Comparative Analysis: Under Running vs. Top Running Bridge Cranes
Comparative Analysis of Under Running vs. Top Running Bridge Cranes
Bridge cranes, also known as overhead cranes, are essential pieces of equipment used for lifting and moving heavy loads across a predetermined area. These cranes consist of parallel runways with a traveling bridge spanning the gap. Attached to the bridge is a hoist, which lifts and transports the load.
The main purpose of bridge cranes is to facilitate the efficient handling of materials, reducing the need for manual labor and enhancing workplace safety. By enabling the easy movement of heavy items, bridge cranes play a crucial role in streamlining operations, minimizing handling time, and preventing potential damage to goods.
Types of Bridge Cranes
Bridge cranes come in two primary types: under running bridge cranes and top running bridge cranes. Each type has unique characteristics that make them suitable for different applications.
Under running bridge crane 1 ton 10 ton for sale
Under Running Bridge Cranes
Under running bridge cranes, also known as underhung cranes, are designed so that the bridge and hoist are suspended from the bottom flange of the runway beams. These runway beams are typically supported by the roof structure of the building, eliminating the need for additional floor-mounted columns.
- Key Features and Benefits: Space Efficiency: Under running bridge cranes are ideal for facilities with limited headroom because they maximize the available vertical space.
- Flexibility: These cranes can operate on multiple runways within the same building, providing greater flexibility in crane placement and operation.
- Cost-Effective Installation: The absence of floor-mounted support columns can reduce installation costs, making under running cranes a cost-effective solution for certain applications.
- Building Integration: They integrate well with existing building structures, which can be advantageous in older facilities where adding floor-mounted supports might be challenging.
- Typical Applications: Manufacturing Facilities: Especially in environments where space is at a premium and materials need to be moved across multiple workstations.
- Assembly Lines: Where precision and accessibility are crucial.
- Light to Medium Duty Operations: Best suited for operations that do not require extremely heavy lifting, making them perfect for small to medium-sized loads.
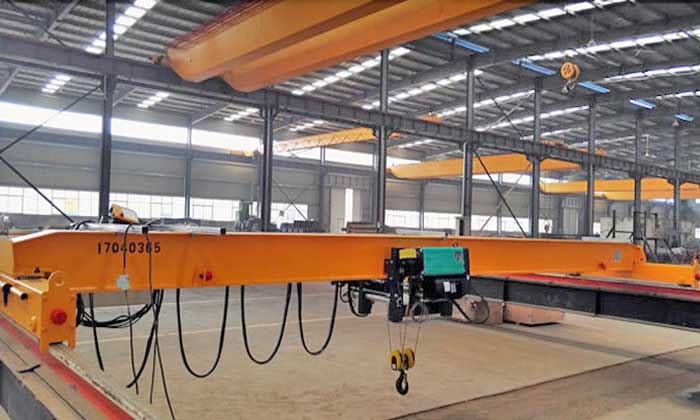
Top Running Bridge Cranes
Top running bridge cranes, on the other hand, are mounted on top of the runway beams. These beams are usually supported by columns or the building structure itself, allowing the crane to travel along the top of the beams.
- Key Features and Benefits: Higher Load Capacity: Top running cranes can handle significantly higher loads compared to under running cranes, making them suitable for heavy-duty applications.
- Greater Stability: The design provides better stability and reduces sway during operation, which is essential for precise load placement.
- Wide Span: They can cover larger spans, making them ideal for wide work areas or large industrial spaces.
- Versatility in Heavy Industries: These cranes are versatile and can be used in a variety of heavy industrial applications, from steel manufacturing to shipbuilding.
- Typical Applications: Heavy Manufacturing and Industrial Settings: Where large, heavy items need to be moved frequently and with precision.
- Large Warehouses and Storage Facilities: For handling bulky or heavy items over vast areas.
- Construction and Shipyards: Where the ability to lift and transport extremely heavy loads is critical.
Comparison Summary: Under Running Bridge Cranes are more suited for environments with space constraints and lighter load requirements. They are cost-effective and flexible, making them an excellent choice for small to medium-sized operations.
Top Running Bridge Cranes are designed for heavy-duty lifting and larger spans, providing greater stability and higher load capacity. They are ideal for large-scale industrial applications where heavy lifting is a regular requirement.
These differences helps in selecting the right type of bridge crane for specific operational needs, ensuring efficiency, safety, and cost-effectiveness.
Scope and Limitations
This analysis will cover several critical aspects of under running and top running bridge cranes but will also have some limitations to maintain focus and relevance.
- Scope: Technical Design and Specifications: Detailed examination of the structural and functional characteristics of each crane type.
- Advantages and Disadvantages: In-depth discussion on the benefits and drawbacks, providing a balanced view.
- Application Suitability: Analysis of various industry scenarios and operational environments where each crane type excels.
- Performance Metrics: Assessment of load capacity, span capabilities, stability, and operational efficiency.
- Cost Analysis: Overview of initial investment, installation costs, maintenance expenses, and overall cost-effectiveness.
- Limitations: Specific Brand Comparisons: The analysis will focus on the general types of cranes rather than specific brands or manufacturers.
- Niche Applications: While various industries will be considered, the analysis may not cover highly specialized applications that require unique crane configurations.
- Technological Innovations: Emerging technologies and advancements in crane design may not be fully addressed if they have not been widely adopted or standardized.
The scope ensures a thorough and practical comparison, while the limitations acknowledge the vast diversity within industrial applications and the continuous evolution of crane technology. This focused approach aims to provide actionable insights for selecting the right bridge crane type for common industrial needs.
Technical Specifications and Design

Under Running Bridge Cranes
Structural Design
Under running bridge cranes, also known as underhung cranes, are characterized by their unique structural design where the bridge and hoist are suspended from the bottom flange of the runway beams. This design allows the crane to operate below the runway, offering several advantages in terms of space utilization and flexibility. The key components of the structural design include:
- Bridge: The horizontal beam that spans the gap between the runway beams, supporting the hoist.
- Hoist: The lifting mechanism attached to the bridge, capable of moving along the bridge to lift and transport loads.
- End Trucks: Located at the ends of the bridge, these components allow the bridge to move along the runways.
- Runway Beams: The horizontal beams, usually attached to the building’s roof structure, that support the entire crane system.
This design makes under running bridge cranes particularly suitable for environments where floor space is limited or where maximum headroom is required.
Rail Placement and Support System
The rail placement and support system for under running bridge cranes are distinct and crucial for their functionality:
- Rail Placement: The rails are placed on the bottom flange of the runway beams, allowing the bridge to travel beneath the beams. This configuration minimizes the amount of vertical space the crane occupies.
- Support System: Under running cranes rely on the building’s existing roof or ceiling structure for support. The runway beams are typically mounted to the roof trusses or ceiling joists, eliminating the need for additional floor-mounted columns.
- Installation Considerations: The support system must be strong enough to bear the combined weight of the crane and the maximum load it will carry. This often requires careful structural analysis to ensure the building can handle these stresses.
Load Capacity and Span
Under running bridge cranes generally have a lower load capacity and span compared to top running cranes, which suits them well for specific applications:
- Load Capacity: These cranes are typically designed for light to medium duty applications, with load capacities ranging from a few hundred pounds to several tons. While they can handle significant weights, they are not intended for the heaviest industrial loads.
- Span: The span of under running cranes, which is the distance between the runway beams, is usually more limited than that of top running cranes. However, they can still cover substantial areas, making them effective for various manufacturing and assembly operations.
- Customization: Despite their lower load capacity, under running cranes can be customized to fit specific operational needs, including variations in span length and load handling capabilities.
Overall, the technical specifications and design of under running bridge cranes make them highly effective for industries where space efficiency and flexible integration into existing structures are paramount. They offer a practical solution for a range of light to medium duty material handling applications, providing a balance of functionality, efficiency, and cost-effectiveness.
Top Running Bridge Cranes
Structural Design
Top running bridge cranes are designed with the bridge mounted on top of the runway beams. This design allows the crane to operate above the runway beams, providing robust support and stability for heavy lifting tasks. Key components of the structural design include:
- Bridge: The main horizontal beam that spans the distance between the runway beams, supporting the hoist and allowing horizontal movement.
- Hoist: The lifting mechanism that moves along the bridge, capable of lifting and transporting heavy loads.
- End Trucks: Located at the ends of the bridge, these components facilitate the movement of the bridge along the runway beams.
- Runway Beams: Heavy-duty beams that support the entire crane system and are typically mounted on independent columns or integrated into the building structure.
The structural design of top running bridge cranes provides enhanced load capacity and stability, making them suitable for heavy-duty applications.
Rail Placement and Support System
The rail placement and support system for top running bridge cranes are designed to handle higher loads and provide greater stability:
- Rail Placement: The rails are placed on top of the runway beams, allowing the bridge to travel on the top surface. This configuration supports higher weight capacities and reduces sway during operation.
- Support System: Top running cranes often require robust support systems, which typically include floor-mounted columns or integration into the building’s structural framework. This ensures that the crane can handle the significant loads it is designed to lift.
- Installation Considerations: Installing top running cranes involves ensuring that the runway beams and support columns are securely anchored and capable of bearing the maximum load capacity. This may require additional structural reinforcements, especially in older buildings.
Load Capacity and Span
Top running bridge cranes are known for their high load capacity and ability to cover large spans, making them ideal for heavy industrial applications:
- Load Capacity: These cranes are designed for heavy-duty operations, with load capacities ranging from several tons to hundreds of tons. Their robust construction allows them to lift and transport extremely heavy loads safely and efficiently.
- Span: The span of top running cranes can be significantly larger than that of under running cranes, enabling them to cover wide work areas. This makes them suitable for large warehouses, manufacturing plants, and other extensive facilities.
- Customization: Top running cranes can be highly customized to meet specific operational needs, including varying span lengths, load capacities, and specialized lifting requirements. This flexibility ensures they can be adapted to a wide range of industrial applications.
Overall, the technical specifications and design of top running bridge cranes make them essential for industries requiring heavy lifting and extensive coverage. Their ability to handle large loads and provide stable, efficient operation over wide areas makes them a critical component in many industrial settings.
Advantages
Under Running Bridge Cranes
- Space Efficiency : Under running bridge cranes are designed to maximize vertical space, making them ideal for facilities with low headroom or space constraints. Since the crane operates below the runway beams and the hoist is suspended from the bottom flange, it occupies less vertical space compared to top running cranes. This allows for better utilization of the available space, enabling more efficient workflow and storage.
- Flexibility in Building Integration : One of the significant advantages of under running bridge cranes is their ability to integrate seamlessly into existing building structures. Because they rely on the roof or ceiling for support, they do not require additional floor-mounted columns. This makes them highly adaptable to various building layouts, especially in older or pre-existing structures where adding floor supports might be impractical or too costly. Additionally, under running cranes can operate on multiple runways within the same facility, enhancing operational flexibility.
- Cost-Effectiveness for Certain Applications : Under running bridge cranes can be more cost-effective in specific scenarios, particularly in light to medium-duty applications. The lack of floor-mounted supports and the simpler installation process can reduce initial setup costs. Moreover, their efficient use of space can lead to lower operational costs, as they allow for better utilization of the existing building footprint without requiring extensive modifications.
Top Running Bridge Cranes
- Higher Load Capacity : Top running bridge cranes are designed for heavy-duty applications, offering significantly higher load capacities compared to under running cranes. They can handle loads ranging from several tons to hundreds of tons, making them suitable for industries that require the lifting and transportation of extremely heavy materials. This high load capacity is achieved through their robust structural design and the use of heavy-duty runway beams and support columns.
- Greater Stability and Reduced Sway : The design of top running bridge cranes provides superior stability, especially when lifting heavy loads. Since the bridge travels on top of the runway beams, it benefits from a more stable and secure support system. This reduces sway and movement during operation, which is critical for precise load handling and placement. The greater stability also enhances safety, minimizing the risk of accidents and equipment damage.
- Better Suited for Larger Spans and Heavy-Duty Applications : Top running bridge cranes are ideal for applications that require wide spans and the handling of large, bulky items. Their ability to cover extensive work areas makes them perfect for large warehouses, manufacturing plants, and construction sites. They can span greater distances than under running cranes, providing comprehensive coverage of the work area. This makes them indispensable in industries such as steel manufacturing, shipbuilding, and heavy construction, where both high load capacity and large operational spans are essential.
In summary, both under running and top running bridge cranes offer distinct advantages that make them suitable for different applications. Under running cranes excel in space efficiency, flexibility, and cost-effectiveness for lighter applications, while top running cranes provide higher load capacity, greater stability, and suitability for large spans and heavy-duty tasks. Understanding these advantages helps in selecting the right crane type based on specific operational requirements.
Disadvantages
Under Running Bridge Cranes
- Limited Load Capacity : One of the primary disadvantages of under running bridge cranes is their limited load capacity. These cranes are generally designed for light to medium-duty applications, which means they can handle loads from a few hundred pounds up to several tons. However, they are not suitable for heavy-duty tasks requiring the lifting of extremely heavy loads. Industries needing high-capacity lifting solutions may find under running cranes insufficient for their requirements.
- Potential for More Wear on the Support Structure : Since under running bridge cranes rely on the building's roof or ceiling structure for support, there is a potential for increased wear and tear on these elements. Over time, the constant weight and movement of the crane can stress the roof trusses or ceiling joists, leading to maintenance issues or the need for structural reinforcement. This can result in additional costs and downtime for repairs, impacting the overall efficiency of the operation.
- Constraints in Certain Building Layouts : While under running bridge cranes are flexible in terms of integration, they can still face constraints in certain building layouts. For instance, buildings with insufficiently strong roof structures may not be able to support the crane's weight. Additionally, low ceilings can limit the crane's operational height, restricting the types of materials that can be handled and the overall lifting capacity. In such cases, the feasibility of installing an under running crane becomes questionable.
Top Running Bridge Cranes
- Higher Initial Cost : Top running bridge cranes typically involve higher initial costs compared to under running cranes. This is due to the need for heavy-duty components, such as robust runway beams, support columns, and advanced hoisting mechanisms. The structural enhancements required to support the crane's weight and load capacity also contribute to the higher costs. These initial expenses can be a significant consideration for businesses with limited capital.
- Requires Robust Building Structure :The installation of top running bridge cranes demands a robust building structure capable of supporting the crane system and the heavy loads it will handle. This often requires substantial structural modifications or reinforcements to ensure the building can bear the additional weight and stresses. Older buildings or those not initially designed for heavy-duty crane operations may require significant upgrades, adding to the overall installation cost and complexity.
- More Complex Installation and Maintenance : Top running bridge cranes involve more complex installation processes compared to under running cranes. The need for precise alignment of runway beams, secure anchoring of support columns, and integration with the building's structural framework increases the installation time and complexity. Additionally, maintenance can be more challenging and costly due to the crane's heavy-duty components and higher operational demands. Regular inspections and upkeep are essential to ensure safe and efficient operation, adding to the long-term maintenance burden.
In conclusion, while both under running and top running bridge cranes offer significant advantages, they also come with specific disadvantages that need to be carefully considered. Under running cranes are limited by their load capacity and potential structural wear, whereas top running cranes face higher initial costs, the need for robust structures, and complex installation and maintenance requirements. Understanding these drawbacks is crucial for making informed decisions about the most suitable crane type for a given application.
Suitable Applications
Under Running Bridge Cranes
- Manufacturing Facilities with Space Constraints : Under running bridge cranes are highly effective in manufacturing facilities where space is at a premium. Their design allows them to be integrated into existing building structures without the need for additional floor-mounted supports. This maximizes the available floor space for other uses, such as machinery, storage, and workflow pathways. These cranes are ideal for plants where every square foot of floor space is valuable and needs to be utilized efficiently.
- Light to Medium Duty Operations : These cranes are best suited for light to medium duty operations, which involve the handling of loads up to several tons. Industries such as electronics manufacturing, small parts assembly, and packaging can benefit from the efficiency and flexibility of under running bridge cranes. Their ability to handle a wide range of smaller loads makes them versatile tools for various production processes that do not require heavy lifting capabilities.
- Situations Requiring Flexibility in Crane Placement : Under running bridge cranes offer significant flexibility in terms of placement and operation. They can be easily integrated into various sections of a facility, and multiple cranes can operate on the same runway system. This is particularly useful in dynamic work environments where the production layout may need to change over time. Their ability to move across different areas without extensive structural modifications provides a versatile solution for adaptable and evolving industrial spaces.
Top Running Bridge Cranes
- Heavy Manufacturing and Industrial Settings : Top running bridge cranes are essential in heavy manufacturing and industrial settings where lifting extremely heavy loads is a routine requirement. Industries such as steel production, automotive manufacturing, and shipbuilding utilize these cranes to move massive components and assemblies. Their high load capacity and robust design make them indispensable for operations that demand the handling of large, heavy materials with precision and safety.
- Large Warehouses and Storage Facilities : In large warehouses and storage facilities, top running bridge cranes provide the ability to cover extensive areas efficiently. They can handle bulky items and heavy pallets, facilitating the smooth and organized movement of goods within the warehouse. The capability to span wide distances without intermediate supports makes these cranes ideal for large-scale storage environments where maximizing vertical and horizontal space is crucial for operational efficiency.
- Environments with High Load Requirements and Large Spans : Top running bridge cranes are designed to meet high load requirements and accommodate large spans, making them suitable for environments where both factors are critical. This includes facilities involved in heavy construction, power generation, and large-scale fabrication. Their ability to handle substantial loads and cover wide areas ensures that they can support complex and demanding industrial processes, providing the strength and stability needed for heavy-duty operations.
In summary, the suitable applications for under running and top running bridge cranes vary based on their design and capabilities. Under running cranes excel in environments with space constraints, light to medium duty operations, and situations requiring flexible crane placement. Top running cranes, on the other hand, are ideal for heavy manufacturing, large warehouses, and environments with high load requirements and large spans. Understanding these applications helps in selecting the right crane type to optimize operational efficiency and effectiveness in various industrial settings.
Case Studies
Under Running Bridge Crane Application :Automotive Manufacturing Assembly Line
In an automotive manufacturing plant, under running bridge cranes are commonly used to facilitate the assembly of vehicles on the production line. These cranes are installed above the assembly stations where workers assemble various components such as engines, transmissions, and chassis.
Benefits:
- Space Efficiency: The under running bridge cranes operate below the runway beams, maximizing vertical space. This allows for efficient use of the factory floor area, which is crucial in automotive assembly plants where space is optimized for production efficiency.
- Flexibility in Crane Placement: Automotive assembly lines often require frequent reconfiguration to accommodate changes in production models or workflows. Under running cranes provide flexibility in crane placement without disrupting the assembly line layout. They can easily move along the runways to different workstations as needed, supporting efficient assembly operations.
- Improved Ergonomics and Safety: By lifting and maneuvering heavy components such as engines and chassis, under running cranes reduce the physical strain on assembly line workers. This improves ergonomics and enhances workplace safety by minimizing the risk of injuries related to manual lifting.
- Cost-Effectiveness: For automotive manufacturers, under running bridge cranes offer a cost-effective solution compared to alternative lifting methods or heavier crane systems. The simplified installation process and integration into existing building structures help control initial investment costs, contributing to overall operational efficiency.
Top Running Bridge Crane Application:Steel Manufacturing Plant
Scenario: In a steel manufacturing plant, top running bridge cranes are essential for handling heavy steel coils, slabs, and finished products throughout the production process. These cranes are installed to cover large spans across the production area, including the storage yards and processing facilities.
Benefits:
-
High Load Capacity: Top running bridge cranes are capable of lifting and transporting extremely heavy loads, which is critical in steel manufacturing where materials such as steel coils can weigh several tons. The robust design and high load capacity of these cranes ensure efficient handling of heavy materials without compromising safety or operational efficiency.
- Greater Stability and Control: The design of top running cranes provides superior stability and control during lifting operations. This reduces sway and ensures precise positioning of steel materials during handling and processing, minimizing the risk of damage or accidents.
- Span Coverage: Steel manufacturing plants require cranes that can cover extensive areas, including large storage yards and processing facilities. Top running bridge cranes are designed to span wide distances without the need for intermediate supports, optimizing space utilization and enabling seamless movement of materials across the production site.
- Enhanced Productivity: By streamlining material handling processes, top running bridge cranes contribute to improved productivity in steel manufacturing plants. They facilitate efficient loading and unloading of materials, reduce downtime, and support continuous operations to meet production schedules and customer demands.
In conclusion, both under running and top running bridge cranes demonstrate their effectiveness in specific industrial applications. Under running cranes excel in environments requiring space efficiency, flexibility, and lighter load capacities, such as automotive assembly lines. Top running cranes are indispensable in heavy-duty industries like steel manufacturing, where high load capacities, stability, and extensive span coverage are essential for efficient operations. Understanding these case studies helps illustrate how each crane type contributes to operational efficiency and safety in their respective industries.
Comparative Analysis
Performance Metrics
Load Capacity
- Under Running Bridge Cranes: Load Capacity: Typically suitable for light to medium-duty applications, ranging from a few hundred pounds to several tons depending on the specific configuration. They are designed to handle smaller loads efficiently within their operational limits.
- Top Running Bridge Cranes: Load Capacity: Designed for heavy-duty applications, capable of lifting extremely heavy loads ranging from several tons to hundreds of tons. They excel in industries requiring robust lifting capabilities and high load capacities.
Comparison: Load Capacity
Top Running Bridge Cranes:
- High Load Capacities: Designed to handle heavy loads efficiently, typically ranging from several tons to over a hundred tons. Ideal for industries such as steel manufacturing, automotive, aerospace, and heavy machinery where lifting and moving substantial loads are common.
- Long Span Capabilities: Equipped with robust structural support systems that allow for longer spans between runways. Can cover expansive work areas and provide flexibility in material handling across large production floors or warehouse spaces.
- Versatility and Efficiency: Capable of lifting and transporting larger volumes of materials in a single operation, reducing handling times and improving overall operational efficiency. Suitable for applications requiring continuous and heavy-duty operations with minimal downtime.
Under Running Bridge Cranes:
- Moderate Load Capacities: Generally have lower load capacities compared to top running cranes due to structural limitations associated with their underhung design. Typically used for lighter loads and applications where heavy lifting requirements are less frequent or critical.
- Compact Design Benefits: Offer advantages in facilities with limited headroom or where ceiling heights are restrictive. Suitable for smaller workspaces or operations that prioritize precise maneuverability and handling of smaller loads.
Industry Preferences:
- Preference for Top Running Cranes: Industries with heavy material handling requirements, such as manufacturing plants, warehouses, and shipping terminals, often prefer top running bridge cranes. These cranes provide the necessary capacity to handle large and heavy loads efficiently, supporting high-throughput operations and maximizing productivity.
- Considerations for Under Running Cranes: While under running cranes have their advantages in specific applications, industries with extensive material handling needs typically opt for top running cranes due to their superior load capacities and operational capabilities.
Top running bridge cranes significantly outperform under running cranes in terms of load capacity, making them the preferred choice for industries where heavy material handling requirements are predominant. The decision between these crane types should consider specific operational needs, facility constraints, and long-term efficiency goals to ensure optimal performance and productivity in material handling operations.
Installation and Maintenance Costs
Under Running Bridge Cranes:
- Installation Costs: Generally lower compared to top running cranes due to simpler structural requirements and less complex installation processes. They often integrate into existing building structures, reducing the need for additional support columns.
- Maintenance Costs: Typically lower as well, primarily due to their simpler design and fewer components. Maintenance tasks are generally easier to perform and require less frequent inspections.
Top Running Bridge Cranes:
- Installation Costs: Higher initial investment due to the need for robust support structures, including heavy-duty runway beams and support columns. Installation may require significant structural modifications to the building.
- Maintenance Costs: Higher maintenance costs due to the complexity of the crane system, heavy-duty components, and the critical nature of ensuring structural integrity and operational safety.
Comparison:
Under Running Bridge Cranes:
- Lower Installation Costs: - Generally easier and quicker to install compared to top running bridge cranes due to their simpler structural requirements. - Require less robust structural support, which can lead to cost savings in terms of materials and construction.
- Simplified Installation Process: - Installation of under running cranes typically involves mounting the crane on existing roof beams or structural supports. - Requires fewer modifications to the building structure, resulting in reduced labor costs and shorter installation timelines.
- Cost-Effective for Limited Requirements: - Ideal for applications where heavy lifting capabilities are not essential or where lighter loads are handled. - Suitable for smaller facilities or operations with space constraints that do not justify the investment in a higher capacity crane.
Maintenance Cost Benefits:
- Easier Access for Maintenance: - Components of under running cranes, such as hoists and trolleys, are typically located underneath the crane runway. - Provides easier access for routine maintenance tasks, reducing labor costs associated with servicing and inspections.
- Reduced Downtime: - Simplified maintenance procedures and accessibility to components contribute to shorter downtime periods for repairs and upkeep. - Minimizes disruptions to operations and improves overall equipment reliability and availability.
Industry Applications:
- Suitability for Lighter Loads: - Under running cranes are well-suited for applications where heavy lifting capabilities are not critical, such as small machine shops, assembly lines with moderate load requirements, or storage facilities. - Provide cost-effective material handling solutions without compromising operational efficiency.
- Budget-Conscious Considerations: - Industries or businesses with budget constraints may find under running cranes more financially viable, particularly when heavy lifting capacities are not a primary requirement. - Offers a balance between cost-effectiveness and operational efficiency for applications with moderate material handling needs.
Under running bridge cranes offer advantages in both installation and maintenance costs, making them a cost-effective solution for applications where heavy lifting capabilities are not essential. Businesses looking to optimize upfront investment and ongoing maintenance expenses while maintaining efficient material handling operations may find under running cranes to be a practical choice. However, the decision should consider specific operational requirements, facility constraints, and long-term efficiency goals to ensure the selected crane configuration meets overall business objectives effectively.
Space and Structural Requirements
Under Running Bridge Cranes:
- Space Requirements: Excel in environments with limited headroom as they operate beneath the runway beams, maximizing vertical space utilization.
- Structural Requirements: Relies on the building’s roof structure for support, minimizing the need for additional floor-mounted columns. This makes them suitable for facilities where floor space is at a premium.
Top Running Bridge Cranes:
- Space Requirements: Require ample overhead clearance for the crane and load movement above the runway beams. They are suitable for environments with high ceilings and extensive horizontal space.
- Structural Requirements: Demand robust support systems, including heavy-duty runway beams and support columns. Installation may require significant structural reinforcements to support the crane's weight and operational loads.
- Comparison: Under running bridge cranes are advantageous in space efficiency and structural integration, particularly in facilities with constrained vertical space. Top running cranes require more significant space and structural investments but offer superior load capacity and operational capabilities.
Operational Efficiency
Ease of Use
- Under Running Bridge Cranes: Generally easier to operate and maneuver due to their simpler design and lighter load capacities. Operators can quickly learn to use the controls effectively, contributing to operational efficiency.
- Top Running Bridge Cranes: More complex controls and operational procedures due to their heavy-duty capabilities and larger load handling. Operators may require more extensive training and experience to operate these cranes safely and efficiently.
Reliability and Lifespan
- Under Running Bridge Cranes: Known for their reliability in light to medium-duty applications. With proper maintenance, under running cranes can have a long operational lifespan, providing consistent performance over time.
- Top Running Bridge Cranes: Designed for heavy-duty operations, offering robust reliability and durability. When maintained correctly, top running cranes can withstand rigorous industrial environments and maintain operational efficiency for decades.
Comparison: Reliability, Service Life, and Durability
Top Running Bridge Cranes:
- Engineered for Heavy-Duty Use: - Designed to withstand rigorous industrial environments and heavy material handling requirements. - Constructed with robust structural components, including stronger bridge girders and runway beams, to support higher load capacities.
- Longer Service Life: - Typically offer a longer service life compared to under running cranes due to their heavy-duty construction and durable components. - Designed to endure frequent use, high loads, and continuous operation without compromising performance or reliability.
- Durability in Demanding Settings: - Suitable for demanding industrial settings such as steel mills, manufacturing plants, and shipping terminals where continuous and heavy lifting operations are common. - Provide reliable performance over extended periods, minimizing downtime and maintenance requirements.
Under Running Bridge Cranes:
- Moderate to Light-Duty Applications: - Suited for applications where heavy lifting capabilities are not essential and lighter loads are handled. - May have a shorter service life compared to top running cranes when subjected to frequent use and heavy loads.
- Cost-Effective Solution: - Offer cost-effective material handling solutions for facilities with moderate material handling needs and budget constraints. - Provide reliable performance with proper maintenance but may require more frequent servicing compared to top running cranes.
Maintenance and Service Considerations:
- Maintenance Requirements: - Top running cranes typically have components located on top of the runway beams, facilitating easier access for maintenance and inspections. - Under running cranes may require specialized equipment or more effort to access components located underneath the runway beams, potentially increasing maintenance time and costs.
- Environmental Factors: - Both types of cranes require proper maintenance to ensure reliability and longevity, taking into account factors such as temperature variations, humidity levels, and exposure to corrosive substances. - Top running cranes are often equipped with protective coatings and materials to enhance resistance to environmental elements, contributing to their durability in harsh conditions.
While both top running and under running bridge cranes can be reliable with proper maintenance, top running cranes are specifically engineered for longer service life and durability in demanding industrial settings. Their heavy-duty construction, robust components, and ability to handle higher loads make them well-suited for continuous and intensive material handling operations. Businesses operating in industries with heavy material handling requirements should consider top running cranes for their superior durability, reliability, and long-term performance, ensuring minimal downtime and maximum operational efficiency over the crane's lifespan.
Economic Considerations
Initial Investment
- Under Running Bridge Cranes: Lower initial investment compared to top running cranes due to simpler design, fewer structural requirements, and lower installation costs. They provide a cost-effective solution for facilities with moderate material handling needs.
- Top Running Bridge Cranes: Higher initial investment due to the need for heavy-duty components, robust support structures, and more complex installation requirements. This initial cost outlay is necessary for industries requiring high load capacities and extensive operational spans.
Comparison: Under running bridge cranes offer a more economical initial investment, making them suitable for budget-conscious projects or operations with lighter material handling demands. Top running cranes justify their higher initial cost through superior performance in heavy-duty applications.
Long-term Operational Costs
- Under Running Bridge Cranes: Lower long-term operational costs due to simpler maintenance requirements and lower energy consumption compared to top running cranes. They are cost-effective to operate over their lifespan, particularly in light to medium-duty applications.
- Top Running Bridge Cranes: Higher long-term operational costs due to more frequent maintenance needs, higher energy consumption, and potential for costly repairs associated with heavy-duty operations and complex crane systems.
Comparison: Under running bridge cranes offer advantages in long-term operational costs, requiring less maintenance and consuming less energy compared to top running cranes designed for heavy-duty applications.
In summary, the comparative analysis between under running and top running bridge cranes highlights their distinct performance metrics, operational efficiencies, and economic considerations. Each type of crane offers unique advantages and trade-offs, making it essential to align the crane choice with specific operational requirements and budget constraints in industrial settings.
Conclusion
Summary of Key Points
Recap of Advantages and Disadvantages
- Throughout this comparative analysis, under running bridge cranes have been highlighted for their space efficiency, flexibility in building integration, and cost-effectiveness for light to medium-duty applications. However, they are limited by their lower load capacity, potential wear on the support structure, and constraints in certain building layouts.
- In contrast, top running bridge cranes offer advantages such as higher load capacity, greater stability, and suitability for heavy-duty applications and larger spans. Despite these strengths, they come with higher initial costs, require robust building structures, and involve more complex installation and maintenance procedures.
Summary of Suitable Applications
- Under running bridge cranes are well-suited for manufacturing facilities with space constraints, light to medium-duty operations, and situations requiring flexibility in crane placement. They excel in environments where maximizing vertical space and integrating into existing structures are essential.
- Top running bridge cranes find their ideal applications in heavy manufacturing and industrial settings, large warehouses and storage facilities, and environments demanding high load capacities and extensive operational spans. They are designed to handle heavy materials and provide stable, reliable performance in rigorous industrial operations.
Final Comparison
Under Running Bridge Cranes: Recommended for industries and applications where space efficiency, flexibility in placement, and lower initial investment are critical. Suitable for light to medium-duty operations and facilities with existing overhead structures suitable for support.
Top Running Bridge Cranes: Recommended for industries requiring high load capacities, stability, and long spans. Ideal for heavy-duty applications, large-scale manufacturing, and facilities with ample vertical and horizontal space.
Decision-Making Factors for Choosing Between Under Running and Top Running Bridge Cranes
- When deciding between under running and top running bridge cranes, consider the following factors:
- Load Requirements: Evaluate the maximum load capacity needed for your operations.
- Space Constraints: Assess the available space and overhead clearance in your facility.
- Budget: Consider initial investment costs, long-term operational expenses, and maintenance requirements.
- Operational Needs: Determine the specific tasks, material handling requirements, and operational efficiencies desired.
Choosing the right crane type involves balancing these factors to align with your operational goals and budget constraints effectively.
The future of bridge cranes will likely see advancements in automation, sensor technology, and digital connectivity. These innovations will enhance crane efficiency, safety features, and operational capabilities, making them more adaptable to evolving industrial demands.
As industries evolve, there will be increased demand for cranes that offer versatility, efficiency, and sustainability. Emerging applications may include integration with IoT (Internet of Things) for predictive maintenance, AI (Artificial Intelligence) for autonomous operations, and eco-friendly designs to reduce energy consumption and environmental impact.
In conclusion, while under running and top running bridge cranes serve distinct purposes and have specific strengths and weaknesses, both types play crucial roles in industrial operations. Understanding their comparative advantages, suitable applications, and future trends is essential for making informed decisions in selecting the appropriate crane type to optimize efficiency, productivity, and safety in industrial environments.