How to Accurately Calculate Overhead Bridge Crane Span and Height
Crane Span and Height
Correctly calculating the span and height of overhead bridge cranes is essential for both safety and operational efficiency. The span refers to the distance between the two runway beams of the crane, while the height determines the vertical clearance between the crane's hook or hoist and the floor beneath it. These two factors play a major role in the crane's functionality, ensuring it can handle loads safely without any clearance issues or operational obstacles.
The purpose of this guide is to provide you with the knowledge and tools to calculate the span and height accurately. By understanding these key measurements, you can ensure that your crane operates effectively in the available space, without compromising safety or efficiency. Whether you're designing a new crane system or upgrading an existing one, getting the span and height calculations right is the first step towards successful installation and long-term operation.
Why It Matters
Properly calculated crane span and height are critical to avoiding operational problems and minimizing risks. If these measurements are incorrect, there could be clearance issues that interfere with load handling, cause crane malfunction, or create safety hazards. For example, if the crane’s height is too low, the load may not have enough vertical space for safe hoisting and movement. Similarly, an incorrectly sized span could result in misalignment with the runway or cause the crane to operate inefficiently, leading to undue stress on the system.
Additionally, accurate crane span and height calculations contribute to the longevity and efficiency of the crane. With the right clearance and span, the crane experiences less wear and tear, reducing the frequency and cost of repairs. Furthermore, having a well-calculated crane setup ensures that the crane operates smoothly, which increases productivity and reduces the risk of downtime.
In essence, the correct span and height calculations allow the crane to fit perfectly within its environment, ensuring that it performs its intended tasks without compromising on safety, reliability, or functionality.
Key Factors in Calculation
Several factors need to be considered when calculating the span and height of a crane:
- Ceiling Height: The available vertical space in the facility plays a critical role in determining the crane height and clearance. The ceiling height limits how high the crane can lift loads and how much headroom is available for operators and equipment.
- Building Layout: The layout of the building or workspace impacts the crane's span and height. The total available width of the space will define the maximum span, while the vertical layout determines the clearance needed for safe operations.
- Load Clearance: Understanding the size, weight, and type of loads that will be handled by the crane is crucial. The load’s height and the lifting requirements directly impact the necessary crane height and the safety gaps to ensure safe operation.
- Safety Margins: Always include a safety margin in the design calculations to allow for load sway, crane movement, and operational adjustments. This extra clearance helps prevent accidents and ensures smooth crane operation even under fluctuating conditions.
- Overhead Space: Consider other overhead features that might affect the crane’s height, such as HVAC systems, light fixtures, or building supports. These elements may require adjustments to the crane’s design to ensure no interference with the crane's operations.
By taking all these factors into account, you can calculate the correct span and height, ensuring the crane performs effectively in its environment while keeping safety and efficiency in focus.
Basics of Crane Span and Height
Crane Span
The crane span refers to the horizontal distance between the two runway beams on which the crane travels. This distance determines the width of the area that the crane can cover during its operation. In simple terms, the span is the width of the crane's operating path, and it influences how far the crane can move horizontally across the facility.
Factors that Impact Span:
- Facility Layout: The overall design and size of the building or workspace where the crane will operate are key considerations. The available width of the facility will define the crane span, and any obstructions (such as columns or walls) must be taken into account to ensure that the crane can travel freely within the space.
- Load Size: The size of the loads the crane will handle also affects the span. Larger or more complex loads may require a wider span to move across the workspace efficiently. For example, a crane lifting oversized components may need a wider span to ensure proper maneuvering and load handling.
- Required Operational Space: The intended application of the crane will dictate the amount of operational space required. If the crane is used in an environment with specific tasks (such as handling large, bulky materials or equipment), a larger span might be necessary to accommodate these requirements and provide greater maneuverability.
Crane Height (Clearance)
Crane height refers to the vertical clearance between the floor and the underside of the crane's hoist or bridge. This dimension is essential for determining how much space is available for the crane to lift loads safely and effectively. Clearance impacts not only the height of the loads being lifted but also the safety and ease of operation for operators and maintenance staff.
Factors to Consider:
- Ceiling Height: The height of the building’s ceiling plays a direct role in determining the crane’s maximum lifting height. The crane’s height must allow for proper clearance to lift loads without interference from overhead structures like beams, ductwork, or light fixtures.
- Load Clearance: The type and size of the loads being handled will determine the required height clearance. Larger loads may need additional vertical space to ensure they can be lifted safely without coming into contact with surrounding structures.
- Hook Height: The hook height is the distance between the floor and the crane’s lifting hook at its maximum extension. This measurement directly impacts the crane's lifting capacity and the height at which it can place or retrieve loads.
- Safety Margins: Always account for safety margins when calculating crane height. These margins are essential to prevent potential issues such as load sway, crane movement, or unexpected clearance requirements during operation. A sufficient safety gap ensures that the crane can perform efficiently under varying load conditions and maintains operational flexibility.
By thoroughly understanding the crane span and height, and the factors that influence these measurements, you can ensure that your crane is optimally designed for both safety and operational effectiveness within your facility.
Key Factors in Calculating Overhead Crane Span and Height
Building Layout and Facility Dimensions
- Overall Building Dimensions:The first step in calculating the crane span and height is to thoroughly understand the building’s layout and dimensions. This includes the length, width, and available height within the facility. The available width will help determine the crane’s span, while the height will define the clearance needed for the crane to operate without obstruction.
- Building Structure and Crane Size:The relationship between the building’s structural design and the crane size is essential. Support beams, columns, walls, and other architectural features influence where and how the crane can be positioned. For example, columns may reduce the available span, and low ceilings may restrict the crane’s lifting capacity. Understanding the structural constraints of the building ensures that the crane fits and operates effectively within the available space.
Load Requirements
Size, Weight, and Shape of Loads:
One of the primary factors in determining both the span and height of an overhead crane is the type of loads it will be handling. Different loads have different spatial requirements:
- Weight: Heavier loads often require stronger crane structures and may need wider spans to accommodate the necessary lifting power.
- Size and Shape: Oversized or awkwardly shaped loads may require more space to move safely. For example, large machinery or long beams will need ample space in both height and span to avoid contact with walls or other structures during movement.
Lifting Height:
The height at which a crane must lift a load is critical to the overall clearance requirements. High ceilings may be necessary if you’re lifting large or tall items. Additionally, it’s important to consider the height of the crane hook at its highest position and ensure there’s enough clearance to lift and maneuver loads without risk of obstruction.
Safety Margins
- Operational Safety Gaps:Safety margins are crucial when calculating both the crane span and height. These include the additional clearance space needed to account for factors like crane swing, load sway, and unexpected movements during operations. For example, cranes can experience some degree of horizontal or vertical sway, particularly when lifting heavy or unbalanced loads. Including extra space for these movements reduces the risk of accidents and ensures smooth operations.
- Load Movement and Sway:Allowing enough space for the load to move safely is essential. When lifting and transporting loads, especially heavy ones, it’s possible for the load to swing or sway, particularly if the crane is moving at higher speeds or over long distances. By calculating for sway, you can ensure that the crane has sufficient clearance to avoid bumping into structural elements, machinery, or personnel.
- Future Equipment Installations:It’s also wise to include extra space to accommodate potential future equipment or upgrades, such as additional cranes or storage systems. Having a bit of extra room allows for flexibility in the future, particularly if the operational needs of the facility evolve or grow.
Including adequate safety margins for load movement, sway, and potential expansions ensures that the crane system will be safe, efficient, and adaptable for years to come. Proper planning and accounting for these factors will minimize operational disruptions and enhance long-term performance.
Step-by-Step Guide to Calculating Overhead Crane Span
Measure the Facility’s Width
Begin by measuring the total width of the facility or structure where the crane will be installed. The measurement should be taken from wall to wall at the points where the crane will travel, ensuring accuracy for proper crane fit.
- Measure both at the ground level and overhead to account for structural elements.
- Consider any obstructions like columns, beams, or supports that may limit the crane's span or movement.
By accurately measuring the building width, you can determine how much available space the crane will have for its travel path, ensuring that no structural obstacles interfere with its movement.
Determine the Required Span
Once you have the building width, the next step is to choose the crane span. The span is the distance between the two runway beams that the crane travels along. The span must accommodate both the building width and the load dimensions.
- Single Girder Cranes: Ideal for lighter loads, these cranes have a narrower span and are cost-effective for smaller operational spaces.
- Double Girder Cranes: These are suitable for heavier loads and require a wider span due to the increased lifting capacity. They offer better stability but need more space.
In determining the required span, it’s crucial to consider the size and weight of the loads that the crane will handle. Larger or heavier loads may require a wider span to allow for proper lifting and movement.
Add Safety and Operational Gaps
To ensure smooth operation, add safety gaps to both sides of the crane. This extra space will account for any sway or movement, especially when lifting heavy or unbalanced loads.
- Safety Gaps: Typically 3-6 inches on each side, these gaps help avoid interference from the building structure and prevent accidents.
- Future Modifications: It’s also important to leave space for potential future expansions, such as adding additional cranes or equipment. Having extra space allows flexibility for future upgrades without the need for significant changes to the crane's infrastructure.
Safety gaps and space for future upgrades are essential in ensuring that the crane can operate smoothly and that the facility can adapt to future operational needs without major modifications.
Step-by-Step Guide to Calculating Crane Height and Clearance
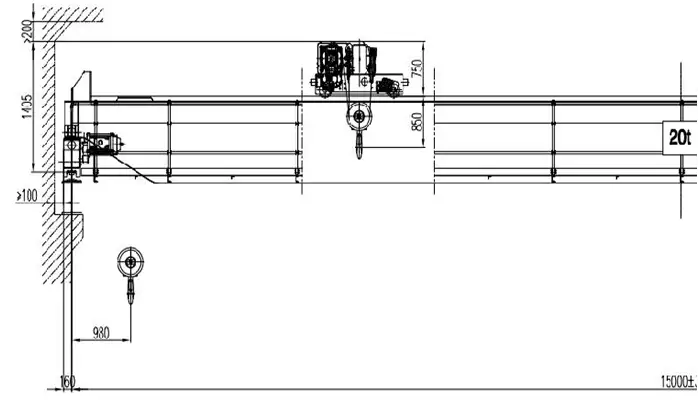
Measure Ceiling Height
Start by determining the total ceiling height from the floor to the roof or support beams. This is the maximum available vertical space for the crane and its components.
- Consider Structural Features: Take into account any obstructions like HVAC systems, ducts, light fixtures, or overhead pipes that might reduce the available clearance for the crane.
- Accurate Measurement: Ensure that the measurement is taken from the floor level up to the highest point of the ceiling, especially if there are any sloped rooflines or uneven structures.
By measuring the ceiling height, you establish the upper limits of the crane’s travel, ensuring that the crane fits and operates safely within the available space.
Determine Hook Height
Next, calculate the minimum hook height required for safe load handling. The hook height is the vertical distance from the floor to the bottom of the crane’s hook.
- Load Size Considerations: Factor in the height of the loads being lifted. Larger or bulkier loads may require a higher hook to avoid interference with the ceiling or other obstacles.
- Clearance Requirements: For some operations, such as moving tall or oversized items, additional clearance may be necessary to prevent damage to both the crane and the load.
The hook height ensures that the crane can safely pick up and move loads without interference, while providing enough clearance for the load itself during travel.
Add Safety Margin for Crane Travel
To account for dynamic movements and operational safety, incorporate a safety margin between the highest point of the load and the ceiling. This ensures there is enough space for both the crane’s hoisting and lowering operations.
- Safety Gaps: Add a buffer zone (typically a few inches) above the load to prevent it from coming into contact with the ceiling during lifting or lowering.
- Dynamic Considerations: Take into account any sway or load movement that may occur when the crane is in operation, particularly with heavy or irregularly shaped loads.
The safety margin helps prevent collisions with the ceiling and ensures that the crane operates smoothly even under variable conditions, reducing the risk of accidents and damage to both the crane and its environment.
Accounting for Environmental and Operational Factors
Temperature and Weather Considerations
When calculating crane span and height, it's essential to factor in environmental conditions, as temperature fluctuations can significantly impact crane performance and structure.
- Impact of Temperature Changes: Steel and other crane components can expand or contract with temperature changes, which may affect clearance and operation. This is particularly important in facilities exposed to extreme temperatures.
- High Heat Environments: In environments like steel mills, where temperatures can rise significantly, crane components must be designed to withstand the heat. This may require higher clearance to ensure the crane operates safely without interference from heated structures.
- Cold Storage Conditions: In freezing environments, such as cold-storage facilities, the crane system should be designed with materials that can handle low temperatures without becoming brittle or losing structural integrity. Additional clearance may be needed to account for frost buildup or expanded safety margins to avoid accidents.
By understanding how environmental factors affect crane operation, you can ensure that the crane is built to last and operate efficiently under various temperature conditions.
Maintenance and Future Modifications
Considering future maintenance and potential upgrades is critical when planning crane span and height.
- Routine Inspections and Adjustments: As part of the crane's lifecycle, plan for regular inspections and maintenance schedules. Ensure that the crane's design allows for easy access to key components that need servicing, such as hoists, motors, or control systems.
- Space for Modifications: Future upgrades or adjustments, like the installation of new hoists, motors, or even more advanced bridge systems, might be necessary. Leave additional space around the crane to accommodate these changes without needing to significantly alter the existing setup.
- Proactive Planning: By thinking ahead, you can avoid disruptions when modifications are required and reduce downtime, saving both time and money.
Accounting for future needs in the crane design phase helps reduce long-term operational disruptions and ensures that the crane remains adaptable to evolving business requirements.
Floor Space and Safety Margins
The crane's footprint and the available floor space are crucial in ensuring safety, efficiency, and compliance within your facility.
- Operator and Equipment Space: Ensure there is adequate space for crane operators to safely access control panels and for the crane to maneuver loads without obstruction. Consider the clearance needed for the operator’s line of sight, as well as access paths for maintenance personnel and emergency responders.
- Facility Layout: Avoid placing the crane system in areas that could impede foot traffic, storage, or other essential operations. The crane should not obstruct critical pathways or create bottlenecks that could compromise workflow.
- Safety Margins: Allow additional space between the crane's movement path and any fixed objects (such as walls, machines, or other cranes) to prevent accidental collisions. Implementing these safety gaps ensures that the crane operates safely and minimizes the risk of damage to equipment, people, and the facility itself.
By accounting for floor space and safety margins, you can ensure that the crane operates efficiently without compromising the operational flow or safety of your facility.
Practical Example: Calculating Span and Height for a Specific Facility
Scenario Setup
Imagine you are working with a 50x80 ft warehouse that has a ceiling height of 25 feet. To ensure the correct crane design, we need to calculate the span and height for an overhead crane that will fit within these dimensions and meet operational needs and safety standards.
Facility Dimensions:
- Warehouse dimensions: 50 feet wide by 80 feet long.
- Ceiling height: 25 feet from floor to roof.
We will now apply these measurements to determine the crane's span, height, and safety margins.
Step-by-Step Application of Measurements
Measure the Building Width and Ceiling Height
Start with the basic facility dimensions: the warehouse is 50 feet wide and the ceiling is 25 feet high. These values will guide both the span and height calculations.
Determine the Crane Span
The span is the distance between the two runway beams on which the crane will travel. Ideally, the crane span should match the width of the warehouse, with some clearance for safety. In this case, we choose a span of 48 feet, allowing for a 1-foot safety margin on each side.
Determine the Crane Height (Clearance)
The height refers to the distance between the floor and the underside of the crane’s hoist or bridge. To ensure safe operation, allow 5 feet of clearance between the hook and the ceiling, plus a 2-foot safety margin for crane movement. This means the hook height should be 18 feet (25-foot ceiling - 5 feet clearance - 2 feet safety margin).
Add Safety and Operational Margins
To ensure smooth movement and reduce the risk of collision, add a 2-foot safety gap on each side of the crane. This space is important for load sway and crane swing, ensuring there’s enough room for safe operation.
Final Measurements:
- Crane Span: 48 feet (fit for warehouse width with safety margins)
- Crane Height: 18 feet (accommodating hook height and operational margins)
Adjustments Based on Load Requirements
Once the basic measurements are set, adjustments need to be made for specific load requirements.
Adjustments for Large Machinery or Heavy Loads
If the crane is required to lift large machinery or heavy components, the height of the load must be considered. For example:
- If the load is tall (e.g., large equipment), the crane’s hook height will need to be raised to ensure clearance.
- For heavy loads, additional space may be needed to ensure the crane can safely lift and move the item without risk of overloading.
Calculating the Necessary Hook Height
Let’s say the load itself is 10 feet tall. To safely lift this load, the crane needs to be able to accommodate its height, the necessary clearance, and additional safety. The new hook height should be 22 feet (10-foot load height + 5 feet clearance + 2 feet safety margin).
Adjusting for Safety Margins
Given the load’s size and the need to avoid collision or swing, we add an additional 2 feet of safety margin to both the span and the height of the crane. This ensures that the crane can move the load without obstruction or risk.
Updated Measurements for Load Handling:
- Crane Span: 50 feet (increased for load clearance and safety).
- Crane Height: 22 feet (adjusted to accommodate taller loads and clearance requirements).
In this practical example, we calculated the crane span and height for a 50x80 ft warehouse with a 25-foot ceiling, while considering facility dimensions, safety margins, and load requirements. By following this step-by-step process, we can ensure the crane will operate efficiently, safely, and with the necessary clearance. This method allows for smooth operations, a reduction in potential accidents, and optimized crane performance over time.
Common Mistakes to Avoid When Calculating Span and Height
Safety Margins
One of the most common errors when calculating crane span and height is underestimating the necessary safety margins. Failing to allow enough space for crane movement or load clearance can result in operational issues, such as the crane colliding with structures or equipment, or the load interfering with the crane's operation.
- Why It’s Important: Safety margins are critical for crane movement, especially during hoisting and lowering actions. Tight fits can cause damage to both the crane and the building, as well as increase the risk of accidents.
- Best Practice: Always account for additional space on both sides of the crane and around the load, to provide ample room for movement and unforeseen changes in the operational environment.
Ignoring Future Modifications
Another mistake is failing to account for potential future modifications or upgrades in the facility. For example, as equipment evolves or operational demands change, your crane may need to handle heavier or larger loads. This might require more height clearance, or an increased span to accommodate new equipment.
- Why It’s Important: Not planning for future-proofing can result in unnecessary costs down the line, such as the need for crane adjustments, building modifications, or even replacing the crane entirely.
- Best Practice: Include extra space for future expansions or upgrades when designing the crane system. This will help avoid the inconvenience and cost of retrofitting the crane system later.
Inaccurate Load Clearance Estimations
A critical mistake that can cause operational inefficiencies is miscalculating load clearance or hook height. If the crane is not designed with the appropriate clearance for the load being lifted, this can lead to frequent breakdowns, safety hazards, or the need for costly modifications.
- Why It’s Important: Inaccurate load clearance can lead to improper load handling, causing strain on the crane’s mechanical components or preventing it from performing optimally.
- Best Practice: Carefully calculate the maximum load height and include sufficient clearance to accommodate the tallest and most oversized loads you expect to lift. Factor in any changes in the load's height as well, such as when lifting bulky or uneven items.
By avoiding these common mistakes and properly accounting for safety margins, future modifications, and accurate load clearance, you can ensure that your crane system operates smoothly and efficiently, with fewer issues and lower long-term costs.
Final Considerations and Tips
Consult a Crane Specialist
When designing or purchasing an overhead bridge crane, it is highly recommended to work closely with crane manufacturers or engineers. These professionals can help ensure that your span and height calculations align with both operational needs and safety standards.
- Why It’s Important: Specialists bring valuable expertise, ensuring that the crane will function efficiently in your specific environment, while meeting safety regulations and standards.
- Best Practice: Don’t hesitate to ask for customized crane solutions tailored to your facility’s unique requirements, particularly if you're working with specialized loads or have unique space constraints.
Review Local Codes and Regulations
It is essential to familiarize yourself with local codes and regulations related to overhead cranes. These regulations can affect not only the span and height calculations but also other critical factors, such as load limits, safety features, and maintenance schedules.
- Why It’s Important: Compliance with local safety standards and regulations prevents potential legal issues and ensures safe crane operation.
- Best Practice: Review the relevant codes regularly and consult with local authorities or experts to ensure your crane system adheres to all necessary guidelines.
Utilize Advanced Tools for Planning
For the most accurate and efficient planning, consider using specialized crane planning software or simulation tools. These tools can help you calculate span and height precisely and optimize the crane system for your specific operational needs.
- Why It’s Important: Advanced tools can help avoid human error and provide more precise, data-driven calculations that account for a wide range of variables.
- Best Practice: Leverage these tools to simulate different load scenarios and evaluate the crane’s performance in your facility before making a final decision on the design.
By consulting experts, staying compliant with regulations, and utilizing advanced planning tools, you can ensure your crane system is both efficient and safe while also minimizing long-term costs and operational issues.
Conclusion: Ensuring Safe and Efficient Crane Operation
Calculating the correct crane span and height is crucial for ensuring safe, efficient, and long-lasting crane operations. These calculations directly affect the crane's ability to function without risk of accidents or unnecessary wear, helping to maintain optimal performance over time.
Key Factors to Consider: Always incorporate safety margins, environmental conditions, and potential future operational requirements when planning your crane system. This holistic approach will not only improve safety but also enhance crane longevity and operational efficiency.
Final Tips for Successful Crane Design and Installation
To achieve a successful crane installation, start by prioritizing accurate measurements of your facility’s available space and the crane’s specific operational needs. Additionally, always account for potential growth or changes in your operations, which could affect the crane’s requirements in the future.
Best Practices:
- Factor in future expansions or equipment upgrades.
- Work closely with crane experts to ensure a design that fits your current and future needs.
- Don’t overlook safety and environmental considerations in your planning.
By following these tips, you’ll be well-positioned to design and install a crane system that is safe, efficient, and adaptable to your facility’s changing needs.