Custom Bridge Crane Specifications to Operational Needs
Custom Bridge Crane Specifications to Operational Needs. Optimize operations by aligning precise bridge crane specs with specific industrial requirements for enhanced efficiency & productivity. Design bridge crane for you!Maximizing Efficiency: Matching Bridge Crane Specifications to Operational Needs:
Both the capacity and specifications of bridge cranes is crucial for optimizing operational efficiency in various industrial applications. Bridge cranes, with their diverse designs, offer tailored solutions for lifting and transporting loads within specific capacity ranges. This article explores the different types and designs of bridge cranes, emphasizing how these variations impact specifications and performance.
Bridge cranes, also known as overhead cranes, consist of parallel runways with a traveling bridge spanning the gap. The hoist, the lifting component, moves along the bridge, allowing for horizontal and vertical load movement. These cranes are pivotal in manufacturing, assembly lines, and material handling due to their ability to move heavy loads with precision and control.
Crane capacity, defined as the maximum weight a crane can safely lift, directly influences key specifications such as span (distance between runways), lift height (vertical distance the load can be raised), speed (hoisting and traveling), and duty cycle (frequency and duration of use). Different crane designs, even within the same capacity range, can offer varying specifications tailored to specific operational needs.
Bridge Cranes by Capacity, Design, and Specifications:
1 to 5 Ton Bridge Cranes:
Typical Applications: Light manufacturing, small workshops, assembly lines.
Single Girder Bridge Cranes:
- Span: 20 to 60 feet.
- Lift Height: 10 to 20 feet.
- Speed: 20 to 50 feet per minute (FPM).
- Duty Cycle: Light to moderate.

Double Girder Bridge Cranes:
- Span: 30 to 100 feet.
- Lift Height: 20 to 30 feet.
- Speed: 30 to 60 FPM.
- Duty Cycle: Moderate to heavy.
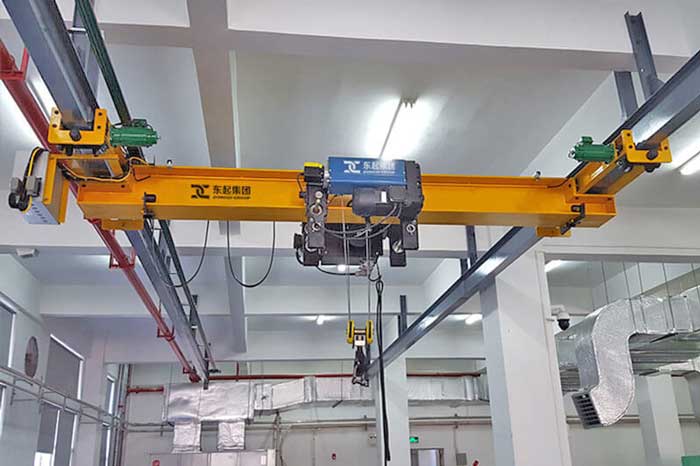
Underhung Bridge Cranes:
- Span: 10 to 30 feet (limited by ceiling structure).
- Lift Height: 10 to 15 feet.
- Speed: 20 to 40 FPM.
- Duty Cycle: Light to moderate.
6 to 20 Ton Bridge Cranes:
Typical Applications: Medium-sized facilities, heavier manufacturing processes, larger assembly lines.
Single Girder Bridge Cranes:
- Span: 30 to 80 feet.
- Lift Height: 20 to 30 feet.
- Speed: 20 to 50 FPM.
- Duty Cycle: Moderate.
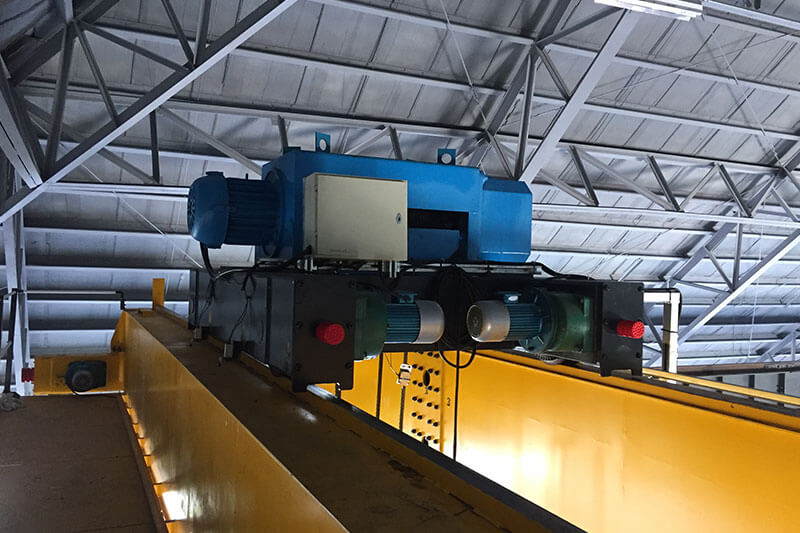
Double Girder Bridge Cranes:
- Span: 40 to 100 feet.
- Lift Height: 25 to 35 feet.
- Speed: 30 to 70 FPM.
- Duty Cycle: Heavy.
25 to 50 Ton Bridge Cranes:
Typical Applications: Large-scale manufacturing, construction sites, heavy equipment handling. 32 ton bridge crane
Double Girder Bridge Cranes:
- Span: 50 to 120 feet.
- Lift Height: 30 to 50 feet.
- Speed: 40 to 90 FPM.
- Duty Cycle: Heavy.
100 Ton Bridge Cranes and Beyond:
Typical Applications: Extremely heavy lifting in industries such as shipbuilding, steel mills, major construction projects.
Double Girder Bridge Cranes:
- Span: Up to 200 feet.
- Lift Height: 50 to 100 feet.
- Speed: 50 to 120 FPM.
- Duty Cycle: Continuous.
Factors to Consider When Evaluating Specifications:
When selecting a bridge crane, several critical factors must be considered to ensure that the crane meets the operational needs efficiently and safely. These factors include load capacity, span and lift height, hoisting and travel speed, duty cycle, and environmental conditions. Here is a more detailed look at each of these factors:
Load Capacity:
Definition: The maximum weight that a crane can safely lift and transport.
Considerations:
- Peak Loads: Ensure the crane can handle the heaviest load it will encounter, including any potential future increases in load requirements.
- Safety Margins: Factor in a safety margin above the expected maximum load to account for any unforeseen circumstances.
- Distribution of Load: Consider how the load will be distributed. Uneven loads can place additional stress on the crane and its components.
- Regulations and Standards: Adhere to industry regulations and standards for load capacity to ensure safety and compliance.
Span and Lift Height:
Span:
- Definition: The horizontal distance between the runways of the bridge crane.
- Workspace Dimensions: Ensure the span matches the dimensions of the workspace. A span that is too short or too long can limit the crane's effectiveness.
- Structural Considerations: Ensure the building structure can support the crane's span, especially for long spans that may require additional support.
Lift Height:
- Definition: The vertical distance the crane can lift the load from the ground.
- Operational Requirements: Match the lift height to the operational requirements, ensuring it can accommodate the tallest items or highest lifts needed.
- Obstructions: Account for any potential obstructions within the lift path, such as beams, pipes, or other equipment.
Hoisting and Travel Speed:
Hoisting Speed:
- Definition: The speed at which the crane can lift and lower the load.
- Efficiency: Faster hoisting speeds can improve productivity but must be balanced with safety considerations.
- Precision: For delicate or precise operations, slower speeds may be necessary to ensure careful handling of the load.
Travel Speed:
- Definition: The speed at which the crane moves horizontally along the runways and the hoist moves along the bridge.
- Workflow Integration: Ensure travel speed aligns with the workflow speed to avoid bottlenecks.
- Safety: Higher speeds require additional safety measures to prevent accidents or collisions.
Duty Cycle:
Definition: The frequency and duration of the crane's use, often expressed as a percentage of operation time over a specific period.
Usage Patterns:
- Light Duty: For occasional or intermittent use, typically with long idle periods between uses.
- Medium Duty: For regular use with moderate frequency and duration.
- Heavy Duty: For continuous or near-continuous use with minimal idle time.
- Component Selection: The duty cycle affects the selection of components, such as motors and brakes, which need to withstand the expected operational demands.
Environmental Conditions:
Indoor vs. Outdoor Use:
- Indoor Cranes: Typically shielded from weather elements but may face challenges like limited space or specific facility layouts.
- Outdoor Cranes: Must withstand weather conditions, including rain, wind, and temperature variations, requiring robust and weather-resistant components.
Temperature:
- Extreme Cold: May require heaters or insulated components to prevent freezing and ensure smooth operation.
- Extreme Heat: May require cooling systems or heat-resistant materials to prevent overheating and ensure longevity.
Humidity:
- High Humidity: Can cause corrosion and rust, necessitating corrosion-resistant materials and regular maintenance.
- Dust and Debris: In dusty environments, additional filtration and sealing may be required to protect the crane's moving parts and electrical components.
- Chemical Exposure: In environments with chemical exposure, materials resistant to specific chemicals and additional protective coatings may be necessary.
By thoroughly evaluating these factors, businesses can ensure that the selected bridge crane not only meets their immediate operational needs but also provides long-term reliability and safety in their specific working environment.
Matching Specifications to Operational Needs:
Choosing the right bridge crane involves aligning its specifications with the specific requirements of the operation it will serve. This ensures that the crane performs optimally, safely, and efficiently. Below are detailed considerations and examples of how to match crane specifications to operational needs.
Case Studies:
Electric hoist trolley for double girder bridge crane for sale Philippines
Crane type: Double girder bridge crane with electric hoist trolley European style
Crane capacity: 35t/5 ton
Crane span: 49m
Crane lifting height: 10m
Crane power supply: 400V60HZ/3Phase
Project location: Philippines
Crane Type: Open Winch Double Girder Overhead Crane
Crane Capacity: 45 Ton
Crane Span: 22.785 m
Crane Lifting Height: 15 m
Crane Power Supply: 415V50HZ3P
Crane Control: Joystick Remote Control
European style double girder bridge crane 40 ton for sale America
Crane specification:
Overhead bridge crane capacity: 40 ton,
Bridge crane span: 22.25m
Crane lifting height:10.688m.
Quantity; 2 sets
Application: Indoor use for die and mold handling
Customization Options:
- Tailored Spans: Customizing the span to fit specific workspace dimensions, ensuring maximum coverage and efficiency.
- Adjustable Lift Heights: Offering adjustable lift heights to accommodate varying load sizes and workspace heights.
- Variable Speeds: Implementing variable speed controls for both hoisting and travel, allowing for precision handling of delicate loads and faster movement for non-sensitive items.
- Specialized Hoists: Using hoists designed for specific applications, such as magnet hoists for lifting metal sheets or grab bucket hoists for handling bulk materials.
- Environmental Adaptations: Customizing materials and components to suit specific environmental conditions, such as corrosion-resistant finishes for marine environments or explosion-proof designs for hazardous locations.
Detailed Considerations:
Load Capacity:
- Ensuring the crane can handle the maximum load, factoring in the weight of attachments and any potential overloading scenarios.
- Consulting with engineers to determine the optimal load capacity that balances safety and operational needs.
Span and Lift Height:
- Conducting a thorough analysis of the workspace dimensions and layout to determine the ideal span and lift height.
- Considering future expansions or changes in the workspace that may require adjustments in span or lift height.
Hoisting and Travel Speed:
- Analyzing the workflow to determine the required speed for lifting and moving loads without causing delays or hazards.
- Implementing speed control mechanisms to allow for adjustments based on the type of load and the precision required.
Duty Cycle:
- Evaluating the frequency and duration of crane use to select components that can withstand the expected operational demands.
- Choosing a duty cycle that matches the intensity of operations, ensuring longevity and reliability of the crane.
Environmental Conditions:
- Assessing indoor vs. outdoor use and the impact of weather conditions, such as temperature extremes, humidity, and exposure to chemicals.
- Selecting materials and finishes that provide durability and resistance to environmental factors, ensuring the crane's longevity and safety.
Matching Specifications to Specific Operational Needs:
- Manufacturing Plants: Light to medium duty cycles, moderate spans, and lift heights suitable for indoor environments. Single girder or underhung cranes may be ideal.
- Heavy Industry: Heavy duty cycles, large spans, and high lift heights to handle substantial loads. Double girder or box girder cranes provide the necessary robustness and capacity.
- Construction Sites: Versatile duty cycles, adaptable spans, and lift heights to accommodate various stages of construction. Gantry cranes with adjustable heights and spans can be highly effective.
- Specialized Applications: For industries like shipbuilding or steel mills, heavy-duty cranes with continuous duty cycles and customized specifications ensure safe and efficient handling of extremely heavy and bulky loads.
By carefully evaluating these considerations and customizing specifications, businesses can ensure their bridge cranes are perfectly suited to their operational needs, maximizing efficiency, safety, and longevity.
Cost Considerations:
When selecting and deploying a bridge crane, understanding the full scope of costs involved is crucial for budgeting and ensuring a return on investment. The cost considerations can be broadly categorized into initial purchase costs, installation costs, and maintenance and operational costs. Here are detailed insights into each of these aspects:
Initial Purchase Cost:
Capacity:
- Influence on Cost: Higher capacity cranes generally cost more due to the need for stronger materials and more robust components.
- Examples: A 5-ton crane will be significantly less expensive than a 50-ton crane because of the differences in structural requirements and materials used.
Design Type:
Single Girder vs. Double Girder:
- Single Girder Cranes: Typically less expensive due to simpler construction and lighter materials.
- Double Girder Cranes: More costly as they provide higher capacities, longer spans, and greater lift heights, requiring additional materials and engineering.
Additional Features:
- Customization: Tailoring a crane to specific operational needs, such as unique span lengths, specialized hoists, or additional safety features, increases the initial cost.
- Advanced Controls: Features like remote operation, automated controls, and variable speed drives add to the cost but can enhance efficiency and safety.
Installation Costs:
Crane Size and Complexity:
- Larger Cranes: Installation of larger cranes, such as those with longer spans or higher capacities, requires more time, labor, and equipment, increasing costs.
- Complex Designs: Cranes with intricate designs or multiple components may need more detailed assembly and calibration, leading to higher installation expenses.
Site Preparation:
- Structural Modifications: Existing structures may need reinforcement or modification to support the new crane, adding to the installation cost.
- Foundation Work: For gantry cranes or heavy-duty bridge cranes, substantial foundation work may be required to ensure stability and safety.
Installation Location:
- Indoor vs. Outdoor: Outdoor installations might require additional weatherproofing and protections against environmental factors, increasing costs.
- Site Accessibility: Difficult-to-access sites may incur higher costs due to the need for specialized equipment or additional labor.
Maintenance and Operational Costs:
Regular Inspections:
- Routine Checks: Regular inspections are essential to identify and address wear and tear, ensuring safe operation and extending the crane's lifespan.
- Frequency: The frequency of inspections should align with the crane's duty cycle and usage intensity, impacting ongoing costs.
Preventive Maintenance:
- Scheduled Maintenance: Includes tasks such as lubrication, cleaning, and adjusting components to prevent breakdowns and maintain performance.
- Replacement Parts: Periodic replacement of parts like cables, hooks, and brakes is necessary to maintain safety and functionality.
Operator Training:
- Initial Training: Training operators on the safe and efficient use of the crane is crucial and can incur upfront costs.
- Ongoing Training: Regular refresher courses and updates on new features or safety protocols ensure that operators remain proficient, contributing to operational costs.
Operational Efficiency:
- Energy Consumption: The energy required to operate the crane is a recurring cost. More efficient cranes with energy-saving features can reduce long-term operational expenses.
- Downtime Costs: Regular maintenance can minimize downtime, but unplanned breakdowns can be costly due to lost productivity and emergency repair expenses.
Environmental Impact:
- Compliance Costs: Ensuring the crane meets environmental regulations may involve additional costs for emissions control or noise reduction features.
- Sustainability: Investing in environmentally friendly technologies, such as energy-efficient motors or recyclable materials, can have higher initial costs but may reduce long-term operational expenses.
By carefully considering these cost factors, businesses can make informed decisions about their bridge crane investments, balancing initial expenditures with long-term benefits to achieve optimal efficiency and cost-effectiveness.
Maintenance Tips for Bridge Cranes:
Maintaining bridge cranes is essential for ensuring safe operation, maximizing uptime, and prolonging their operational lifespan. Here are key maintenance tips to keep bridge cranes in optimal condition:
Regular Inspections:
Purpose: Conduct routine inspections to identify potential issues early and ensure compliance with safety standards.
Components to Inspect:
- Structural Components: Check for signs of wear, corrosion, or deformation in the crane structure, including girders, rails, and connections.
- Mechanical Components: Inspect hoists, trolleys, and end trucks for wear on wheels, brakes, gears, and bearings.
- Electrical Components: Verify the condition of wiring, cables, connectors, and controls to prevent electrical faults.
- Safety Features: Test emergency stop systems, limit switches, and overload protection devices for proper operation.
Preventive Maintenance:
Scheduled Tasks:
- Lubrication: Regularly lubricate moving parts such as gears, bearings, and wheels to reduce friction and wear.
- Bolt Tightening: Check and tighten bolts, nuts, and fasteners to maintain structural integrity and prevent loosening over time.
- Electrical Checks: Inspect electrical connections and components for signs of wear, corrosion, or overheating.
- Cleaning: Keep the crane and its components clean from dirt, dust, and debris that can cause mechanical or electrical issues.
- Manufacturer Guidelines: Follow maintenance schedules and recommendations provided by the crane manufacturer to ensure warranty compliance and optimal performance.
Training for Operators:
Operator Competence:
- Training Programs: Provide comprehensive training for crane operators on safe operating procedures, including load handling, emergency protocols, and equipment limitations.
- Skill Development: Offer ongoing training to keep operators updated on new technologies, regulations, and best practices for crane operation.
Capacity Awareness:
- Load Limits: Ensure operators understand the crane's load capacity and adhere to weight limits to prevent overloading and structural damage.
- Feature Familiarization: Familiarize operators with specific crane features, such as variable speed controls, automation systems, and safety devices, to enhance operational efficiency and safety.
Safety :
- Reporting Procedures: Encourage operators to report any maintenance issues or safety concerns promptly to prevent accidents and downtime.
- Team Collaboration: Foster a collaborative environment where operators and maintenance personnel work together to address maintenance needs and ensure continuous improvement in crane performance.
By implementing these maintenance tips, businesses can minimize the risk of unplanned downtime, extend the lifespan of their bridge cranes, and maintain a safe working environment for operators and personnel. Regular inspections, preventive maintenance, and ongoing operator training are integral to achieving efficient and reliable crane operations.
Conclusion:
Selecting the right bridge crane capacity and matching it with appropriate specifications is crucial for ensuring safety, efficiency, and productivity in industrial operations. The diverse range of crane designs and their respective specifications empowers businesses to make informed decisions that align with their specific operational needs. Here's a detailed summary of the key points discussed:
Importance of Choosing the Right Crane Capacity and Specifications:
- Safety: Properly matching crane capacity to the weight of loads and operational demands reduces the risk of accidents and equipment failure.
- Efficiency: Optimal crane specifications, including span, lift height, hoisting speed, and duty cycle, enhance operational efficiency by minimizing downtime and maximizing productivity.
- Cost-effectiveness: Investing in a crane that precisely meets operational requirements ensures cost-effectiveness over its lifecycle through reduced maintenance costs and improved performance.
Different Crane Designs and Specifications:
- Single Girder vs. Double Girder Cranes: Variations in span, lift height, and capacity cater to different load requirements and operational environments.
- Box Girder and Gantry Cranes: Specialized designs provide enhanced strength and versatility for handling heavier loads and spanning larger areas.
- Environmental Considerations: Choosing between indoor and outdoor cranes based on environmental factors such as temperature, humidity, and exposure to corrosive elements.
Consulting with Experts and Assessing Requirements:
- Expert Guidance: Collaborating with crane manufacturers, engineers, and consultants ensures thorough evaluation of operational requirements and adherence to safety standards.
- Technical Support: Accessing specialized knowledge and experience helps businesses navigate complex crane specifications and make informed decisions.
In conclusion, by carefully assessing their specific operational requirements, consulting with experts, and understanding the diverse range of crane designs and specifications available, businesses can select the optimal bridge crane. This approach not only enhances safety and efficiency but also maximizes productivity and operational effectiveness, contributing to long-term success in industrial operations. Choosing the right bridge crane is a strategic investment that pays dividends in safety, efficiency, and profitability for years to come.