15 Ton HD Single Girder Crane & Electric Hoist for Sale Paraguay
Overview of the Project
This case study outlines the supply and integration of heavy-duty lifting equipment for a glass manufacturing facility in Paraguay. The project involved providing both HD+ European Style hoists and CD electric hoists. The goal was to enhance the lifting capacity, efficiency, and safety within the client's production processes.
Brief Introduction to the Customer (Paraguay)
The customer, based in Paraguay, operates within the glass manufacturing industry. Known for its demand for reliable and efficient lifting solutions, the customer required high-performance hoists to handle large and heavy glass products. Their operations rely on maximizing uptime and minimizing maintenance, making advanced hoisting solutions essential.
European style wire rope electric hoist
Description of the Equipment Supplied
HD Overhead Crane + European Style Hoist
- 15T-13.22M H8.15M
- 15T-16.95M H6.95M
- 380V 60HZ 3P
These hoists were designed to lift heavy glass materials with precision, providing the necessary lifting capacity and clearance for smooth operation.
CD Electric Hoist
- 5T-6M
- 380V 50HZ 3P
This hoist was specifically chosen to handle lighter loads, offering flexibility and versatility for various tasks in the production process.
Significance of This Case Study in Terms of Product Application and Industry
This project is significant as it showcases how advanced hoisting systems are applied in the glass manufacturing industry. The combination of the HD European Style hoists and CD electric hoists allowed the customer to streamline their production processes, enhancing both safety and efficiency. The ability to handle different load capacities with precision is critical in the glass industry, where lifting heavy and delicate items is common. The case highlights how tailored lifting solutions can improve operational productivity in demanding environments.
Project Scope
Client Requirements: Lifting Capacity and Specifications for Hoists
The client’s primary requirement was a lifting system capable of handling heavy glass products with high precision.
- 15T HD+ European Style Hoists: These hoists were selected to meet the customer’s need for lifting large, heavy glass pieces safely. The specifications of 13.22M H8.15M and 16.95M H6.95M ensured they could accommodate the varying load requirements within the production facility.
- 5T CD Electric Hoist: This hoist was required to manage lighter glass pieces and smaller tasks within the same facility.
Size and Weight Constraints for Transportation
Given the scale of the hoists, size and weight were critical factors during the planning and transportation phase.
- The hoists had to be compact enough to fit within standard shipping containers (1x40HC) while maintaining their full operational capacity.
- The dimensions and weight were carefully balanced to ensure safe transport and installation without exceeding the limitations of local infrastructure.
Specific Power Requirements
- The HD+ European Style Hoists were designed to run on 380V 60HZ 3P power, matching the industrial electrical systems in the client's facility.
- The CD Electric Hoist, on the other hand, required a slightly different voltage of 380V 50HZ 3P, which was also compatible with the existing power grid in the facility.
Key Deliverables
The deliverables for the project were clearly outlined:
Two 15T HD European Style Overhead Crane Kit + European Style Hoists
- Specifications: 15T capacity, 13.22M span, 8.15M lifting height, 16.95M span, and 6.95M lifting height
- Designed to handle the primary heavy lifting requirements in the client’s operations.
One 5T CD Electric Hoist
- Specifications: 5T capacity, 6M span
- Designed for lighter and more precise lifting tasks.
Industry Application: Glass Manufacturing
The application of these hoists within the glass manufacturing industry is crucial for safe and efficient lifting. Glass manufacturing involves the handling of large, delicate sheets that require precise lifting to avoid damage. The hoists’ configuration and power specifications were tailored to meet the specific demands of this industry, enhancing both operational safety and efficiency in production.
Timeline of Events
Order Details
- April 28: The order was placed by the customer for two 15T HD+ European Style Hoists and one 5T CD Electric Hoist.
- May 20: Delivery of the two 15T hoists was expected after a 15-day pickup period, ensuring the production and inspection processes were on track.
Manufacturing and Production
- February 24: The main beam for the hoists was formed, marking the beginning of the construction phase.
- June 2: The NR10 hoist was completed and ready for delivery, ensuring the primary lifting equipment was on schedule.
- June 6: Preparation for rust removal and painting began, a crucial step to ensure the longevity and appearance of the hoists.
- June 9: The main hoist was fully completed, and final checks were made to ensure it met all specifications.
- July 7: An additional 5T CD hoist was included in the project, adding flexibility for smaller lifts within the facility.
Shipping Details
- Port of Departure: The hoists were shipped from Qingdao, one of China’s major ports for international trade.
- Container: The shipment was packed into a 1*40HC (40-foot High Cube container), a standard shipping container used for large, heavy equipment.
- Shipping to Paraguay: The hoists were scheduled to arrive in Paraguay on August 20, 2022, completing the transportation phase of the project.
This timeline ensures that each stage of the project was executed efficiently, from order placement to final shipping, meeting the customer’s requirements within the agreed timeframe.
Production Process and Challenges
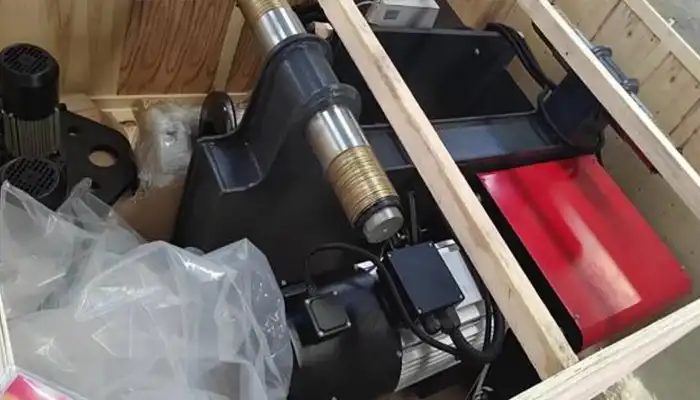
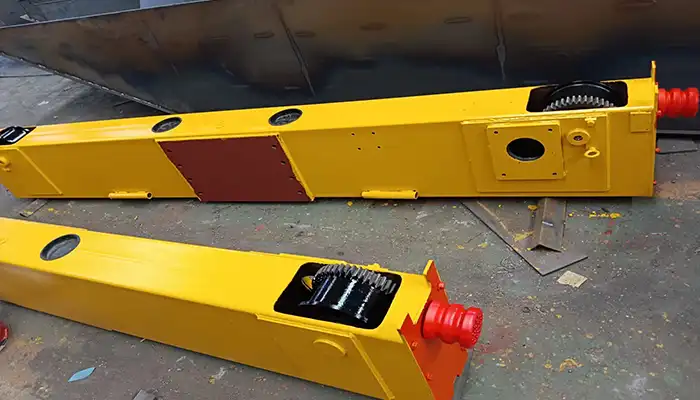
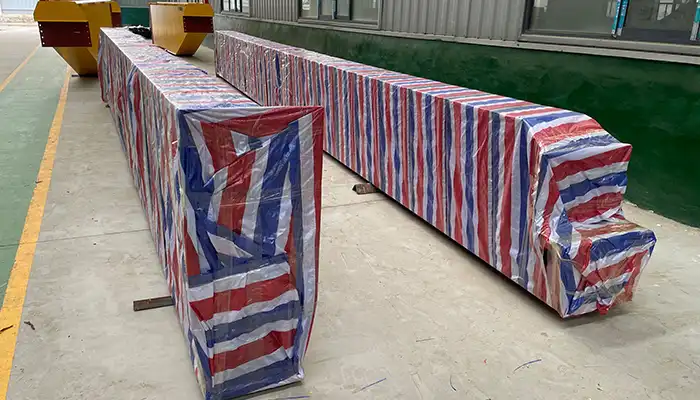
Manufacturing Progress
The production process followed a well-structured timeline to meet the customer’s expectations:
- February 24: The main beam for the hoists was formed, marking the start of the construction process.
- June 2: The NR10 hoist was ready for delivery after passing final inspections.
- June 6: Rust removal and painting began to ensure the hoists’ durability and aesthetic quality.
- June 9: The main hoist was completed and subjected to quality control.
- July 7: The addition of the 5T CD hoist was finalized and integrated into the production schedule.
Throughout this period, the production team worked diligently to meet deadlines while ensuring each hoist was crafted with precision. All systems were designed to meet the customer’s specific requirements for lifting capacity and operational needs.
Quality Control Checks and Customizations
- During the production process, each hoist went through rigorous quality control checks to ensure that all components met the highest industry standards.
- Customizations, such as ensuring the 380V60HZ3P and 380V50HZ3P power specifications, were carefully implemented. This was essential to meet the unique power requirements for each hoist type.
- Special attention was paid to ensuring that the 15T HD+ European style hoists were built to provide smooth and reliable lifting in the glass manufacturing industry.
Challenges Encountered
While the production process was largely smooth, there were a few challenges faced along the way:
- Short-term Delays: The rust removal and painting process took slightly longer than expected, pushing the timeline back a few days. This delay was necessary to ensure the hoists were fully protected and maintained their longevity in the customer’s facility.
- Coordination of Multiple Hoist Configurations: The project involved several different hoist types, each with its own specifications and requirements. Managing these multiple configurations required careful coordination between departments to ensure no errors during production.
- Integration of the CD Hoist: Initially, the order only included the two 15T hoists, but the customer later requested a 5T CD hoist for smaller lifts. Integrating this additional hoist into the production schedule added complexity, but the team adapted quickly to meet the customer’s evolving needs.
Despite these challenges, the project was completed on time and met the customer’s expectations, demonstrating the team’s ability to adapt and deliver quality equipment under pressure.
Key Technical Features
HD Overhead + European Style Hoist
The HD Overhead Hoists paired with European Style Hoists are designed to handle heavy-duty lifting tasks with high load capacities, perfect for industrial settings like glass manufacturing. Key technical features include:
- Heavy-duty lifting capacity: With the 15T hoists, they can lift significant weights and large loads with ease.
- Precision operation: The hoists are equipped with advanced control systems to ensure smooth and precise lifting, making them ideal for handling delicate or heavy glass materials.
- Reliability and durability: Built to withstand demanding industrial environments, these hoists are made with robust components to ensure long-lasting performance and minimal downtime.
- Easy operation: The hoists feature user-friendly controls for operators, reducing training time and improving overall efficiency in the workplace.
These features are critical in a glass manufacturing environment, where heavy materials need to be moved with accuracy and care.
CD Electric Hoist
The 5T CD Electric Hoist provides a lower lifting capacity but is essential for smaller, more precise tasks. Key features of the CD hoist include:
- Smaller load capacity: With a 5-ton lifting capacity, it is perfect for tasks that require less weight but more precision.
- Adaptability to power requirements: The hoist is specifically designed to operate on 380V50HZ3P, perfectly matching the electrical requirements for smaller lifts.
- Easy installation: Its compact design and flexible configuration make it suitable for integration into various crane systems, making it a versatile solution in spaces with limited headroom.
The CD Electric Hoist meets the unique demands of lifting smaller glass pieces or tools with high precision, which is essential in the glass manufacturing process.
Adaptation to Industry Needs
The combination of these hoists plays a crucial role in glass manufacturing:
- Handling heavy materials: The 15T HD Overhead hoists are used for moving large glass sheets, pallets, or molds, ensuring that heavy loads are lifted efficiently without strain on the equipment.
- Precision in lifting: The 5T CD hoist caters to tasks that require more delicate handling of glass materials, such as positioning and lifting smaller components or glass products.
- Adaptability: The hoists’ flexibility to operate in different conditions (low headroom, varying power needs) and their customization options make them ideal for an industry with diverse lifting requirements.
In a glass manufacturing facility, having reliable and precise lifting equipment like the HD Overhead Hoists and CD Electric Hoists is essential for productivity and safety. These hoists work together to optimize the handling of both large and small loads, making the production process smoother and more efficient.
Logistics and Shipping
Packaging and Containerization
When shipping heavy-duty equipment like hoists, ensuring the safety and integrity of the products during transport is a key priority. For this project, the following packaging and containerization steps were taken:
- Secure packaging: The hoists and all components were carefully packed using high-quality materials designed to protect them from damage during transit. This included protective wrapping, custom supports, and cushioning to prevent any shifts or impacts that could affect the equipment.
- Container specifications: A 40HC (40-foot High Cube) container was chosen for this shipment. This type of container offers extra height, ensuring that the hoists and all components fit comfortably without being compressed. The larger volume allows for optimal use of space, minimizing the risk of damage while keeping shipping costs efficient.
The packaging process was designed to ensure the hoists would arrive in Paraguay in optimal condition, ready for quick installation and operation.
Shipping Challenges
Shipping heavy machinery internationally comes with its set of challenges, especially when it comes to coordinating timelines, customs, and international regulations. For this project, the shipping process included:
- Managing international shipping: Coordinating the shipment of such large equipment across multiple borders requires careful planning and monitoring. The shipment was tracked from Qingdao Port to Paraguay, ensuring that each step of the journey was on schedule. Any delays, such as at ports or due to weather, were closely monitored to avoid disrupting the final delivery.
- Customs and documentation: Navigating customs can be complex when shipping heavy industrial equipment. Ensuring all required documentation (such as invoices, certificates of origin, and technical specifications) was completed properly helped streamline the customs clearance process.
- Timely delivery: Meeting the client’s delivery expectations was crucial. The hoists were scheduled to arrive on August 20, 2022, and ensuring the timely arrival involved close communication between the shipping partners, the manufacturer, and the client. The coordination of shipping dates, transit time, and final delivery ensured the hoists were delivered as promised.
Despite potential delays and logistical hurdles, the shipment was delivered on time, meeting the client’s needs and ensuring they could begin using the hoists without issue.
Customer Interaction and Feedback
Communication
Effective communication played a crucial role throughout the project. To ensure the customer was always informed, regular updates were provided at key stages of the production and delivery process:
- Production updates: The customer received timely notifications about the progress of the hoists’ manufacturing, including milestones such as the completion of the main beam, painting and rust removal, and the addition of the CD hoist. These updates helped keep the customer reassured that the project was on track.
- Delivery notifications: From the manufacturing stages to the shipping details, the customer was kept informed about the timeline, including the expected delivery date in Paraguay. Any minor delays, such as those related to the painting process, were promptly communicated and addressed.
- Handling queries: Whenever the customer had questions regarding the specifications, progress, or any other concerns, the project team was quick to respond. By maintaining an open line of communication, any issues were addressed promptly to ensure the customer's satisfaction throughout the project.
Customer Satisfaction
The customer’s feedback upon receiving and installing the hoists highlighted the success of the project in meeting their requirements. Some of the key takeaways from the feedback included:
- Quality and precision: The customer praised the HD Overhead hoists and the European style hoists for their robust quality and precision. The hoists performed as expected, with seamless operation and reliable lifting capability. The precision and sturdiness of the equipment made a significant impact on the customer’s operations, especially in the glass manufacturing industry, where accuracy is essential.
- Ease of installation and operation: The customer appreciated the straightforward installation process. Detailed instructions and support from the manufacturer ensured that the equipment was set up quickly and efficiently. Additionally, the user-friendly controls of the hoists and the maintenance-friendly design were highlighted. The customer found it easy to operate the equipment and adjust settings according to the lifting tasks.
The feedback was overwhelmingly positive, confirming that the project met the customer’s expectations in both product quality and service. This case exemplified how effective communication and a focus on customer satisfaction can lead to successful outcomes in international projects.
Conclusion and Outcomes
Project Success
The project was deemed a success due to several key achievements:
- Timely delivery: All hoists were delivered as per the agreed schedule, despite minor delays related to the rust removal and painting process. The delivery was successfully completed in August 2022, meeting the client’s expectations.
- Seamless integration: The HD Overhead Hoists and the European Style Hoists, along with the CD Electric Hoist, were integrated efficiently into the customer’s operations. These hoists worked flawlessly within the client’s glass manufacturing facility, ensuring reliable lifting and material handling.
Impact on the Client
The hoists had a significant positive impact on the client’s operations:
- Improved efficiency: With the newly installed hoists, the customer experienced smoother and faster lifting operations. The robust design of the 15T hoists allowed for the safe and efficient movement of heavy materials, reducing downtime and increasing overall productivity.
- Enhanced lifting capabilities: The European Style Hoists and CD Hoist facilitated precise and heavy-duty lifting, crucial for the glass manufacturing industry. This upgrade resulted in better handling of large glass sheets, ensuring safety and minimizing the risk of damage to fragile materials.
Lessons Learned
Several key lessons were drawn from this project:
- Clear communication and coordination: Effective communication with the international client played a critical role in ensuring smooth project execution. Regular updates and quick responses to queries ensured that the client remained informed and satisfied at every stage of the project.
- Efficient manufacturing and shipping management: A well-organized timeline for production and shipping proved essential. The ability to manage international shipping challenges, along with timely production, ensured that the hoists arrived on time and met the client’s operational needs.
Overall, this project highlighted the importance of a structured approach to project management, with a focus on customer satisfaction, timely delivery, and seamless integration of equipment. The successful completion of this project strengthened the relationship with the client, setting the stage for potential future collaborations.