Automated 55 Ton Overhead Crane for Lid Operations
Background of Automated 55 Ton Overhead Cranes
Background of Automated 55 Ton Overhead CranesThis project focuses on automating a 55-ton bridge crane to operate in a complex industrial environment. The crane is specifically built to handle a task that requires high precision—opening and closing the lids of sealed containers. These containers are critical in industries such as manufacturing and logistics, where safe and efficient handling of materials is essential.
Automation in Material Handling Automation is increasingly important in industrial operations. It boosts efficiency by speeding up processes and reduces the risk of human error. In this project, the goal is to automate the lid-opening process. By doing so, we aim to:
- Reduce the need for manual labor
- Increase the overall efficiency of the operation
- Improve safety by minimizing human involvement in potentially hazardous tasks
As industries continue to look for ways to improve production, automation helps maintain high performance and allows businesses to meet growing demands. With this automated crane, the operation becomes faster, more consistent, and safer, which is a significant improvement over traditional manual methods.
Objective The primary objective of this project is to design, install, and integrate a 55-ton automated overhead crane that can efficiently handle the opening and closing of sealed container lids. This automation will streamline operations in a high-capacity industrial environment.
Key Features of the Project:
- Automation of Lid Operations: The crane will be programmed to automate the task of opening and closing sealed container lids, which is typically done manually. This reduces labor costs and improves operational efficiency.
- Integration with Existing Systems: The crane will be integrated with existing equipment and control systems at the site to ensure seamless operation within the industrial workflow.
- Safety Enhancements: Automation reduces the risk of human error and ensures safer working conditions by minimizing human involvement in high-risk tasks.
- Improved Efficiency: The automated crane will operate with higher precision and speed, improving overall productivity and reducing downtime.
This project aims to elevate operational and safety standards while optimizing efficiency and reducing manual labor, making it a crucial step in advancing industrial automation at the site.
Project Objectives
Key Goals of the Automation Design
- Enhancing Operational Efficiency: The automation system is designed to streamline the lid-opening and closing tasks, ensuring precise control over every lifting and closing action. By eliminating manual errors and improving precision, the crane operates at maximum efficiency, minimizing downtime and boosting productivity.
- Reducing Labor Costs and Human Error: Automating the operation significantly reduces the need for manual labor, which is often associated with human errors. These errors can cause delays, safety concerns, and costly operational inefficiencies. With automation, these issues are mitigated, leading to smoother operations.
- Improved Consistency: Automation guarantees that every lid-opening action is performed to the same high standards, ensuring uniformity and reliability. The system can handle sealed containers with accuracy, consistently positioning lids with precision, and avoiding variations in performance.
Specific Requirements
- 55-Ton Capacity: The crane is designed with the capability to handle up to 55 tons of weight. This is essential due to the heavy-duty nature of the container lid operations, where each lid and its surrounding infrastructure can be significantly heavy.
- Automated Operation: The crane must operate autonomously, with the ability to automatically open and close container lids based on pre-set commands. It needs to be integrated with the site’s control systems to perform these tasks efficiently without manual intervention, ensuring a smooth and safe operation throughout.
Design and Automation Solution
Crane Design OverviewStructural Design Considerations: The 55-ton bridge crane is built with a robust frame to handle the heavy loads required for the operation of opening and closing sealed container lids. This design ensures that the crane remains stable even under maximum load conditions, which is crucial for high-capacity tasks. The frame is made from high-strength materials, providing both durability and reliability over time.
Main Components:
- Motorized Systems: The crane includes heavy-duty motors that control the lifting, lowering, and horizontal movement of the load. These motors are designed for precision, ensuring smooth and controlled motions for lifting and placing the container lids.
- Hoists and Trolleys: Optimized for high-capacity operations, the hoists and trolleys work together to lift and move the lids with the required precision. They ensure the loads are safely handled and transferred to the correct positions, preventing any errors during operation.
- Control Systems: The crane is equipped with an advanced control system that manages the automation and remote control functions. This system integrates with other equipment in the facility, enabling operators to control the crane from a central command station. It ensures that the crane performs autonomously but still allows for human oversight and manual control when needed.
Automation Features
- Advanced Control Systems: The automation of the 55-ton crane is powered by sophisticated control systems. These systems enable remote operation from a central control station, which simplifies operations and reduces the need for direct human intervention. The crane can autonomously perform lid-opening and closing tasks, with operators able to monitor and adjust settings as necessary.
- Sensors and Monitoring: The crane is equipped with a range of sensors that provide real-time feedback on its positioning. These sensors ensure that the lid-opening and closing processes are carried out with high precision. They continuously monitor the crane's movements, making adjustments as needed to maintain accurate control over the task.
Safety Measures: To ensure safe operation, the crane includes several critical safety features:
- Automatic Shut-offs: If the crane experiences a malfunction or reaches a predefined limit, it will automatically shut down to prevent further issues.
- Real-time Fault Monitoring: The system constantly monitors the crane’s health, detecting any faults or malfunctions as they occur. If a fault is detected, the system immediately alerts operators, reducing the risk of accidents or equipment damage.
These automation features work together to ensure that the crane performs its tasks efficiently, safely, and with minimal human involvement.
Crane Positioning and Operational Workflow
The crane operates in a fully automated workflow for the precise handling of sealed container lids. Here's how the process unfolds:
- Lid Operations: The system is designed to automatically move the crane to the correct container location. Once in position, the hoisting mechanism lifts the lid. Based on pre-set instructions, the crane either opens or closes the lid, performing the task with high accuracy and efficiency. The operation is triggered by a set of pre-programmed commands that dictate each movement, ensuring the task is completed without manual intervention.
- Pre-Programmed Instructions: The crane follows detailed, pre-programmed instructions to ensure consistency in every operation. These instructions define how the crane should position itself, lift the lid, and execute either an opening or closing motion. By relying on these pre-set parameters, the crane ensures each task is carried out with minimal error and within the defined time frame.
- Automatic Movement and Precision: The crane’s automation system guarantees that each movement is calculated with precision. It precisely lifts the lids and positions them correctly, which is crucial for the safety and efficiency of the container handling process. Every action is optimized to maintain high performance throughout operations.
Safety Measures
Ensuring safety is a top priority in the design of the automated crane. Several layers of safety features have been integrated to protect both the equipment and the personnel working around it:
- Emergency Stop Mechanism: In case of any unexpected malfunction or dangerous condition, the crane is equipped with an automatic emergency stop function. This feature ensures that operations cease immediately, preventing further damage to the crane or any potential injuries to nearby personnel. The emergency stop can be triggered by the system itself or manually by an operator when necessary.
- Fault Detection: Real-time monitoring systems continuously check for any operational issues or malfunctions. These systems can detect failures as they occur, ensuring that the crane doesn’t continue to operate in a faulty state. As soon as a fault is identified, the system sends an alert to the operator, allowing for immediate intervention to resolve the issue. This proactive approach minimizes the risk of accidents or disruptions in the workflow.
By integrating these safety measures, the crane can operate autonomously while ensuring the highest standards of safety and reliability.
Implementation Process
The successful implementation of the 55-ton automated crane involved a series of well-coordinated steps, ensuring the system was ready for smooth operation from day one. Here is an overview of the process:
Site Preparation and Installation
- Site Assessment: Before installation, a thorough site assessment was carried out to determine if the crane would fit within the existing facility's space. This included evaluating the available area for crane movement and ensuring the structure could support the crane's weight and operational requirements. The facility’s infrastructure, including power supply and support for crane movement, was also assessed to avoid any issues during installation.
- Infrastructure Readiness: Along with evaluating the space, the installation team made sure the existing infrastructure was equipped to handle the crane’s heavy-duty operations. This included ensuring that the power supply could support the high-energy demands of the crane, and that there was sufficient space for the crane to move freely without obstacles.
- Integration with Existing Systems: The new crane was seamlessly integrated into the facility’s existing automated systems. This integration included connecting the crane to the central control system, ensuring that all movements and operations would be coordinated automatically with the rest of the plant’s automated processes. The goal was to create a cohesive system where all components work in sync for maximum efficiency.
System Integration
- Coordination with Automation Systems: The crane's control systems were carefully synchronized with the facility’s automation software, which is responsible for coordinating all tasks across the plant. This included the lid-handling system, which was integrated into the broader operational flow. Real-time data transmission ensures that the crane can be remotely controlled and monitored, providing full visibility into operations at any given time.
- Real-Time Monitoring and Control: The operation of the crane is constantly monitored, with data being transmitted in real time to the central control system. This allows operators to stay informed on the crane’s performance, identify potential issues early, and make adjustments if needed. The integration of real-time monitoring ensures that operations are continuously optimized, helping to improve productivity and maintain high safety standards.
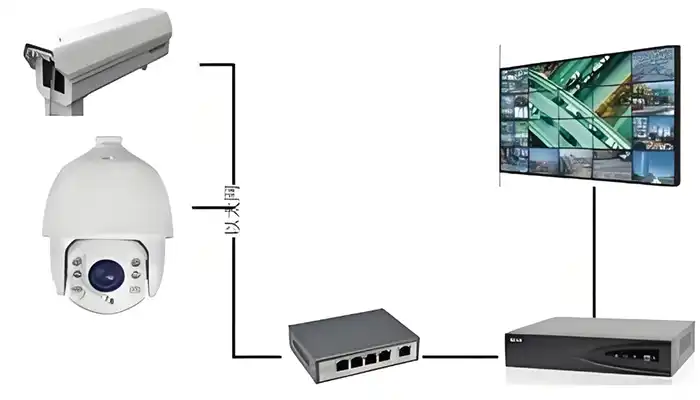
Testing and Commissioning
- Initial Testing: Prior to fully launching the crane’s operations, an extensive round of testing was conducted. This involved verifying the functionality of each component, including motors, control systems, and sensors. Special attention was given to ensure that the crane performed its lid-opening and closing tasks with high precision and accuracy. Testing also checked the system’s response times, ensuring that it met the required operational standards.
- Commissioning: After successful testing, the crane was formally commissioned and became fully operational. During this phase, any last-minute adjustments were made to ensure the crane worked smoothly within the facility’s automated systems. Once commissioned, the crane began its operations, handling container lids with autonomy and precision.
This implementation process ensured the seamless installation and operation of the 55-ton automated crane, setting the stage for efficient, safe, and precise lid handling in the facility.
Benefits and Impact
The integration of the 55-ton automated overhead crane into the facility has brought numerous benefits, improving operational efficiency, reducing costs, and enhancing safety. Here's an overview of the key impacts:
Operational Efficiency
- Faster Operations: The automated crane has drastically reduced the time required to open and close the sealed container lids. The system operates continuously without breaks, unlike manual operations that are slower and subject to human fatigue. This efficiency has translated into smoother, more consistent workflows in the facility.
- Consistent Performance: Automation ensures that the lid-opening and closing processes are always executed to the same high standard, with precise movements every time. This consistency eliminates the variability that can occur with manual handling, which can lead to delays and errors.
- Minimal Downtime: The system’s ability to run around the clock, without breaks or downtime, allows for continuous operation. This increases the overall throughput of the facility and supports the production of goods without interruption.
Cost Efficiency
- Labor Savings: A significant reduction in manual labor has been achieved with the automation of lid operations. By removing the need for workers to perform these repetitive tasks, the facility has saved on labor costs. This not only reduces wage expenses but also frees up workers for other, more strategic roles within the company.
- Lower Maintenance Costs: Automation contributes to lower long-term maintenance costs. Since the crane operates with precision and fewer human interventions, the wear and tear on the system are significantly reduced. This extends the lifespan of key components, resulting in fewer repairs and replacements over time.
- Energy Efficiency: The automated crane operates with energy-efficient motors and control systems, contributing to lower energy consumption compared to manual processes. This reduces the facility’s overall energy costs, making the operation more sustainable and cost-effective.
Safety Improvements
- Reduced Human Intervention: One of the major safety improvements is the reduced need for human intervention. By automating the lid operation process, workers no longer need to be exposed to the hazardous environment around the crane. This greatly minimizes the risk of accidents, such as those related to lifting operations or mechanical failures.
- Enhanced Safety Protocols: The crane’s safety features, including real-time monitoring, sensors, and an emergency stop mechanism, ensure that the system operates within safe parameters at all times. If an issue is detected, the system can automatically stop the crane, preventing accidents and allowing for immediate attention to the issue. These enhanced safety protocols provide peace of mind for both operators and management.
- Fault Detection and Prevention: The crane’s real-time monitoring system can detect faults before they become serious problems. By identifying issues early, the system can prevent potential safety risks, reducing the chances of accidents and costly downtime. This proactive approach to maintenance and safety improves the overall workplace environment.
Overall, the automation of the 55-ton overhead crane has provided significant operational, cost, and safety improvements, transforming the way container lid operations are carried out and setting a high standard for future automated systems.
Challenges and Solutions
While the implementation of the automated 55-ton overhead crane has brought significant benefits, the project was not without its challenges. Here’s an overview of the key challenges faced during the project, along with the solutions that were implemented to overcome them.
Challenges Faced
- Site Constraints: The physical layout of the facility presented challenges in fitting the 55-ton crane into the available space. The crane had to move within limited room, which required precise planning and design. There was also the need to ensure that the crane could reach the necessary areas of operation while avoiding interference with existing equipment.
- System Integration: One of the significant challenges was integrating the new automated crane with the existing systems at the facility. Ensuring that the crane’s control system could communicate effectively with other automation systems was crucial. Compatibility between the crane’s systems and the existing infrastructure had to be verified to ensure smooth operations without disruptions.
Solutions Implemented
- Customized Design: To address the space constraints, a customized crane design was developed specifically for this project. The design took into account the limited space available for crane movement, optimizing the crane’s dimensions and operational range. This allowed the crane to perform its tasks efficiently without interfering with other equipment or operations.
- Advanced Control Systems: To overcome the integration challenge, the crane was equipped with advanced control systems that offered flexibility in syncing with the existing infrastructure. These control systems were designed to be compatible with the facility’s automation platform, allowing for seamless communication between the crane and other systems. This ensured that all functions, from lid handling to safety checks, were synchronized perfectly with the rest of the operations.
By addressing these challenges with customized design and advanced control systems, the project team was able to successfully implement the automated 55-ton overhead crane without compromising on performance or safety.
Conclusion
The automated 55-ton bridge crane designed for sealed container lid operations has successfully achieved all of the project’s key objectives. The system has significantly enhanced operational efficiency by automating the heavy lifting and precise control required for opening and closing the lids. This has led to a noticeable reduction in downtime and has streamlined the workflow within the facility.
Additionally, by minimizing the need for manual labor, the crane has helped lower labor costs while improving consistency in operations. The automation has also boosted safety standards by reducing human exposure to hazardous tasks and incorporating real-time monitoring and safety features.
As a result, the overall productivity of the facility has been greatly increased. The ability of the system to handle these heavy-duty tasks automatically has ensured smoother and more reliable operations, benefiting both the facility’s workforce and the company’s bottom line.
- Expansion of Automation: Following the success of this project, there is a strong possibility of expanding automation across other areas of the facility. Other heavy-duty lifting tasks and operations that currently rely on manual labor could be automated in the future. This would further improve operational efficiency and reduce labor costs across the site.
- Industry-Wide Implications: The successful implementation of the automated 55-ton overhead crane serves as a model for similar industries seeking to automate material handling operations. It demonstrates the significant benefits of integrating automation into the manufacturing and production processes, setting a standard that could be applied to various industries worldwide. By reducing manual labor, improving precision, and increasing overall safety, automation is becoming an integral part of modern industrial operations.
As automation continues to evolve, the lessons learned from this project will play a crucial role in shaping the future of industrial automation, making operations more efficient, safer, and cost-effective.