Overhead Crane for Brass & Bronze Industry, Custom Crane for You
Comprehensive Guide to Overhead Cranes for Brass and Bronze Industrial Applications
Importance in the Brass and Bronze Industry
In the brass and bronze industry, where the art of metallurgy meets the demands of modern manufacturing, overhead cranes play a pivotal role. These industries deal with non-ferrous metals like copper, zinc, and their alloys, which often come in forms ranging from raw materials to intricate components. Overhead cranes become the linchpin that ensures the seamless flow of these materials throughout the production process.
Why Choose Overhead Cranes?
Why opt for overhead cranes when there are various material handling solutions available? The answer lies in the unparalleled advantages they offer:
- 1. Exceptional Load Capacity: Overhead cranes are capable of handling heavy loads, making them indispensable in the brass and bronze industry where materials can be substantial.
- 2. Precision and Control: These cranes provide precise control over load positioning, enabling the delicate handling required for non-ferrous materials.
- 3. Efficiency: Overhead cranes are designed for efficiency, reducing the time and labor required for material transport and positioning.
- 4. Safety: Safety is paramount, and overhead cranes come equipped with advanced safety features to protect both personnel and materials.
- 5. Versatility: Overhead cranes are versatile and can be tailored to specific industry needs, from foundry operations to clean room manufacturing.
- 6. Space Optimization: They maximize floor space utilization, crucial in facilities where every inch counts.
- 7. Integration: Overhead cranes can seamlessly integrate with other manufacturing processes and automation systems.
- 8. Cost-Effective: Over time, the efficiency and reliability of overhead cranes contribute to cost savings and improved ROI.
As we journey deeper into this comprehensive guide, we'll delve into the different types of overhead cranes, their features, benefits, and their myriad applications in the brass and bronze industry. So, buckle up as we explore how these mechanical marvels empower the world of metallurgy and manufacturing.
Basic Components of Overhead Cranes
To truly understand the marvel that is an overhead crane, it's essential to dissect its anatomy. Overhead cranes are precision-engineered machines comprised of several key components, each with a specific function. Let's take a closer look at these fundamental building blocks:
- A. Bridge - The bridge, often referred to as the "bridge girder," forms the horizontal framework of the overhead crane. It serves as the primary load-bearing structure and runs horizontally along two parallel runways. The bridge is responsible for carrying the hoist and trolley, enabling them to traverse the length of the crane's span.
- B. Hoist -At the heart of every overhead crane lies the hoist, the lifting mechanism responsible for gripping and elevating loads. The hoist is equipped with a drum or a wheel around which the wire rope or chain is wound. This ingenious device converts electrical or manual power into the lifting force required to effortlessly hoist heavy materials.
- C. Trolley -Mounted on the bridge, the trolley is the horizontal movement mechanism that carries the hoist and load. It provides the lateral mobility necessary for precise positioning of the load. Depending on the crane's design, the trolley can move along the bridge through manual operation, electrical power, or a combination of both.
- D. Controls -Controlling the movements of an overhead crane is a task that requires finesse and precision. Crane controls, which can vary from simple push-button pendants to advanced radio remote controls, enable operators to manipulate the hoist's lifting and lowering actions, as well as the trolley's horizontal movement. Modern controls often incorporate automation features, enhancing both safety and efficiency.
Safety Features
Safety is paramount in the world of overhead cranes, and a multitude of safety features are integrated into their design. These include:
- 1. Limit Switches: Prevent over-travel of the crane's movements, ensuring that it stops at designated points.
- 2. Emergency Stop Button: Allows for an immediate halt of crane operations in case of emergencies.
- 3. Load Limiters: Monitor and limit the maximum load capacity to prevent overloading.
- 4. Collision Avoidance Systems: Utilize sensors and alarms to prevent collisions between the crane and obstacles.
- 5. Anti-Sway Control: Minimize load swinging during hoisting and trolley movements for safer and more precise handling.
- 6. Overhead Runway Structure: Engineered to withstand the loads and forces imposed during crane operations.
These components work in harmony to ensure the safe and efficient movement of materials within the brass and bronze industry. From lifting heavy ingots to transporting delicate components, overhead cranes are only as good as the sum of their parts, and each component plays a vital role in their overall functionality.
Types of Overhead Cranes for Brass and Bronze Industrial
In the world of material handling, diversity is the key to versatility. Different applications within the brass and bronze industry call for specialized solutions, and overhead cranes rise to the occasion with a variety of types tailored to specific needs. Let's explore these formidable crane types:

Features:
- Horizontal bridge that moves along parallel runways.
- Can have single or double girders.
- Capable of high load capacity.
Benefits:
- Efficient coverage of large work areas.
- Quick and precise load movement.
- Ideal for handling heavy brass and bronze materials.
Typical Applications:
- Moving raw materials, finished products, and molds within manufacturing plants.
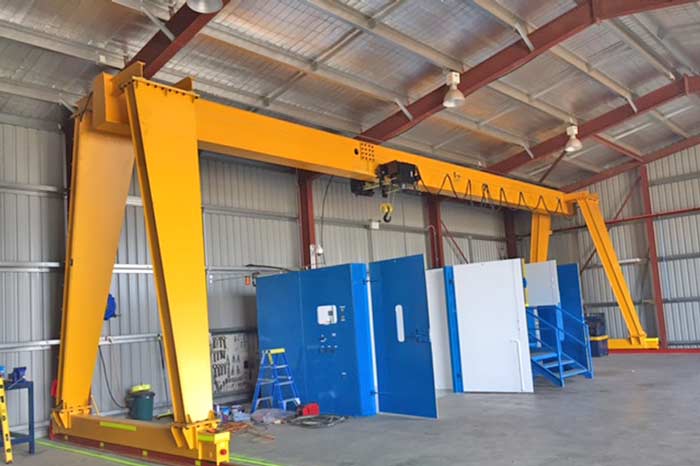
Features:
- Legs or supports on both sides of the bridge.
- Move along rails on the ground.
- Available in single-leg and double-leg configurations.
Benefits:
- Versatile for outdoor and indoor applications.
- Ideal for handling large and irregularly shaped brass and bronze materials.
- Mobility to different locations within a facility.
Typical Applications:
- Handling large components, loading/unloading trucks, and managing outdoor storage.
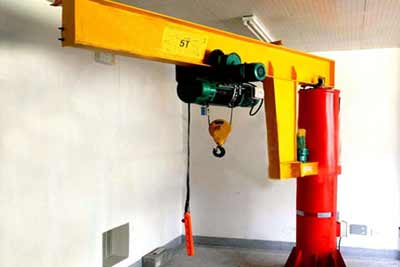
Features:
- Horizontal boom (jib) that can rotate around a vertical column or wall-mounted bracket.
Benefits:
- Precise positioning for lifting and placing materials.
- Space-saving design for smaller work areas.
Typical Applications:
- Lifting and positioning brass and bronze components during manufacturing.
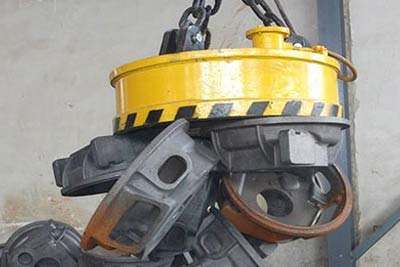
Features:
- Equipped with powerful electromagnets for handling ferrous and non-ferrous materials.
- Ideal for non-magnetic brass and bronze materials.
Benefits:
- Efficient handling of non-ferrous materials.
- Reduced manual labor, enhancing safety and productivity.
Typical Applications:
- Lifting brass and bronze sheets, coils, and components with non-magnetic properties.
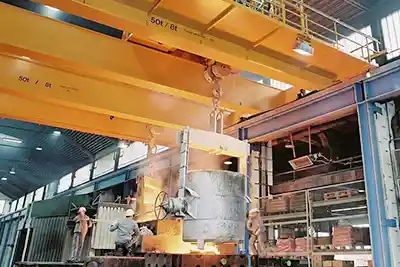
Features:
- Designed for high-heat environments, such as foundries and metal casting facilities.
- Heat-resistant components.
Benefits:
- Operate safely in extreme temperatures.
- Ensure safety for workers in challenging conditions.
Typical Applications:
- Handling brass and bronze ingots, molds, and materials in foundries.
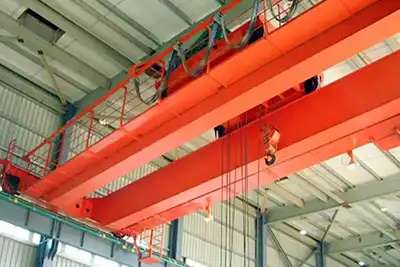
Features:
- Designed for use in environments with flammable gases, dust, or hazardous materials.
- Prevent sparks and electrical faults.
Benefits:
- Safety in hazardous environments.
- Compliance with safety regulations.
Typical Applications:
- Handling brass and bronze materials in areas with flammable substances.
Typical Applications for Overhead Cranes in Brass and Bronze Industry
Overhead cranes are the unsung heroes of the brass and bronze industry, seamlessly weaving their utility into various applications, ensuring the smooth flow of materials and products. Here's a closer look at their typical applications within this dynamic industry:
- 1. Raw Material Handling - - Overhead cranes are essential for unloading raw materials like copper and zinc from trucks and transporting them to storage areas.
- 2. Melting and Alloying - - Overhead cranes play a vital role in moving raw materials to the melting furnaces and carrying alloying elements for the crucial alloying process.
- 3. Casting and Molding - - Foundry cranes are indispensable for transporting molds to casting stations and accurately positioning them for pouring molten brass or bronze.
- 4. Heat Treatment - - Bridge cranes are used to transfer materials to and from heat treatment furnaces or ovens, ensuring proper treatment cycles.
- 5. Machining and Fabrication - - Jib cranes and monorail cranes assist in moving raw materials to machining centers and deliver finished components to inspection and assembly areas.
- 6. Assembly and Inspection - - Jib cranes are instrumental in the assembly of brass and bronze components, and they facilitate efficient inspection processes.
- 7. Storage and Warehousing - - Gantry cranes help organize and move materials within storage facilities or warehouses, optimizing space utilization.
- 8. Shipping and Dispatch - - Bridge cranes are employed for loading finished brass and bronze products onto trucks, shipping containers, or pallets for distribution.
- 9. Maintenance and Repairs - - Jib cranes in maintenance areas assist with lifting and replacing components in machinery and equipment used in the brass and bronze industry.
- 10. Specialized Handling - - Magnetic lifting cranes are tailored for handling non-ferrous materials like brass and bronze sheets and coils.
- 11. Clean Room Manufacturing - - Clean room cranes ensure contamination-free handling of materials in environments with stringent cleanliness requirements, such as electronics manufacturing.
- 12. Automation and Integration - - Automated overhead cranes with robotic controls are at the forefront of automation and integration, facilitating the seamless transfer of brass and bronze components between machining, assembly, and inspection stations.
The brass and bronze industry relies on the versatility and precision of overhead cranes at every stage of the production process. From the handling of raw materials to the assembly of intricate components and the efficient management of storage and shipping, these cranes are the backbone that ensures the industry's success. Whether in traditional manufacturing or cutting-edge automation, overhead cranes continue to shape the landscape of brass and bronze production.
Industrial Requirements for Overhead Cranes
When considering the use of overhead cranes in the brass and bronze industry, it's essential to align your crane selection with specific industrial requirements. Let's explore these crucial requirements in detail:
- 1. Load Capacity - Determine the maximum load capacity your overhead crane needs to handle, factoring in the heaviest materials or components used in your processes. It's critical to choose a crane that can safely manage these loads.
- 2. Material Compatibility - Ensure that the crane's design and components are compatible with the materials you work with, especially considering non-ferrous metals like brass and bronze. Certain materials may require specialized lifting attachments or precautions to prevent damage.
- 3. Environmental Conditions - Evaluate the environmental conditions in your facility. Consider factors such as temperature extremes, humidity, and exposure to corrosive substances, as these can impact crane performance and longevity.
- 4. Safety Regulations - Adherence to safety regulations is non-negotiable. Ensure that the overhead crane you choose complies with local, national, and industry-specific safety standards. This includes features like limit switches, emergency stops, and load limiters.
- 5. Space and Layout - Assess your facility's layout and available space. Optimize crane design and positioning to maximize space utilization and ensure that the crane can access all necessary work areas.
- 6. Automation and Integration - Determine if you require automation and integration capabilities for your processes. Automated cranes with robotic controls can streamline operations and enhance efficiency, particularly in high-throughput manufacturing.
- 7. Energy Efficiency - Consider the energy efficiency of the crane, especially if you plan to use it extensively. Energy-efficient features can reduce operational costs over time. Look for regenerative braking, variable frequency drives, and other energy-saving technologies.
- 8. Operator Training - Proper operator training is essential for safe crane operation. Ensure that your operators receive comprehensive training to handle the crane efficiently and safely. Training should cover both routine operations and emergency procedures.
- 9. Remote Control and Safety Features - Evaluate the availability of remote control options for your crane. Remote controls can enhance safety by allowing operators to maintain a safe distance during certain operations. Additionally, look for advanced safety features like collision avoidance systems and anti-sway controls.
- 10. Customization - Understand that one-size-fits-all solutions may not suit your specific needs. Explore customization options to tailor the crane to your industry's unique requirements, whether it's special attachments, additional safety features, or specific controls.
By addressing these industrial requirements, you can make an informed decision when selecting an overhead crane for your brass and bronze manufacturing facility. Each requirement plays a vital role in ensuring the safe, efficient, and productive use of overhead cranes in your operations, ultimately contributing to the success of your business.
Top Concerns of Overhead Crane Users
Users of overhead cranes in the brass and bronze industry are no strangers to the challenges and concerns that come with operating these critical pieces of equipment. Here are the top concerns that weigh on their minds:
- 1. Safety: Ensuring Safe Operation - Safety is paramount. Users are concerned about preventing accidents, ensuring operator training, and implementing safety features to protect both personnel and materials.
- 2. Maintenance: Keeping Cranes in Optimal Condition - Proper maintenance is essential for crane longevity and performance. Users are focused on routine inspections, repairs, and preventive maintenance to minimize downtime and maximize reliability.
- 3. Efficiency: Enhancing Productivity - Productivity is a constant goal. Users seek ways to optimize crane operations, reduce material handling time, and streamline processes for increased efficiency.
- 4. Compliance: Meeting Regulatory Standards - Staying compliant with safety and environmental regulations is a top priority. Users are concerned with adhering to local, national, and industry-specific standards.
- 5. Space Constraints: Maximizing Space Utilization - Facility layouts often have limited space. Users work to maximize the use of available space, ensuring that cranes can access all necessary areas without congestion.
- 6. Material Compatibility: Handling Non-Ferrous Materials - Dealing with non-ferrous materials like brass and bronze presents unique challenges. Users need to ensure that their cranes are equipped for the safe and efficient handling of these materials.
- 7. Cost-Effectiveness: Balancing Costs and Benefits - Balancing the costs of crane acquisition, operation, and maintenance with the benefits they provide is a constant concern. Users aim to achieve the best ROI while meeting operational needs.
- 8. Integration: Seamless Process Integration - Integrating cranes into the broader manufacturing process is critical for efficiency. Users are concerned with seamless integration, especially when implementing automated systems.
- 9. Downtime: Minimizing Production Disruptions - Downtime is costly. Users strive to minimize disruptions caused by crane maintenance, repairs, or unexpected breakdowns to keep production running smoothly.
Addressing these concerns requires a combination of proper planning, regular maintenance, safety protocols, operator training, and strategic investment decisions. Overcoming these challenges allows overhead crane users in the brass and bronze industry to optimize their material handling processes and maintain a competitive edge in the market.
Frequently Asked Questions (FAQs)
In the world of overhead cranes for the brass and bronze industry, questions often arise. Here are some frequently asked questions and their informative answers:
Q1. What load capacity do I need for handling brass and bronze materials?
A: The load capacity depends on the weight of the heaviest brass or bronze materials or components you intend to handle. Ensure your crane's capacity exceeds this maximum load to ensure safe operations.
Q2. Are there special considerations for handling non-ferrous materials?
A: Yes, non-ferrous materials like brass and bronze require special handling to prevent damage. Consider cranes with features like magnetic lifting cranes or custom lifting attachments designed for non-magnetic materials.
Q3. How do I choose the right type of overhead crane for my facility?
A: Selecting the right crane type depends on factors like load capacity, material compatibility, available space, and specific applications. Consult with crane experts to determine the most suitable type for your needs.
Q4. What safety features should I look for in an overhead crane?
A: Look for safety features such as limit switches, emergency stop buttons, load limiters, collision avoidance systems, and anti-sway controls to enhance crane safety.
Q5. How can I optimize energy efficiency in crane operations?
A: Opt for cranes with energy-efficient features like regenerative braking and variable frequency drives. Ensure operators follow energy-saving practices, such as avoiding unnecessary idling.
Q6. What are the key maintenance practices for overhead cranes?
A: Regular inspections, lubrication, and preventive maintenance are crucial. Keep a maintenance schedule and address any issues promptly to prevent breakdowns and downtime.
Q7. Can overhead cranes be customized for specific needs?
A: Yes, overhead cranes can be customized with features like special lifting attachments, automation controls, or additional safety measures to meet specific requirements.
Q8. What are the benefits of using automated overhead cranes?
A: Automated overhead cranes improve precision, efficiency, and integration with other processes. They reduce manual labor, enhance safety, and streamline material handling operations.
Q9. How can I ensure compliance with safety regulations?
A: Stay informed about local, national, and industry-specific safety regulations. Choose cranes that meet or exceed these standards and ensure that operators are trained in compliance with safety protocols.
These FAQs offer valuable insights into the world of overhead cranes in the brass and bronze industry, addressing common concerns and helping users make informed decisions for their material handling needs.
Conclusion
In the realm of brass and bronze manufacturing, where precision, efficiency, and safety are paramount, overhead cranes stand as indispensable allies. Their role in the brass and bronze industry is nothing short of transformative, shaping the way materials are handled, processed, and crafted into intricate components.
The Role of Overhead Cranes in Brass and Bronze Manufacturing
Overhead cranes are the unsung heroes that facilitate the smooth flow of materials, from the arrival of raw copper and zinc to the meticulous assembly of finished products. These mechanical marvels handle the heat of foundry operations, navigate through intricate machining processes, and ensure that every component meets stringent quality standards.
From the towering bridge cranes with their heavy load capabilities to the nimble jib cranes offering precise positioning, the diverse types of overhead cranes cater to the specific needs of the industry. Magnetic lifting cranes delicately handle non-ferrous materials, while clean room cranes maintain sterile environments. Automation and integration capabilities take manufacturing to new heights, improving efficiency and productivity.
Making Informed Decisions for Your Material Handling Needs
Selecting the right overhead crane for your brass and bronze manufacturing facility is not merely a choice; it's a strategic decision. Understanding load capacities, material compatibility, safety regulations, and customization options is vital. Efficiency, compliance, and cost-effectiveness all play a role in optimizing operations and achieving the best return on investment.
While concerns such as safety, maintenance, and space constraints may be ever-present, users of overhead cranes in the brass and bronze industry navigate these challenges with expertise and diligence. Through proper planning, operator training, and adherence to safety protocols, these concerns can be managed effectively.
In closing, overhead cranes are more than machines; they are the backbone of an industry that fuses craftsmanship and metallurgy. They empower manufacturers to create the intricate and enduring products that define the world of brass and bronze manufacturing. By embracing the knowledge and insights shared in this comprehensive guide, users can harness the full potential of overhead cranes, ensuring their success in the vibrant and dynamic world of brass and bronze production.