Integrating Hook Tracking with Crane Maintenance for Safety
Crane Maintenance in Steel Mills
Crane maintenance is essential in steel mills for ensuring continuous, safe, and efficient operations. Cranes are heavily relied upon to move large and heavy materials such as billets, coils, and slabs. Since these cranes are constantly in use, regular maintenance is crucial to prevent breakdowns and avoid costly delays. Keeping cranes in optimal working condition also reduces the risk of accidents and downtime.
- Cranes face extreme operational conditions.
- Regular maintenance helps to minimize wear and tear.
- Prevents unexpected breakdowns and keeps production running smoothly.
The Importance of Safety in Lifting Operations
Safety is a major concern during crane operations, especially in a steel mill where heavy lifting is a daily task. A crane failure during a critical lift can result in serious accidents, damage to materials, and harm to workers. It's essential that steel mills have systems in place to prevent such failures. The stakes are high, and safety protocols must be strictly followed to protect both personnel and equipment.
- Lifting operations pose high risks.
- Failures can lead to accidents, injuries, or damage.
- Safety is a top priority to ensure smooth and risk-free operations.
Why Integrate Hook Tracking Systems with Crane Maintenance Systems?
Integrating hook tracking systems with crane maintenance platforms provides a way to enhance both safety and efficiency. Hook tracking systems monitor the performance and condition of key crane components, particularly the hook and related parts. By linking this data with a preventive maintenance system, mills can detect wear and tear early, allowing for timely repairs before a failure occurs. This integration ensures cranes are properly maintained and can continue functioning safely without unexpected interruptions.
- Hook tracking provides real-time data on crane performance.
- Maintenance systems use this data to predict and prevent failures.
- Proactive maintenance reduces the chances of sudden breakdowns and safety risks.
By connecting hook tracking systems with maintenance platforms, steel mills can improve operational safety, reduce downtime, and extend the lifespan of critical equipment. This integration is a powerful tool in creating a safer and more reliable work environment.
Overhead Hook Tracking Systems
Definition and Function of Hook Tracking Systems
Hook tracking systems are technologies used to monitor and track the condition and movement of crane hooks in real-time. These systems provide valuable data about the crane's operational status, including the load being lifted, the hook's position, and any signs of wear. By integrating these systems into the crane's operation, operators can make informed decisions on maintenance and safety, reducing the likelihood of failures during critical lifts.
- Monitor the movement and position of crane hooks.
- Track load and wear patterns in real-time.
- Enhance operational efficiency and safety by providing crucial data.
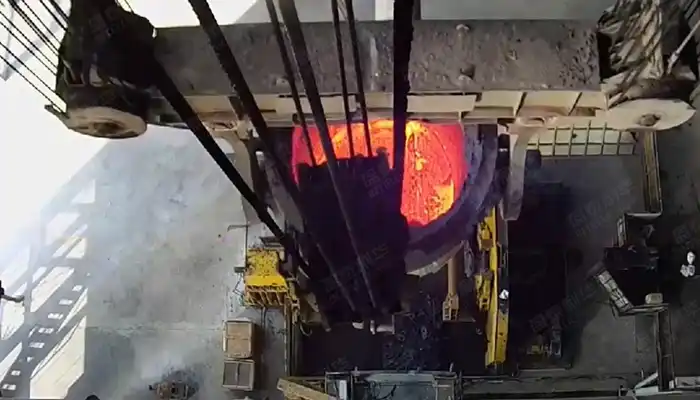
ladle overhead crane hook tracking system
Types of Hook Tracking Technologies
Several technologies are used in hook tracking systems, each offering distinct advantages depending on the application:
- RFID (Radio Frequency Identification): RFID tags are attached to the hook or crane components. These tags transmit data to a reader, allowing operators to track the location and operational status of the hook.
- GPS (Global Positioning System): GPS-based systems provide precise location data, tracking the hook’s position during lifts, especially in large steel mills with expansive layouts.
- Sensors: Different types of sensors, such as strain and load sensors, are installed on hooks to monitor stress, wear, and load capacity in real time. These sensors provide detailed insights into hook performance and help predict when maintenance is needed.
Each technology helps gather essential data that can be used to optimize crane operations and prevent potential issues.
How Hook Tracking Systems Improve Crane Operation Visibility and Control
Hook tracking systems provide improved visibility and control over crane operations by offering detailed, real-time data. Operators can monitor the hook's load, location, and condition, which enhances decision-making during lifting operations. This helps in:
- Ensuring that hooks are not overloaded or subjected to unnecessary stress.
- Preventing operational errors caused by poor visibility or human oversight.
- Reducing risks by allowing for immediate intervention if problems are detected.
With this data, operators can better plan maintenance schedules and adjust crane operations, leading to smoother, safer, and more efficient operations.
The Role of Preventive Maintenance in Steel Mill Crane Operations
Explanation of Preventive Maintenance and Its Significance
Preventive maintenance (PM) involves regularly scheduled inspections and servicing of equipment to identify and address issues before they lead to failures. In steel mills, cranes are critical assets that handle heavy loads under demanding conditions. Implementing a preventive maintenance strategy ensures that cranes remain operational, safe, and reliable. It’s far more cost-effective to address wear and tear early than to deal with unexpected breakdowns that can halt production and pose safety risks.
- Involves regular checks and servicing of crane components.
- Aims to detect potential problems before they cause major failures.
- Helps extend the lifespan of equipment and reduce unexpected downtime.
Common Wear and Tear Issues in Cranes
Cranes, particularly those in steel mills, undergo intense physical stress, which leads to wear and tear over time. Common issues include:
- Hooks: Over time, hooks can develop cracks, bends, or signs of fatigue, making them less reliable for heavy lifting.
- Ropes: Worn or frayed ropes can lose their strength, which compromises safety when lifting heavy materials.
- Motors and Drive Systems: The motors that drive the crane may experience wear, leading to reduced lifting capacity or even mechanical failure.
- Brakes and Bearings: Worn brakes or bearings can cause operational delays or unsafe conditions during lifts.
Regular inspection of these parts through preventive maintenance helps avoid catastrophic failures by detecting early signs of wear.
How Preventive Maintenance Platforms Monitor and Predict Equipment Failure
Preventive maintenance platforms are designed to integrate data from various sensors and tracking systems (such as hook tracking) to monitor the health of crane components. These platforms analyze the data to predict when certain parts need attention or replacement. For example:
- Sensor data from hook tracking systems can indicate when a hook is under excessive stress, alerting operators before it becomes a safety hazard.
- Usage patterns and wear metrics can help predict when ropes or motors will need servicing, avoiding unexpected failures.
- Automated alerts can notify operators of upcoming maintenance tasks, reducing human error and improving operational efficiency.
By using these platforms, steel mills can proactively address potential issues, ensuring cranes operate safely and efficiently, and reducing the risk of downtime.
Integration of Hook Tracking with Preventive Maintenance Systems
Benefits of Real-Time Data Collection Through Hook Tracking Systems
Real-time data collection through hook tracking systems offers numerous advantages for crane operations. By continuously monitoring the hook's condition and performance, operators can:
- Receive up-to-the-minute insights into the hook’s load, position, and stress levels.
- Detect unusual wear patterns, helping to predict potential failures before they occur.
- Optimize crane usage by ensuring components are functioning within their safe operational limits.
This immediate access to data ensures more informed decision-making and can significantly improve maintenance scheduling and operational efficiency.
How Hook Tracking Data Can Be Integrated into Maintenance Platforms
Integrating hook tracking data with maintenance platforms allows steel mills to streamline their maintenance processes. The data from the tracking system is fed directly into the maintenance software, which can then analyze this information to predict wear and plan maintenance activities.
- Data from hook sensors (load, position, stress) is automatically uploaded to the maintenance platform.
- Maintenance systems process the data to identify when components are reaching critical wear thresholds.
- The system generates alerts and schedules preventive maintenance before failures occur.
This integration eliminates manual tracking and ensures that maintenance tasks are based on real, actionable data, making maintenance more efficient and timely.
Seamless Communication Between Tracking Systems and Maintenance Software
For effective integration, communication between hook tracking systems and maintenance software must be seamless. This ensures that the data flows smoothly from one system to the other, enabling real-time insights and quick decision-making. The key to seamless communication includes:
- Automated Data Transfers: Data from hook tracking systems is automatically sent to the maintenance platform without manual intervention.
- Real-time Updates: Both the tracking system and maintenance software are updated in real-time, allowing for instant response to any issues.
- Centralized Dashboard: Operators and maintenance teams can view all relevant information on a single platform, improving coordination and response time.
This level of integration improves operational transparency and ensures that both operators and maintenance teams are on the same page, enhancing overall efficiency.
Improving Safety Through Hook Tracking Integration
Early Detection of Wear and Tear on Hooks and Related Components
Integrating hook tracking systems with preventive maintenance helps detect early signs of wear and tear on critical crane components like hooks, ropes, and bearings. The tracking system continuously monitors the hook’s load, stress, and condition, providing early warnings about potential issues. By detecting these issues early, maintenance can be scheduled before a failure occurs, significantly reducing the risk of accidents.
- Monitoring helps detect cracks, bends, or signs of fatigue in hooks.
- Early detection allows for timely repairs, reducing the risk of failure.
- Preventive maintenance can be planned to address worn-out components before they cause accidents.
Predictive Maintenance and Its Role in Reducing Sudden Failures
Predictive maintenance is an essential aspect of improving crane safety. Using data from hook tracking systems, maintenance platforms can predict when a component is likely to fail, allowing for proactive repairs. Predictive maintenance helps to avoid sudden breakdowns that could occur during critical lifting operations, minimizing disruptions and safety risks.
- Predictive maintenance uses real-time data to forecast potential failures.
- Allows maintenance teams to act before components fail unexpectedly.
- Prevents sudden equipment breakdowns during high-risk operations.
By integrating predictive maintenance with hook tracking systems, mills can reduce the likelihood of catastrophic failures, making lifting operations safer.
Enhancing Worker Safety by Preventing Malfunction During Critical Lifting Operations
The ultimate goal of integrating hook tracking systems with maintenance platforms is to improve worker safety. Crane malfunctions, especially during critical lifts, pose significant risks to both operators and nearby workers. Real-time data from hook tracking systems helps to ensure that all crane components are functioning properly, preventing dangerous malfunctions.
- Continuous monitoring helps ensure that crane hooks are not overloaded or in poor condition.
- Reduces the likelihood of accidents caused by equipment failure during high-stakes lifts.
- Enhances overall safety by enabling timely maintenance and reducing unplanned downtime.
By using hook tracking to predict and prevent failures, steel mills can ensure that workers are not exposed to unnecessary risks, creating a safer working environment.
Case Studies and Industry Examples
Real-Life Examples of Steel Mills Implementing Integrated Systems
Several steel mills around the world have successfully implemented hook tracking systems integrated with their preventive maintenance platforms. For example:
- Steel Mill A (Europe): A leading steel mill in Europe integrated RFID-based hook tracking with its maintenance system. The system provided real-time monitoring of hook performance, allowing the mill to schedule maintenance based on actual wear data. This approach significantly reduced unexpected downtime and improved the crane’s operational efficiency.
- Steel Mill B (Asia): In an Asian steel mill, a GPS-based hook tracking system was installed on overhead cranes to monitor their location and load during lifts. The integration with the maintenance system helped the mill predict wear on hooks and ropes, leading to proactive repairs. The result was a noticeable reduction in crane failures and an increase in worker safety.
Results Observed in Terms of Equipment Lifespan, Safety, and Reduced Downtime
The integration of hook tracking systems with maintenance platforms has led to several positive outcomes for these mills:
- Extended Equipment Lifespan: Regular monitoring of crane components helped identify issues before they became critical, extending the lifespan of hooks, ropes, and motors.
- Improved Safety: Early detection of wear on crane components reduced the risk of accidents and injuries. Operators were better informed, and maintenance teams could act before issues led to malfunctions during critical lifts.
- Reduced Downtime: By predicting maintenance needs and scheduling repairs in advance, mills experienced fewer unexpected breakdowns, leading to more consistent and efficient operations. Unplanned downtime was reduced by up to 30%.
Lessons Learned from These Implementations
From these implementations, steel mills learned several key lessons:
- Data Accuracy is Crucial: The effectiveness of hook tracking systems depends on accurate and consistent data. Calibration and regular testing of the sensors are vital to ensure the system’s reliability.
- Staff Training: Proper training for operators and maintenance teams is essential to make the most of the integrated system. Without understanding how to interpret and act on the data, the system’s potential can be limited.
- Integration with Existing Systems: Seamless integration with existing crane management and maintenance software is crucial for success. Any gaps in communication between the tracking system and maintenance platform can reduce the effectiveness of the integration.
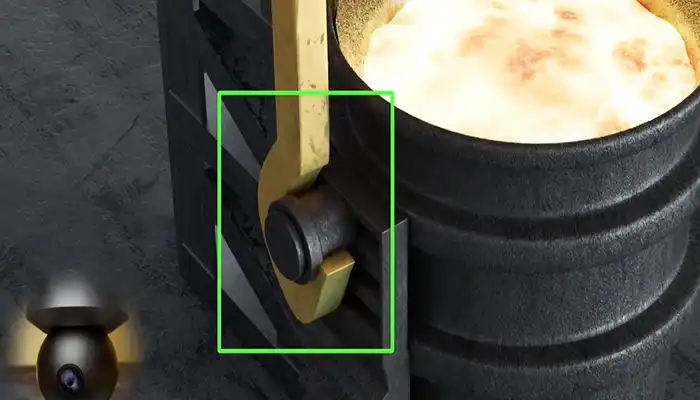
Challenges and Considerations in Integration
Technical and Logistical Challenges in Integrating Hook Tracking with Maintenance Systems
While integrating hook tracking with maintenance systems offers significant benefits, there are several technical and logistical challenges to consider:
- Compatibility Issues: Different systems and technologies used in hook tracking and maintenance platforms may not always be compatible, leading to integration difficulties.
- Installation Complexity: Installing sensors and tracking equipment on existing cranes can be complex, especially in older mills with outdated infrastructure. Retrofitting may require significant time and resources.
- Data Management: Managing the large volume of data generated by real-time tracking systems can be overwhelming without the right software or infrastructure. Proper data storage, processing, and analysis capabilities are essential.
Costs and ROI Considerations for Steel Mills
The upfront costs of installing hook tracking systems and integrating them with maintenance platforms can be significant. However, the return on investment (ROI) can be substantial in the long run. Considerations include:
- Initial Investment: The cost of installing sensors, software, and integration tools can be high. This may include purchasing new equipment, training staff, and setting up maintenance systems.
- Operational Savings: By reducing unplanned downtime and extending equipment lifespan, the overall cost of maintenance is reduced. Mills can also minimize the need for emergency repairs, which are often more expensive.
- ROI Over Time: Over time, the savings from increased operational efficiency, reduced downtime, and improved safety can offset the initial investment, providing a strong ROI.
Data Security and Privacy Concerns with Real-Time Tracking and Monitoring
As with any real-time tracking system, data security and privacy concerns are critical when integrating hook tracking with maintenance systems. The continuous transmission of operational data increases the risk of cyber threats. Steel mills must ensure:
- Data Protection: Sensitive operational data should be encrypted and stored securely to prevent unauthorized access or cyberattacks.
- Access Control: Only authorized personnel should have access to the system’s data. This requires proper user authentication and role-based access controls.
- Compliance with Regulations: Steel mills must ensure that their tracking systems comply with industry standards and regulations, particularly those related to data privacy and security.
Addressing these concerns through robust security measures and ongoing monitoring can help protect the integrity of the system and the data it generates.
Future Trends in Hook Tracking and Crane Maintenance Integration
Emerging Technologies in Crane Maintenance and Hook Tracking
The integration of emerging technologies in crane maintenance and hook tracking systems is poised to revolutionize steel mill operations. Key advancements include:
- Artificial Intelligence (AI): AI is being used to analyze large volumes of data collected by hook tracking systems. AI algorithms can predict component failures with greater accuracy and optimize maintenance schedules in real time. AI also enables cranes to learn from past behavior, improving operational efficiency and safety.
- Internet of Things (IoT): IoT technology allows various crane components to be connected, enabling real-time communication between the crane, maintenance platforms, and operators. IoT sensors can provide data on hook wear, load limits, and crane performance, which helps in the predictive maintenance process.
These technologies are advancing the capabilities of hook tracking systems and allowing for better data analysis, predictive insights, and operational decision-making.
Potential for Automation and Autonomous Cranes in the Future
Automation is another trend shaping the future of crane operations. Autonomous cranes, driven by AI and IoT, could become commonplace in steel mills. These cranes would be capable of performing lifting operations without direct human control, relying on real-time data and predictive maintenance to operate safely and efficiently.
- Autonomous Lifting: Future cranes may use AI to independently perform complex lifting tasks, adjusting their behavior based on real-time environmental and load data.
- Self-Maintenance: In the future, cranes could perform basic maintenance tasks autonomously, such as lubricating moving parts or adjusting load limits, without the need for human intervention.
This shift towards automation could further improve operational efficiency, safety, and cost savings.
Ongoing Innovations Aimed at Improving Safety and Reducing Maintenance Costs
Continual innovations are being made to enhance crane safety and reduce maintenance costs. These include:
- Advanced Sensors and Monitoring Systems: New sensors capable of detecting even more subtle signs of wear and fatigue, such as microscopic cracks or temperature variations, are being developed to improve early detection of issues.
- Smart Predictive Analytics: More advanced algorithms are being created to predict failures more accurately, allowing for more precise maintenance schedules and reducing unnecessary maintenance costs.
- Wearable Safety Technology: Operators could wear smart devices that monitor their health and safety in real-time, providing alerts if they’re in proximity to a malfunctioning crane.
These innovations focus on improving safety standards and reducing the cost of maintenance by ensuring timely repairs and enhancing crane reliability.
Conclusion
The integration of hook tracking systems with preventive maintenance platforms offers significant advantages for steel mills. By continuously monitoring crane components in real time, mills can reduce unexpected breakdowns, extend the lifespan of equipment, and enhance worker safety. This proactive approach to maintenance ensures smoother, more efficient operations, minimizing downtime and preventing costly repairs.
This integration represents a major step forward in ensuring that steel mill cranes operate safely and efficiently. The ability to monitor and predict wear and tear on crane components provides operators with the tools needed to maintain equipment in optimal condition. As a result, safety improves, downtime decreases, and overall productivity increases. With fewer unplanned failures, mills can maintain a steady production flow and reduce operational costs.
Steel mills are encouraged to embrace the integration of hook tracking systems with preventive maintenance platforms. By doing so, they can significantly enhance safety, reduce maintenance costs, and improve overall productivity. The future of crane operations in steel mills lies in adopting these technologies to create safer, more efficient, and more sustainable workplaces. Don’t wait for a failure to occur – act now and invest in the future of crane maintenance!