Crane Hoist for Sale: Different Types of Hoists Used in Crane Systems
Crane hoist for sale 1 ton to 80 ton. Various cran hoist types used in crane systems, highlighting their functions, applications, and advantages in different industrial settings.
Overview of Crane Systems
Crane systems are vital mechanical devices used for lifting and moving heavy loads in various industries, including construction, manufacturing, and shipping. They consist of multiple components, such as the crane structure, hoist, and controls, all working together to ensure safe and efficient operations. Cranes can range from small portable units to large fixed installations, depending on the specific requirements of a project. Their ability to handle significant weights makes them essential for tasks like loading trucks, erecting buildings, and transporting materials across sites. The versatility of crane systems helps streamline workflows, reduce manual labor, and improve productivity.
Role of Hoists in Crane Operations
Hoists are crucial elements within crane systems, responsible for lifting and lowering loads. They work by using a combination of mechanical components, such as pulleys, chains, or ropes, powered by electric motors or manual effort. Hoists can vary in design and functionality, but their primary purpose remains the same: to provide a safe and reliable means of moving heavy items. By integrating hoists into crane operations, businesses can enhance efficiency, as hoists allow for quick adjustments in load height and positioning. The right hoist contributes significantly to overall safety, ensuring that materials are handled securely and minimizing the risk of accidents. Understanding the role of hoists is essential for selecting the appropriate equipment for specific tasks, ultimately leading to smoother and safer operations.
Types of Crane Hoists
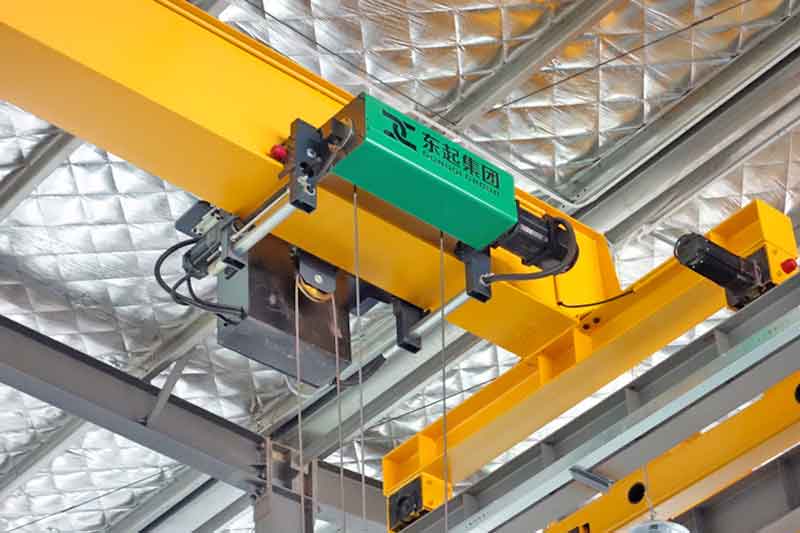
Electric Hoists
- Description and Mechanism
Electric hoists operate using an electric motor to lift and lower loads. They typically feature a drum or a chain where the lifting medium (rope or chain) is wound. When powered on, the motor turns the drum, allowing the hoist to raise or lower the load efficiently. Many electric hoists come with controls that enable precise handling and movement, making them user-friendly for operators. - Applications
Electric hoists are widely used in various industries, including construction, manufacturing, and warehousing. They are ideal for tasks such as lifting heavy machinery, loading and unloading materials, and moving components along assembly lines. Their ability to handle heavy loads with ease makes them a popular choice in environments where efficiency is crucial. - Advantages and Disadvantages
Advantages: Electric hoists are known for their speed and efficiency, making them suitable for high-frequency lifting tasks. They require less physical effort from operators and can lift heavier loads compared to manual hoists. Additionally, their automated controls allow for precise positioning.
Disadvantages: On the downside, electric hoists depend on a power source, which may limit their use in areas without electrical access. They can also be more expensive to purchase and maintain than manual alternatives.
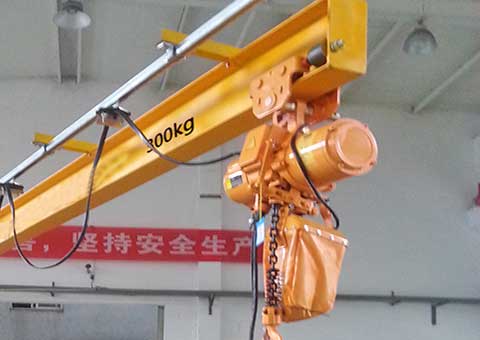
Chain Hoists
- Description and Mechanism
Chain hoists use a system of chains and gears to lift loads. When the operator pulls on the chain, it engages the gears, causing the load to rise. These hoists can be either manual or powered, with manual versions relying entirely on human effort to lift and lower loads, while powered versions use electricity or air. - Applications
Chain hoists are commonly found in construction sites, factories, and maintenance workshops. They are particularly useful for lifting heavy materials, such as beams or equipment, in tight spaces where larger cranes might not fit. Their versatility makes them a go-to option for various lifting needs. - Advantages and Disadvantages
Advantages: Chain hoists are robust and can handle substantial weights, making them suitable for heavy-duty applications. They are also relatively simple in design, which often translates to lower maintenance costs. Manual chain hoists, in particular, are portable and can be used in locations without electricity.
Disadvantages: However, the manual operation can be physically demanding, especially for heavier loads, which may limit their efficiency in high-volume applications. Additionally, the lifting speed is generally slower compared to electric hoists, potentially impacting productivity in time-sensitive tasks.
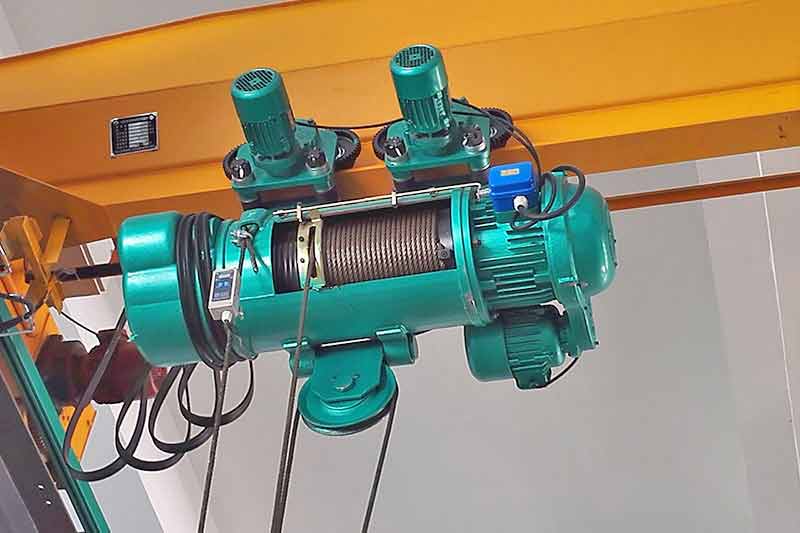
Wire Rope Hoists
- Description and Mechanism
Wire rope hoists utilize a strong steel wire rope wound around a drum to lift and lower loads. The mechanism involves an electric or manual motor that rotates the drum, allowing the wire rope to extend or retract as needed. This design provides smooth and efficient operation, making wire rope hoists suitable for various heavy lifting tasks. - Applications
Wire rope hoists are commonly used in construction, manufacturing, and shipping industries. They excel in environments that require lifting heavy loads over significant heights, such as warehouses, shipyards, and industrial facilities. Their design also makes them effective for applications involving overhead cranes and large machinery. - Advantages and Disadvantages
Advantages: One of the main strengths of wire rope hoists is their high load capacity, making them ideal for heavy-duty applications. They also offer excellent lifting speed and precision, which can enhance productivity. Additionally, the wire rope design reduces wear and tear, contributing to a longer lifespan.
Disadvantages: On the downside, wire rope hoists can be more complex to maintain than other types, as they require regular inspection of the wire rope for wear. They may also be heavier and less portable than chain or manual hoists, limiting their use in tight or temporary spaces.
Manual Hoists
- Description and Mechanism
Manual hoists operate through human effort, using a system of chains or ropes that the operator pulls to lift loads. These hoists typically feature a simple design, allowing for easy handling and operation without the need for electricity or complex controls. Manual hoists can be chain-driven or lever-operated, providing versatility in how they are used. - Applications
Manual hoists are ideal for smaller operations or areas with limited access, such as garages, workshops, and construction sites. They are particularly useful for tasks that require occasional lifting of lighter loads, such as hanging tools, lifting equipment, or moving materials in tight spaces. - Advantages and Disadvantages
Advantages: The primary benefit of manual hoists is their portability and ease of use. They are often less expensive than powered alternatives and do not require a power source, making them versatile in various locations. Additionally, they are straightforward to maintain, with fewer components that could fail.
Disadvantages: However, manual hoists can be physically demanding, especially when lifting heavier loads, which may limit their efficiency in high-volume tasks. Their lifting speed is typically slower than that of electric hoists, making them less suitable for time-sensitive operations.
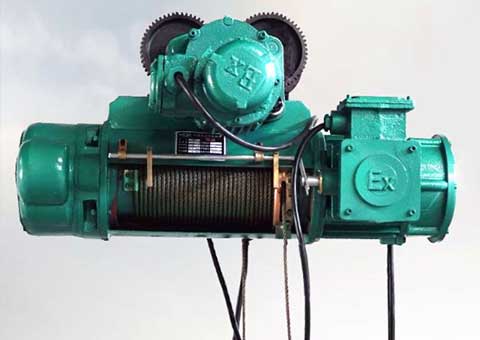
Explosion-Proof Hoists
- Description and Mechanism
Explosion-proof hoists are specifically designed to operate safely in environments where flammable gases, vapors, or dust may be present. These hoists feature robust enclosures that prevent sparks or hot surfaces from igniting hazardous materials. They often utilize special motors and electrical components that comply with strict safety standards, ensuring reliable performance in volatile settings. - Applications
These hoists are commonly used in industries such as oil and gas, chemical manufacturing, pharmaceuticals, and mining. Environments like refineries, grain storage facilities, and paint shops benefit from explosion-proof hoists, where the risk of explosions or fires is significant. Their design allows for safe lifting and movement of materials in these high-risk areas. - Advantages and Disadvantages
Advantages: The primary advantage of explosion-proof hoists is their safety in hazardous environments, allowing for efficient operations without the risk of ignition. They are built to withstand harsh conditions and typically have long service lives. Their specialized design enables compliance with industry regulations, which is crucial for operational integrity.
Disadvantages: However, explosion-proof hoists can be more expensive than standard hoists due to their specialized components and construction. They may also be heavier and bulkier, which can limit their portability. Additionally, maintenance and inspections may require specific expertise to ensure ongoing compliance and functionality.
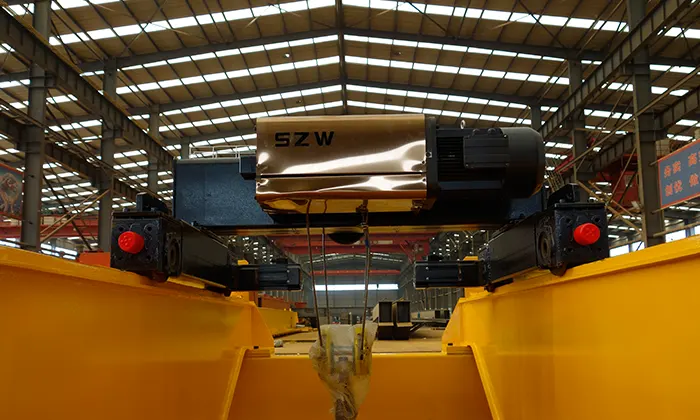
Low Headroom Hoists
- Description and Mechanism
Low headroom hoists are designed for environments with limited vertical space, allowing for efficient lifting without requiring excessive height. These hoists typically feature a compact design, which includes a low-profile trolley and a unique lifting mechanism that maximizes the available headroom. This setup enables them to operate effectively in tight areas, such as under beams or ceilings. - Applications
Low headroom hoists are commonly used in warehouses, factories, and maintenance facilities where space constraints are a concern. They are particularly useful in applications like lifting equipment, moving materials in confined spaces, and supporting assembly lines. Their ability to fit into low-clearance areas makes them ideal for maximizing vertical lifting capabilities in various industrial settings. - Advantages and Disadvantages
Advantages: The main advantage of low headroom hoists is their ability to operate in areas where standard hoists would not fit, thus optimizing space utilization. They often provide smooth lifting and lowering operations while maintaining safety. Additionally, their compact design can enhance maneuverability in tight work environments.
Disadvantages: On the downside, low headroom hoists may have lower load capacities compared to standard hoists, limiting their use for heavier applications. They can also be more complex in design, which may lead to increased maintenance requirements. Furthermore, their specialized features can result in higher costs compared to conventional hoists.
Key Features of Hoists
Load Capacity
- Definition and Importance
Load capacity refers to the maximum weight a hoist can safely lift. It is a critical factor in selecting the right hoist for a specific application, as using a hoist beyond its rated capacity can lead to equipment failure and serious safety hazards. Understanding load capacity helps ensure that operations remain efficient and safe, preventing accidents and damage to materials or machinery. - Common Load Ratings
Different types of hoists come with varying load capacities. For example, manual chain hoists often have capacities ranging from 0.5 tons to 10 tons, while electric hoists can handle loads from 1 ton to over 50 tons. Wire rope hoists typically support heavier loads, often exceeding 100 tons, making them suitable for industrial applications. Knowing the typical capacities allows operators to choose the right hoist for their specific lifting needs.
Lifting Speed
- Impact on Efficiency
Lifting speed is the rate at which a hoist can raise or lower a load. Higher lifting speeds can significantly enhance operational efficiency, allowing tasks to be completed faster. In busy environments, such as manufacturing or construction sites, the ability to lift and move materials quickly can improve overall productivity and reduce downtime. - Comparison of Hoist Types
Lifting speeds can vary widely among hoist types. Electric hoists typically offer the fastest lifting speeds, often ranging from 10 to 30 feet per minute. Pneumatic hoists also provide good speed but may not match the higher-end electric models. Manual hoists generally have the slowest lifting speeds, as they rely on human effort. This comparison helps businesses select a hoist that aligns with their operational requirements.
Safety Features
- Critical Safety Mechanisms
Safety features are essential for protecting both operators and equipment. Standard mechanisms include overload protection, which prevents the hoist from lifting loads beyond its capacity, and emergency stop buttons that allow for immediate cessation of operation. Other safety features may include limit switches to prevent over-travel and mechanical brakes to secure loads when not in motion. - Regulatory Compliance
Meeting industry safety standards is crucial for hoists and their operators. Regulatory bodies often set guidelines for hoist design, testing, and operation to ensure safe practices. Compliance with these regulations not only protects workers but also helps organizations avoid legal liabilities and promotes a culture of safety within the workplace.
Choosing the Right Hoist for Your Needs
Assessing Operational Requirements
- Load Characteristics
When selecting a hoist, it's essential to analyze the weight, size, and shape of the loads you'll be handling. Different hoists have varying load capacities and designs suited for specific shapes or dimensions. Understanding these characteristics helps ensure that the hoist can safely and efficiently manage the intended materials, preventing potential hazards and operational inefficiencies. - Work Environment
Evaluating the work environment is crucial in making an informed decision. Consider factors such as available space, accessibility, and specific conditions like temperature and humidity. For instance, outdoor environments may require weather-resistant hoists, while indoor settings might prioritize compact designs for tight areas. Assessing these conditions ensures that the selected hoist will perform optimally in its intended setting.
Cost Considerations
- Initial Investment vs. Long-term Costs
Cost is a significant factor when choosing a hoist. While the initial purchase price is important, it's equally vital to consider long-term costs, including maintenance, operation, and potential downtime. Analyzing these aspects can help identify the most cost-effective solution. Sometimes, a higher initial investment in a durable, reliable hoist can lead to lower overall costs through reduced maintenance and longer service life.
Manufacturer Recommendations
- Researching Reliable Brands
Selecting a hoist from an established manufacturer is crucial for ensuring quality and reliability. Researching reputable brands can provide insights into product performance, safety features, and customer support. Established manufacturers often have a proven track record and adhere to industry standards, which can be invaluable when making a purchase. Prioritizing brands with positive reviews and comprehensive warranties can help secure a hoist that meets your operational needs effectively.
Maintenance and Safety Practices
Regular Maintenance Protocols
Routine Inspections
Regular maintenance is crucial for the longevity and safe operation of hoist systems. Implementing a structured maintenance schedule can prevent costly downtimes and enhance safety.
Visual Inspection:
- Check cables, chains, and hooks for signs of wear, fraying, or deformation.
- Inspect the hoist body for cracks, rust, or any visible damage.
- Ensure that the lifting mechanism operates smoothly without unusual sounds.
Load Testing:
- Perform load tests monthly or quarterly, depending on usage.
- Use a certified test weight to verify that the hoist can handle its rated capacity safely.
- Document all load test results for compliance and future reference.
Lubrication:
- Regularly lubricate moving parts according to the manufacturer’s guidelines.
- Use appropriate lubricants to reduce friction and prevent wear.
- Check lubrication points during each inspection to ensure they are not clogged.
Electrical Checks:
- Inspect wiring, connectors, and electrical components for signs of wear or corrosion.
- Test the functionality of all controls and emergency stop buttons.
- Schedule an electrician to check for any potential electrical hazards annually.
Safety Features:
- Ensure all safety mechanisms, such as limit switches and overload protection, are operational.
- Test emergency stops and alarms during routine inspections.
- Replace any malfunctioning safety components immediately.
Common Maintenance Issues
Being aware of common maintenance issues can help mitigate risks and ensure smooth operation.
Worn Cables or Chains:
- Look for signs of wear, such as kinks or fraying in cables.
- Replace worn cables or chains promptly to avoid failure during operation.
Loose Connections:
- Check all bolts, screws, and connectors to ensure they are tight and secure.
- Use a torque wrench to verify that all fasteners are within the manufacturer's specifications.
Corrosion:
- Inspect hoists in outdoor or humid environments for rust.
- Apply protective coatings or treatments to prevent corrosion on metal components.
Electrical Malfunctions:
- Be vigilant for unusual noises, flickering lights, or operational inconsistencies.
- Address any signs of electrical issues immediately to prevent accidents.
Safety Practices in Operation
Training Requirements
Comprehensive training is essential for operators to ensure safe and efficient hoist usage.
Understanding Hoist Functionality:
- Operators should receive training specific to the hoist model they will be using.
- Familiarize them with controls, indicators, and safety features.
Load Handling Techniques:
- Train operators on how to assess load weight, size, and shape.
- Teach proper techniques for securing loads to avoid shifting during lifting.
- Emphasize the importance of never exceeding the hoist’s rated capacity.
Safety Procedures:
- Educate operators on personal protective equipment (PPE) requirements, such as hard hats and gloves.
- Ensure they understand the importance of maintaining a clear area around the hoist during operation.
Emergency Procedures
Establishing clear emergency protocols is vital for effective response during incidents.
Immediate Actions:
- Operators should know how to quickly stop the hoist and secure the load if a malfunction occurs.
- Establish a clear procedure for safely lowering the load in the event of a power failure.
Communication Protocols:
- Ensure all team members know how to communicate during an emergency.
- Designate a safety officer or supervisor responsible for coordinating responses.
Regular Drills:
- Conduct emergency drills regularly to familiarize operators with procedures.
- Review lessons learned from drills and update procedures as needed.
Review and Update Plans:
- Regularly review emergency procedures to account for changes in equipment or operational environments.
- Keep emergency contact numbers and procedures visibly posted in work areas for quick access.
Conclusion
In this guide, we explored various types of hoists, including electric, chain, wire rope, manual, pneumatic, and explosion-proof hoists. Each type serves distinct purposes across different industries, from heavy lifting in manufacturing to safe operations in hazardous environments. Understanding the specific applications and mechanisms of each hoist type helps users choose the most appropriate equipment for their needs, ensuring both effectiveness and safety in their operations.
Selecting the right hoist is crucial for maintaining operational safety and efficiency. Factors such as load characteristics, work environment, and cost considerations play significant roles in this decision-making process. Additionally, regular maintenance and operator training are vital to ensure that hoists perform reliably and safely. By prioritizing these aspects, organizations can enhance their lifting operations, minimize risks, and promote a culture of safety within the workplace.