10 Ton Gantry Crane Design, Choose Right Design for Your Project
10 ton gantry crane design: Selecting right solution for your uses, optimizing efficiency & performance.Check all you want to know on gantry crane design.
10 Ton Gantry Crane Design: Choosing the Right Solution for Your Application
A 10 ton gantry crane is a robust lifting solution designed to handle heavy loads up to 10 tons within various industrial and commercial settings. Gantry cranes are characterized by their overhead structure supported by legs that run on rails or wheels, allowing for horizontal movement along a fixed path. This design provides versatility in material handling, making them suitable for applications ranging from manufacturing and construction to logistics and shipbuilding.
Selecting the appropriate 10 ton gantry crane design is crucial for optimizing operational efficiency, ensuring safety, and maximizing productivity. Factors such as the type of gantry (single girder or double girder), beam structure (box girder or truss girder), hoisting mechanism (electric hoist or open winch trolley), and control system significantly impact the crane's performance and suitability for specific tasks.
The right design choice depends on various considerations including the operational environment (indoor or outdoor), the frequency and nature of lifts, available space, and budget constraints. Each design option offers distinct advantages in terms of load capacity, span length, operational flexibility, and maintenance requirements. By understanding these factors, businesses can effectively streamline their material handling processes, enhance workplace safety, and achieve long-term cost-effectiveness with a well-chosen 10 ton gantry crane design.
Basic Concepts of Gantry Cranes
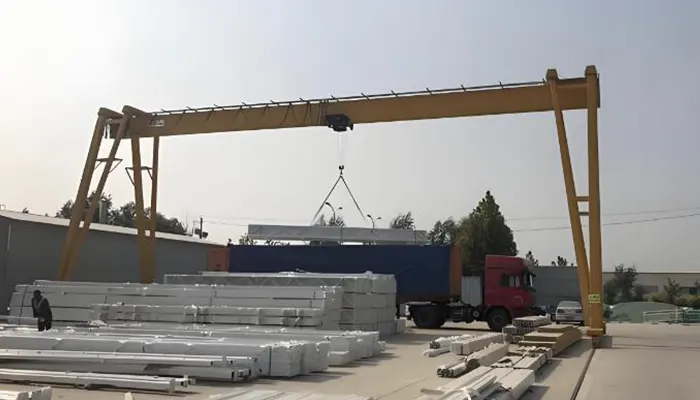
single girder gantry crane with box girder design
Definition and Components
Gantry cranes, also known as portal cranes, are overhead cranes supported by uprights (legs) that move on fixed rails or wheels. They are designed to lift and transport heavy loads horizontally within a defined area. Key components include:
- Bridge: The horizontal beam that spans between the legs and supports the trolley.
- Legs (Uprights): Vertical supports that provide stability and guide the crane's movement.
- Trolley: Moves horizontally along the bridge and carries the hoist.
- Hoist: The lifting mechanism that raises and lowers the load.
- Control System: Manages crane movements and ensures safe and efficient operation.
Applications and Industries
Gantry cranes are indispensable in various industries due to their versatility and lifting capacity. Common applications include:
- Manufacturing: Handling materials during production processes, such as loading/unloading machine tools.
- Construction: Lifting and moving heavy components at construction sites.
- Warehousing and Logistics: Loading and unloading goods in warehouses and distribution centers.
- Shipbuilding: Moving ship components and materials in shipyards.
- Transportation: Loading/unloading cargo from trucks and railcars in freight terminals.
Their ability to operate in diverse environments, from indoor facilities to outdoor yards, makes gantry cranes essential equipment for improving efficiency and safety in material handling operations across different sectors.
Types of 10 Ton Gantry Cranes
Single Girder vs. Double Girder
Single Girder Gantry Cranes: Single girder gantry cranes feature a single horizontal beam spanning the width between the legs. They are lighter and more cost-effective, suitable for moderate load capacities and shorter spans. Ideal for applications where space and cost efficiency are priorities.
Double Girder Gantry Cranes: Double girder gantry cranes have two parallel horizontal beams across the span. They offer increased strength, stability, and higher load capacities compared to single girder cranes. Suitable for heavy-duty applications requiring longer spans, frequent lifting operations, or handling oversized loads.
box girder gantry crane with double girder designs
Box Girder vs. Truss Girder Designs
Box Girder Gantry Cranes: Box girder gantry cranes use a hollow rectangular structure for the bridge girder. This design provides superior strength and resistance to torsional forces, making them suitable for heavy loads and long spans. Box girder cranes are preferred for applications requiring precise and efficient material handling.
Truss Girder Gantry Cranes: Truss girder gantry cranes feature an open framework of beams arranged in a triangular pattern (trusses). They offer high strength-to-weight ratio and are lighter compared to box girder cranes. Truss girder cranes are versatile, cost-effective, and ideal for applications with varying load capacities and spans.
Choosing between single and double girder cranes depends on the specific requirements of your application, including load capacity, span length, operational frequency, and budget considerations. Similarly, selecting between box and truss girder designs involves evaluating factors such as structural integrity, environmental conditions, and the need for specialized features like enhanced stability or reduced weight.
Truss girder gantry crane with single girder design
Design Considerations
Load Capacity and Span Length
- Load Capacity: The primary design consideration for a 10 ton gantry crane is its ability to safely lift and maneuver heavy loads up to 10 tons. The crane's structural components, including girders and legs, must be engineered to withstand the specified load without deformation or failure.
- Span Length: The distance between the legs of the gantry crane, known as the span length, dictates the crane's structural requirements. Longer spans require stronger girders and more robust support structures to maintain stability and operational safety.
Environmental Factors (Indoor vs. Outdoor)
- Indoor Applications: Gantry cranes used indoors are typically protected from harsh environmental conditions like weather and corrosion. However, they may still be subject to factors like dust and temperature variations, requiring considerations for material durability and maintenance.
- Outdoor Applications: Cranes used outdoors must withstand exposure to weather elements such as rain, wind, and UV radiation. Corrosion-resistant materials and protective coatings are crucial to ensure longevity and minimize maintenance costs in outdoor environments.
Operational Requirements (Frequency of Use, Speed)
- Frequency of Use: The operational intensity of the gantry crane, including how frequently it will be used and the duration of each operation, influences design choices. Heavy-duty operations require robust components and possibly redundant systems to minimize downtime and ensure continuous productivity.
- Operational Speed: The speed at which the crane needs to lift, move, and position loads affects the selection of hoisting mechanisms, trolley speeds, and overall structural design. Optimal operational efficiency is achieved by matching crane speed capabilities with operational requirements to enhance productivity and safety.
Carefully evaluating these design considerations ensures that the 10 ton gantry crane is tailored to meet specific application needs, whether in manufacturing facilities, construction sites, warehouses, or other industrial environments. Each factor plays a crucial role in determining the crane's performance, longevity, and overall cost-effectiveness.
Structural Components
Gantry Structure and Legs
- Gantry Structure: The gantry structure forms the main framework of the crane, supporting the hoisting mechanism and providing stability during lifting operations. It consists of vertical legs or posts connected by horizontal beams. The design of the gantry structure ensures sufficient strength and rigidity to handle the crane's load capacity and operational requirements.
- Legs: Gantry crane legs provide vertical support and stability to the crane structure. They are typically made from steel and anchored firmly to the ground or foundation to withstand the forces generated during lifting and movement of heavy loads. The configuration of the legs can vary based on the type of gantry crane and the specific application requirements, such as A-frame, U-frame, or L-frame designs.
Beam Design (Box Girder, Truss Girder)
- Box Girder: A box girder design features a closed rectangular cross-section, offering superior strength and torsional stiffness compared to other designs. It is well-suited for applications requiring heavy lifting capacities and long spans. The enclosed structure provides enhanced resistance to bending and torsional forces, making it ideal for demanding industrial environments.
- Truss Girder: Truss girder designs use an open framework of triangular or lattice-shaped elements to support the crane's load. This design offers high strength-to-weight ratio, reducing material costs while maintaining structural integrity. Truss girders are versatile and suitable for both indoor and outdoor applications where weight reduction and cost-effectiveness are priorities.
Cantilever Design (if applicable)
- Cantilever: In some gantry crane designs, a cantilever extends horizontally beyond the gantry legs, providing additional reach and flexibility in material handling operations. The cantilevered section supports the crane's load without the need for additional support structures, maximizing workspace utilization and operational efficiency. This feature is beneficial for accessing and maneuvering loads in confined or irregularly shaped work areas.
Each structural component of the 10 ton gantry crane is carefully designed to optimize performance, durability, and safety based on specific application requirements. The choice between box girder and truss girder designs, as well as the inclusion of a cantilever, depends on factors such as load capacity, span length, operational environment, and budget considerations. These components work together to ensure reliable and efficient material handling operations in various industrial settings.
Hoisting Mechanism
Electric Hoist vs. Open Winch Trolley
- Electric Hoist: Electric hoists are commonly used in gantry cranes for their efficiency and precise control over lifting operations. They are powered by electric motors and feature a robust lifting mechanism capable of handling heavy loads up to 10 tons. Electric hoists offer variable lifting speeds, smooth acceleration, and deceleration, making them suitable for applications requiring precise positioning and controlled movements. These hoists are ideal for indoor environments where noise levels and emissions need to be minimized.
- Open Winch Trolley: Open winch trolleys utilize a more traditional design where the hoisting mechanism is mounted on an open trolley that moves along the gantry beam. This design is versatile and allows for higher lifting heights and capacities. Open winch trolleys are often used in outdoor environments or applications where heavy-duty lifting is required. They provide robust performance, reliability, and ease of maintenance, making them suitable for demanding industrial operations.
Hoist Capacity and Speed
- Hoist Capacity: The hoist capacity of a 10 ton gantry crane determines its maximum lifting capability. It is crucial to match the hoist capacity with the intended load requirements to ensure safe and efficient lifting operations. Hoists for 10 ton gantry cranes are designed with sufficient capacity margins to handle loads within their rated capacity without strain or overload, ensuring safety and longevity of the equipment.
- Lifting Speed: The lifting speed of the hoisting mechanism influences the productivity and efficiency of material handling operations. Higher lifting speeds reduce cycle times and increase throughput, especially in applications with frequent load movements. The speed of the hoist can be adjusted to accommodate different operational requirements, balancing between productivity and precision based on specific application needs.
The choice between electric hoists and open winch trolleys for a 10 ton gantry crane depends on factors such as operational environment, load handling requirements, and budget considerations. Both options offer distinct advantages in terms of performance, reliability, and suitability for various industrial applications, ensuring optimal material handling efficiency and safety.
Control Systems
Types of Control Systems
- Remote Control: Remote control systems enable operators to control the gantry crane from a distance using wireless technology. This type of control offers flexibility and safety by allowing operators to move around the workspace while maintaining full control over crane operations. Remote controls are ideal for applications requiring maneuverability and visibility of the load from different angles.
- Pendant Control: Pendant controls consist of a handheld pendant with buttons or joysticks connected to the crane by a cable. They provide direct control over crane movements and are commonly used in gantry cranes for their simplicity and reliability. Pendant controls allow operators to be in close proximity to the crane, offering precise control over lifting, lowering, and trolley movements.
- Cabin Control: Cabin control systems involve a dedicated operator cabin mounted on the gantry crane structure. Operators have a comprehensive view of the workspace and can control crane operations from a comfortable and protected environment. Cabin controls are suitable for applications requiring continuous operation or where operators need to oversee complex lifting tasks and manage multiple cranes simultaneously.
Safety Features and Compliance
- Load Limiters: Load limiters are safety devices that prevent the crane from lifting loads beyond its rated capacity. They ensure safe operation by automatically stopping hoisting or trolley movements when load limits are exceeded, preventing equipment damage and ensuring personnel safety.
- Emergency Stop Button: Emergency stop buttons are critical safety features that immediately halt all crane movements in case of emergencies or hazardous situations. They are strategically located on the crane and control panels for quick access by operators in urgent situations.
- Overload Protection: Overload protection systems monitor the load on the crane and provide warnings or automatically stop operations when loads exceed safe limits. These systems prevent structural damage and enhance crane safety during heavy lifting operations.
- Collision Avoidance Systems: Collision avoidance systems use sensors and alarms to detect obstacles or other cranes in the workspace. They alert operators to potential collisions and automatically stop crane movements to prevent accidents and damage to equipment.
- Compliance with Standards: Gantry cranes are designed and manufactured to comply with international safety standards and regulations, such as ISO 9001 and CE certification. Compliance ensures that gantry cranes meet strict safety criteria and are suitable for use in various industrial environments without compromising operational safety and efficiency.
Choosing the right control system and integrating essential safety features are crucial aspects of designing a 10 ton gantry crane. These systems enhance operational efficiency, ensure workplace safety, and comply with industry standards, making gantry cranes reliable solutions for demanding material handling applications.
Customization Options
Special Features
- Walkways and Platforms: Integrating walkways and platforms into the gantry crane design enhances accessibility for maintenance tasks and operator movement. Walkways are typically located along the length of the gantry crane's bridge or gantry structure, providing safe access to critical components. Platforms offer elevated working areas for operators to oversee operations or manage equipment, improving efficiency and safety in industrial settings.
- Weather Protection: Weather protection features such as canopies or shelters can be added to shield operators, equipment, and loads from adverse weather conditions like rain, snow, or intense sunlight. These features ensure uninterrupted operations and protect sensitive materials from environmental exposure, extending the crane's lifespan and minimizing maintenance requirements.
Additional Load Handling Equipment
- Rotating Hooks: Rotating hooks allow for easy manipulation and orientation of loads during lifting and positioning operations. They enhance operational flexibility and efficiency by reducing the need for manual adjustments, especially in applications requiring precise load alignment or rotation.
- Specialized Attachments: Customized attachments such as spreader bars, lifting beams, or magnetic lifters can be integrated to handle specific load types or shapes. These attachments optimize the crane's versatility and adaptability to diverse material handling tasks, improving productivity and operational efficiency.
- Automatic Positioning Systems: Automated positioning systems utilize sensors and programmable controls to accurately position loads within predefined coordinates. These systems minimize human error, increase operational speed, and ensure precise load placement, making them ideal for high-volume production environments or repetitive handling tasks.
Customizing a 10 ton gantry crane with special features and additional load handling equipment enhances its functionality, efficiency, and safety in various industrial applications. These options allow operators to tailor the crane's capabilities to specific operational requirements, ensuring optimal performance and productivity.
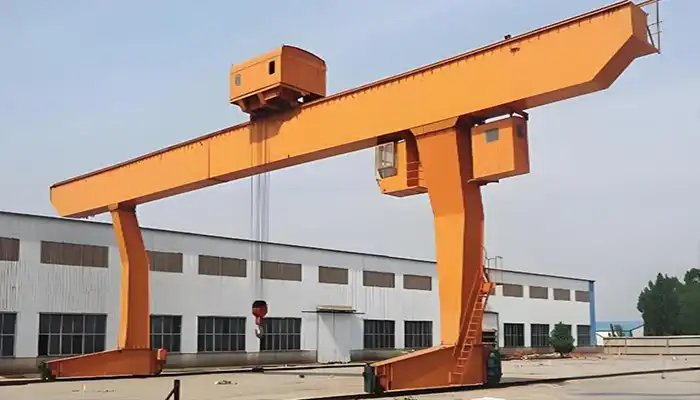
Installation Considerations
- Site Preparation: Before installation, ensure the site is level, stable, and able to support the gantry crane's weight and operational loads. This may involve foundation work, such as pouring concrete footings or installing ground anchors, depending on the crane's design and local building codes.
- Assembly and Erection: Gantry cranes typically arrive partially assembled for on-site erection. Ensure skilled personnel follow manufacturer guidelines and safety protocols during assembly to ensure structural integrity and operational safety. Specialized lifting equipment may be required to lift and position heavy components.
- Testing and Commissioning: After assembly, conduct thorough testing and commissioning to verify operational readiness. This includes testing the hoisting mechanism, trolley movement, control systems, and safety features. Ensure all components meet performance specifications and comply with regulatory standards before putting the crane into service.
Maintenance Requirements and Costs
- Scheduled Inspections: Implement a regular inspection schedule to detect wear, fatigue, or potential failures early. Inspections should cover structural components, electrical systems, hoisting mechanisms, and safety devices. Follow manufacturer recommendations for inspection frequency and procedures.
- Routine Maintenance: Perform routine maintenance tasks such as lubrication, alignment checks, and minor adjustments to ensure smooth operation and prolong component lifespan. Addressing minor issues promptly can prevent costly repairs and downtime.
- Repair and Overhaul: Plan for periodic major inspections and overhauls to address wear and component fatigue. This may involve replacing worn parts, refurbishing mechanical components, or upgrading obsolete technology to enhance crane performance and safety.
- Cost Considerations: Factor in maintenance costs, including labor, spare parts, and downtime, when budgeting for crane operations. Investing in proactive maintenance and timely repairs can minimize overall costs and extend the crane's operational lifespan.
Proper installation and proactive maintenance are critical to maximizing the performance, longevity, and safety of a 10 ton gantry crane. By adhering to best practices and manufacturer guidelines, operators can ensure reliable and efficient operation throughout the crane's service life.
Cost Considerations
Initial Investment vs. Long-term Costs
- Initial Investment: The cost of a 10 ton gantry crane includes procurement, delivery, and installation expenses. Factors influencing initial costs include crane type (single girder, double girder), hoisting mechanism (electric hoist, open winch trolley), structural design (box girder, truss girder), and customization options (special features, additional load handling equipment).
- Long-term Costs: Beyond initial investment, consider ongoing expenses such as maintenance, repairs, and operational costs. Opting for durable materials and efficient design can reduce long-term maintenance and repair costs. Regular maintenance and proactive repairs help minimize downtime and extend the crane's lifespan, contributing to overall cost-effectiveness.
Factors Affecting Cost
- Material Selection: The choice of materials for gantry crane components, including girders, legs, and hoisting mechanisms, significantly impacts costs. High-strength steel alloys are durable but may incur higher upfront costs compared to standard steel. Consider environmental factors (corrosion resistance) and operational requirements (load capacity) when selecting materials.
- Design Complexity: Crane design complexity affects both initial and long-term costs. Double girder cranes generally cost more than single girder cranes due to their higher load capacity and structural requirements. Box girder designs offer enhanced strength but may involve higher fabrication and installation expenses compared to truss girder designs, which are lighter and simpler to construct.
By carefully assessing these cost considerations, including initial investment versus long-term costs and factors influencing cost such as material selection and design complexity, businesses can make informed decisions when choosing a 10 ton gantry crane tailored to their operational needs and budget constraints.
Conclusion
Tips for Choosing the Right 10 Ton Gantry Crane Design
- Assess Operational Needs: Evaluate your specific lifting requirements, including load capacity, span length, and operational environment (indoor or outdoor).
- Consider Structural Requirements: Choose between single girder and double girder designs based on load capacity and span requirements.
- Factor in Hoisting Mechanism: Select the appropriate hoisting mechanism (electric hoist vs. open winch trolley) based on lifting speed and efficiency needs.
- Evaluate Control Systems: Decide on the control system (remote, pendant, cabin) that suits your operational preferences and safety requirements.
- Customization Options: Explore additional features like walkways, platforms, and specialized load handling equipment that enhance crane functionality.
- Budget and Long-term Costs: Balance initial investment with long-term maintenance and operational costs to ensure cost-effectiveness over the crane's lifespan.