Customization Options for Top Running Double Girder Bridge Cranes
Explore tailored enhancements for top running double girder bridge cranes, optimizing performance, safety & efficiency to meet specific industrial needs.
Customization Options for Top Running Double Girder Bridge Cranes
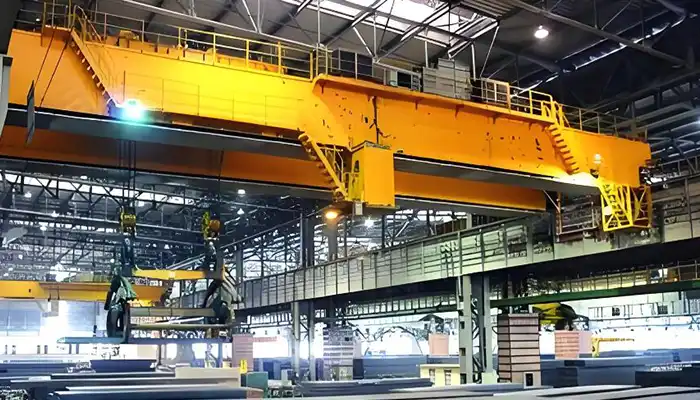
Overview of Top Running Double Girder Bridge Cranes
Top running double girder bridge cranes are industrial cranes where the bridge, supported by two girders, runs on rails mounted on top of runway beams. These beams are usually supported by the building's columns, allowing the crane to travel along the length of the facility. The double girder configuration provides increased strength and stability, making it suitable for heavy-duty lifting. The hoist and trolley, which move along the bridge, lift and transport materials across the workspace.
Top running double girder bridge cranes are integral to many industrial environments due to their robustness and versatility. They are commonly used in sectors such as manufacturing, steel production, automotive, and warehousing. These cranes facilitate the efficient and safe handling of heavy loads, significantly improving operational productivity. Their ability to cover large work areas and lift heavy materials makes them indispensable for tasks that require precision and reliability.
Purpose of Customization
- Enhancing Performance and Efficiency: Customization allows top running double girder bridge cranes to be tailored to specific operational needs, enhancing their performance and efficiency. By integrating features such as variable frequency drives, advanced control systems, and precision positioning, these cranes can be optimized for smoother operation, reduced wear and tear, and lower energy consumption. Customizing cranes to match the exact requirements of a task or workflow ensures maximum efficiency and productivity.
- Adapting to Specific Operational Needs: Every industrial application has unique demands, and customization enables cranes to meet these specific needs. Whether it's adjusting the crane's load capacity, modifying the span to fit within a particular facility, or adding specialized lifting attachments, customization ensures that the crane is perfectly suited to its intended use. This adaptability not only improves the crane's performance but also enhances safety and operational flexibility. Custom features such as weatherproofing, automation capabilities, and ergonomic controls make the crane more effective in diverse environments, from outdoor construction sites to indoor manufacturing plants.
In summary, the customization of top running double girder bridge cranes is essential for maximizing their utility in various industrial applications. By tailoring these cranes to meet specific requirements, businesses can achieve greater efficiency, safety, and operational excellence.
Types of Customization Options
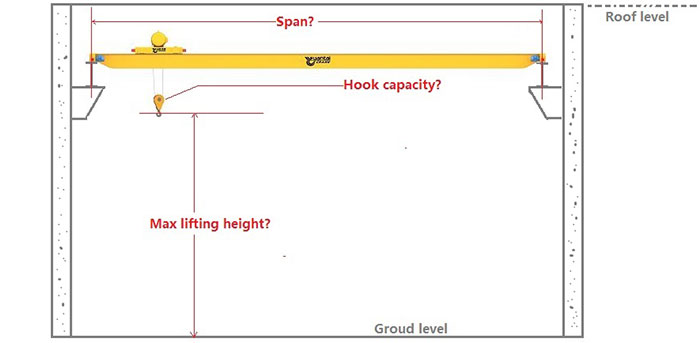
Main parameters of top running double girder bridge cranes needed to custom your crane
Capacity Customization
Adjusting Load Capacity for Different Applications
One of the primary customization options for top running double girder bridge cranes is adjusting the load capacity. Load capacity refers to the maximum weight the crane can safely lift and move. Depending on the industry and specific application, the required load capacity can vary significantly. Customizing the crane's capacity ensures it can handle the specific weights involved in the operations, whether it's lifting heavy machinery, large containers, or bulky materials.
Examples of Industries and Their Capacity Requirements
- Steel Manufacturing: Requires high-capacity cranes capable of lifting heavy steel coils, slabs, and other large materials, often exceeding 50 tons.
- Automotive Industry: Typically uses cranes with moderate to high capacities (ranging from 5 to 20 tons) for lifting car parts, engines, and assemblies.
- Warehousing and Logistics: May require lower capacity cranes (1 to 5 tons) for handling pallets, boxes, and other packaged goods.
- Construction: Needs cranes with variable capacities depending on the project, ranging from 10 to 30 tons or more for lifting building materials and equipment.
Span and Lift Height Adjustments
Customizing Crane Span for Facility Size
The span of a crane is the distance between the rails on which the crane travels. Customizing the span is crucial to ensure that the crane fits perfectly within the width of the facility. A well-fitted span maximizes the crane's operational range and ensures efficient use of the available space. This customization is especially important in facilities with unique dimensions or layouts, where standard spans may not be suitable.
Modifying Lift Height for Specific Tasks
Lift height customization involves adjusting the vertical reach of the crane to suit specific tasks. Different operations may require varying lift heights to accommodate the handling of materials at different elevations. For instance, in a facility with high shelving or storage racks, a greater lift height is necessary. Conversely, in environments where materials are primarily handled at floor level, a lower lift height may suffice. By customizing the lift height, businesses can ensure that the crane operates effectively within their specific vertical constraints, enhancing both safety and productivity.
In summary, customizing the load capacity, span, and lift height of top running double girder bridge cranes allows businesses to tailor the equipment to their precise operational needs. This ensures optimal performance, safety, and efficiency in handling a wide range of materials and tasks across various industries.
Speed Control
Variable Frequency Drives for Hoisting and Travel
Variable frequency drives (VFDs) are essential for customizing the speed control of top running double girder bridge cranes. VFDs allow precise control over the crane's hoisting and travel speeds by adjusting the motor's frequency and voltage. This flexibility enables smooth acceleration and deceleration, reducing mechanical stress on the crane components and improving overall safety and efficiency. VFDs can be programmed to suit specific operational requirements, providing operators with the ability to fine-tune the crane's performance for various tasks.
Benefits of Adjustable Speed Settings
- Enhanced Precision: Adjustable speed settings allow operators to perform delicate lifting operations with greater accuracy, which is especially important when handling fragile or sensitive materials.
- Improved Safety: By controlling the speed, operators can minimize the risk of accidents and collisions, particularly in environments with high traffic or confined spaces. Slow speeds can be used for precision movements, while faster speeds can be employed for longer, unobstructed travel distances.
- Reduced Wear and Tear: Smooth acceleration and deceleration help to reduce the mechanical stress on the crane's components, leading to less wear and tear and extending the equipment's lifespan.
- Energy Efficiency: VFDs optimize the crane's energy consumption by adjusting the motor's power output to match the operational load, resulting in significant energy savings over time.
Safety Enhancements
- Anti-Collision Systems: Anti-collision systems are crucial safety features that help prevent collisions between the crane and other objects or structures within the facility. These systems use sensors to detect obstacles in the crane's path and automatically slow down or stop the crane to avoid collisions. This is particularly important in busy industrial environments where multiple cranes or other machinery operate simultaneously.
- Overload Protection Mechanisms: Overload protection mechanisms ensure that the crane does not lift more weight than it is designed to handle. These systems monitor the load being lifted and trigger an alarm or shut down the hoisting operation if the load exceeds the crane's rated capacity. Overload protection is vital for preventing equipment damage and ensuring the safety of both the operator and the surrounding environment.
- Emergency Stop Features: Emergency stop features provide a critical safety mechanism that allows operators to quickly halt all crane operations in the event of an emergency. These features are typically integrated into the control system and can be activated by pressing a clearly marked emergency stop button. This immediate response capability is essential for preventing accidents and mitigating potential hazards in urgent situations.
Incorporating advanced speed control options and essential safety enhancements significantly improves the performance and reliability of top running double girder bridge cranes. These customizations not only enhance operational efficiency but also ensure a safer working environment, protecting both personnel and equipment.
Operator Controls
Wireless Remote Controls
Wireless remote controls provide operators with the flexibility to operate the crane from a distance, enhancing safety and convenience. These controls use radio frequency (RF) technology to communicate with the crane, allowing operators to maneuver loads from a safe location, away from potential hazards. Wireless remote controls can feature intuitive interfaces with easy-to-use buttons and joysticks, ensuring precise control over the crane's movements.
Benefits:
- Increased operator safety by allowing control from a distance
- Enhanced visibility and maneuverability in tight spaces
- Improved operational efficiency by reducing the need for multiple operators
Ergonomic Control Stations
Ergonomic control stations are designed to improve operator comfort and efficiency. These stations can be customized with adjustable seats, armrests, and control panels that are positioned for optimal reach and usability. Ergonomic designs help reduce operator fatigue, enhance precision in crane operation, and promote a safer working environment by minimizing the risk of repetitive strain injuries.
Features:
- Adjustable components for personalized comfort
- Intuitive layout of controls for easy access and use
- Integrated displays and indicators for real-time feedback on crane status
Automation and Semi-Automation Options
Automation and semi-automation options allow for the integration of advanced technologies to streamline crane operations. Fully automated cranes can perform lifting and transporting tasks with minimal human intervention, using pre-programmed instructions and advanced sensors to navigate and position loads accurately. Semi-automated systems provide assistance to operators, such as automated lifting sequences or collision avoidance, while still allowing for manual control when necessary.
Advantages:
- Enhanced precision and repeatability in lifting operations
- Reduced labor costs and increased productivity
- Improved safety through automated monitoring and control systems
Applications:
- Fully automated systems are ideal for repetitive tasks in high-volume manufacturing environments.
- Semi-automated systems are suitable for operations requiring both manual intervention and automated assistance, such as in assembly lines or material handling in warehouses.
By incorporating advanced operator controls, including wireless remote controls, ergonomic control stations, and automation options, top running double girder bridge cranes can be tailored to meet specific operational needs. These enhancements not only improve the efficiency and safety of crane operations but also contribute to a more comfortable and user-friendly experience for operators.
Environmental Adaptations
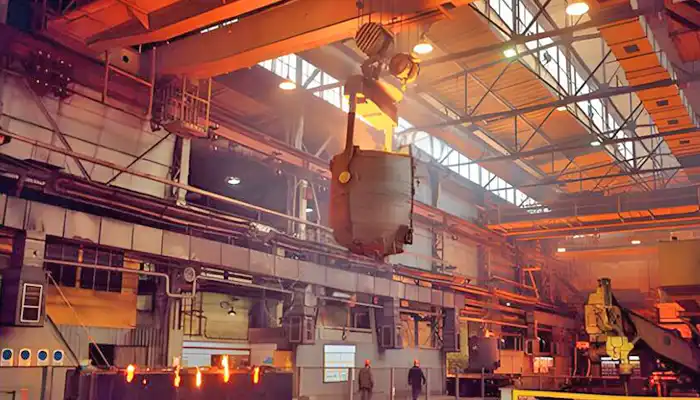
Weatherproofing for Outdoor Use
Weatherproofing is essential for cranes that operate in outdoor environments. This customization involves sealing and protecting the crane's components from exposure to rain, snow, wind, and other harsh weather conditions. Weatherproofing ensures that the crane can function reliably and safely regardless of the weather.
Benefits:
- Protection against moisture, preventing rust and corrosion
- Enhanced durability and longevity of the crane components
- Reliable performance in various weather conditions, reducing downtime
Dust and Corrosion-Resistant Coatings
Dust and corrosion-resistant coatings are applied to the crane's surfaces to protect against abrasive particles and corrosive elements. These coatings are especially important in environments with high levels of dust, such as construction sites, or corrosive materials, such as chemical plants.
Features:
- Special coatings that resist the buildup of dust and debris
- Corrosion-resistant materials that protect against chemical exposure and salt spray
- Extended service life and reduced maintenance costs
Applications:
- Construction sites with heavy dust and debris
- Chemical plants where exposure to corrosive substances is common
- Coastal areas with high salt content in the air
Temperature Control for Extreme Environments
Temperature control adaptations are crucial for cranes operating in extreme temperature conditions, whether hot or cold. This customization includes features like insulated cabins, heating systems, and cooling mechanisms to ensure that the crane can operate efficiently and safely in extreme temperatures.
Benefits:
- Insulated cabins to protect operators from extreme cold or heat
- Heating systems to prevent the freezing of mechanical components in cold environments
- Cooling systems to prevent overheating and ensure reliable operation in hot climates
Applications:
- Arctic or high-altitude environments where temperatures are extremely low
- Desert or tropical regions with high temperatures and humidity
- Industrial facilities with high-temperature processes or furnaces
By integrating environmental adaptations such as weatherproofing, dust and corrosion-resistant coatings, and temperature control mechanisms, top running double girder bridge cranes can be customized to operate effectively in diverse and challenging environments. These adaptations not only protect the crane and its components but also ensure the safety and comfort of operators, leading to improved performance and reliability in various settings.
Specialized Attachments
Lifting Devices
Custom Hooks and Grabs
Custom hooks and grabs are tailored lifting devices designed to handle specific types of loads. These attachments can be customized in shape, size, and capacity to suit various materials and lifting requirements. Custom hooks are ideal for lifting irregularly shaped or difficult-to-handle items, while grabs can securely grasp materials like logs, scrap metal, or loose bulk materials.
Benefits:
- Enhanced safety and efficiency in lifting operations
- Reduced risk of damage to the load
- Improved handling of irregular or awkwardly shaped items
Applications:
- Scrap yards and recycling centers for handling scrap metal
- Forestry operations for lifting and transporting logs
- Construction sites for moving heavy and irregularly shaped materials
Magnets and Vacuum Lifters
Magnets and vacuum lifters are specialized attachments used for lifting ferrous and non-ferrous materials, respectively. Magnetic lifters use powerful electromagnets to securely lift and move metal objects, while vacuum lifters create a suction grip to lift non-metallic items such as glass, plastic, or wooden panels.
Features:
- Magnetic lifters can handle heavy metal objects quickly and efficiently
- Vacuum lifters offer gentle handling for fragile or delicate materials
- Both types of lifters can be easily attached and detached from the crane
Applications:
- Metal fabrication shops for moving steel plates and parts
- Glass manufacturing facilities for handling large glass panels
- Woodworking and furniture industries for lifting wooden boards and panels
Spreaders and Beams for Handling Bulky Items
Spreaders and beams are lifting attachments designed to distribute the load evenly across multiple lifting points. These devices are particularly useful for handling bulky or long items that require support at multiple points to prevent bending or damage. Spreaders and beams can be customized in length and capacity to suit specific applications.
Benefits:
- Even distribution of weight to prevent damage to the load
- Increased stability and control during lifting operations
- Versatility in handling a wide range of bulky items
Applications:
- Shipping and logistics for lifting and moving large containers
- Construction sites for handling long beams and structural components
- Warehouses for moving oversized pallets and packages
By incorporating specialized lifting devices such as custom hooks and grabs, magnets and vacuum lifters, and spreaders and beams, top running double girder bridge cranes can be adapted to handle a wide variety of materials and tasks. These attachments enhance the crane's versatility, safety, and efficiency, making it a valuable tool for diverse industrial applications.
Hoist and Trolley Options
Open Winch vs. Hoist Trolley Systems
Open Winch Systems
Open winch systems are designed for heavy-duty applications that require high lifting capacities and long lifting heights. The open design allows for easy inspection, maintenance, and cooling, making it suitable for demanding industrial environments. Open winch systems provide precise control over lifting and lowering operations, ensuring safe and efficient handling of heavy loads.
Benefits:
- High lifting capacity suitable for heavy-duty applications
- Easy access for maintenance and inspection
- Superior cooling and durability in harsh environments
Applications:
- Steel mills and foundries for handling heavy materials
- Heavy machinery manufacturing for lifting large components
- Construction sites for moving large structural elements
Hoist Trolley Systems
Hoist trolley systems are compact, versatile, and ideal for a wide range of lifting applications. The hoist is mounted on a trolley that moves along the bridge girders, allowing for efficient horizontal movement. These systems are suitable for medium to heavy-duty lifting tasks and can be easily integrated with other crane components. Hoist trolleys can be electric or manual, depending on the application requirements.
Benefits:
- Compact and versatile design for various lifting tasks
- Smooth and efficient horizontal movement
- Easy integration with existing crane systems
Applications:
- Warehouses and distribution centers for handling goods and materials
- Manufacturing plants for assembly line operations
- Maintenance facilities for lifting and moving equipment
Dual Hoist Configurations for Synchronized Lifting
Dual hoist configurations involve the use of two hoists operating in synchronization, allowing for the precise handling of long or bulky loads. This setup provides greater stability and control, reducing the risk of load swinging or tipping. Dual hoist systems are particularly useful in applications where balanced lifting is critical, such as when handling long beams, pipes, or large machinery.
Benefits:
- Enhanced stability and control for lifting long or bulky items
- Reduced risk of load swinging or tipping
- Increased lifting capacity and flexibility
Applications:
- Construction and infrastructure projects for lifting long beams and girders
- Shipyards for handling large sections of ships and vessels
- Manufacturing facilities for moving large machinery and equipment
By offering a variety of hoist and trolley options, including open winch systems, hoist trolley systems, and dual hoist configurations, top running double girder bridge cranes can be customized to meet the specific needs of different industrial applications. These options enhance the crane's versatility, performance, and safety, ensuring efficient and reliable handling of diverse materials and tasks.
Performance Enhancements
Energy Efficiency
Energy-Saving Drives and Motors
Energy-saving drives and motors are essential components for improving the energy efficiency of top running double girder bridge cranes. Variable frequency drives (VFDs) adjust the speed and torque of the motors based on the load requirements, optimizing power consumption. High-efficiency motors are designed to use less energy while providing the same or greater power output compared to standard motors. These upgrades not only reduce operational costs but also minimize the environmental impact.
Benefits:
- Reduced energy consumption and operational costs
- Lower carbon footprint and environmental impact
- Enhanced motor performance and longevity
Applications:
- Facilities looking to reduce their energy bills
- Operations with sustainability initiatives
- Industries with high crane usage, such as manufacturing and logistics
Regenerative Braking Systems
Regenerative braking systems capture and reuse energy that would otherwise be lost during braking. When the crane slows down or stops, the regenerative braking system converts the kinetic energy into electrical energy, which is then fed back into the power grid or used to power other crane operations. This not only improves energy efficiency but also reduces wear on the braking system.
Benefits:
- Energy recovery and reduced power consumption
- Lower maintenance costs due to reduced brake wear
- Improved overall crane efficiency
Applications:
- High-frequency crane operations where frequent stopping is required
- Facilities aiming to maximize energy efficiency
- Industries focused on sustainability and cost reduction
Precision and Accuracy
Load Positioning Systems
Load positioning systems enhance the precision and accuracy of crane operations by providing real-time data on the load's position. These systems use advanced technologies such as laser positioning, GPS, or RFID to ensure that loads are placed exactly where they need to be. Operators can use this information to make fine adjustments, improving the accuracy of lifting and placing operations.
Benefits:
- Enhanced precision in load handling
- Reduced risk of load damage and accidents
- Increased efficiency and productivity
Applications:
- Assembly lines requiring precise placement of components
- Warehouses with high-density storage requirements
- Construction sites where accurate placement of materials is critical
Advanced Sensors and Feedback Mechanisms
Advanced sensors and feedback mechanisms provide real-time data on various crane parameters, such as load weight, speed, and position. These sensors can detect anomalies and provide immediate feedback to operators, allowing for quick adjustments and preventing potential issues. Integrating these technologies ensures smoother and safer crane operations.
Benefits:
- Real-time monitoring and feedback for improved safety
- Early detection of potential issues, reducing downtime
- Enhanced control over crane operations
Applications:
- Safety-critical environments such as chemical plants and refineries
- High-precision manufacturing processes
- Facilities aiming to minimize operational risks and downtime
By incorporating energy-efficient components, regenerative braking systems, load positioning technologies, and advanced sensors, top running double girder bridge cranes can achieve significant performance enhancements. These upgrades not only improve the crane's efficiency and precision but also contribute to safer and more sustainable operations across various industries.
Integration with Facility Systems
Crane Management Software
Monitoring and Control Systems
Crane management software provides comprehensive monitoring and control of crane operations, enabling real-time tracking of various parameters such as load weight, position, and movement speed. These systems often feature user-friendly interfaces and dashboards that allow operators and managers to oversee crane activities efficiently. Monitoring systems can also alert operators to potential issues, ensuring prompt intervention and maintenance.
Benefits:
- Real-time monitoring and control for enhanced operational efficiency
- Improved safety through proactive issue detection and alerts
- Streamlined operations with centralized management and oversight
Applications:
- Large industrial facilities with multiple cranes
- Environments requiring precise load handling and tracking
- Facilities focused on enhancing operational safety and efficiency
Integration with ERP and Maintenance Systems
Integrating crane management software with enterprise resource planning (ERP) and maintenance systems ensures seamless coordination across all operational aspects. This integration allows for automated scheduling of maintenance tasks based on usage data and wear patterns, enhancing the reliability and longevity of the cranes. It also facilitates better resource management, inventory control, and operational planning.
Benefits:
- Automated maintenance scheduling based on real-time data
- Improved resource allocation and inventory management
- Enhanced operational planning and coordination
Applications:
- Manufacturing plants with complex workflows and resource management needs
- Warehouses and logistics centers aiming to optimize maintenance and operations
- Any facility seeking to enhance overall operational efficiency and reliability
Interoperability with Other Equipment
Coordination with Conveyors and Automated Systems
Ensuring interoperability between cranes and other equipment, such as conveyors and automated systems, is crucial for streamlined material handling processes. Cranes can be integrated with automated systems to coordinate the movement of materials, improving overall workflow efficiency. This coordination allows for seamless transfer of loads between different handling equipment, reducing manual intervention and increasing productivity.
Benefits:
- Improved workflow efficiency through coordinated operations
- Reduced need for manual handling, enhancing safety and productivity
- Streamlined material transfer processes
Applications:
- Automated warehouses and distribution centers
- Manufacturing facilities with integrated production lines
- Logistics hubs requiring efficient material handling solutions
Compatibility with Other Cranes and Lifting Devices
Compatibility with other cranes and lifting devices ensures that different pieces of equipment can work together harmoniously. This interoperability is essential in facilities where multiple cranes or lifting devices are used simultaneously or sequentially. Ensuring compatibility can involve standardizing control systems, synchronization protocols, and safety features across all equipment.
Benefits:
- Enhanced operational flexibility and efficiency
- Synchronized lifting operations for complex tasks
- Improved safety through standardized control and safety protocols
Applications:
- Large construction sites with multiple lifting operations
- Industrial facilities with various types of cranes and lifting devices
- Environments requiring coordinated lifting and material handling activities
By integrating crane management software with monitoring and control systems, ERP and maintenance systems, and ensuring interoperability with other equipment, top running double girder bridge cranes can be seamlessly integrated into facility operations. These enhancements lead to improved efficiency, safety, and coordination, making crane operations more reliable and effective in diverse industrial settings. Open winch trolley top running double girder bridge cranes for your reference
Case Studies and Examples
Industry-Specific Customizations
Customizations for Steel Manufacturing
Steel manufacturing facilities require robust crane systems capable of handling heavy loads and operating in harsh environments. Customizations for steel manufacturing often include:
- High Load Capacity: Cranes with capacities ranging from 20 tons to over 100 tons to lift heavy steel coils, slabs, and structural components.
- Heat Resistance: Special coatings and materials to withstand high temperatures and exposure to molten metal.
- Precise Control: Advanced positioning systems for accurate placement of steel materials during production and storage.
- Safety Features: Overload protection and anti-collision systems to ensure safe operations in busy manufacturing environments.
Adaptations for Automotive Assembly Lines
Automotive assembly lines require cranes that can handle medium to heavy loads efficiently and facilitate smooth production processes. Customizations for automotive assembly lines often include:
- Medium Capacity: Cranes with capacities ranging from 5 tons to 20 tons for lifting car bodies, engines, and components.
- Fast and Precise Movements: High-speed hoisting and travel capabilities to support rapid assembly line operations.
- Integration with Automation: Compatibility with automated systems for seamless material handling and assembly processes.
- Compact Design: Hoist trolley systems for flexible movement along assembly stations and tight spaces.
Special Features for Warehousing and Logistics
Warehousing and logistics operations require cranes that prioritize efficiency, versatility, and safety in handling various types of goods and materials. Customizations for warehousing and logistics often include:
- Variable Capacities: Cranes with capacities ranging from 1 ton to 10 tons to handle palletized goods, containers, and packages.
- Space Optimization: Span and lift height adjustments to maximize vertical and horizontal storage space utilization.
- Safety and Efficiency Enhancements: Wireless remote controls for flexible operation, anti-collision systems to prevent accidents, and energy-efficient drives to minimize operational costs.
- Integration with Conveyor Systems: Coordination with conveyor belts and automated storage systems for seamless material flow and distribution.
These case studies illustrate how top running double girder bridge cranes can be customized to meet specific requirements and challenges in different industries. By adapting crane designs, features, and functionalities, manufacturers can optimize operational efficiency, enhance safety standards, and support the unique needs of various industrial applications.
Frequently Asked Questions
What are the benefits of customizing a double girder bridge crane?
Customizing a double girder bridge crane offers several benefits:
- Optimized Performance: Tailoring the crane to specific operational needs improves efficiency and productivity.
- Enhanced Safety: Custom features such as anti-collision systems and precise control mechanisms reduce the risk of accidents.
- Increased Versatility: Adaptations like variable speed control and specialized attachments enable the crane to handle diverse tasks and materials effectively.
- Long-Term Cost Savings: Energy-efficient components and reduced downtime from customized features contribute to lower operational costs over time.
How can I determine the best customization options for my application?
To determine the best customization options for your application:
- Assess Operational Needs: Identify specific requirements such as load capacities, environmental conditions, and operational constraints.
- Consult with Experts: Engage with crane manufacturers or consultants who specialize in crane customization to discuss your unique needs and explore available options.
- Consider Industry Standards: Ensure that customizations align with industry standards and safety regulations applicable to your operations.
- Evaluate ROI: Assess the potential return on investment (ROI) based on improved efficiency, reduced downtime, and operational cost savings.
What are the costs associated with crane customization?
The costs of crane customization can vary based on:
- Scope of Customization: Extent and complexity of modifications required.
- Equipment and Materials: Cost of specialized components, such as advanced control systems or custom attachments.
- Labor and Installation: Charges for engineering, installation, and commissioning of customized features.
- Maintenance and Support: Consider long-term maintenance costs and support services for custom features.
How do custom features impact the maintenance of the crane?
Custom features can impact crane maintenance in various ways:
- Specific Maintenance Requirements: Customized components may require specialized maintenance procedures and trained personnel.
- Increased Reliability: Well-designed custom features can reduce wear and tear, leading to fewer maintenance interventions.
- Longevity: Properly maintained custom features can extend the overall lifespan of the crane.
- Support and Expertise: Access to manufacturer support and expertise for maintenance and troubleshooting of custom components.
Can existing cranes be retrofitted with new customization options?
Yes, existing cranes can often be retrofitted with new customization options, depending on their design and condition:
- Compatibility Assessment: Evaluate the structural integrity and mechanical suitability of the crane for retrofitting.
- Engineering Evaluation: Engage with crane specialists to assess feasibility and develop retrofitting plans.
- Cost-Benefit Analysis: Consider the cost of retrofitting versus potential benefits such as improved performance, safety enhancements, and extended lifespan.
- Regulatory Compliance: Ensure that retrofitted features meet current safety standards and regulatory requirements.
Retrofitting allows you to upgrade older cranes with modern technologies and features, extending their usability and adapting them to evolving operational needs.
Conclusion
Customizing double girder bridge cranes is crucial for maximizing their performance and meeting the specific needs of diverse industries. By tailoring cranes with specialized features and adaptations, businesses can enhance operational efficiency, improve safety standards, and achieve greater versatility in material handling tasks. Whether optimizing load capacities, integrating advanced control systems, or adapting to environmental challenges, customization ensures that cranes operate at their highest potential, contributing to overall productivity and profitability.