Overhead Crane 3T, 5T, 10T for Soybean Meal Feed Pellet Plants
Overhead Crane 3T, 5T, 10T for Soybean Meal Feed Pellet Plants. Overhead cranes for material handling in soybean meal feed pellet facilities in Argentina to ensure precise ingredient dosing & maintain product consistency.
Advanced Overhead Cranes for Soybean Meal Feed Pellet Facilities in Argentina
In industrial operations, few tools are as indispensable as overhead cranes. These versatile machines, known for their ability to lift heavy loads with ease, play a crucial role in material handling across various industries. Today, we delve into their significance within the context of soybean meal feed pellet facilities in Argentina.
At their core, overhead cranes are heavy-duty machines designed to lift, move, and position loads horizontally within a defined area. They typically consist of a hoist, which is used for lifting, and a trolley that traverses along a bridge or gantry beam. These cranes come in various configurations, each tailored to specific applications and operational requirements.
The importance of overhead cranes cannot be overstated in the realm of material handling. These robust machines enhance efficiency, safety, and·productivity in industrial settings by streamlining the movement of heavy and bulky loads. Their versatility allows for the seamless transfer of materials across production lines, warehouses, and storage yards, making them a cornerstone of modern manufacturing processes.
Argentina, renowned for its thriving agricultural sector, boasts a significant presence in the global soybean market. Soybean meal, a key byproduct of soybean processing, serves as a vital ingredient in animal feed production. In Argentina, feed pellet facilities play a pivotal role in transforming soybean meal into nutritious pellets for livestock consumption. These facilities operate round the clock, handling large volumes of raw materials and finished products with precision and efficiency.
Stay tuned as we explore the role of advanced overhead cranes in optimizing material handling processes within soybean meal feed pellet facilities in Argentina. From enhancing dosing accuracy to ensuring product consistency, these cutting-edge machines are revolutionizing the way feed pellets are produced and distributed.
Types of Overhead Cranes
In the field of material handling, selecting the right crane is essential for smooth and efficient operations. Let's explore two commonly used types of overhead cranes and their applications in feed pellet facilities.
Bridge Cranes
Bridge cranes, also referred to as overhead bridge cranes or overhead traveling cranes, feature a horizontal beam (bridge) that spans the width of the workspace. Supported by end trucks, these cranes move along a runway system positioned above the work area. A hoist, attached to a trolley, enables vertical lifting and horizontal movement of loads.
Bridge cranes offer several benefits:
- High Load Capacity: Capable of lifting heavy loads, bridge cranes are ideal for transporting bulk materials like soybean meal and feed additives.
- Precise Control: Operators enjoy excellent visibility and control, facilitating precise maneuvering of loads.
- Space Efficiency: Utilizing overhead space efficiently, bridge cranes free up valuable floor space for other operations and equipment.
- Versatility: Customizable with multiple hoists, special attachments, and automation systems, bridge cranes adapt to various applications.
Applications in Feed Pellet Facilities:
Bridge cranes are indispensable in feed pellet facilities for:
- Loading and unloading raw materials from trucks and storage silos.
- Transporting materials between processing stages, including mixing, grinding, pelletizing, and packaging.
- Positioning and assembling equipment used in feed production lines.
- Conducting maintenance and inspection tasks on production equipment and storage facilities.
Gantry Cranes
Gantry cranes, also known as portal cranes, feature a horizontal beam supported by legs or uprights on either side, forming a stable, rectangular frame. Unlike bridge cranes, gantry cranes operate on ground-level tracks or wheels, enabling movement along a fixed path. A hoist and trolley system provide both vertical lifting and horizontal movement capabilities similar to bridge cranes.
Gantry cranes offer several advantages:
- Mobility: Easily relocatable within a facility or deployable in outdoor environments, gantry cranes provide flexibility in material handling operations.
- Accessibility: Ground-level design simplifies loading and unloading processes, allowing direct access to materials and workpieces.
- Cost-effectiveness: Requiring minimal infrastructure compared to bridge cranes, gantry cranes are cost-effective for temporary or remote work sites.
- Adaptability: Configurable with adjustable heights, spans, and lifting capacities, gantry cranes accommodate diverse loads and operational requirements.
Applications in Feed Pellet Facilities:
Gantry cranes play vital roles in feed pellet facilities by:
- Facilitating movement of materials between indoor and outdoor storage areas, such as warehouses, silos, and loading docks.
- Supporting maintenance and repair activities on production equipment, storage facilities, and infrastructure.
- Handling oversized or irregularly shaped loads challenging to maneuver with other crane types.
- Providing backup lifting capacity during peak production periods or where overhead clearance is limited.
In conclusion, bridge and gantry cranes are essential assets in the efficient operation of feed pellet facilities, contributing to increased productivity, safety, and profitability. Their unique features and capabilities ensure smooth material handling processes, enabling seamless production of high-quality feed pellets.
Typical Loads Lifted in Soybean Meal Feed Pellet Facilities
Soybean meal stands as a cornerstone ingredient in the production of animal feed. Let's delve into its significance and the considerations surrounding its handling within feed pellet facilities.
Soybean Meal
Importance in Animal Feed Production:
Soybean meal holds a pivotal role in animal feed formulation for various reasons:
- High Nutritional Value: Rich in protein, soybean meal serves as a primary source of essential amino acids crucial for animal growth and development.
- Balanced Nutrition: Its composition complements other feed ingredients, aiding in achieving optimal nutritional balance for different livestock species.
- Cost-effectiveness: Compared to alternative protein sources, soybean meal offers a cost-effective solution for meeting the protein requirements of livestock diets.
- Digestibility: Soybean meal is easily digestible, ensuring efficient nutrient absorption by animals, which ultimately translates to improved feed conversion ratios and overall productivity.
Handling Considerations:
Efficient handling of soybean meal within feed pellet facilities requires careful consideration of several factors:
- Hygiene and Contamination Control: Maintaining cleanliness and preventing contamination are paramount to ensure feed safety and quality. Proper handling practices, including regular cleaning of equipment and storage areas, are essential.
- Moisture Management: Soybean meal is susceptible to moisture absorption, which can lead to mold growth and spoilage. Adequate ventilation and moisture control measures are necessary to preserve its quality during storage and handling.
- Particle Size Consistency: Consistent particle size of soybean meal contributes to uniform mixing and pellet formation in feed production. Therefore, employing equipment capable of precise dosing and handling is crucial to maintain product quality.
- Dust Control: Handling soybean meal can generate dust, posing respiratory hazards to workers and potentially contaminating the environment. Implementing dust control measures, such as proper ventilation and use of dust collection systems, is essential to ensure a safe and healthy working environment.
In summary, soybean meal holds significant importance in animal feed production due to its nutritional value, cost-effectiveness, and digestibility. However, its efficient handling within feed pellet facilities requires attention to hygiene, moisture management, particle size consistency, and dust control to maintain feed quality and ensure the safety of both workers and the environment.
Protein Concentrates
Role in Animal Nutrition:
Protein concentrates play a vital role in meeting the protein requirements of animals, contributing to their growth, development, and overall health. Here's why they're indispensable in animal nutrition:
- High Protein Content: Protein concentrates contain a high concentration of protein, making them valuable sources of essential amino acids necessary for muscle development, immune function, and metabolic processes in animals.
- Nutritional Balance: Incorporating protein concentrates into animal feed formulations helps achieve the desired balance of amino acids, ensuring optimal growth performance and feed efficiency.
- Digestibility: Protein concentrates are typically highly digestible, allowing for efficient utilization of nutrients by animals and minimizing waste production.
- Versatility: Protein concentrates can be derived from various sources, including soybeans, fish meal, and poultry by-products, providing flexibility in formulating diets tailored to the specific nutritional requirements of different animal species and production stages.
Handling Challenges:
Despite their nutritional benefits, protein concentrates present certain challenges in handling within feed pellet facilities:
- Hygroscopic Nature: Protein concentrates, particularly those of plant origin like soybean meal, tend to absorb moisture from the surrounding environment, leading to clumping and caking issues. Proper storage conditions, such as low humidity levels and adequate ventilation, are essential to prevent moisture-related spoilage.
- Particle Size Uniformity: Ensuring consistent particle size distribution of protein concentrates is crucial for achieving uniform mixing and pellet quality in feed production. Handling equipment capable of precise dosing and particle size reduction is necessary to maintain product consistency.
- Allergen Management: Protein concentrates derived from common allergenic sources, such as soybeans and wheat, may pose allergen cross-contamination risks in feed processing facilities. Implementing stringent allergen control measures, including segregation, cleaning, and allergen testing, is critical to prevent allergen-related incidents and ensure feed safety.
- Dust Generation: Handling protein concentrates can generate dust, posing respiratory hazards to workers and contamination risks to the surrounding environment. Employing dust control measures, such as dust extraction systems and personal protective equipment, is essential to mitigate these risks and maintain a safe working environment.
In summary, protein concentrates play a crucial role in animal nutrition by providing essential amino acids necessary for growth and health. However, their handling within feed pellet facilities requires attention to challenges such as moisture management, particle size uniformity, allergen management, and dust control to ensure feed quality and safety while safeguarding the well-being of workers and the environment.
Feed Additives
Types and Functions:
Feed additives encompass a diverse range of substances added to animal feed to improve nutritional value, enhance feed efficiency, and promote animal health and performance. Here are some common types and their functions:
- Vitamins: Essential for various metabolic processes, vitamins are added to animal feed to prevent deficiencies and support overall health and immune function.
- Minerals: Minerals such as calcium, phosphorus, and magnesium are vital for bone development, muscle function, and metabolic regulation in animals.
- Amino Acids: Amino acids serve as the building blocks of protein and are added to feed formulations to ensure optimal protein synthesis and growth performance.
- Enzymes: Enzymes such as phytase and protease help improve nutrient digestibility and utilization, leading to enhanced feed efficiency and reduced environmental impact.
- Antioxidants: Antioxidants such as vitamin E and selenium help protect feed ingredients from oxidation and maintain feed quality during storage.
- Antibiotics and Growth Promoters: While controversial, certain antibiotics and growth promoters may be used in animal feed to prevent disease, improve feed efficiency, and promote growth. However, their use is increasingly restricted due to concerns about antimicrobial resistance and consumer preferences for antibiotic-free products.
Specialized Handling Requirements:
Feed additives often have specialized handling requirements due to their unique properties and regulatory considerations:
- Sensitive to Environmental Conditions: Some feed additives, such as vitamins and enzymes, are sensitive to heat, moisture, and light, which can degrade their potency and effectiveness. Proper storage conditions, including temperature and humidity control, are crucial to maintain additive stability.
- Accurate Dosing and Mixing: Feed additives are typically added to feed formulations in precise quantities to achieve desired nutritional outcomes. Therefore, handling equipment must be capable of accurate dosing and thorough mixing to ensure uniform distribution of additives throughout the feed matrix.
- Regulatory Compliance: Feed additives are subject to regulatory oversight to ensure their safety and efficacy. Compliance with regulatory requirements, including labeling, documentation, and quality control measures, is essential to meet regulatory standards and ensure consumer confidence in feed products.
- Safety Considerations: Some feed additives may pose occupational health and safety risks to workers if mishandled. Adequate training, personal protective equipment, and handling protocols are necessary to minimize risks and ensure a safe working environment.
In summary, feed additives play critical roles in animal nutrition and feed production, providing essential nutrients, enhancing feed efficiency, and promoting animal health and performance. However, their specialized handling requirements necessitate careful attention to storage conditions, accurate dosing, regulatory compliance, and safety considerations to maintain additive efficacy and ensure feed quality and safety.
Core Focus of Advanced Overhead Crane Implementation
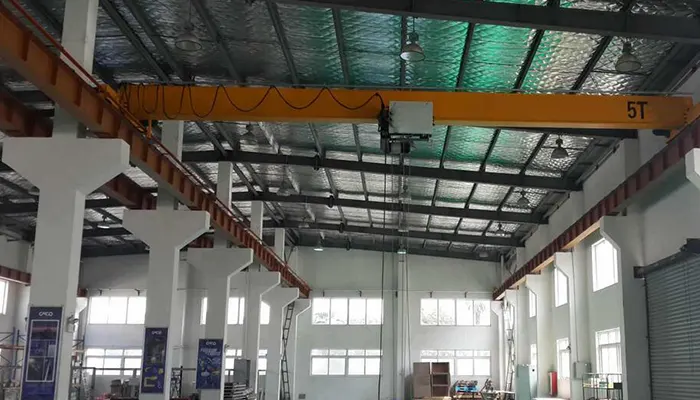
Implementing Advanced Material Handling Techniques
Automation and Robotics Integration:
In modern industrial settings, the integration of automation and robotics into overhead crane systems revolutionizes material handling processes. Here's how:
- Increased Efficiency: Automation reduces the reliance on manual labor, streamlining material handling tasks and minimizing the risk of human error. This results in faster throughput and improved operational efficiency in feed pellet facilities.
- Enhanced Safety: By automating repetitive and potentially hazardous tasks, such as lifting heavy loads or navigating confined spaces, overhead cranes equipped with robotics enhance workplace safety and reduce the risk of accidents and injuries.
- Optimized Resource Utilization: Automated overhead crane systems optimize resource utilization by operating continuously, maximizing uptime, and minimizing downtime associated with manual intervention or maintenance activities.
- Flexibility and Adaptability: Advanced overhead crane systems equipped with robotics offer flexibility and adaptability to changing production requirements and operational environments. They can be programmed to perform a wide range of tasks, from simple material handling to complex assembly or sorting processes.
- Data-driven Insights: Integration with data analytics and monitoring systems enables real-time tracking of crane performance, load characteristics, and operational metrics. This data-driven approach facilitates proactive maintenance scheduling, predictive maintenance, and performance optimization, maximizing crane uptime and longevity.
Precision Control Systems:
Precision control systems are integral to the efficient operation of advanced overhead crane systems, offering the following benefits:
- Accurate Positioning: Precision control systems enable precise positioning and movement of loads, ensuring optimal alignment with processing equipment and minimizing the risk of product damage or spillage.
- Variable Speed Control: Variable speed control allows operators to adjust crane movement speeds according to load characteristics, operational requirements, and environmental conditions. This flexibility enhances safety, efficiency, and productivity in material handling operations.
- Load Sensing and Monitoring: Integrated load sensing and monitoring systems provide real-time feedback on load weight, distribution, and stability, enabling operators to make informed decisions and adjustments to ensure safe and efficient crane operation.
- Collision Avoidance: Advanced overhead crane systems utilize sensors, cameras, and collision avoidance algorithms to detect obstacles, personnel, and other equipment in the crane's path. These safety features prevent accidents and damage to both the crane and surrounding infrastructure.
- Remote Monitoring and Control: Remote monitoring and control capabilities enable operators to supervise crane operations from a centralized location, improving visibility, accessibility, and responsiveness to operational challenges or emergencies.
By implementing advanced material handling techniques such as automation and robotics integration, along with precision control systems, overhead crane systems in feed pellet facilities can achieve unprecedented levels of efficiency, safety, and productivity. These technological advancements not only optimize operational performance but also pave the way for future innovations in the field of material handling and industrial automation.
Ensuring Precise Ingredient Dosing
Importance in Feed Quality and Nutrition:
Precise ingredient dosing is paramount in feed pellet production as it directly impacts feed quality, nutritional consistency, and animal performance. Here's why it's crucial:
- Nutritional Balance: Accurate dosing ensures that feed formulations contain the correct proportions of essential nutrients, vitamins, minerals, and additives required for optimal animal nutrition. This helps maintain the nutritional balance necessary for healthy growth, development, and overall well-being of livestock.
- Feed Uniformity: Consistent dosing of ingredients results in uniform feed pellets with consistent nutritional content and physical characteristics. Uniformity ensures that animals receive a balanced diet in every feeding, reducing the risk of nutrient deficiencies or imbalances that can affect animal health and performance.
- Feed Efficiency: Precise dosing minimizes ingredient waste and excess usage, optimizing feed efficiency and reducing production costs. By avoiding over- or under-dosing, feed manufacturers can maximize the utilization of raw materials and improve profitability.
- Product Quality Assurance: Accurate dosing contributes to the production of high-quality feed pellets with consistent texture, flavor, and nutritional value. This enhances consumer satisfaction, fosters brand reputation, and ensures compliance with regulatory standards and industry certifications.
Role of Crane Technology in Dosing Accuracy:
Advanced crane technology plays a significant role in achieving precise ingredient dosing in feed pellet facilities by leveraging the following capabilities:
- Integrated Weighing Systems: Many modern overhead crane systems are equipped with integrated weighing systems that accurately measure the weight of loads during lifting and transportation. These systems provide real-time feedback on load weight, allowing operators to adjust dosing parameters and ensure accurate ingredient delivery.
- Automation and Control Software: Crane automation and control software enable precise positioning and movement of loads, allowing for controlled dosing of ingredients into mixers or feed processing equipment. Automation reduces human error and variability, enhancing dosing accuracy and consistency.
- Load Cell Technology: Load cells integrated into crane lifting mechanisms provide accurate weight measurement of loads in real-time. This data is transmitted to control systems, which adjust crane operations to maintain target dosing parameters and optimize feed formulation.
- Feedback and Monitoring Systems: Crane technology may include feedback and monitoring systems that continuously monitor dosing performance, detect deviations from set parameters, and provide alerts or alarms for corrective action. This proactive approach helps prevent dosing errors and ensures adherence to quality standards.
- Integration with Process Control Systems: Advanced overhead crane systems can be integrated with feed production process control systems, enabling seamless communication and coordination between material handling and manufacturing processes. This integration ensures synchronization of ingredient dosing with other production stages, optimizing overall feed pellet production efficiency and quality.
In summary, advanced crane technology plays a pivotal role in ensuring precise ingredient dosing in feed pellet facilities. By leveraging integrated weighing systems, automation software, load cell technology, feedback mechanisms, and process integration capabilities, overhead cranes contribute to the production of high-quality feed pellets with consistent nutritional content and performance benefits for livestock.
Maintaining Product Consistency
Challenges in Pellet Production:
Consistency is paramount in feed pellet production to ensure uniform quality, nutritional value, and physical characteristics of the pellets. Several challenges may hinder consistency, including:
- Ingredient Variation: Variability in the characteristics of raw materials, such as particle size, moisture content, and nutritional composition, can lead to inconsistencies in pellet quality and nutritional content.
- Equipment Performance: Wear and tear, misalignment, or malfunction of processing equipment, including pellet mills, mixers, and dryers, can result in variations in pellet size, density, and texture.
- Process Variability: Fluctuations in process parameters, such as temperature, moisture levels, and mixing times, can affect the homogeneity and integrity of pellet formulations, leading to inconsistencies in product quality.
- Operator Error: Human factors, such as errors in ingredient measurement, formulation, or process control, can introduce variability and deviation from desired product specifications.
- Environmental Factors: External factors, such as seasonal changes in humidity, temperature, and ambient conditions, may influence the performance of feed processing equipment and impact pellet quality and consistency.
How Advanced Cranes Address Consistency Issues:
Advanced overhead crane systems play a crucial role in addressing consistency challenges in feed pellet production through the following mechanisms:
- Integrated Process Control: Advanced crane systems can be integrated with feed processing equipment and control systems, enabling real-time monitoring and adjustment of material handling processes to maintain consistent ingredient dosing, mixing, and pelletization.
- Automated Material Handling: Automation and robotics integration in overhead crane systems minimize reliance on manual labor and reduce the risk of human error in material handling tasks, ensuring consistent handling and transfer of raw materials and finished products.
- Precision Control and Positioning: Advanced crane technology offers precision control systems that enable accurate positioning and movement of materials within the production environment, ensuring uniform distribution of ingredients and consistent pellet formation.
- Load Monitoring and Feedback: Crane systems equipped with load monitoring sensors and feedback mechanisms provide real-time data on load characteristics, enabling operators to detect deviations from target parameters and take corrective actions to maintain consistency.
- Customization and Adaptability: Modern crane systems are customizable and adaptable to diverse production requirements and operational environments, allowing for the implementation of tailored solutions to address specific consistency challenges.
- Predictive Maintenance: Advanced crane systems may incorporate predictive maintenance algorithms and condition monitoring capabilities to anticipate and prevent equipment failures or performance degradation that could compromise consistency in pellet production.
In summary, advanced overhead crane systems play a vital role in maintaining product consistency in feed pellet production by addressing challenges related to ingredient variation, equipment performance, process variability, operator error, and environmental factors. Through integration with process control systems, automation, precision control, load monitoring, and customization capabilities, advanced crane technology ensures uniform quality, nutritional content, and physical characteristics of feed pellets, contributing to improved animal performance and customer satisfaction.
Double girder overhead crane for sale , European style
Challenges and Solutions
Operational Challenges Faced in Implementing Advanced Cranes
The implementation of advanced overhead crane systems in feed pellet facilities may encounter several operational challenges, including:
- Integration Complexity: Integrating advanced crane technology with existing equipment and processes can be complex and require careful planning to ensure seamless operation and compatibility.
- Training and Skills Gap: Operating and maintaining advanced crane systems may require specialized skills and training for personnel. A lack of skilled workforce can pose challenges in maximizing the benefits of crane technology.
- Initial Investment Costs: The upfront investment required for acquiring and installing advanced crane systems may be significant, potentially posing financial challenges for feed pellet facilities.
Strategies for Overcoming Implementation Hurdles
To overcome the operational challenges associated with implementing advanced overhead crane systems, feed pellet facilities can adopt the following strategies:
- Comprehensive Planning and Assessment: Conduct a thorough assessment of current operations, infrastructure, and workforce capabilities before implementing advanced crane technology. Develop a comprehensive implementation plan that addresses integration requirements, training needs, and potential risks.
- Investment in Training and Development: Invest in training programs and skill development initiatives to ensure that personnel are adequately trained to operate and maintain advanced crane systems. Provide ongoing support and resources to facilitate continuous learning and skill enhancement.
- Cost-Benefit Analysis: Conduct a detailed cost-benefit analysis to evaluate the financial feasibility and potential return on investment of implementing advanced crane technology. Explore financing options, incentives, and cost-saving measures to mitigate upfront investment costs.
Continuous Improvement and Adaptation
Continuous improvement and adaptation are essential for maximizing the benefits of advanced crane systems in feed pellet facilities. Here are some strategies to foster continuous improvement:
- Performance Monitoring and Optimization: Implement monitoring and analytics tools to track crane performance, identify areas for improvement, and optimize operational efficiency. Regularly review performance metrics and implement corrective actions to address inefficiencies or bottlenecks.
- Feedback and Collaboration: Encourage feedback from operators, maintenance personnel, and other stakeholders to identify challenges and opportunities for improvement. Foster collaboration between different departments and external partners to leverage collective expertise and drive innovation.
- Technology Upgrades and Innovation: Stay abreast of technological advancements and industry trends in overhead crane technology. Consider upgrading or retrofitting existing crane systems with new features or capabilities to enhance performance, reliability, and safety.
- Flexibility and Adaptability: Maintain flexibility and adaptability in response to changing operational requirements, market dynamics, and regulatory requirements. Continuously evaluate and adjust crane operations and processes to remain competitive and responsive to customer needs.
By addressing operational challenges, implementing effective strategies for implementation, and fostering a culture of continuous improvement and adaptation, feed pellet facilities can successfully leverage advanced overhead crane systems to enhance efficiency, productivity, and competitiveness in the dynamic livestock industry.
Conclusion
Throughout this exploration of advanced overhead crane systems in soybean meal feed pellet facilities, several key points have emerged:
- Overhead cranes, including bridge and gantry types, play a crucial role in material handling within feed pellet facilities, lifting loads such as soybean meal, protein concentrates, and feed additives.
- The implementation of advanced material handling techniques, precise ingredient dosing, and maintenance of product consistency are essential for optimizing feed pellet production.
- Challenges such as operational complexities, integration hurdles, and initial investment costs must be addressed when implementing advanced crane systems.
- Strategies including comprehensive planning, investment in training, and cost-benefit analysis can help overcome implementation challenges and maximize the benefits of advanced crane technology.
Importance of Advanced Overhead Crane Systems in Soybean Meal Feed Pellet Facilities
The importance of advanced overhead crane systems in soybean meal feed pellet facilities cannot be overstated. These systems are instrumental in optimizing material handling processes, ensuring precise ingredient dosing, and maintaining product consistency. By leveraging advanced technologies such as automation, robotics, and precision control, overhead crane systems contribute to increased efficiency, productivity, and profitability in feed pellet production. Additionally, advanced crane systems enhance safety, sustainability, and regulatory compliance, further underscoring their importance in the industry.
Implications for the Industry and Recommendations for Further Research
The implications of advanced overhead crane systems extend beyond individual feed pellet facilities to the broader livestock industry. As feed manufacturers strive to meet growing demand for high-quality, nutritionally balanced feed products, the adoption of advanced crane technology will become increasingly prevalent. Furthermore, ongoing research and innovation in crane design, automation, and sustainability will drive continuous improvement and transformation in material handling practices.
In conclusion, advanced overhead crane systems represent a cornerstone of modern material handling practices in soybean meal feed pellet facilities. By embracing innovation, collaboration, and continuous improvement, the livestock industry can harness the full potential of advanced crane technology to achieve its goals of efficiency, sustainability, and excellence in feed production.