Overhead Cranes Reduce Steel Production Costs & Environmental Impact
How do energy-efficient overhead cranes contribute to cost savings and sustainability in steel manufacturing? Check how bridge cranes benefit steel production.
Overhead cranes, often referred to as bridge cranes or overhead traveling cranes, are indispensable mechanical devices in various industrial sectors, playing a pivotal role in material handling and manufacturing processes. These robust structures are comprised of a horizontal beam, often called a bridge, that traverses a factory floor on a set of parallel runways, while a hoist or trolley moves loads up and down. Overhead cranes come in different types and configurations, each tailored to specific applications, making them versatile assets in the industrial landscape.
Double girder ladle crane for steel production
The steel production industry is known for its high energy consumption and environmental impact. The immense energy requirements for processes like melting, rolling, and forging are not only costly but also contribute significantly to carbon emissions and resource depletion. As the world seeks more sustainable and cost-effective ways of steel production, energy efficiency has become a paramount concern. Energy-efficient practices not only reduce operational costs but also help in minimizing the carbon footprint of the steel industry.
The purpose of this article is to explore how energy-efficient overhead cranes can make a substantial contribution to addressing the challenges of energy consumption, cost savings, and environmental impact in the steel manufacturing sector. By examining the significance of overhead cranes in steel production, the role of energy-efficient technology, and the resulting economic and environmental benefits, we aim to provide a comprehensive understanding of this innovative approach. We will also delve into real-world examples, challenges, and emerging trends in the use of energy-efficient overhead cranes, shedding light on their potential to shape the future of steel manufacturing. So, let's embark on this journey to uncover how these remarkable machines can revolutionize the steel industry.
Energy Efficiency in Steel Production
The steel industry is renowned for its massive energy appetite, consuming a substantial portion of the world's total energy resources. To put this into perspective, steel production accounts for approximately 7-9% of the world's total energy consumption. The energy-intensive nature of steel manufacturing stems from various stages of the process, including iron ore smelting, steelmaking, and subsequent processing and finishing.
The primary sources of energy consumption in steel production include the following:
- Blast Furnaces: Iron ore is reduced into molten iron using coke and coal in blast furnaces. This stage is extremely energy-intensive.
- Electric Arc Furnaces (EAFs): In EAF steelmaking, scrap steel is melted using electric arcs. While more energy-efficient than blast furnaces, they still require substantial electricity.
- Rolling Mills: The shaping and rolling of steel into various products involve high energy demands.
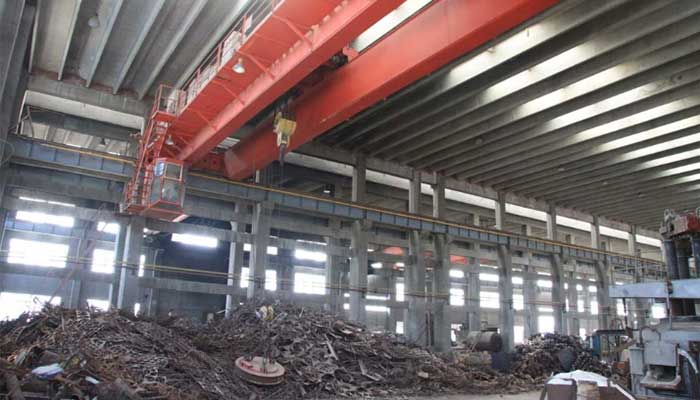
Importance of reducing energy consumption
Reducing energy consumption in steel production is of paramount importance for several compelling reasons:
- Cost Savings:Energy costs are a significant expense for steel manufacturers. By adopting energy-efficient practices, companies can significantly reduce operational costs, leading to improved profitability.
- Environmental Impact:The steel industry is a major contributor to carbon emissions and resource depletion. Lowering energy consumption can help reduce the industry's carbon footprint and alleviate environmental concerns.
- Sustainability:As the world increasingly focuses on sustainable practices, energy-efficient steel production becomes a key factor in maintaining a competitive edge in the market.
- Regulatory Compliance:Many countries have imposed strict energy efficiency regulations, and adherence to these standards is essential to avoid fines and maintain a positive public image.
The role of technology in energy efficiency
Technology plays a pivotal role in enhancing energy efficiency in steel production. Some of the key technological advancements and strategies include:
- Energy-Efficient Equipment:The utilization of state-of-the-art machinery and equipment, including energy-efficient overhead cranes, can substantially reduce energy consumption in material handling and manufacturing processes.
- Process Optimization:Continuous improvement in the design and operation of steel production processes, such as the recycling of waste heat and the utilization of alternative energy sources, contributes to energy conservation.
- Data Analytics:Advanced data analytics and automation enable real-time monitoring and control of energy usage, allowing for quick adjustments and optimizations in response to changing conditions.
- Renewable Energy Integration:The incorporation of renewable energy sources like wind and solar power into steel plants helps reduce reliance on fossil fuels and lower carbon emissions.
As we progress in this exploration, we will delve deeper into how energy-efficient overhead cranes, as a part of these technological advancements, can make a significant impact on energy efficiency in the steel industry.
Overhead Cranes in Steel Manufacturing
Overhead cranes, a fundamental part of steel manufacturing facilities, are heavy-duty lifting devices designed to move materials and products within a factory or production environment. They are characterized by a horizontal bridge that travels along elevated runways, offering unparalleled versatility in material handling. Overhead cranes are used in a wide range of industries, including automotive, construction, and, significantly, in steel manufacturing plants.
Their significance in steel production processes
The significance of overhead cranes in steel production processes cannot be overstated. These cranes are pivotal in several key aspects of steel manufacturing:
- Raw Material Handling:Overhead cranes are employed for transporting and positioning raw materials, such as iron ore, coal, and scrap metal, to various stages of the steel production process. This efficient material handling is a critical prerequisite for smooth operations.
- Steel Production:Overhead cranes play a central role in steelmaking, as they facilitate the movement of molten metal in ladles, pouring it into molds for casting, and transferring steel products to cooling areas. This precise handling ensures product quality and minimizes losses.
- Product Finishing:After steel products are formed, overhead cranes are used for transporting and positioning them for further processing, including cutting, cooling, and inspection.
- Maintenance and Repairs:Overhead cranes are invaluable for maintaining and repairing equipment in steel plants, enabling workers to access hard-to-reach areas with ease and safety.
The reliability and efficiency of overhead cranes are essential to the continuous flow of steel production processes. Any improvement in their energy efficiency can have a significant positive impact on overall operational efficiency and cost-effectiveness.
Types of overhead cranes used in the industry
In steel manufacturing, several types of overhead cranes are utilized, each designed for specific tasks:
- Bridge Cranes:Also known as single girder or double girder cranes, these are versatile and commonly used for general material handling and steel production tasks.
- Gantry Cranes:Gantry cranes are mobile cranes mounted on legs or wheels that move on a track or rails. They are well-suited for outdoor operations and can handle heavy loads.
- Ladle Cranes:These specialized cranes are designed for the precise handling of ladles filled with molten metal, a crucial step in the steelmaking process.
- Scrap Handling Cranes:These cranes are optimized for the efficient and safe handling of scrap metal, a common material used in steel recycling.
- Coil Handling Cranes:Coil cranes are designed to safely and efficiently transport large steel coils within the production facility.
The choice of overhead crane type depends on the specific needs of the steel manufacturing process. Energy-efficient variants of these cranes have become increasingly important as steel plants seek to reduce their energy consumption and environmental impact while maintaining productivity.
Energy-Efficient Overhead Cranes
Energy-efficient overhead cranes are an advanced breed of lifting equipment designed to reduce energy consumption while maintaining or improving performance. These cranes incorporate various features and technologies that set them apart from traditional models. Key characteristics of energy-efficient overhead cranes include:
- Variable Speed Drives:Energy-efficient cranes are equipped with variable speed drives (VSDs) for precise control over lifting and movement, allowing operators to adjust speed as needed. This feature minimizes unnecessary energy consumption during idle times.
- Regenerative Braking:Energy-efficient cranes often use regenerative braking systems, which capture and convert kinetic energy into electricity during deceleration. This recovered energy can be used to power other crane functions or returned to the grid.
- High-Quality Materials:These cranes are constructed with high-quality, lightweight materials to reduce the overall weight and energy requirements during lifting and movement.
- Smart Control Systems:Energy-efficient cranes are equipped with advanced control systems that optimize crane movements and reduce unnecessary starts and stops, resulting in energy savings.
- LED Lighting:Utilizing energy-efficient LED lighting for crane work areas and control cabins reduces power consumption compared to traditional lighting systems.
Technologies and features that enhance energy efficiency
Several technologies and features enhance the energy efficiency of overhead cranes:
- Energy Monitoring Systems:These systems provide real-time data on energy consumption, allowing operators to make informed decisions to optimize energy usage.
- Load-Dependent Speed Control:Energy-efficient cranes can adjust their speed according to the load they are carrying, minimizing energy waste when lifting lighter loads.
- Inverter Control:Inverters are used to regulate the voltage and frequency of the crane's motor, resulting in more efficient energy usage.
- Remote Diagnostics:Advanced monitoring systems enable remote diagnostics and maintenance, reducing downtime and energy waste during servicing.
- Lightweight Materials:The use of lightweight components, such as carbon fiber or advanced composites, reduces the overall weight of the crane, which in turn lowers the energy required for movement.
Benefits of using energy-efficient overhead cranes
Implementing energy-efficient overhead cranes in steel manufacturing plants offers a multitude of benefits:
- Energy Savings:The most obvious advantage is the significant reduction in energy consumption. This translates to lower utility bills and operational costs for the steel plant.
- Reduced Carbon Emissions:Energy-efficient cranes contribute to the steel industry's efforts to lower its carbon footprint. By using less energy, they minimize greenhouse gas emissions, aligning with sustainability goals and regulatory requirements.
- Enhanced Productivity:Energy-efficient cranes often come with improved control systems, which lead to smoother and more precise operations, reducing the risk of accidents and improving overall productivity.
- Long-Term Cost Savings:While energy-efficient cranes may have a higher initial investment, the long-term cost savings in energy and maintenance typically far outweigh the upfront costs.
- Competitive Advantage:As sustainability becomes a key consideration in steel production, adopting energy-efficient technology can give manufacturers a competitive edge in the market and open up new business opportunities.
Energy-efficient overhead cranes are not just a technological innovation; they are a strategic choice for steel producers looking to reduce costs, minimize environmental impact, and secure a sustainable future.
Cost Savings through Energy Efficiency
How energy-efficient overhead cranes contribute to cost reduction ?
Energy-efficient overhead cranes play a crucial role in cost reduction for steel manufacturing operations. Their contributions to cost savings are multifaceted:
- Reduced Energy Costs:Energy-efficient cranes consume less electricity or other power sources during their operations. This directly translates into lower energy bills, a substantial operational cost reduction.
- Maintenance Savings:These cranes are often designed with high-quality, durable components, reducing the frequency and cost of maintenance and repairs.
- Enhanced Productivity:Energy-efficient cranes are equipped with advanced control systems, allowing for precise and efficient movements. This leads to increased productivity and reduced labor costs.
- Regulatory Compliance:Some regions offer incentives or tax benefits for companies that invest in energy-efficient equipment, further contributing to cost savings.
Long-term economic benefits
The long-term economic benefits of using energy-efficient overhead cranes are substantial:
- Return on Investment (ROI):While the initial investment in energy-efficient cranes may be higher, the return on investment is relatively quick due to ongoing cost savings in energy, maintenance, and increased productivity.
- Sustainable Operations:Energy-efficient practices ensure the long-term sustainability of steel production, allowing companies to remain competitive and environmentally responsible.
- Risk Mitigation:By reducing energy costs, steel manufacturers are less vulnerable to fluctuations in energy prices, providing stability and predictability in their operations.
- Positive Public Image:Operating with energy-efficient overhead cranes aligns with the growing consumer demand for environmentally responsible products. This can enhance a company's public image and open up new markets.
In summary, the financial benefits of using energy-efficient overhead cranes in steel production are undeniable. These cranes not only reduce immediate operational costs but also position steel manufacturers for long-term economic success, making them a wise and strategic investment.
Environmental Impact Reduction
The environmental challenges of steel production
Steel production, while essential for modern society, poses significant environmental challenges. Some of the key environmental issues associated with steel manufacturing include:
- High Carbon Emissions:The steel industry is a major contributor to global carbon dioxide (CO2) emissions due to the combustion of fossil fuels, particularly in blast furnaces.
- Resource Depletion:Steel production requires vast amounts of natural resources, including iron ore, coal, and water, leading to resource depletion and environmental degradation.
- Waste Generation:Steel production generates substantial waste in the form of slag, emissions, and hazardous by-products, contributing to environmental pollution.
- Energy Intensity:The energy-intensive nature of steel manufacturing places a heavy demand on electricity and fossil fuels, further exacerbating environmental challenges.
How energy-efficient cranes contribute to environmental sustainability
Energy-efficient overhead cranes play a pivotal role in addressing the environmental challenges of steel production and promoting sustainability:
- Reduced Energy Consumption:By consuming less energy during operations, energy-efficient cranes directly contribute to a reduction in the environmental impact of steel manufacturing. Lower energy usage means fewer greenhouse gas emissions and decreased reliance on fossil fuels.
- Regenerative Braking:The regenerative braking systems in these cranes capture and reuse energy that would otherwise be wasted as heat, minimizing overall energy waste and reducing environmental harm.
- Efficient Operations:Energy-efficient cranes are designed to operate with precision and minimize wasteful movements, further reducing the carbon footprint of steel production.
- Resource Conservation:The use of energy-efficient technology and materials, such as lightweight components, helps reduce resource consumption, contributing to resource conservation and environmental sustainability.
Reduction in carbon emissions and resource conservation
The adoption of energy-efficient overhead cranes leads to tangible reductions in carbon emissions and resource conservation:
- Carbon Emission Reduction:A significant portion of a steel plant's carbon emissions comes from the energy-intensive processes that overhead cranes are a part of. Energy-efficient cranes can help reduce these emissions by decreasing energy consumption, which is critical for meeting global climate goals.
- Resource Conservation:Lightweight materials, more efficient operations, and energy recovery systems reduce the demand for natural resources. This not only conserves resources but also minimizes the environmental damage associated with resource extraction.
- Air Quality Improvement:Lower energy consumption and more efficient operations result in reduced air pollution, benefiting the local environment and the health of surrounding communities.
- Compliance with Regulations:Energy-efficient practices align with increasingly stringent environmental regulations and demonstrate a commitment to responsible manufacturing, reducing the risk of fines and legal issues.
In summary, the use of energy-efficient overhead cranes is a significant step toward mitigating the environmental challenges posed by steel production. By reducing energy consumption, minimizing carbon emissions, and conserving resources, these cranes contribute to a more sustainable and environmentally responsible steel manufacturing industry.
Challenges and Considerations
Potential challenges in adopting energy-efficient overhead cranes
The adoption of energy-efficient overhead cranes in steel manufacturing comes with several potential challenges:
- Initial Investment:Energy-efficient overhead cranes often require a higher upfront investment than traditional models, which can be a barrier for some companies, particularly smaller ones.
- Operational Disruption:The installation and integration of new cranes can lead to operational disruptions, impacting production schedules and requiring downtime for installation.
- Training and Adaptation:Operators and maintenance personnel may need training to operate and maintain energy-efficient cranes effectively. Adaptation to new technology can be challenging.
- Limited Compatibility:Some existing steel manufacturing facilities may not be designed to accommodate the electrical and mechanical requirements of energy-efficient cranes, making retrofitting more complex.
- Regulatory Compliance:Meeting energy efficiency standards and environmental regulations can pose challenges, especially in regions with strict compliance requirements.
Maintenance and operational considerations
Effective maintenance and operation of energy-efficient overhead cranes are essential for long-term success:
- Regular Maintenance:Energy-efficient cranes should undergo regular maintenance to ensure that energy-saving features like regenerative braking and VSDs continue to function optimally.
- Operator Training:Operators must be well-trained in the use of energy-efficient cranes to maximize their efficiency and safety.
- Monitoring and Data Analysis:Real-time monitoring and data analysis tools are crucial for identifying and addressing any performance issues promptly.
- Safety Protocols:Maintaining safety protocols is of utmost importance when operating energy-efficient cranes, as they often involve advanced features and technology.
- Spare Parts and Support:Ensuring the availability of spare parts and a reliable support network is vital to prevent operational downtime.
Return on investment and payback period
The return on investment (ROI) and payback period for energy-efficient overhead cranes depend on various factors, including the scale of implementation, energy cost savings, and maintenance expenses:
- Energy Cost Savings:The primary driver of ROI is the reduction in energy consumption, which directly impacts the payback period. The higher the energy costs and the more significant the reduction, the faster the payback period.
- Maintenance Costs:Lower maintenance costs due to energy-efficient crane features can accelerate the payback period and increase the long-term ROI.
- Scale of Implementation:Implementing energy-efficient cranes across an entire steel manufacturing facility can lead to quicker ROI compared to a partial implementation.
- Incentives and Rebates:Government incentives, tax rebates, or utility company programs can significantly impact the financial feasibility and shorten the payback period.
- Long-Term Benefits:While the upfront investment may be higher, the long-term economic benefits in energy savings, reduced maintenance, and increased productivity typically result in a positive ROI over the crane's lifecycle.
It's important for steel manufacturers to conduct a thorough financial analysis, considering these factors, to determine the specific ROI and payback period for their investment in energy-efficient overhead cranes. In many cases, the long-term economic and environmental advantages justify the initial costs.
Wrap it up,
Energy-efficient overhead cranes have emerged as pivotal tools in revolutionizing steel production. Their significance lies in their ability to address the energy consumption, cost savings, and environmental impact challenges that have long plagued the steel manufacturing industry. These cranes offer advanced features and technologies that reduce energy usage, contribute to sustainability, and enhance the overall efficiency of steel manufacturing operations.
The implementation of energy-efficient overhead cranes leads to substantial cost savings and a significant reduction in the environmental impact of steel production. By consuming less energy, recovering energy through regenerative braking, and optimizing operations, these cranes directly translate into lower energy bills, reduced maintenance costs, and minimized carbon emissions. The long-term economic benefits are evident, with a positive return on investment driven by energy savings, enhanced productivity, and reduced environmental compliance risks.
Energy-efficient overhead cranes are set to play a pivotal role in shaping the future of steel production. As the steel industry faces increasing pressure to reduce its carbon footprint, conserve resources, and embrace sustainability, these cranes offer a tangible solution. Their advanced technologies and features will continue to drive the steel manufacturing sector toward a more environmentally responsible and cost-effective future. Moreover, they position steel manufacturers for long-term success, competitive advantage, and compliance with evolving regulatory standards.
In conclusion, the adoption of energy-efficient overhead cranes is not merely a technological innovation; it is a strategic choice that benefits the industry, the environment, and the bottom line. As the steel production landscape evolves, these cranes will remain at the forefront of progress, demonstrating that sustainability and profitability can go hand in hand.