40 Ton Overhead Crane Heavy Duty for Steel Coil Handling
40 ton overhead crane for sale. Check double girder overhead crane's efficiency, safety & cost-effectiveness in steel coil loading & unloading operations.
Overview of the 40 Ton Overhead Cranes
This case study highlights the use of a 40-ton overhead crane in handling steel coils in a steel mill warehouse. The crane is a QD heavy-duty model, featuring a double girder design and an open winch trolley. This design is tailored for lifting and transporting heavy, large steel coils efficiently and safely in a challenging industrial environment.
40 ton double girder overhead crane with open winch trolley for coil handling
- Model: QD heavy-duty overhead crane
- Design: Double girder with an open winch trolley
- Capacity: 40 tons
- Application: Steel coil handling in a steel mill warehouse
The crane’s combination of heavy-duty design and operational flexibility makes it ideal for handling heavy loads like steel coils, which require precision and stability.
Application Focus: Handling Steel Coils in a Steel Mill Warehouse
Steel coils are bulky, heavy, and challenging to move, requiring specialized equipment. In a steel mill warehouse, steel coils need to be unloaded from trucks, positioned accurately on storage racks, and moved to various processing areas.
The QD overhead crane with its 40-ton capacity is perfectly suited for this task. The open winch trolley design allows the crane to move steel coils with precision, ensuring safe and efficient handling in a crowded and high-stakes environment.
- Primary Task: Unloading and positioning steel coils
- Importance: Safe handling of heavy, bulky materials
- Design Benefit: Precision movement in tight spaces
By using this crane, steel mills can avoid the inefficiencies and risks associated with less specialized equipment.
Purpose of the Case Study
The purpose of this case study is to explore the effectiveness of the 40-ton QD overhead crane in handling steel coils. We will look into its benefits in terms of efficiency, safety, and productivity. Additionally, the case study will examine the challenges involved in steel coil handling and how this crane addresses those challenges.
This analysis will demonstrate how the QD crane optimizes space, improves operational efficiency, and contributes to a safer working environment in the steel mill warehouse.
- Focus Areas: Efficiency, safety, and challenges
- Goal: Show the crane's impact on steel coil handling
- Outcome: Understanding the benefits of using the crane in a steel mill
Background Information
Steel Coil Handling in Steel Mills
Steel coils are one of the most essential products in a steel mill, used in various industries ranging from automotive to construction. Handling these coils requires precision and care. These materials are heavy, often weighing several tons, and have a delicate surface that can easily be damaged during transport.
The importance of handling steel coils safely and efficiently cannot be overstated. Mishandling can lead to material damage, production delays, and safety hazards. Moreover, the process of unloading, storing, and transporting steel coils often takes place in tight, cluttered spaces, which increases the need for precise maneuvering.
- Importance of Safe Handling: Prevents damage and injury
- Efficiency: Reduces delays and boosts productivity
- Challenges: Heavy weight, large size, and delicate surface
Steel mills must rely on equipment that ensures both speed and safety when dealing with such a demanding material.
Overview of Challenges Faced in Steel Coil Handling
Handling steel coils presents several unique challenges:
- Weight: Steel coils are extremely heavy, often requiring equipment that can lift several tons safely.
- Size: These coils are bulky, making it difficult to position them accurately in storage or processing areas.
- Delicate Nature: The surface of steel coils is often coated or treated, meaning any mishandling could lead to scratches or other damage.
These challenges demand specialized equipment capable of lifting and moving steel coils without causing damage or compromising safety.
- Heavy Loads: Requires cranes with high load capacity
- Bulky Items: Necessitates precise control and maneuverability
- Delicate Surfaces: Needs to avoid surface damage during handling
A solution that can tackle all these challenges while maintaining safety and efficiency is essential in the steel mill environment.
40 ton overhead bridge crane with C hook for steel coil handling
Overview of Overhead Cranes
Overhead cranes are commonly used in industrial environments for handling heavy loads. They provide the ability to lift and move large items like steel coils with precision and control. Unlike other types of cranes, overhead cranes are mounted on tracks above the workspace, which allows for movement in both horizontal and vertical directions.
- Role in Industry: Overhead cranes are essential for material handling in steel mills, warehouses, and factories.
- Design Advantage: Their ability to move loads safely in tight spaces and high-clearance areas makes them ideal for environments like steel mills.
One of the main reasons overhead cranes are preferred is their ability to work in high-ceiling environments, optimizing vertical space and reducing the need for ground-based equipment.
Explanation of Double Girder and Open Winch Trolley Design
The QD overhead crane in this case study features a double girder design, which provides superior strength and stability. This design allows the crane to handle very heavy loads, such as the 40-ton steel coils, with ease and precision.
- Double Girder Design: Provides greater stability and higher lifting capacity.
- Open Winch Trolley: Increases flexibility by allowing smooth horizontal movement of the crane along the beam, making it easier to position heavy loads.
The combination of these two design elements makes the QD overhead crane well-suited for the steel mill environment, where heavy, bulky items need to be moved efficiently.
The Significance of a 40-Ton Capacity Crane for Handling Heavy Loads
A 40-ton capacity crane is an essential tool in steel mills where large and heavy materials like steel coils are the norm. These cranes are built to handle loads that smaller cranes simply cannot manage, providing greater operational capacity and reducing the need for multiple lifts or equipment.
- Heavy Load Capability: Can handle the heaviest steel coils with ease.
- Efficiency: Reduces time spent on lifting and transporting heavy materials.
- Safety: With higher lifting capacity, the risk of equipment failure or strain is minimized.
In a steel mill setting, using a 40-ton crane means faster, safer, and more efficient handling of steel coils, ultimately leading to increased productivity and a safer working environment.
Crane Design and Features
Design Specifications
Double Girder Design:
The QD 40-ton overhead crane features a double girder design, which offers significant advantages in both load handling and structural stability. This design consists of two main girders supporting the crane’s hoist, which allows for better distribution of the weight across the structure. The double girder setup enhances the crane's capacity to handle heavy loads like steel coils, reducing the strain on individual components and ensuring long-term durability.
Advantages:
- Increased strength and stability for handling heavy loads.
- Allows for larger spans and greater lifting height, providing flexibility in warehouse design.
- Better load distribution reduces wear and tear on components.
The design is particularly ideal for environments like steel mills where large, heavy materials are moved regularly.
Open Winch Trolley:
The open winch trolley design plays a crucial role in the crane’s operational flexibility. This feature allows the hoist to move horizontally along the crane’s beam, providing precise control over the steel coils' positioning. The open winch setup also makes maintenance easier, as the components are more accessible than in closed designs.
Impact on Flexibility:
- Enhanced movement capability for positioning heavy coils with precision.
- Allows for smooth horizontal and vertical adjustments, reducing the risk of mishandling.
- Easy to maintain, ensuring higher uptime for the crane.
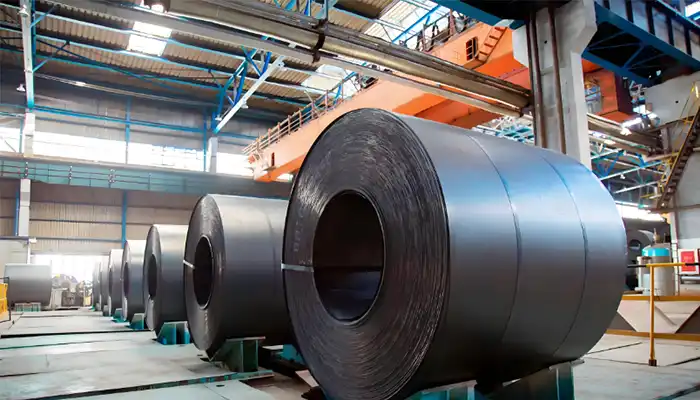
Load Capacity (40 Ton):
The 40-ton overhead crane is perfectly suited for handling steel coils, which are often very heavy and large. The 40-ton capacity ensures that the crane can lift and move even the heaviest steel coils with ease, making it an ideal choice for steel mills where such heavy-duty lifting is common.
Why 40 Tons Is Ideal:
- Meets the typical weight range of steel coils without risk of overloading.
- Provides flexibility for other heavy-duty tasks within the steel mill.
- Ensures operational efficiency by reducing the need for multiple lifts.
Lifting Mechanisms:
The lifting mechanisms of the crane are designed to ensure smooth and precise handling of heavy loads. The hoisting speed is adjustable to allow for both quick lifts and more controlled, slower movements. The load control system ensures that the crane operator can maintain steady, controlled lifting, minimizing the risk of load swinging or instability.
Features of the Lifting Mechanism:
- Hoisting Speed: Adjustable for quick or precise lifting operations.
- Load Control: Ensures stable and controlled movement, reducing risks of sudden jerks or swings.
- Precision: Allows for accurate positioning of steel coils, essential for tight storage spaces and processing areas.
Safety Features
Anti-Collision Systems:
Safety is a top priority when working with heavy loads. The overhead crane is equipped with anti-collision systems to prevent accidental crashes between the crane and surrounding structures or equipment. This system uses sensors and automated controls to detect obstacles in the crane's path, stopping the crane automatically if it gets too close to anything.
- Prevents: Collisions with walls, beams, or other equipment.
- Improves: Workplace safety by reducing human error and unexpected accidents.
Overload Protection:
The crane is also equipped with overload protection mechanisms to prevent it from lifting loads that exceed its rated capacity. This ensures that the crane operates within safe limits, avoiding the risk of structural damage, mechanical failure, or accidents.
- How it Works: Monitors load weight in real-time and automatically stops operation if the crane exceeds its 40-ton capacity.
- Benefit: Reduces the risk of damage to both the crane and the steel coils being handled.
Emergency Stops and Operational Alarms:
In case of emergencies or abnormal conditions, the crane is equipped with emergency stop buttons and operational alarms. These systems alert the operator to any potential issues, allowing them to stop operations quickly to prevent accidents or damage.
- Emergency Stops: Immediately halts crane movement in case of danger.
- Alarms: Alerts the operator to issues like overloads, system malfunctions, or operational hazards.
Materials and Construction
Durable Materials Suited for Handling Heavy and Bulky Steel Coils:
The crane is built using high-strength materials that are capable of handling the intense forces involved in lifting and transporting heavy steel coils. The structural components, including the girders and hoist, are made of steel alloys designed to resist wear and tear, ensuring that the crane performs efficiently over its lifespan.
- Durability: Materials are resistant to high stress, wear, and heavy loads.
- Impact: Helps to prevent frequent repairs and downtime, ensuring long-term operational reliability.
Protective Coatings to Prevent Wear from Heavy Loads:
Given the challenging conditions in a steel mill, the crane’s components are coated with protective layers to reduce wear from constant exposure to heavy loads and harsh environments. These coatings protect against rust, corrosion, and abrasion, ensuring that the crane remains in good condition for longer periods.
- Protective Coatings: Applied to high-wear areas like the hoist, trolley, and crane rails.
- Purpose: Prevents corrosion, extends equipment lifespan, and reduces maintenance costs.
With these durable materials and protective features, the crane is designed to withstand the harsh conditions of a steel mill while maintaining peak performance.
Application in Steel Coil Handling
Loading and Unloading Process
The process of loading and unloading steel coils using the 40-ton overhead crane is highly efficient, offering safety and precision in a typically fast-paced steel mill environment. Below is a step-by-step overview of the procedure:
Preparation:
- Ensure the crane and its components are fully operational with routine checks.
- Position the truck near the crane's operating area for easy access.
Lifting:
- The crane operator uses the control system to move the hook and load the steel coil from the truck.
- The crane's hoist is carefully lowered to securely grip the steel coil using slings or other lifting devices.
Transporting:
- The crane moves the steel coil horizontally across the workspace, ensuring a smooth and steady lift.
- The open winch trolley design allows for precise control of the load, especially in tight or crowded spaces.
Positioning:
- Once the coil reaches its destination, the crane positions it in the correct storage area or processing location.
- Steel coils are gently placed, ensuring they are secure and properly aligned.
Securing the Load:
- After unloading, the steel coil is secured in place using appropriate supports or cradles to prevent any shifting or damage.
This method is precise, reduces handling time, and is safer compared to manual labor or alternative machines, providing a clear advantage in steel coil management.
Operational Efficiency
Time and Space Optimization:
The overhead crane significantly improves the efficiency of loading and unloading steel coils. With its high lifting capacity, it reduces the need for multiple lifts, speeding up the process. Moreover, the crane can operate in narrow aisles and reach high storage areas, maximizing the available warehouse space.
- Time Efficiency: The crane handles heavy loads quickly, minimizing delays.
- Space Efficiency: It operates above the ground, utilizing vertical space and freeing up floor space for other operations.
Comparison to Other Methods (e.g., Forklifts):
When compared to forklifts or other manual methods, the overhead crane excels in both efficiency and safety:
- Efficiency: Forklifts can only lift and move one coil at a time, whereas the overhead crane can handle larger loads, reducing the need for multiple machines or lifts.
- Safety: The crane minimizes the risk of worker injury from manual handling or accidents that often occur when forklifts are used in cramped spaces.
By optimizing both time and space, the overhead crane is an essential tool in improving operational workflow in steel mills.
Space Optimization
How the Overhead Crane Allows for Better Use of Space:
In steel mills, space is often limited, and maximizing storage capacity is crucial. The overhead crane offers substantial space optimization by moving loads vertically, reducing the need for wide aisles or expansive ground-based equipment. This frees up valuable floor space for other operations or storage.
- Vertical Lift: The crane can lift and store steel coils in high-clearance areas, using overhead space to avoid congestion on the ground.
- Compact Design: Overhead cranes need less ground space than alternative equipment, such as forklifts, which often require large areas to maneuver.
Benefits of Working in High-Ceiling Environments for Greater Clearance:
High ceilings are a significant advantage in warehouses and steel mills. They provide ample room for overhead cranes to lift materials to higher levels, maximizing storage efficiency and enabling easy movement of large loads.
- Clearance Advantage: High ceilings enable the crane to use more of the vertical space for storage and transport, enhancing the overall layout.
- Flexibility: Steel coils can be stacked or positioned at various heights without interfering with other operations, optimizing both space and flow within the warehouse.
Performance and Productivity
Increased Handling Capacity
Comparison of Steel Coil Handling Before and After the Implementation of the Crane:
Before implementing the 40-ton overhead crane, steel coil handling was typically more manual and slower. Workers used forklifts or other equipment to move the coils, which required more time and led to potential handling errors.
- Before the Crane: Steel coils were often moved with forklifts, resulting in slower transport and a higher risk of damage.
- After the Crane: The overhead crane significantly reduces handling time, while its precise lifting and movement reduce the chance of error, increasing throughput.
How the 40-Ton Capacity Crane Enhances Throughput and Reduces Downtime:
The 40-ton capacity crane can handle large and heavy coils without the need for multiple lifts. This capability leads to faster transport of coils, reducing overall downtime. Additionally, fewer equipment breakdowns occur because the crane is designed to handle heavy loads efficiently without strain.
- Throughput: The crane handles more material in less time.
- Downtime: Less frequent breakdowns and faster recovery times due to the crane's robust design.
Cost Efficiency
Reduction in Labor Costs Through Automation and Ease of Operation:
The use of the overhead crane reduces the need for extensive manual labor. Operators can control the crane easily, automating much of the lifting and transportation work. As a result, fewer workers are needed for the task, leading to lower labor costs.
- Labor Reduction: Fewer operators required, reducing staffing costs.
- Automation: The crane’s automation streamlines the process, reducing the reliance on manual labor and making operations more efficient.
Decrease in Potential Damage to Materials (Steel Coils) Through Precise Handling:
The precise control provided by the overhead crane helps reduce the risk of damage to steel coils during transport. Unlike forklifts or manual methods, the crane can lift and place the coils carefully, minimizing the chances of scratches, dents, or other damage.
- Damage Reduction: Less mishandling leads to fewer damaged coils.
- Cost Savings: Reduced material damage means fewer replacements and lower costs associated with damaged goods.
Energy Efficiency
Energy Consumption Comparison with Other Types of Cranes or Handling Equipment:
The 40-ton overhead crane is designed to be energy efficient, especially in comparison to other equipment like forklifts or cranes with lower load capacities. Its high lifting capacity ensures fewer operations are needed to move materials, reducing overall energy consumption.
- Energy Efficiency: The crane uses energy effectively by completing tasks faster and reducing the need for frequent operations.
- Comparison to Other Equipment: While forklifts and smaller cranes may need more frequent lifts to move the same amount of material, the 40-ton crane can achieve the same results in fewer movements, saving energy.
This combination of increased capacity, reduced energy use, and cost savings makes the 40-ton overhead crane a highly efficient choice for steel coil handling in a steel mill.
Safety and Risk Mitigation
Safety Protocols
Regular Maintenance Schedules and Checks:
To ensure the crane operates safely and efficiently, regular maintenance schedules are crucial. These checks include inspecting key components like the hoist, winch, trolley, and lifting mechanisms for wear and tear. Preventative maintenance helps to detect any potential issues before they become serious problems, reducing downtime and the risk of mechanical failure during operation.
- Routine Inspections: Daily checks before operation, including inspecting load-bearing parts, wires, and control systems.
- Scheduled Maintenance: Periodic servicing to maintain peak performance and prolong crane lifespan.
Operator Training and Certification:
Training is essential to ensure crane operators are equipped with the knowledge and skills to operate the crane safely. Operators undergo comprehensive training programs, covering safe handling practices, crane controls, emergency response procedures, and load management. Certification ensures that only qualified personnel operate the crane, reducing the risk of human error.
- Training: Emphasis on safety, proper handling of materials, and emergency protocols.
- Certification: Ensures operators are well-versed in safe crane operation, reducing accidents related to improper use.
Emergency Response Procedures for Crane Malfunction or Accident Scenarios:
In case of crane malfunctions or accidents, clear emergency response procedures must be in place. These procedures include stopping crane operations immediately, notifying supervisors, and performing necessary safety checks. Emergency stop buttons and alarms allow for quick intervention. Additionally, operators are trained to respond swiftly and efficiently to minimize risks to personnel and equipment.
- Emergency Stops: Immediate response to dangerous situations, ensuring the crane halts to prevent further damage.
- Communication: Operators and safety teams are trained to communicate during emergencies to resolve issues quickly.
Risk Mitigation
Prevention of Injuries or Accidents During Crane Operation:
The safety of workers is paramount, and specific measures are put in place to minimize the risk of injury. The crane’s design, including features like anti-collision systems, reduces the likelihood of accidents. Furthermore, safety zones are marked around the crane’s operating area to keep workers at a safe distance.
- Anti-Collision Systems: Prevents accidents by detecting obstacles and stopping the crane automatically.
- Safety Zones: Establishes clear areas for personnel to avoid the crane’s path during operation.
Addressing Challenges Like Load Swinging or Crane Tipping:
Handling heavy and bulky steel coils involves managing potential risks like load swinging or crane tipping. The overhead crane’s design, including its double girder structure, helps maintain stability even with heavy loads. Operators are also trained to control crane movements smoothly to avoid sudden jerks that could cause load instability or crane tipping.
- Load Control: Precise control of the crane helps prevent swinging loads.
- Stability Measures: The design and proper operation ensure the crane remains stable even with large, heavy loads.
Challenges and Solutions
Challenges Encountered
Potential Difficulties in Crane Operation or Maintenance in a Steel Mill Environment:
Operating cranes in a steel mill environment presents several challenges. The environment is often harsh, with high temperatures, dust, and debris, which can affect the crane’s performance and maintenance needs. Furthermore, the crane must operate in tight, congested spaces where maneuvering can be challenging.
- Harsh Conditions: High temperatures, heavy dust, and debris can cause wear and damage.
- Limited Space: Tight spaces can make crane operation more difficult and increase the risk of accidents.
Possible Operational Challenges with Handling Steel Coils, Such as Stability and Weight Distribution:
Steel coils are heavy, bulky, and sometimes irregularly shaped, which can make them difficult to handle. Maintaining load stability is crucial to prevent the crane from tipping or the coils from shifting during transport. The weight distribution of steel coils can also be uneven, requiring careful adjustments to ensure a secure lift.
- Load Stability: Steel coils can shift or roll, posing a risk of load swinging or tipping.
- Uneven Weight Distribution: Some steel coils may not be perfectly balanced, requiring extra caution when lifting.
Solutions and Adjustments
Engineering Solutions or Modifications Made to Improve Crane Performance:
To address these challenges, engineering modifications are made to the crane to improve its performance. This includes adding specialized lifting hooks or slings designed specifically for steel coils, providing better load control. The crane’s anti-collision system can be enhanced to account for the tight spaces in a steel mill.
- Specialized Lifting Equipment: Custom hooks or slings for securing steel coils.
- Enhanced Control Systems: Adjustments to the anti-collision and load control systems for better performance in cramped spaces.
Operational Adjustments to Handle Unique Aspects of Steel Coils (e.g., Size, Weight Distribution):
Operators make specific adjustments during the handling of steel coils to ensure safe and efficient lifting. For example, the crane may need to lift from different angles or adjust its speed to prevent load swinging. Proper load securing techniques, such as using multiple slings or protective pads, can prevent coil damage and improve stability.
- Adjusting Speed and Angles: Operators adjust movement speed and crane angles for stability and precision.
- Secure Load Handling: Multiple slings or custom supports help secure the steel coil and ensure even weight distribution.
By addressing these challenges through both engineering solutions and operational adjustments, the crane operates efficiently and safely, ensuring the reliable handling of steel coils in even the most difficult steel mill environments.
Conclusion
Summary of Key Findings
The 40-ton QD overhead crane has proven to be an invaluable asset in steel coil handling, providing numerous advantages over traditional methods. Its double girder design and open winch trolley ensure superior stability, control, and precision in lifting heavy steel coils. The crane’s 40-ton capacity makes it ideally suited for moving large, heavy loads with ease, which is crucial in the demanding environment of a steel mill.
- Efficiency: The crane has significantly reduced handling times, optimizing both space and time in the warehouse. Its high lifting capacity allows for quick and smooth transport of steel coils, which increases overall throughput and minimizes downtime.
- Safety: The implementation of anti-collision systems, overload protection, and operator training has enhanced workplace safety. The crane’s design and operational features have minimized the risk of accidents, ensuring a safer environment for operators and workers.
- Cost-Effectiveness: By reducing labor costs, improving material handling precision, and decreasing the likelihood of damage to steel coils, the crane has proven to be a cost-effective investment. Energy efficiency also contributes to its overall value, as it consumes less power compared to other handling equipment.
In conclusion, the 40-ton QD overhead crane has delivered outstanding performance in steel coil handling, improving efficiency, safety, and cost-effectiveness. With potential for further improvements and applications, it stands as a critical component in modernizing steel mill operations and enhancing industrial productivity.