10-15 Tons Overhead Cranes for Automotive Part Heavy-Duty Transmission Handling
Overview of Heavy-Duty Transmission Handling in Automotive Manufacturing
In the automotive manufacturing sector, handling heavy-duty transmissions is a critical task. Transmissions, which are vital components of a vehicle's drivetrain, can weigh between 10 and 15 tons. Due to their substantial weight and intricate design, moving and positioning these units requires specialized equipment. Efficient handling of transmissions is crucial for maintaining the smooth operation of assembly lines and ensuring that vehicles are built to high standards of quality and performance.
Importance of Efficient Handling for Heavy Transmissions
Efficient handling of heavy transmissions offers several key advantages. Firstly, it significantly improves the speed of the assembly process. By using specialized equipment designed to lift and maneuver these heavy units, manufacturers can streamline the workflow, reducing the time it takes to assemble each vehicle. This efficiency helps to meet production deadlines and increase overall throughput.
Moreover, effective handling reduces the risk of damage to both the transmissions and other vehicle components. Heavy transmissions are delicate and expensive; improper handling can lead to costly repairs or replacements. Efficient handling minimizes the potential for such damage, protecting valuable assets and reducing operational costs.
Another important factor is the safety of the workforce. Handling heavy transmissions manually or with inadequate equipment poses significant risks to workers. Injuries from lifting or positioning heavy parts can lead to downtime and increased insurance costs. Using appropriate overhead cranes mitigates these risks by allowing for safer and more precise movements, thereby creating a safer working environment.
Role of Overhead Cranes in Enhancing Productivity and Safety
Overhead cranes play a crucial role in improving both productivity and safety in the handling of heavy-duty transmissions. These cranes are designed to lift and move heavy loads with ease, offering a level of precision and control that manual methods cannot match. By automating the lifting and positioning processes, overhead cranes help to reduce the physical strain on workers and minimize the likelihood of errors.
In terms of productivity, overhead cranes enable faster and more efficient assembly operations. They can quickly and accurately position transmissions where they are needed, allowing assembly lines to maintain a steady pace. This increased efficiency not only helps to meet production targets but also contributes to overall operational effectiveness.
Safety is another major benefit of using overhead cranes. These cranes are equipped with advanced safety features such as overload protection, emergency stop functions, and precise control systems. These features help to prevent accidents and ensure that transmissions are handled safely and securely. Additionally, the use of overhead cranes reduces the need for manual lifting, further lowering the risk of worker injuries.
In summary, overhead cranes are essential for efficient and safe handling of heavy-duty transmissions in automotive manufacturing. Their ability to enhance productivity, ensure precision, and improve safety makes them invaluable tools in the industry.
Understanding Heavy-Duty Overhead Cranes
Definition and Purpose
Heavy-duty overhead cranes are industrial lifting devices designed to handle very heavy loads, typically ranging from 10 to 15 tons. These cranes are characterized by their robust construction and powerful lifting mechanisms, making them suitable for tasks that require moving and positioning large, heavy components. In automotive manufacturing, these cranes are indispensable for handling critical components like transmissions, which are crucial for vehicle performance but are too heavy and cumbersome to manage manually.
The primary purpose of a 10-15 tons overhead crane is to efficiently lift and transport these heavy units within the manufacturing or assembly plant. By providing a controlled and safe method for handling such loads, these cranes help streamline production processes, improve workflow efficiency, and reduce the risk of injuries associated with manual handling.
What Defines a 10-15 Tons Overhead Crane
A 10-15 tons overhead crane is defined by its lifting capacity, which ranges from 10 to 15 tons, making it suitable for handling heavy automotive components. These cranes are designed with the strength and durability to support and maneuver such substantial weights safely.
Key characteristics that define these cranes include:
- Load Capacity: The ability to lift and move loads between 10 and 15 tons.
- Span and Reach: The width and length of the crane’s coverage area, which determines how far it can extend to lift and place loads.
- Construction: Typically built with heavy-gauge steel and high-strength materials to withstand the stress of lifting heavy weights.
- Hoisting Mechanism: Equipped with powerful hoists and trolleys capable of handling the substantial load.
Typical Applications in Automotive Manufacturing
In automotive manufacturing, 10-15 tons overhead cranes are commonly used in various applications, including:
- Transmission Assembly: Lifting and positioning heavy transmissions during the assembly process, ensuring they are accurately placed in the vehicle.
- Component Handling: Moving large and heavy parts between different stages of production or to storage areas.
- Maintenance and Repair: Facilitating the removal and installation of transmissions for maintenance or repair, which requires careful handling due to the weight and complexity of these components.
These cranes are essential for managing the logistical challenges associated with heavy automotive parts, enabling a smooth and efficient manufacturing process.
Key Features and Specifications
Load Capacity and Range
One of the most critical specifications of a 10-15 tons overhead crane is its load capacity, which ensures it can handle the heavy transmissions and other automotive components. The load capacity directly impacts the crane's performance and efficiency in handling large components. Additionally, the crane’s range, including its span and lift height, must be suitable for the specific layout and operational needs of the manufacturing facility.
Design Variations Specific to Transmission Handling
Overhead cranes used for transmission handling are designed with specific features to accommodate the unique requirements of these heavy components:
- Heavy-Duty Hoists: Equipped with hoists that can handle the high weight of transmissions without compromising safety or performance.
- Customizable Lifting Devices: Some cranes may include specialized lifting devices or attachments designed for the precise handling of transmissions.
- Enhanced Stability Features: Design elements that ensure stability during lifting and maneuvering, such as reinforced support structures and advanced control systems.
In summary, 10-15 tons overhead cranes are vital for the efficient handling of heavy transmissions in automotive manufacturing. Their robust design and specialized features enable them to manage substantial loads safely and effectively, contributing to streamlined production and enhanced safety.
Benefits of Using 10-15 Tons Overhead Cranes
Efficiency in Assembly Processes
Streamlining the Transmission Installation
Overhead cranes with a 10-15 tons capacity greatly enhance the efficiency of transmission installation in automotive manufacturing. By providing a controlled and precise method for lifting and positioning heavy transmissions, these cranes help speed up the assembly process. The crane’s ability to easily maneuver and place transmissions in exact locations reduces the time required for manual handling and adjustments. This streamlined approach allows for faster assembly cycles, contributing to higher production rates and meeting stringent manufacturing deadlines.
Reducing Manual Labor and Associated Risks
Manual handling of heavy transmissions can be labor-intensive and risky. Overhead cranes alleviate the need for workers to manually lift and position these heavy components, thereby reducing physical strain and potential injuries. By automating the lifting process, the crane minimizes the need for manual labor and associated risks, such as musculoskeletal injuries or accidents related to handling cumbersome parts. This not only protects the workforce but also ensures that the transmissions are handled with the precision necessary to avoid damage.
Enhanced Safety Measures
Safety Features and Compliance with Regulations
Modern 10-15 tons overhead cranes come equipped with a range of safety features designed to comply with industry regulations and standards. These features include overload protection systems, emergency stop functions, and advanced control mechanisms. Overload protection ensures that the crane does not exceed its rated capacity, which can prevent mechanical failures and potential accidents. Emergency stop functions provide a quick means to halt crane operation in the event of an unforeseen issue. These safety measures contribute to a safer working environment and help manufacturers adhere to strict safety regulations.
Minimizing the Risk of Accidents and Damage
The use of overhead cranes significantly reduces the risk of accidents and damage associated with handling heavy transmissions. The crane’s precise control over lifting and positioning helps to avoid mishandling, which could lead to accidents or damage to both the transmissions and surrounding equipment. By minimizing manual intervention and ensuring that heavy components are securely lifted and placed, overhead cranes help create a safer and more controlled environment in the manufacturing facility.
Improved Maintenance and Repairs
Facilitating Easy Access to Transmission Units
When it comes to maintenance and repair activities, overhead cranes are invaluable. They provide easy access to transmission units by allowing them to be lifted and positioned precisely where needed. This accessibility makes it simpler for maintenance personnel to inspect, repair, or replace parts without having to navigate around obstacles or struggle with heavy components. By facilitating straightforward access, cranes help ensure that maintenance tasks are performed efficiently and accurately.
Reducing Downtime During Maintenance Activities
Overhead cranes play a crucial role in minimizing downtime during maintenance activities. With their ability to quickly and safely lift and move heavy transmissions, the time required to perform maintenance tasks is significantly reduced. This efficiency helps to keep production lines running smoothly and minimizes interruptions to the manufacturing process. By reducing downtime, overhead cranes contribute to overall productivity and operational efficiency in automotive manufacturing.
In summary, the use of 10-15 tons overhead cranes offers substantial benefits in terms of efficiency, safety, and maintenance. They streamline assembly processes, enhance safety measures, and improve maintenance procedures, all of which are crucial for maintaining an effective and productive manufacturing operation.
Types of 10-15 Tons Overhead Cranes Suitable for Transmission Handling
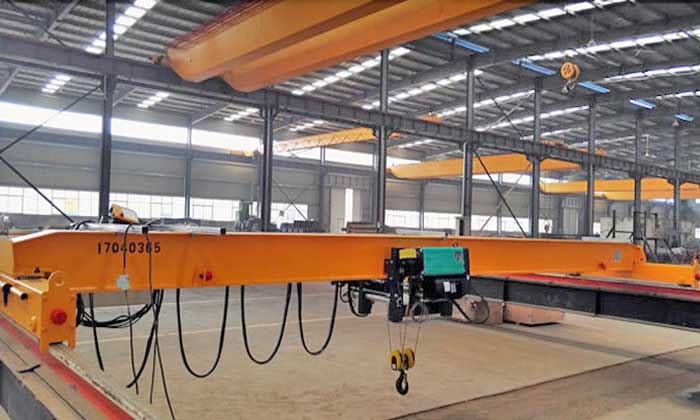
Single Girder Overhead Cranes
Design and Advantages for Heavy-Duty Tasks
Single girder overhead cranes are designed with a single horizontal beam (girder) supported by end trucks. This straightforward design makes them a cost-effective solution for many industrial lifting needs. For heavy-duty tasks, these cranes can be configured with robust hoists and trolleys to handle loads up to 15 tons. The simplicity of the single girder design allows for easier maintenance and reduced installation costs compared to more complex systems.
Typical Load Capacities and ApplicationsSingle girder cranes typically handle loads between 10 and 15 tons, making them suitable for many automotive manufacturing applications. They are often used in environments where space is limited or where budget constraints are a concern. In transmission handling, single girder cranes can efficiently lift and position transmissions, though they may be less suitable for extremely heavy or oversized components compared to double girder models.
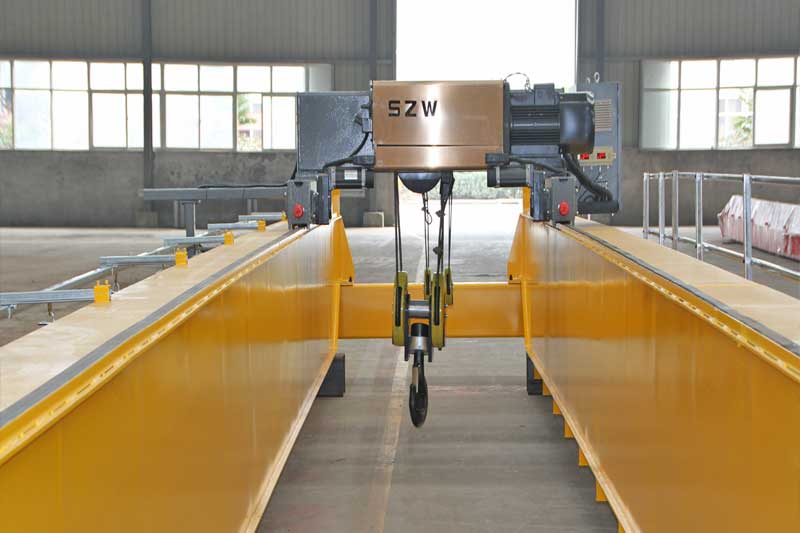
Double Girder Overhead Cranes
Enhanced Stability and Capacity
Double girder overhead cranes feature two parallel beams (girders) that provide increased strength and stability. This design allows for higher load capacities and better distribution of weight, making them ideal for handling very heavy loads like automotive transmissions. The double girder setup provides greater structural support and allows for larger hoists with higher lifting capacities, enhancing the crane’s overall performance.
Benefits for Handling Heavy Transmission Units
For handling transmissions that weigh up to 15 tons, double girder cranes offer significant benefits. The increased stability and strength of the double girder design reduce the risk of load sway and ensure smooth, precise movements. This stability is crucial for positioning heavy transmissions accurately and safely. Additionally, the larger span and higher lifting heights available with double girder cranes accommodate the diverse needs of transmission handling in automotive plants.
Bridge Cranes
Versatility and Coverage in Large Assembly Areas
Bridge cranes, often referred to as overhead bridge cranes, consist of a bridge that spans the width of the work area with a hoist and trolley system moving along the bridge. This design provides extensive coverage over large assembly areas, making it ideal for automotive manufacturing facilities with expansive workspaces. The ability to cover a wide area allows for versatile handling of heavy transmissions and other large components.
Specific Features for Handling Transmissions
Bridge cranes can be equipped with specialized features to enhance their effectiveness in handling transmissions. These may include:
- Extended Hoist Reach: To access transmissions across a wide area without repositioning the crane.
- Advanced Control Systems: For precise and smooth operation when lifting and positioning heavy units.
- Customizable Lifting Attachments: To accommodate the specific shape and weight distribution of transmissions.
These features make bridge cranes particularly valuable in environments where large and heavy transmissions need to be maneuvered across extensive production or assembly lines.
In summary, each type of 10-15 tons overhead crane offers unique advantages for handling heavy transmissions. Single girder cranes are cost-effective and suitable for many tasks, double girder cranes provide enhanced stability and capacity, and bridge cranes offer versatility and extensive coverage in large assembly areas. Selecting the appropriate crane type depends on the specific needs of the manufacturing facility and the characteristics of the transmissions being handled.
10 Ton Overhead Crane
Overview: A 10-ton overhead crane is designed to lift and move loads weighing up to 10 tons. It is commonly used in various industrial applications, including automotive manufacturing, where it handles components such as engines, transmission units, and heavy machinery parts. These cranes can be configured as single girder or double girder systems, depending on the specific needs of the application.
Single girder overhead crane 10 ton for sale
Key Features:
- Load Capacity: Up to 10 tons, suitable for medium to heavy-duty tasks.
- Design Variations: Available in single girder and double girder configurations. Single girder cranes are more cost-effective and suited for lighter loads, while double girder cranes offer greater stability and load capacity.
- Hoist and Trolley Systems: Equipped with powerful hoists and trolleys to handle the specified load capacity. Features include variable speed controls, load limit switches, and smooth start/stop mechanisms.
- Applications: Ideal for handling medium-heavy parts in automotive manufacturing, construction, and general industrial settings.
Benefits:
- Efficiency: Improves workflow by automating the lifting and moving of heavy loads, reducing manual labor.
- Safety: Equipped with safety features to prevent overloads and accidents, enhancing workplace safety.
- Versatility: Suitable for a range of tasks, from assembly to maintenance and repair.
15 Ton Overhead Crane
Overview: A 15-ton overhead crane is built to handle heavier loads, making it ideal for applications that involve substantial components, such as large automotive parts or heavy industrial equipment. This crane type is usually available in both single girder and double girder designs, with the double girder configuration offering enhanced load capacity and stability.
Key Features:
- Load Capacity: Up to 15 tons, designed for heavy-duty lifting tasks.
- Design Variations: Typically found in double girder configurations for increased strength and stability, although single girder models are available for lighter tasks.
- Hoist and Trolley Systems: Features high-capacity hoists and trolleys for handling heavy loads. Includes advanced control systems for precise operation, and overload protection systems to prevent equipment failure.
- Applications: Commonly used for lifting and moving large automotive parts, such as transmissions and engine blocks, as well as heavy machinery in manufacturing and industrial environments.
Benefits:
- Enhanced Capacity: Can handle larger and heavier loads than 10-ton cranes, making it suitable for more demanding tasks.
- Improved Stability: Double girder configurations provide greater stability and reduce load sway, ensuring precise positioning.
- Increased Efficiency: Streamlines heavy lifting processes, reducing manual labor and improving operational productivity.
Both 10-ton and 15-ton overhead cranes offer significant advantages in handling heavy loads in various industrial applications. The choice between them depends on the specific lifting requirements and operational needs of the facility.
Components of 10-15 Tons Overhead Cranes
Hoists and Trolleys
Mechanisms for Lifting and Moving Heavy Loads
Hoists and trolleys are critical components of 10-15 tons overhead cranes, responsible for lifting and moving heavy loads. The hoist is the mechanism that actually raises and lowers the load. For cranes handling transmissions and other heavy components, hoists must be capable of lifting weights up to 15 tons. They typically employ electric motors and gear systems to provide the necessary power and control.
Trolleys, on the other hand, move along the bridge of the crane, allowing the hoist to position the load horizontally. They are equipped with wheels and tracks designed to support heavy loads and ensure smooth travel across the crane’s span. Together, hoists and trolleys work in tandem to provide efficient and precise handling of large, heavy transmissions.
Features Ensuring Smooth Operation
To ensure smooth operation, hoists and trolleys come with several features:
- Variable Speed Controls: Allow for fine-tuned lifting and moving speeds, which is crucial for precise positioning of heavy transmissions.
- Load Limit Switches: Prevent overloading by automatically stopping the hoist when the maximum load capacity is approached.
- Smooth Start/Stop Mechanisms: Reduce mechanical strain and ensure stable movements, preventing jerky motions that could damage the load or crane.
Bridge and Runway Systems
Structural Components Supporting Crane Functionality
The bridge and runway systems are the structural backbone of overhead cranes, providing support and stability for lifting and moving operations. The bridge spans the width of the work area, while the runway system includes the tracks or beams on which the bridge travels.
- Bridge: Composed of the main horizontal beams (single or double girder) that support the hoists and trolleys. It is designed to withstand the heavy loads and forces exerted during operation.
- Runway System: Includes the rails or beams installed along the length of the work area, allowing the crane to move back and forth. Proper alignment and support are essential to maintain crane stability and operational efficiency.
Considerations for Effective Installation
Effective installation of bridge and runway systems requires careful planning and execution:
- Load-Bearing Capacity: Ensure that the supporting structures, such as building columns or walls, can handle the weight and forces transmitted by the crane.
- Alignment and Leveling: Accurate alignment and leveling of the runway system are crucial for smooth crane operation and to prevent excessive wear or mechanical issues.
- Maintenance Access: Design installation with future maintenance in mind, ensuring that all components can be easily accessed for inspections and repairs.
Control Systems
Types of Controls (Manual, Electric, Automated)
Control systems govern the operation of overhead cranes, providing the means for operators to manage lifting and movement tasks.
- Manual Controls: Involve physical levers or pendant controls that allow operators to manually control the hoist and trolley movements. These systems offer simplicity but may require more physical effort and precision from the operator.
- Electric Controls: Use electric switches and motors to control the crane’s functions. Electric controls provide greater precision and ease of operation compared to manual systems, reducing the physical strain on operators.
- Automated Controls: Include advanced control systems with programmable settings, remote operation capabilities, and integration with automated manufacturing systems. Automated controls enhance precision, efficiency, and can be customized for specific tasks, such as handling heavy transmissions.
Enhancing Precision and Operator Ease
Control systems are designed to enhance both precision and operator ease:
- Fine Control Settings: Allow for precise adjustments in lifting speeds and movements, crucial for handling heavy components with accuracy.
- User-Friendly Interfaces: Modern control systems often feature intuitive interfaces, including touchscreens or remote controls, making it easier for operators to manage crane functions.
- Safety Features: Incorporate safety measures such as emergency stop buttons and overload alarms to ensure safe operation and protect both the crane and its operators.
In summary, the components of 10-15 tons overhead cranes, including hoists and trolleys, bridge and runway systems, and control systems, play essential roles in ensuring effective and efficient handling of heavy loads. Proper design, installation, and maintenance of these components are key to achieving smooth operation and reliable performance in automotive manufacturing environments.
Installation and Maintenance Considerations
Site Preparation and Installation
Requirements for Effective Crane Setup
Effective installation of a 10-15 tons overhead crane begins with thorough site preparation. The following requirements must be met to ensure a successful crane setup:
- Structural Support: The installation site must have adequate structural support to bear the weight and operational forces of the crane. This includes ensuring that building columns, beams, and floors are strong enough to handle the crane’s load and any dynamic forces generated during operation.
- Clearance Space: Adequate clearance must be provided for the crane’s bridge and runway systems. This includes vertical clearance above the crane and horizontal clearance around the crane’s travel path.
- Power Supply: Ensure that the site has a reliable and appropriately rated power supply for the crane’s electrical systems. Electrical connections must comply with local codes and be capable of handling the crane’s operational demands.
Key Installation Steps and Considerations
- Foundation and Structural Preparation: Begin with the preparation of the foundation and supporting structures. This involves reinforcing floors or installing new supports to accommodate the crane’s weight and operational stresses.
- Runway Installation: Install the runway beams or rails according to the crane’s specifications. Ensure precise alignment and leveling to facilitate smooth crane movement and prevent mechanical issues.
- Bridge Assembly: Assemble the bridge structure, ensuring that it is correctly aligned and securely mounted on the runway system. Verify that all connections are properly fastened and that the bridge operates smoothly across the runway.
- Hoist and Trolley Installation: Install the hoist and trolley systems on the bridge, ensuring that they are correctly positioned and calibrated. Test the systems to confirm that they operate correctly and can handle the specified load capacities.
- Electrical and Control Systems Setup: Connect and test the crane’s electrical and control systems. Ensure that all wiring and controls are properly installed and functioning according to specifications.
Routine Maintenance Practices
Regular Inspections and Maintenance Schedules
Routine maintenance is essential to ensure the reliable performance and longevity of a 10-15 tons overhead crane. Key maintenance practices include:
- Scheduled Inspections: Conduct regular inspections of all crane components, including hoists, trolleys, bridge and runway systems, and control systems. Inspections should check for wear and tear, alignment issues, and signs of potential problems.
- Lubrication and Cleaning: Regularly lubricate moving parts such as hoists, trolleys, and bearings to reduce friction and wear. Keep the crane clean and free of debris to prevent damage and ensure smooth operation.
- Safety Checks: Verify that safety features such as overload protection, emergency stops, and limit switches are functioning correctly. Regularly test these systems to ensure they will operate as intended in case of an emergency.
Addressing Common Issues and Ensuring Longevity
Addressing common issues promptly helps to extend the crane’s lifespan and maintain its performance:
- Load and Travel Issues: Address any problems related to load handling or travel, such as uneven lifting or jerky movements. These issues may indicate problems with alignment, lubrication, or component wear.
- Electrical and Control Problems: Diagnose and repair any issues with the crane’s electrical or control systems, such as malfunctioning controls or power supply problems. Regular checks and maintenance of these systems are crucial for safe and efficient operation.
- Structural Integrity: Monitor the structural integrity of the crane’s bridge and runway systems. Look for signs of wear, cracks, or deformation, and address any structural issues immediately to prevent potential failures.
By adhering to these installation and maintenance considerations, you can ensure the reliable operation and longevity of 10-15 tons overhead cranes. Proper site preparation, installation, and routine maintenance practices are essential for maximizing crane performance, minimizing downtime, and maintaining a safe working environment.
Case Studies and Examples
Successful Implementations in Automotive Plants
Examples of Effective Use in Heavy-Duty Transmission Handling
Case Study 1: Global Automotive Manufacturer’s Assembly Line Upgrade
Background: A leading global automotive manufacturer faced challenges with the handling and installation of heavy transmissions on its assembly line. The existing manual processes were inefficient and prone to errors, causing production delays and safety concerns.
Solution: The company implemented a series of 10-15 tons double girder overhead cranes designed specifically for transmission handling. These cranes featured high-capacity hoists, advanced control systems, and robust safety features.
Implementation:
- Installation: The cranes were installed along the assembly line, with the runway system precisely aligned to cover the entire work area. The installation process included reinforcing the building’s structure to support the new cranes.
- Operation: The cranes were used to lift and position transmissions with high precision, reducing the need for manual handling.
Results and Benefits Observed:
- Increased Efficiency: Production efficiency improved significantly, with assembly times reduced by 30%. The automation of heavy lifting tasks streamlined operations and minimized production delays.
- Enhanced Safety: The new cranes reduced the risk of worker injuries related to manual handling. Safety features such as overload protection and emergency stops contributed to a safer working environment.
- Reduced Downtime: Maintenance and repair tasks were completed more quickly, leading to less downtime and improved overall productivity.
Case Study 2: European Automotive Parts Manufacturer’s Facility Expansion
Background: An automotive parts manufacturer in Europe needed to upgrade its facility to handle an increased volume of heavy-duty transmissions. The existing equipment was outdated and could not meet the new production demands.
Solution: The facility expanded its operations by installing 10-15 tons bridge cranes with extended hoist reach and specialized lifting attachments tailored for transmissions.
Implementation:
- Installation: The bridge cranes were installed in newly constructed sections of the facility. The installation included setting up the runway system to cover the expanded work area and integrating the new cranes with existing production lines.
- Operation: The cranes were equipped with advanced control systems that allowed for precise movements and positioning of heavy transmissions.
Results and Benefits Observed:
- Versatility and Coverage: The new bridge cranes provided extensive coverage over the expanded facility, allowing for versatile handling of transmissions across large assembly areas.
- Improved Production Capacity: The facility’s production capacity increased by 25% due to the enhanced efficiency and flexibility provided by the new cranes.
- Operational Reliability: The cranes’ advanced control systems and reliability reduced the frequency of mechanical issues and improved overall operational consistency.
Case Study 3: North American Automotive Supplier’s Safety Improvement Initiative
Background: An automotive supplier in North America identified safety concerns with its existing manual transmission handling methods. The manual processes were leading to frequent safety incidents and inefficiencies.
Solution: The supplier upgraded to 10-15 tons single girder overhead cranes with state-of-the-art safety features, including load limit switches and smooth start/stop mechanisms.
Implementation:
- Installation: The single girder cranes were installed in key areas of the plant where heavy transmission handling was most critical. The installation focused on integrating the cranes with existing workflows to minimize disruption.
- Operation: The new cranes facilitated safer and more efficient lifting of transmissions, reducing manual labor and enhancing overall safety.
Results and Benefits Observed:
- Enhanced Safety: The safety features of the new cranes significantly reduced the number of workplace injuries. The automation of lifting tasks minimized the physical strain on workers and mitigated safety risks.
- Operational Efficiency: The upgrade led to a more streamlined workflow and a 20% reduction in the time required for transmission handling tasks.
- Cost Savings: The reduction in manual labor and associated safety incidents resulted in cost savings related to injury claims and operational disruptions.
In summary, these case studies highlight the successful implementation of 10-15 tons overhead cranes in automotive manufacturing plants. By addressing specific challenges related to transmission handling, these cranes provided significant improvements in efficiency, safety, and operational capacity. The results demonstrate the value of investing in advanced crane systems to meet the demands of modern automotive production environments.
Conclusion
Summary of Key Points
In summary, 10-15 tons overhead cranes are crucial in automotive manufacturing, particularly for handling heavy transmissions. These cranes offer a robust solution for lifting and moving substantial loads with precision and efficiency. Key types of these cranes, including single girder, double girder, and bridge cranes, each bring unique advantages to the table, tailored to different operational needs and facility layouts.
Recap of Benefits and Features
- Efficiency in Assembly Processes: Overhead cranes significantly enhance the efficiency of transmission installation and other heavy-duty tasks. They streamline operations by automating lifting and positioning, reducing manual labor, and minimizing associated risks.
- Enhanced Safety Measures: Modern overhead cranes come equipped with advanced safety features such as overload protection, emergency stop functions, and precise control systems, contributing to a safer work environment and compliance with safety regulations.
- Improved Maintenance and Repairs: Cranes facilitate easier access to heavy transmissions during maintenance and repair activities, reducing downtime and improving overall productivity.
Final Thoughts on the Role of 10-15 Tons Overhead Cranes in Enhancing Transmission Handling
10-15 tons overhead cranes play a pivotal role in modern automotive manufacturing by addressing the challenges of handling heavy transmissions with efficiency, precision, and safety. Their ability to lift and maneuver substantial loads with ease not only enhances production processes but also contributes to a safer and more productive work environment. By investing in the right overhead crane system, automotive manufacturers can optimize their operations, reduce manual labor, and ensure that their facilities are equipped to meet the demands of today’s automotive industry.