Reduce Steel Mill Crane Risks with Advanced Hook Tracking System
Advanced hook tracking technology in steel mills reduces crane risks by providing real-time monitoring, overload prevention, and improved safety.
Overview of Crane Risks in Steel Mills
Steel mills are high-risk environments. Steel Mill Cranes carry heavy loads of molten metal, which require great precision and care. The risks are significant, as even small errors can lead to accidents or equipment failure.
Common risks include:
- Overload Conditions: Lifting beyond the crane’s capacity can damage the equipment and cause accidents.
- Hook Detachment: If the hook detaches from the load, it can cause the load to fall, creating a serious safety hazard.
- Misalignment: Mispositioned hooks or loads can lead to dangerous situations, especially when handling molten metal.
These risks demand reliable systems that can monitor and control crane operations effectively.
The Role of Advanced Hook Tracking Technology
AI-powered hook tracking systems are designed to address these risks. These systems use advanced technology to monitor the crane’s hook and load in real time. By providing constant feedback, these systems help operators make quick, informed decisions.
- Real-Time Feedback: The system tracks the hook's position and load weight, alerting operators immediately if there is a problem.
- Precise Control: AI algorithms ensure the hook stays securely in place and within safe operating limits, reducing the chances of overload or detachment.
In short, these systems play a critical role in preventing accidents and improving safety in steel mills.
Steel Mill Crane Risks
Operational Risks in Steel Mills
Steel mills are complex, high-risk environments where cranes are used to lift heavy loads of molten metal. Several operational risks can occur:
- Overload Conditions: When the crane is tasked with lifting loads beyond its capacity, it can lead to equipment failure, structural damage, or even catastrophic accidents.
- Hook Detachment: If the hook becomes detached from the load, the molten metal or heavy materials could fall, causing damage to both people and equipment.
- Mispositioning of Loads: When the crane’s load is misaligned, it can create unstable conditions that increase the likelihood of accidents. This is especially dangerous when dealing with molten metal or heavy materials.
- Environmental Factors: Harsh conditions like high heat, smoke, or poor visibility can make it difficult for operators to monitor the crane's operation effectively. These factors increase the chances of human error.
Impact of These Risks
The consequences of these operational risks are serious:
- Potential Accidents and Injuries: A mispositioned load, overload, or detached hook can lead to accidents, resulting in severe injuries or fatalities for workers in the mill.
- Equipment Damage: Overloading or improper hook attachment can damage cranes, ladles, or other machinery, leading to costly repairs or replacements.
- Increased Downtime and Maintenance Costs: Cranes that experience overload conditions or other failures often need downtime for repairs. This results in lost production time and higher maintenance costs, affecting overall efficiency and profitability.
These risks underscore the importance of advanced safety systems to minimize accidents and maintain smooth operations.
How AI-Powered Hook Tracking Systems Work
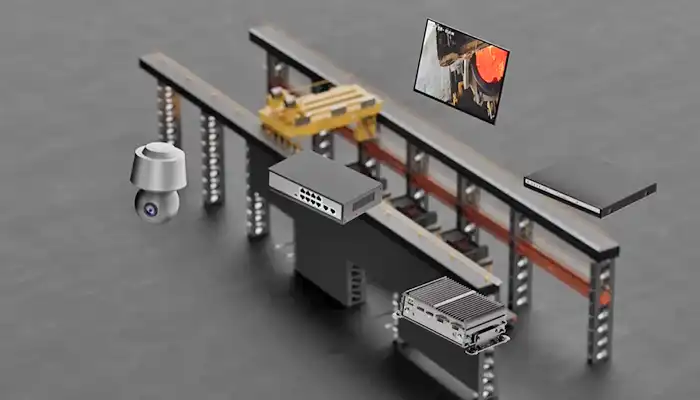
Key Components of the Technology
AI-powered hook tracking systems rely on a combination of cutting-edge technology to monitor crane operations with precision. The key components of this system include:
- AI Algorithms for Real-Time Tracking: AI algorithms are at the heart of the hook tracking system. They continuously monitor the crane’s hook movement and position in real-time. These algorithms process data from cameras and sensors to determine the exact location of the hook, ensuring it stays within safe operating parameters. This level of precision helps prevent issues like mispositioned loads or hook detachment.
- Integration with Crane Systems: The AI system is seamlessly integrated with the crane’s operational controls, allowing it to monitor not just the hook position but also the load weight and stability. This integration ensures that the crane can be automatically adjusted or alerted if the load exceeds safe limits or if the crane is at risk of overloading.
- Use of Cameras and Sensors: Multiple cameras and sensors are installed on the crane to provide a comprehensive view of the hook and load. These sensors track both the physical position of the hook and the load's behavior, while cameras provide visual confirmation. This allows for continuous monitoring of the crane's movements, even in difficult environmental conditions, such as poor visibility or high heat.
Real-Time Data and Feedback
AI-powered hook tracking systems provide valuable, real-time data that helps operators make timely decisions to prevent accidents:
- Continuous Updates on Hook Position and Load Status: The system provides operators with live updates on the position of the hook and load, giving them an accurate representation of the crane’s current status. This continuous flow of information helps operators make quick adjustments or corrections, ensuring that the load remains stable and within the crane's safe operating range.
- AI Algorithms for Early Issue Detection: The system is designed to detect early signs of potential problems. For example, AI algorithms can identify situations where the load is becoming unbalanced or where the hook is in danger of detaching from the load. If the system detects any abnormalities—such as the crane approaching its weight limit or the load shifting—the AI will alert the operator immediately. This early warning allows operators to take corrective actions before a more serious problem occurs, helping to prevent accidents and maintain safe operations.
By providing constant feedback, the AI-powered system ensures that crane operators have the information they need to avoid common risks, such as overloads, hook detachment, or misalignment, all in real time.
Reducing Operational Risks
Overload Prevention
AI-powered hook tracking systems are specifically designed to prevent overload conditions, which are one of the most critical risks in crane operations. Here’s how the system works to safeguard against overloading:
- Real-Time Load Assessment: The system constantly monitors the weight of the load being lifted. AI algorithms analyze this data in real time to ensure that the crane is not lifting beyond its safe weight limit. By integrating with the crane's lifting system, the AI can cross-check the load’s weight with the crane’s rated capacity.
- Alerts and Warnings: If the system detects that the weight of the load exceeds the crane's safe capacity, it triggers an immediate alert. These warnings are sent to the operator, allowing them to take corrective action before the crane is pushed beyond its limits. In some cases, the system may even automatically stop the crane from lifting the load if the weight exceeds predefined safety thresholds.
This proactive approach to overload prevention ensures that cranes operate within safe limits, reducing the likelihood of damage to equipment and preventing dangerous accidents.
Preventing Hook Detachment and Misalignment
Ensuring the hook is properly attached and aligned with the load is essential for safe crane operation. AI-powered hook tracking systems continuously monitor the hook and load to prevent detachment and misalignment:
- Continuous Monitoring of Hook Position: The system uses cameras and sensors to track the hook’s position throughout the lifting process. This continuous monitoring checks the hook’s alignment with the load, ensuring it stays securely attached. AI algorithms analyze the data to detect any potential issues with hook positioning, such as shifting or detachment.
- Real-Time Alerts for Compromised Hook Attachment: If the system detects that the hook is not securely attached to the load or if the attachment is in danger of coming loose, it triggers a real-time alert. This provides immediate feedback to the operator, prompting them to take corrective actions such as stopping the crane or re-positioning the hook.
- Visual Feedback for Operators: The system provides on-screen visual cues to confirm hook attachment status. These visual indicators give the operator clear and immediate confirmation of whether the hook is properly attached or if adjustments are needed. This added layer of feedback helps operators make quicker and more accurate decisions, minimizing the risk of accidents caused by hook detachment or misalignment.
By constantly monitoring hook position and providing real-time feedback, the AI-powered system ensures that hooks remain securely attached, preventing detachment and reducing the risk of load instability.
Real-Time Feedback for Quick Corrective Action
Instant Alerts and Notifications
AI-powered hook tracking systems provide operators with real-time alerts, ensuring that they can take immediate action in case of any operational risks:
- Immediate Feedback on Critical Conditions: The system offers instant alerts when an overload condition, hook detachment, or instability is detected. These notifications are delivered directly to the operator, allowing them to take immediate corrective actions. The faster the response, the lower the chances of an accident or equipment failure.
- Notifications for Corrective Actions: If the system identifies a problem—such as the hook nearing detachment or the load approaching a safe weight limit—it sends notifications to the operator, prompting them to stop the crane or adjust its position. This ensures that any potential issues are addressed before they escalate into serious risks.
Visual Decision-Making Support
Real-time feedback isn’t just limited to alerts; AI systems also provide visual support to aid decision-making:
- On-Screen Visual Cues: The system provides visual indicators on the crane’s control screen, showing the current status of the hook and load. Operators can see if the hook is properly aligned, if the load is within safe weight limits, and whether the system detects any instability. This visual feedback gives operators the information they need to act quickly.
- Stability Assessments: AI algorithms assess the stability of the load in real time and display this data on the screen. Operators can instantly evaluate whether the load is secure or at risk of becoming unstable. Enhanced situational awareness allows operators to make quick, informed decisions to prevent accidents.
By providing real-time visual feedback, the system helps operators react faster and more accurately, reducing human error and enhancing safety.
Minimizing Downtime and Preventing Damage
One of the main benefits of real-time feedback is its ability to minimize downtime and reduce the risk of costly damage:
- Preventing Emergency Repairs: By detecting issues like overload conditions or hook misalignment early, the system allows for timely interventions before the crane or other equipment is damaged. This proactive approach helps avoid emergency repairs, which can be costly and time-consuming.
- Reducing Equipment Damage: Real-time alerts prevent cranes, ladles, and other critical equipment from being subjected to conditions that could lead to damage. By ensuring that loads stay within safe limits and that hooks remain securely attached, the system reduces the likelihood of equipment failure, ultimately prolonging the lifespan of the machinery.
In short, real-time feedback from AI-powered hook tracking systems not only improves safety but also helps maintain the overall efficiency and longevity of crane operations.
Benefits of Advanced Hook Tracking Technology
Improved Safety
The implementation of AI-powered hook tracking systems significantly enhances safety in steel mills:
- Reduction in Accidents and Injuries: By continuously monitoring the hook and load position, the system ensures that cranes operate within safe limits, reducing the likelihood of accidents such as load detachment or misalignment. The real-time alerts also help operators respond quickly to potential risks, preventing accidents before they happen. This leads to fewer injuries and safer working conditions for employees.
- Better Hook Control and Load Monitoring: The AI system tracks both the hook’s position and the load’s stability in real-time, providing operators with detailed insights into crane operations. With constant feedback, operators can ensure that the hook stays securely attached to the load, reducing the risk of mishaps involving hook detachment or instability.
Increased Efficiency
AI-powered hook tracking technology not only improves safety but also boosts overall efficiency in crane operations:
- Faster Operations: The system’s real-time monitoring and quick corrective actions allow for faster decision-making. Operators receive immediate alerts if something goes wrong, enabling them to act swiftly and keep operations running smoothly. This results in faster loading and unloading times, leading to more efficient use of crane resources.
- Better Coordination and Control: With the continuous flow of data, operators can make more informed decisions and coordinate operations more effectively. The system helps prevent miscommunications or mistakes by providing clear and actionable insights into the crane’s current status. This improved control leads to smoother operations across the steel mill.
Long-Term Cost Savings
Investing in advanced hook tracking technology provides significant long-term financial benefits:
- Reduced Maintenance and Repair Costs: By preventing overload conditions, hook detachment, and misalignment, the system helps avoid damage to cranes, ladles, and other equipment. This proactive approach reduces the need for expensive repairs and minimizes maintenance costs, allowing steel mills to allocate resources more effectively.
- Lower Insurance Premiums and Fewer Disruptions: The reduction in accidents and injuries directly impacts insurance premiums, as safer operations generally lead to lower risk assessments. Fewer accidents also mean less downtime for repairs, reducing the likelihood of operational disruptions that can affect production schedules and revenue.
By improving safety, increasing operational efficiency, and offering long-term cost savings, advanced hook tracking technology proves to be a valuable investment for steel mills aiming to optimize crane operations.
Conclusion
The Role of AI in Crane Safety
AI-powered hook tracking systems are transforming crane operations in steel mills by significantly improving safety. These systems provide real-time feedback on the hook and load position, reducing operational risks and enhancing crane precision.
- Real-Time Feedback and Alerts: Continuous monitoring and immediate alerts help operators address risks such as overloads, hook detachment, or misalignment before they escalate.
- Improved Safety and Control: These systems reduce human error, preventing accidents and minimizing downtime, leading to safer working environments.
By offering enhanced monitoring and control, AI systems ensure safer and more efficient crane operations, making them an indispensable tool in modern steel mills.
Looking Ahead: The Future of Steel Mill Operations
The future of steel mill operations will be increasingly shaped by automation and AI technology. As AI-powered systems become more advanced, their role in improving both safety and efficiency will grow.
- Greater Precision and Adaptability: As technology evolves, AI systems will provide even more precise control over crane movements, enabling operators to make quicker, more informed decisions.
- Enhanced Operational Efficiency: Automation and AI will streamline operations, reduce downtime, and boost productivity while maintaining high safety standards.
In the coming years, AI and automation will drive the steel industry toward safer, more efficient, and more sustainable operations, reducing human error and enhancing overall performance.