Double Girder Overhead Crane for Steel Rolling Mill
Double girder eot cranes processed for steel mill to improve your efficiency & safety. Hot & cold steel rolling cranes overview for your reference. Check now.
Rolling mills and EOT cranes
At Yuantai Crane, we take pride in our ability to provide industry-leading fabrication, maintenance and installation services for a wide range of material handling and overhead equipment applications.
Rolling mills
Rolling mills produce hot steel of all types and shapes. In these complex production systems, intermediate steel products undergo forming and finishing processes to obtain their final shape and dimensions. Wire rods, bars, angles, C-sections, beams, flat parts and plates, beams as well as heavy and light steel sections are produced in the rolling mill.
According to the steelmaking process, rolling mills can be divided into hot rolling mills and cold rolling mills. In most cases, billets are heated in furnaces and rolled into shape in finishing mills, hot rolling mills or cold rolling mills. In some applications, steel must be hot and cold rolled.
Double girder overhead crane for steel rolling mills
Hot rolling mill
In hot rolling milling, the Hot-rolled steel is steel that has undergone a rolling process at temperatures above its recrystallization temperature, typically 1700°F or higher. Compared with unprocessed steel, the processed material has better formability and machinability, which makes it easier to process in subsequent processing operations.
The hot rolling process starts with a large rectangular sheet of metal called a billet. First, the ingot is heated and pressed into a large roll. While still hot, it passes through a series of rotating rollers to achieve the desired size. In sheet metal production, the rolled steel is then rolled into coils and cooled. During the production of other shapes, the processed material is cut into predetermined units and packaged.
Cold rolling mill
In cold rolling mill, the Cold-rolled steel is steel that has been hot-rolled, but it has then received additional processing that enhances its dimensional and mechanical properties. During the process of cold rolling, hot rolled steel is cooled, then passes through a second series of rollers at room temperature. Because the material is no longer malleable and hot, a larger amount of pressure is needed to compress it into a desired shape. This procedure is more time-consuming and expensive than hot rolling, but it can produce tighter dimensional specifications and a more favorable surface quality.
Hot Rolled Steel vs. Cold Rolled Steel
As previously mentioned, the temperature at which they are processed is the primary distinction between hot rolled steel and cold rolled steel. In contrast to cold rolled steel, which is rolled below the material's recrystallization temperature, hot rolled steel is rolled above the temperature at which the material recrystallizes. Beyond this characteristic, there are a few further differences between the two materials, such as the following:
Items |
Hot Rolled Steel |
Cold Rolled Steel |
Surface quality. |
|
|
Surface quality/ Material hardness |
Lower strength and hardness |
higher strength and hardness |
Internal stress. |
Lower material strength and hardness |
greater material strength and hardness |
Features |
Since hot rolled steel shrinks slightly during the cooling stage, there is a lesser degree of control over its final shape. |
tighter tolerances and better surface finishes |
Applications |
|
|
Depending on the application, manufacturers use different types of rolling mills, including:
- TMT Bar Mills: These mills produce TMT bars and rods and deformed bars for the construction industry.
- Structural rolling mills: Structural rolling mills use steel ingots and billets as raw materials to produce I-beams (beams), U-beams, angle steels, T-beams, flat bars, round bars, etc.
- Light Section Mills: These mills use rolled billets, ship plates and ingots as raw materials to produce smaller components such as sprue channels, square and round sections, flat products, Z-sections, T-sections, channels, 6 mm rods and 8 mm rods.
Double Girder overhead cranes for rolling mills
Rolling mills require the most reliable and highest quality overhead material handling crane solutions available, as cranes in these environments must be able to travel long distances at high speeds, handle extreme temperatures, and handle loads of different shapes and sizes. Therefore, for steel rolling mills, the double girder overhead cranes and bridge cranes are widely used.
Cold/Hot Rolling Mill Overhead Crane
- Lifting Capacity:10 ton, 20 ton, 30 ton, 50 ton, up to 100 ton
- Span:10-40m
- Lifting Height:12-25m
- Steel Track Recommended:QU80
- Working Class:M5-M8
- Power Supply:Three-phase A.C.380v 50Hz or Customized
Steel Rolling Mill Overhead Crane is a heavy duty double girder open winch overhead crane that is used for handling various steel products such as, steel billet, slab and ingot, and coil, etc. Because of the large range of materials they must handle, a heavy duty open winch overhead crane can be outfitted with a number of lifting devices that vary depending on the material. This sort of overhead crane is seen in pickling sheds, cold rolling sheds, rewinding sheds, annealing sheds, and storage bays, among other places.
Why to use double girder overhead crane for your rolling mill?
The overhead crane in a cold/hot rolling mill is critical to the steel-making process.They are used to load and unload items quickly and safely, and they keep trucks moving throughout the plant. The double girder cranes are also used to transport scrap or raw materials, liquid metal, and melting buckets. The open winch cranes are totally integrated into the processes of a steel mill to ensure smooth operation of the whole processing line.
Custom rolling mill cranes improves your efficiency & safety
Hot steel in rolling mills requires high-performance handling and transport machinery. These slabs and billets must frequently be moved at extremely high temperatures with great reliability in order to remain flexible.EOT cranes, or electric travelling bridge cranes, are important to this procedure.
The slabs and billets that emerge from the melting process are white-hot and flexible. They may be rolled into any shape needed using rolling presses. This is sometimes done right away. They are sometimes kept in a storage area to be processed later. Because the melt shop environment is so dangerous, the presses are normally located some distance away. The double girder steel mill cranes are required to transport the cooling-but-still-hot, flexible shapes from the casting to the rolling mill.


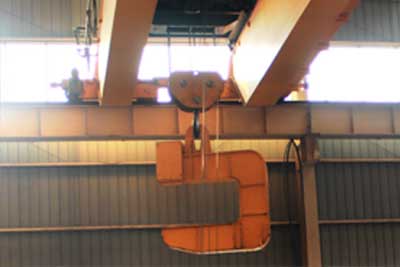

Main functions of rolling mill overhead cranes
Moving hot metal
A billet or slab crane is a processed double girder electric overhead crane. It must travel the considerable distance between the melting shop and the rolling region. If necessary, it can transport the hot, soft metal from the casting area to storage. When necessary, it should be able to feed billets or slabs into the rollers. Before shaping can begin, the steel may need to be reheated in another furnace. The same crane can transport the shaped steel to another conveyor for additional processing or to a storage facility.
Load-handling equipment of all shapes and sizes
Because of the enormous range of products and forms that come off the rollers, the double girder overhead cranes require unique load management gear. Slabs can be picked up using mechanical or hydraulic tongs, slabs, billets, or coils with magnets, and coils and smaller billets with c-hooks. There is some radiated heat since the steel needs to be warm for shaping, and the grips require heat protection.
- Sensitive Positioning and Load Handling: Due to limited production floor area, efficient mobility is required. Reliable cranes assist operators in making the most of their work areas by assisting in the proper placing of steel on conveyors and the safe handling of a wide range of metal products that travel through the shop, such as slabs, billets, and coils.
- The most popular form of overhead crane is the double girder EOT crane, which can be found in almost any factory; their electric operation is controlled by a pendant, operator cabin, or radio/IR remote. Double beam/girder bridge cranes provide additional support for the trolley and hoist when lifting 20 tons or more. When the bridge girders are riding on top of the runway beams, these cranes are said to be "top running."
Features help make hard tasks easier
Heavy duty slab or billet cranes are frequently outfitted with Smart Features like as Sway Control, Slack Rope Prevention, and Target Positioning. These Smart Features help your crane last longer by reducing wear and tear and cutting unforeseen repair and maintenance expenditures. They also make it easier for drivers to do tough tasks, allowing the crane to perform better. These cranes can even be fully automated, advancing your factory that much farther.
- The heavy duty open winch overhead crane height is low, which can significantly increase the plant's space use rate.
- Bridge machines can be used on a variety of sites, allowing both to be situated symmetrically within the plant as needed to maximize the scope of operation.
- Sturdy structure, light dead weight, adequate bearing capacity, and low foundation dead weight.
- Reliable and safe, with a low failure rate and a low daily maintenance workload.
- The electrical control is sophisticated and dependable, resulting in outstanding overall system performance.
Rolling Mill Double Girder EOT Cranes from Yuantai Crane
Yuantai Crane is willing to offer industry-leading material handling overhead crane solutions that improve worker safety, efficiency, and convenience of use. We provide a variety of services and products, such as bridge cranes, gantry cranes, jib cranes, and various processed crane for wide indusrtial uses, and the replacement parts and components, equipment rebuilds, emergency repair, and in-house manufacturing and engineering assistance. If you have any need of rolling mill crane or services, please feel free to contact us.