning of coils, contributing to enhanced efficiency in the assembly process.
Safety Features
- Emergency Stop: An integral safety feature, the emergency stop mechanism allows for immediate halting of crane operations in critical situations. This ensures swift response to unforeseen events, minimizing the risk of accidents.
- Overload Protection: To safeguard both personnel and materials, these cranes are equipped with overload protection systems. This feature automatically halts operations when the load exceeds the crane's rated capacity, preventing potential accidents and material damage.
- Limit Switches: Limit switches contribute to operational safety by defining the maximum and minimum travel limits of the crane. This prevents collisions, ensuring that the crane operates within predefined parameters, reducing the risk of accidents and damage to the equipment.
Customization Options
Recognizing the diverse needs of automotive body shops, manufacturers offer customization options for these cranes. Tailoring the crane to specific requirements may involve modifications in terms of:
- Control Systems: Advanced control interfaces, including radio remote controls or cabin operated systems, can be tailored to the operator's preferences.
- Additional Features: Integration of specialized features such as camera systems for enhanced visibility during operations or automation options to optimize workflow efficiency.
In Part V, we will delve into the practical applications of 5 to 15 tons single girder and double girder overhead cranes in automotive body shops, exploring how they streamline processes, enhance productivity, and contribute to the overall success of manufacturing operations.
C hook overhead crane for coil handling
Application in Automotive Body Shops
Coil Unloading and Loading
The 5 to 15 tons single girder and double girder overhead cranes shine in the critical task of coil unloading and loading. Their robust load capacity and precision control make them ideal for lifting heavy coils from delivery trucks and placing them precisely in the designated processing areas. This not only ensures the safety of personnel but also minimizes the risk of damage to the sensitive coil materials.
Material Transportation within the Shop
Efficient material transportation is the backbone of any automotive body shop. These cranes facilitate seamless movement of coils within the facility. Their span length and coverage allow for swift and controlled transport, ensuring that materials are delivered precisely where they are needed in the manufacturing process. This capability significantly reduces manual handling, mitigating safety risks and enhancing overall workflow efficiency.
Integration with Manufacturing Processes
The adaptability of 5 to 15 tons single girder and double girder overhead cranes extends to their seamless integration with various manufacturing processes. From positioning coils for stamping and cutting to transporting materials to welding stations, these cranes play a pivotal role in the intricate dance of automotive component production. Their versatility ensures that they can be tailored to meet the specific needs of different stages in the manufacturing line.
Role in Improving Efficiency and Productivity
The impact of these cranes on efficiency and productivity within automotive body shops is profound. By automating the handling of heavy coils, they significantly reduce manual labor requirements. This not only enhances safety but also allows skilled workers to focus on more intricate tasks, ultimately improving the overall quality of the manufactured components.
The precision control offered by these cranes contributes to minimizing errors in material placement, reducing the likelihood of defects in the final products. This, coupled with their swift operational speed, translates to faster production cycles and increased output. In an industry where time is money, the efficiency gains realized through the use of 5 to 15 tons single girder and double girder overhead cranes translate directly into improved competitiveness and profitability.
Stay tuned for Part VI, where we explore real world case studies, examining how automotive body shops have successfully implemented these cranes to optimize their manufacturing processes and achieve remarkable results.
Case Studies
Examples of Automotive Body Shops Using 5 to 15 Tons single girder and double girder overhead cranes
The Automotive Manufacturing Co.:
- Challenge: Automotive faced challenges in efficiently handling heavy steel coils in their body shop.
- Solution: They implemented 5 to 15 tons single girder and double girder overhead cranes tailored to their space constraints and load requirements.
- Results: The cranes streamlined coil unloading, loading, and transportation, reducing manual labor and enhancing overall production efficiency.
Innovative Motors Corp.:
- Challenge: Innovative Motors sought a solution for precise coil placement in their automated welding stations.
- Solution: 5 to 15 tons single girder and double girder overhead cranes with customized control systems were integrated into their manufacturing line.
- Results: The cranes provided the accuracy required for automated welding processes, reducing errors and improving the consistency of welds.
Success Stories and Benefits Realized
- Enhanced Safety: Implementing these cranes led to a significant reduction in manual handling, minimizing the risk of injuries and accidents associated with heavy coil manipulation.
- Increased Efficiency: The precision control and adaptability of these cranes optimized material flow, reducing downtime and speeding up production cycles.
- Cost Savings: Automotive body shops realized cost savings by streamlining operations, reducing the need for manual labor, and minimizing material damage.
- Improved Product Quality: The accuracy of coil placement ensured a consistent and high quality manufacturing process, reducing defects in the final automotive components.
- Competitive Edge: Body shops that adopted these cranes reported improved competitiveness within the automotive manufacturing sector, meeting deadlines more consistently and delivering high quality products.
These case studies and success stories underscore the transformative impact of 5 to 15 tons single girder and double girder overhead cranes in automotive body shops. As we conclude our exploration, Part VII will focus on the critical considerations for selecting, installing, and maintaining these cranes to ensure their seamless integration into manufacturing processes.
Considerations for Selection and Installation
Site Assessment
Before embarking on the installation of 5 to 15 tons single girder and double girder overhead cranes, a comprehensive site assessment is imperative. This involves evaluating factors such as:
- Space Constraints: Ensure that the facility has sufficient vertical space for the crane's lifting capacity and adequate horizontal space for its span length.
- Floor Load Capacity: Verify that the floor can support the crane and its load without compromising structural integrity.
- Workflow Integration: Consider how the crane will fit into the existing workflow and whether modifications are needed for optimal efficiency.
Safety Regulations and Compliance
Adherence to safety regulations is paramount in the automotive manufacturing industry. Before selecting and installing overhead cranes, it is crucial to:
- Understand Local Regulations: Familiarize yourself with local safety regulations and standards related to overhead crane operations.
- Compliance Certification: Ensure that the selected crane complies with industry standards and possesses necessary certifications to guarantee safe operations.
- Training Programs: Establish training programs for operators to ensure they are proficient in the safe operation of the cranes.
Installation Process
The installation of 5 to 15 tons single girder and double girder overhead cranes requires meticulous planning and execution. Considerations during the installation process include:
- Professional Installation Teams: Engage experienced and certified installation teams to guarantee the proper setup and alignment of the cranes.
- Integration with Existing Infrastructure: Ensure seamless integration with existing structures and utilities within the facility.
- Testing and Calibration: Rigorous testing and calibration of the crane's components are essential to guarantee optimal functionality and safety.
Maintenance Requirements
Regular maintenance is key to ensuring the longevity and reliable performance of overhead cranes. Maintenance considerations include:
- Scheduled Inspections: Implement a routine inspection schedule to identify and address potential issues before they escalate.
- Lubrication and Component Checks: Regularly lubricate moving parts and conduct thorough checks of critical components to prevent wear and tear.
- Operator Training on Maintenance: Train crane operators to recognize early signs of issues and report them promptly for timely intervention.
- Emergency Response Plan: Develop a comprehensive emergency response plan in case of breakdowns or unexpected malfunctions.
By addressing these considerations during the selection, installation, and maintenance phases, automotive body shops can ensure the seamless integration of 5 to 15 tons single girder and double girder overhead cranes into their manufacturing processes, optimizing safety, efficiency, and overall productivity.
As we wrap up our exploration, these considerations pave the way for the successful utilization of overhead cranes, enhancing the capabilities of automotive body shops in the ever evolving landscape of manufacturing.
Conclusion
In the intricate dance of automotive manufacturing, the 5 to 15 tons single girder and double girder overhead cranes emerge as indispensable allies. Their robust load capacity, precision control, and adaptability make them the ideal solution for coil handling within automotive body shops. From efficiently unloading and loading coils to seamlessly transporting materials within the shop, these cranes contribute significantly to enhancing safety, efficiency, and overall productivity.
The journey through the world of 5 to 15 tons single girder and double girder overhead cranes reveals their transformative impact on coil handling in automotive body shops. As the automotive industry evolves, the need for precision, efficiency, and safety becomes more pronounced. These cranes not only meet these demands but elevate manufacturing processes to new heights.
The benefits realized through the implementation of these cranes are not just in numbers or statistics but in the tangible improvements experienced by automotive body shops across the globe. Enhanced safety, increased efficiency, and improved product quality contribute not only to the bottom line but also to the overall competitiveness and sustainability of automotive manufacturing operations.
As automotive body shops navigate the challenges and opportunities ahead, the choice of 5 to 15 tons single girder and double girder overhead cranes becomes a strategic investment in the future. It's a commitment to precision, a dedication to safety, and a catalyst for achieving new heights in automotive manufacturing excellence.
In closing, as technology continues to advance and manufacturing processes evolve, the role of these cranes will undoubtedly expand, further solidifying their place as essential assets in the ever changing landscape of automotive production.