How Environmental Factors Shape Gantry Crane Design
Environmental factors dictate gantry crane materials, coatings, and features to optimize performance & longevity in diverse operational settings. Design for you!
Gantry cranes, versatile giants of industrial lifting, play a pivotal role across a spectrum of sectors ranging from construction and manufacturing to logistics and shipping. These robust structures are essential for efficiently handling heavy loads, offering unparalleled flexibility in both indoor and outdoor environments. Unlike their overhead counterparts, gantry cranes straddle their workload, utilizing legs or wheels to navigate across a designated area. This unique design allows them to support loads ranging from a few tons to several hundred tons, making them indispensable in industries where precision and power are paramount.
The significance of gantry cranes extends beyond their sheer lifting capacity. They are engineered to withstand the rigors of their operational environments, whether that involves lifting containers in bustling ports or managing materials in expansive warehouses. Designing gantry cranes to harmonize with environmental conditions is crucial for enhancing their longevity, ensuring operational efficiency, and mitigating risks associated with climatic challenges and industrial settings.
Adaptation to environmental factors encompasses a range of considerations, from structural integrity in high-wind zones to corrosion resistance in maritime climates. Each design nuance reflects a strategic response to the demands imposed by nature and industry alike, underscoring the dynamic interplay between technology and environment in modern engineering practices.
In this comprehensive guide, we delve into the intricate relationship between environmental conditions and gantry crane design. By exploring how various factors influence design choices, we aim to provide insights that empower engineers, operators, and decision-makers to optimize crane performance and reliability in diverse operational contexts. Whether navigating extreme weather conditions or meeting stringent cleanliness standards, the adaptation of gantry crane designs underscores their pivotal role in driving efficiency and safety across global industries.
Environmental Factors Influencing Gantry Crane Design
Climate and Weather Conditions
Gantry cranes are designed to operate in a wide range of climatic conditions, from scorching deserts to freezing polar regions, presenting unique challenges for their structural integrity and operational efficiency.
Effects of Temperature Extremes:
Gantry cranes are significantly impacted by temperature extremes. In hot climates, prolonged exposure to excessive heat can lead to accelerated wear and degradation of critical components such as motors, electronics, and lubricants. This not only reduces the operational lifespan of the crane but also diminishes its efficiency over time. Conversely, in cold climates, low temperatures cause materials to contract, affecting mechanical tolerances and causing operational challenges such as stiffness and reduced smoothness in crane movements.
Hot Climates:
- Excessive Heat: Prolonged exposure to high temperatures in hot climates can accelerate the degradation of crane components such as motors, electronics, and lubricants. Heat can cause thermal expansion, leading to increased friction and wear on moving parts.
- Material Degradation: Materials used in crane construction may lose mechanical strength and durability under prolonged heat exposure. Heat-sensitive components, such as electrical wiring and insulation, may degrade faster, compromising crane safety and reliability.
- Cooling Systems: Gantry cranes designed for hot climates incorporate effective cooling systems for motors, electronics, and hydraulic components. These systems may include fans, heat exchangers, and insulated enclosures to maintain optimal operating temperatures and prevent overheating.
Cold Climates:
- Material Contraction: Low temperatures cause materials to contract, affecting mechanical tolerances and potentially causing stiffness in crane movements. This contraction can lead to reduced operational smoothness and increased wear on mechanical components.
- Lubrication Challenges: Cold temperatures can thicken lubricants, reducing their effectiveness and potentially causing increased friction and wear. Specialized low-temperature lubricants are used to ensure smooth crane operation in cold climates.
- Insulation and Heating: Gantry cranes operating in cold climates are equipped with insulation and heating systems to protect critical components from freezing. These systems maintain optimal operating temperatures for motors, hydraulic systems, and electronics, ensuring consistent performance and preventing cold-related malfunctions.
Impact of Wind Speed and Gusts:
High wind speeds pose significant challenges to gantry crane stability and safe operation. Engineers must calculate wind loads and design cranes with robust structural reinforcements to withstand gusts, ensuring operational safety even during adverse weather conditions.
- Impact of Wind Speed and Gusts: Gantry cranes are particularly vulnerable to high wind speeds, which can exert significant forces on their structures, potentially compromising stability and safety during operation. Engineers employ rigorous wind load calculations and design methodologies to mitigate these risks effectively.
- Wind Load Calculations: Engineers analyze the crane's structural configuration, including its height, shape, and geographical location, to determine the magnitude of wind forces it may encounter. Wind speed data specific to the crane's operational environment are crucial inputs for these calculations.
- Design Considerations: Based on wind load calculations, gantry cranes are designed with robust structural reinforcements to resist wind-induced forces. This includes using thicker steel sections, additional bracing, and optimized load distribution to enhance stability and minimize sway.
- Dynamic Effects: During crane operation, dynamic effects such as crane movements and load handling can exacerbate the impact of wind gusts. Crane designs incorporate damping mechanisms and aerodynamic profiles to mitigate these dynamic effects and maintain operational stability.
- Safety Standards: Compliance with international safety standards and regulations, such as those outlined by organizations like ANSI (American National Standards Institute) or EN (European Norms), ensures that gantry cranes are designed to withstand specified wind conditions while ensuring operational safety and reliability.
High wind speed conditions necessitate proactive design strategies and engineering solutions to safeguard gantry crane operations. By integrating advanced wind engineering principles and structural analysis techniques, manufacturers can enhance crane resilience against adverse weather conditions, ensuring uninterrupted productivity and safety across diverse industrial environments.
Outdoor vs. Indoor Environments
Gantry cranes deployed in outdoor environments face exposure to various elements, necessitating specialized design considerations to maintain optimal performance and extend their operational lifespan.
Exposure to Elements:
Outdoor gantry cranes are subjected to environmental factors such as rain, snow, sunlight, and fluctuating temperatures, which can accelerate corrosion and degrade structural materials over time. These elements pose significant challenges to crane durability and reliability.
Protective Measures:
To mitigate environmental wear and ensure long-term performance:
- Weather-Resistant Coatings: Applying weather-resistant coatings to exposed surfaces helps protect against moisture, UV radiation, and chemical pollutants. Epoxy coatings, polyurethane paints, and galvanizing treatments are commonly used to enhance corrosion resistance.
- Galvanized Steel Components: Structural components made from galvanized steel offer superior resistance to rust and corrosion, making them ideal for outdoor crane applications. Galvanization involves applying a protective zinc coating to steel surfaces to prevent oxidation.
- Regular Maintenance: Implementing a proactive maintenance schedule is essential for outdoor gantry cranes. This includes routine inspections, cleaning, lubrication of moving parts, and timely repair of any surface damage or coating degradation. Regular maintenance not only prolongs crane lifespan but also ensures operational safety and reliability.
By integrating these protective measures and maintenance practices, manufacturers and operators can mitigate the adverse effects of outdoor exposure on gantry cranes. This proactive approach enhances crane durability, minimizes downtime, and maximizes productivity in challenging outdoor environments.
Operational Environment
The operational environment significantly influences gantry crane design, particularly in industrial settings where exposure to chemicals and stringent cleanliness standards are prevalent.
Chemical Exposure in Industrial Settings:
- Corrosive Substances: Gantry cranes used in chemical plants and heavy industrial environments are exposed to corrosive substances such as acids, alkalis, and chemical solvents. These substances can accelerate corrosion and degrade crane components over time.
- Materials Selection: Choosing corrosion-resistant materials such as stainless steel or specialized alloys for critical crane components helps mitigate chemical damage. These materials offer superior resistance to chemical corrosion, ensuring crane durability and longevity in harsh industrial environments.
- Surface Treatments: Protective coatings and surface treatments, such as epoxy coatings and chemical-resistant paints, create a barrier against chemical exposure. These treatments prevent direct contact between corrosive substances and crane surfaces, reducing the risk of material degradation and structural damage.
- Sealing Technologies: Sealing critical crane components, such as electrical connections and hydraulic systems, prevents ingress of corrosive substances. Effective sealing methods include gaskets, O-rings, and encapsulation techniques, ensuring operational safety and reliability in chemically aggressive environments.
Cleanroom and Sterile Environments:
- Sterile Requirements: Gantry cranes used in cleanroom environments, such as pharmaceutical, semiconductor, and healthcare industries, must comply with strict cleanliness standards to prevent contamination of sensitive products and equipment.
- Sealed Components: Specialized cleanroom gantry cranes feature sealed components and smooth surfaces to minimize particle generation and microbial contamination. Sealing prevents airborne contaminants from entering crane mechanisms and ensures cleanroom integrity.
- Adherence to Standards: Compliance with stringent cleanliness protocols, such as ISO cleanroom classifications, dictates design considerations for cleanroom gantry cranes. These standards govern material compatibility, surface finishes, and operational practices to maintain sterile conditions and product quality.
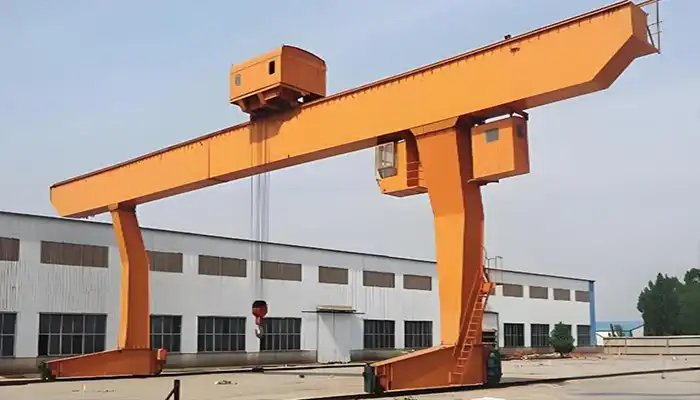
Design Adaptations for Different Environmental Conditions
Cold Weather Conditions
Gantry cranes operating in cold climates require specialized design adaptations to ensure reliable performance and longevity despite freezing temperatures.
- Specialized Lubrication and Material Considerations: Low temperatures can thicken lubricants, impeding crane operation. Gantry cranes designed for cold weather environments use special lubricants that remain fluid at low temperatures. Additionally, materials with high impact resistance and low-temperature stability are chosen to maintain mechanical integrity.
- Insulation and Heating Systems: Critical crane components such as motors, hydraulic systems, and electronics are insulated to prevent freezing and ensure consistent performance. Heating systems may be integrated into crane cabins and control panels to maintain optimal operating conditions.
Hot Weather Conditions
In hot climates, gantry cranes face challenges related to heat exposure, requiring design adaptations to mitigate temperature-related stress on components.
- Cooling Systems for Motors and Electronics: High ambient temperatures can cause overheating of motors and electronic components, leading to decreased efficiency and potential damage. Gantry cranes incorporate cooling systems such as fans, heat sinks, and air circulation to dissipate heat effectively and maintain optimal operating temperatures.
- Heat-Resistant Materials: Components exposed to direct sunlight or high temperatures are constructed from heat-resistant materials such as alloys and thermally stable polymers. These materials ensure structural integrity and prevent deformation or deterioration due to prolonged heat exposure.
Wet and Corrosive Environments
Gantry cranes operating in wet and corrosive environments, such as coastal areas or chemical plants, require robust corrosion protection to withstand exposure to moisture and chemical contaminants.
- Stainless Steel Components: Critical crane components susceptible to corrosion, such as load-bearing structures and fasteners, are fabricated from stainless steel or corrosion-resistant alloys. These materials offer superior resistance to rust and corrosion, prolonging crane lifespan and reducing maintenance requirements.
- Corrosion-Resistant Coatings and Treatments: Protective coatings, such as galvanization or epoxy coatings, are applied to exposed surfaces to create a barrier against moisture and chemical exposure. Regular inspections and maintenance of these coatings are essential to ensure ongoing protection against corrosion.
High Wind and Seismic Zones
Gantry cranes located in regions prone to high wind speeds or seismic activity require structural reinforcements and careful design considerations to ensure operational safety and stability.
- Structural Reinforcements: Crane structures are reinforced with additional bracing, thicker gauge materials, and optimized load distribution to enhance stability and resist wind-induced forces. Finite element analysis (FEA) and structural simulations are used to assess and optimize crane design against seismic loads and wind forces.
- Wind Load Calculations and Considerations: Engineers calculate wind loads based on crane configuration, location, and local wind conditions. Factors such as crane height, wind exposure, and operational conditions are taken into account to determine necessary design modifications and safety measures.
By implementing these design adaptations tailored to specific environmental conditions, gantry cranes can maintain peak performance, reliability, and safety throughout their operational lifespan. These proactive measures not only enhance crane efficiency but also minimize downtime and maintenance costs, ensuring continuous productivity in demanding industrial environments.
Case Studies and Examples
Examples of Gantry Crane Designs Tailored to Specific Environmental Challenges
- Arctic Region Adaptations: In Arctic regions where temperatures plummet well below freezing, gantry cranes used in mining and resource extraction industries are equipped with specialized heating systems and insulated cabins. These cranes feature robust materials resistant to cold-induced brittleness and are designed with Arctic-specific lubricants to ensure smooth operation in extreme cold.
- Coastal Applications: Gantry cranes deployed in coastal areas face constant exposure to saltwater and humidity, leading to accelerated corrosion. Successful designs incorporate stainless steel components, galvanized coatings, and regular maintenance protocols to combat corrosion effectively. Case studies from major ports demonstrate the longevity achieved through corrosion-resistant design adaptations.
Success Stories in Adapting Gantry Cranes for Extreme Climates and Conditions
- Desert Operations: In desert environments characterized by scorching heat and sandstorms, gantry cranes are engineered with heat-resistant materials and cooling systems to withstand high ambient temperatures. Case studies from mining operations in desert regions highlight the integration of dust-proof seals and robust HVAC systems to maintain crane performance under harsh desert conditions.
- High Wind Zones: Gantry cranes operating in regions prone to high wind speeds, such as coastal areas and offshore platforms, are designed with reinforced structures and aerodynamic profiles. Success stories include offshore wind farms where gantry cranes are instrumental in assembling wind turbine components safely amidst strong offshore winds.
These case studies and examples illustrate the versatility and adaptability of gantry crane designs in overcoming environmental challenges. By tailoring crane specifications to specific climate and operational conditions, manufacturers and operators enhance reliability, safety, and operational efficiency, ensuring optimal performance throughout diverse industrial settings.
Conclusion
Designing gantry cranes to withstand diverse environmental conditions is essential for ensuring their longevity, efficiency, and safety across various industrial applications. Throughout this guide, we have explored how environmental factors such as climate, weather conditions, and operational environments influence gantry crane design choices.
Key considerations include:
- Climate and Weather Conditions: From extreme temperatures to high wind speeds, gantry cranes must be engineered with materials and systems that can withstand these challenges without compromising performance.
- Corrosive and Chemical Exposure: Industries such as marine, chemical, and heavy manufacturing require gantry cranes resistant to corrosion and chemical damage, achieved through material selection and protective coatings.
- Operational Environment: Specialized environments like cleanrooms or sterile facilities necessitate gantry cranes with stringent cleanliness standards and contamination prevention measures.
Customization plays a crucial role in adapting gantry crane designs to meet specific operational needs and environmental demands. Collaboration with engineering experts ensures that each crane is tailored with the right materials, coatings, and structural reinforcements to maximize reliability and minimize maintenance costs over its lifespan.
In conclusion, by prioritizing environmental considerations and leveraging advanced engineering solutions, manufacturers and operators can optimize gantry crane performance and safety, supporting efficient operations and enhancing overall industrial productivity. Continual innovation and adaptation to evolving environmental challenges will further drive the evolution of gantry crane design, ensuring they remain indispensable tools in modern industrial landscapes.