Gantry Cranes 10 Ton, 20 Ton, 50 Ton for Precasting Solid Wall Handling
Gantry cranes optimize precast wall handling, enhancing safety, efficiency, and cost-effectiveness in production, transportation, and installation of concrete panels.
Overview of Precasting Solid Walls
Precast solid walls are large concrete panels manufactured in a controlled factory environment. These walls are cast using molds and cured to meet specific strength and durability standards. Once completed, they are transported to construction sites for installation.
The use of precast solid walls in construction offers several key benefits:
- Quality Control: Manufactured off-site, allowing for better consistency in quality and fewer variables that affect the final product.
- Faster Construction: Because the panels are pre-made, construction time on-site is significantly reduced.
- Durability: Precast walls are designed to be durable and resilient, providing long-lasting performance in various building applications.
Precast solid walls are commonly used in a variety of construction projects, including:
- Residential Buildings: Apartment complexes, townhouses, and other housing structures.
- Commercial Buildings: Offices, retail centers, and educational institutions.
- Industrial Buildings: Factories, warehouses, and distribution centers.
Their versatility and ability to be produced in large volumes make them ideal for large-scale projects, where speed and reliability are essential. These walls are typically used for exterior, partition, and fire-resistant walls, offering significant advantages in terms of construction time, cost, and quality.
Single girder gantry crane 10 ton for sale
Need for Specialized Handling Equipment
Handling precast solid walls requires specialized equipment due to the size, weight, and fragility of these concrete panels. Without the right tools, the risks of damage, inefficiency, and safety issues can increase significantly.
Challenges in Handling Precast Solid Walls
- Weight: Precast panels can weigh several tons, demanding heavy-duty equipment capable of lifting and transporting these loads safely.
- Size: The large dimensions of these walls make it difficult to move them manually or with less powerful equipment.
- Fragility: Despite their strength, concrete panels can crack or break if not handled carefully, making precision and control essential during movement.
- Positioning: Accurate placement of the panels is crucial, whether storing them in the yard or positioning them on the construction site.
Why Specialized Equipment is Necessary
- Safety: Handling heavy, fragile loads requires equipment that minimizes the risk of accidents and injuries.
- Efficiency: Specialized cranes allow for faster movement and precise placement, reducing delays in the construction process.
- Damage Prevention: The right equipment ensures that panels are not damaged during handling, saving costs and avoiding delays.
To address these challenges, gantry cranes are often the best choice. These cranes are designed to handle large, heavy loads and can be customized for precise control, making them ideal for lifting and positioning precast solid walls in both outdoor and indoor environments.
Gantry Crane for Precasting Wall Handling
A gantry crane is a type of crane with a structure that consists of a bridge supported by two or more legs, which move on tracks or wheels. This design allows it to travel across a defined area, lifting and moving heavy loads with precision and efficiency. The basic components of a gantry crane include:
- Bridge: The horizontal beam that spans the area to be served, where the hoist and trolley are mounted.
- Gantry Legs: Vertical supports that hold the bridge and provide the necessary structure for mobility. These legs can move along tracks or wheels.
- Trolley and Hoist: The mechanism on the bridge that moves horizontally and vertically to lift, lower, and position loads.
- Tracks/Wheels: These provide the crane with mobility, allowing it to travel across a workspace or outdoor site.
Gantry cranes are ideal for heavy-duty lifting and handling in large, open spaces, offering versatility in both industrial and construction applications. Their ability to handle large and heavy loads over long distances makes them particularly useful for projects involving precast concrete, heavy machinery, and large structural components.
Differences Between Gantry Cranes and Other Types of Cranes
Gantry Cranes vs. Bridge Cranes:
A bridge crane consists of a girder or bridge mounted on fixed tracks or beams, typically overhead within a building or warehouse. Unlike gantry cranes, which are supported by legs and can move along the ground or across a site, bridge cranes are usually stationary and operate within a fixed framework. Gantry cranes offer more flexibility because they do not rely on the structure of the building for support.
Gantry Cranes vs. Jib Cranes:
A jib crane features a single vertical mast with a horizontal arm (jib) that swings to move the load. Unlike gantry cranes, jib cranes have limited range and are typically used for lifting loads within a confined space, such as at a workstation or assembly area. Gantry cranes, on the other hand, are used for moving larger, heavier loads across greater distances, offering superior mobility and capacity.
Types of Gantry Cranes Suitable for Wall Handling
Full Gantry Cranes:
Full gantry cranes are characterized by their robust structure, where both the bridge and the gantry legs are fully supported by tracks or wheels. These cranes can travel across long distances and are typically used in environments where heavy loads, such as precast concrete walls, need to be moved and positioned with precision. They are especially useful in outdoor environments like construction yards or large precast concrete plants.
Heavy duty gantry crane for sale, full gantry crane design for your needs
Semi-Gantry Cranes:
Semi-gantry cranes are similar to full gantry cranes but have only one side supported by tracks, while the other side is mounted on fixed supports, such as a building structure or rail system. These cranes are suitable for applications where full mobility is not required, or when there is limited space. Semi-gantry cranes are often used in environments where heavy lifting needs to be done within a defined range, such as in warehouses or smaller precast facilities.
Rubber Tyred Gantry Cranes:
Rubber tyred gantry cranes (RTGs) are a highly mobile form of gantry crane, equipped with rubber tyres instead of tracks. This allows them to be easily moved across various surfaces, including rough or uneven ground. RTGs are ideal for outdoor applications where mobility and flexibility are crucial, such as port facilities, container yards, or construction sites. They are commonly used for handling large precast wall panels due to their ability to navigate tight spaces and cover long distances.
Key Features of Gantry Cranes for Precasting Solid Wall Handling
High Load Capacity
Gantry cranes used for precasting solid wall handling are designed to manage heavy loads, as the precast panels themselves are often extremely large and heavy. The typical capacities of these cranes range from 10 tons to 50 tons, or even higher, depending on the size and weight of the wall panels being handled. These cranes must be equipped with robust lifting systems to safely lift and transport these heavy loads without risk of damage.
Typical Capacities:
- 10 Tons: Used for smaller precast panels or lighter applications.
- 20 Tons: Common in precast yards where panels are slightly larger but still manageable for mid-range capacity cranes.
- 50 Tons: Required for handling large precast solid wall panels, often used in industrial or high-rise construction projects where the panels are thick and heavy.
Load Distribution and Design Considerations:
The design of gantry cranes for handling solid wall panels involves ensuring proper load distribution across the entire crane structure. The lifting system, including the hoist and trolley, must be designed to handle heavy loads without compromising structural integrity. Gantry cranes typically feature reinforced components to ensure they can bear the weight of large concrete panels, which may exert significant forces on the crane during lifting and movement. Load-sensing systems and anti-sway mechanisms are often used to ensure even lifting and minimize the risk of damage to both the crane and the precast panels.
Wide Span and Lift Height
For precasting solid walls, gantry cranes need to be designed with a wide span and sufficient lift height to effectively manage large, heavy panels.
- Importance of Span: The span of the crane refers to the distance between the gantry legs that supports the bridge. A wider span allows the crane to cover a larger area and accommodate bigger precast panels. The span is essential for reaching across molds, lifting walls from production areas, and placing them in storage or onto transport vehicles. For precast solid wall handling, the span should be wide enough to clear large molds and allow for easy movement of the walls within the production yard or storage area.
- Consideration of Lift Height: The lift height of the crane is equally important, as it determines the crane's ability to lift the solid wall panels from molds and place them onto trucks or into storage. The lift height must be sufficient to clear the height of typical production molds and transportation vehicles, such as flatbed trucks or shipping containers. For precast concrete panels, which may be several meters tall, a gantry crane with an adequate lift height ensures that panels are lifted smoothly and precisely without risk of damage. The crane should also be able to clear any obstructions in the precast yard or production area during lifting and moving operations.
Mobility and Flexibility
One of the most important features of gantry cranes used in precast solid wall handling is their mobility and flexibility. This is achieved through the use of traveling gantry cranes that move along tracks or on rubber tyres, offering excellent maneuverability across large production yards and construction sites.
- Traveling Gantry Cranes: Traveling gantry cranes are designed to move along fixed tracks or wheels, which provides them with the flexibility to cover long distances and navigate across different areas of the precast yard. This allows the crane to lift and position panels at multiple locations without the need to reposition itself manually. The ability to move across the yard is especially beneficial for handling large precast panels, which may need to be repositioned multiple times during production and transport.
- Importance in Precast Yards: In a precast concrete yard, quick and efficient repositioning is essential to maintain the flow of production. Gantry cranes with the ability to move across tracks or rubber tyres help operators optimize space, reduce downtime, and quickly move panels from the production line to storage or transport vehicles. This mobility ensures a smooth workflow, minimizing the time spent in handling each panel and improving overall productivity in the yard. The flexibility to move panels to various parts of the yard or production line allows for efficient use of space, helping to accommodate multiple stages of production, from casting to storage to shipping.
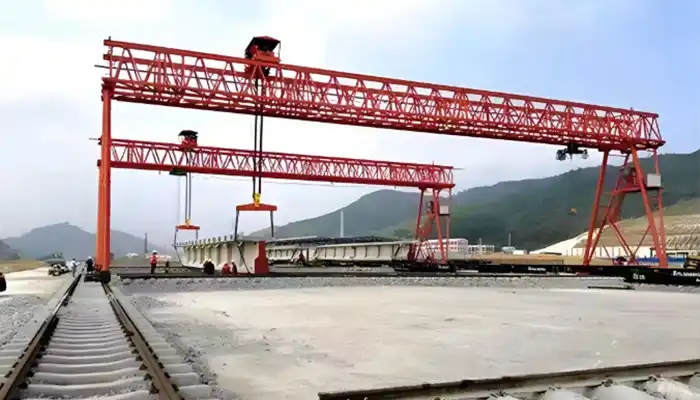
Applications in Precast Concrete Plants
Handling Solid Wall Panels
Gantry cranes are essential in precast concrete plants for lifting and moving solid wall panels throughout the production and transport processes. The efficient movement of these heavy and large panels is critical for maintaining a smooth workflow and meeting production deadlines.
- Lifting and Moving Panels: The primary function of gantry cranes in precast concrete plants is to lift the finished solid wall panels from the production molds. Once the panels have been cured and are ready for transport or storage, the crane’s lifting system uses a hoist and spreader bar to safely lift the panels. The crane then moves the panels from the production area to storage yards or directly onto transport vehicles, such as flatbed trucks or shipping containers.
- Precise Positioning for Loading: Accuracy in positioning is crucial when handling large precast panels. Gantry cranes are equipped with precise control systems to ensure that panels are moved smoothly and placed accurately. This is especially important when loading panels onto trucks or assembly lines, where exact placement is required to avoid damage and ensure safe transport. The ability of gantry cranes to move in multiple directions (longitudinal and lateral) enables them to position panels efficiently, even in tight spaces.
Safe Handling of Heavy and Fragile Loads
Due to the size, weight, and potential fragility of precast concrete panels, it is essential to handle these loads with care to avoid damage during transportation and installation. Gantry cranes are designed to minimize risk and enhance safety during lifting and moving operations.
- Minimizing Risk of Damage: Precast solid wall panels, while strong, can crack or break if subjected to sudden forces or improper handling. Gantry cranes, with their smooth, controlled lifting mechanisms, ensure that the panels are handled carefully and without jerking motions that could lead to cracks or other forms of damage. Specialized lifting equipment, such as lifting clamps, vacuum lifters, or spreader bars, are often used in conjunction with gantry cranes to securely grip the panels and ensure an even lift.
- Importance of Control Systems for Safe Operations: To maintain the integrity of the panels, gantry cranes are typically equipped with advanced control systems that allow operators to manage the lifting speed, angle, and position of the load. Anti-sway technology is often included to prevent the panels from swinging during transport, reducing the risk of damage and ensuring a smooth operation. Moreover, load-sensing systems provide real-time feedback on the weight distribution and load capacity, ensuring that the crane operates within its safe limits.
Outdoor and Indoor Operation
Gantry cranes used in precast concrete plants must be versatile enough to operate in both outdoor and indoor environments. The design of these cranes is adapted to meet the demands of different operating conditions.
- Adaptations for Outdoor Environments: In outdoor precast yards, gantry cranes are exposed to various weather conditions, including rain, snow, and high winds. To ensure reliability and long-lasting performance, these cranes are often equipped with weather-resistant designs. This includes corrosion-resistant materials, like galvanizing or stainless steel components, that prevent damage from exposure to moisture or chemicals commonly found in outdoor environments. Additionally, weatherproof electrical components and protective covers are used to ensure safe operation in inclement weather.
- Indoor Facility Usage: Inside a precast concrete plant, gantry cranes are primarily used for moving panels within the production area. In an indoor environment, these cranes help streamline the production process by quickly and efficiently moving panels from molds to storage or loading areas. With a more controlled environment, the design focus is typically on maximizing efficiency and space utilization, which often leads to the use of cranes with precise control and high lifting capacities. Indoor gantry cranes also help with maintenance tasks and moving other precast elements, such as columns, beams, and other structural components.
The adaptability of gantry cranes to both indoor and outdoor settings ensures they are invaluable assets in the smooth operation of precast concrete plants, whether dealing with heavy loads in harsh weather or facilitating rapid production in controlled environments.
Advantages of Gantry Cranes in Precasting Solid Wall Handling
Improved Safety
Gantry cranes significantly improve safety in precasting plants by reducing the need for human interaction with heavy loads and providing features that enhance operational safety.
Reduced Human Interaction with Heavy Loads:
One of the primary safety advantages of gantry cranes is that they automate the lifting, moving, and positioning of large and heavy precast solid wall panels. By removing the need for workers to manually handle these heavy loads, the risk of injuries, such as musculoskeletal damage, crushing, or falling, is greatly minimized. Operators control the crane from a safe distance, away from the load, which is crucial in preventing accidents.
Enhanced Safety Features:
Gantry cranes come equipped with several safety features to ensure safe lifting and handling of heavy loads:
- Limit switches: These prevent the crane from traveling beyond its designated range, protecting both the crane and the surrounding structures.
- Overload protection: Integrated overload sensors ensure the crane does not exceed its lifting capacity, avoiding the risk of structural failure or damage to the crane.
- Anti-sway systems: These systems prevent swinging and swaying of the load, reducing the risk of the wall panels shifting unexpectedly and causing injury or damage during transport.
These safety features contribute to a more secure and controlled work environment, ensuring the integrity of both the crane and the precast panels.
Enhanced Productivity
The use of gantry cranes in precasting plants can lead to significant increases in productivity, as they drastically reduce the time and manual labor required for moving and handling solid wall panels.
- Increased Speed of Wall Handling: Gantry cranes allow for the rapid lifting, movement, and positioning of solid wall panels, which is much faster than manual handling methods. The crane’s mobility and lifting capacity ensure that panels are handled efficiently, moving from the molds to storage or transport vehicles in a fraction of the time it would take using manual labor or smaller lifting equipment.
- Automation and Control Systems for Streamlined Operations: Many modern gantry cranes are equipped with automation and advanced control systems. These systems allow operators to control the lifting and positioning of panels with minimal effort, enabling precise and consistent movements. Automated features such as load-sensing systems, sway control, and synchronization of the hoist and trolley help streamline operations by reducing the need for manual adjustments and improving the overall efficiency of wall handling.
Cost Efficiency
Investing in gantry cranes for precasting solid wall handling offers substantial long-term cost savings, particularly in labor, material handling, and maintenance.
- Long-Term Cost Savings: By automating the handling of heavy precast panels, gantry cranes reduce the need for large teams of workers to manually move and position these panels. This results in reduced labor costs over time, as fewer workers are required for the same tasks. Additionally, the use of precise control systems ensures that panels are handled with care, reducing the likelihood of material damage during the lifting and moving process. Fewer damaged panels mean fewer material replacements, leading to further cost savings.
- Lower Maintenance and Operational Costs: Gantry cranes are designed for durability and long-term performance, with many models featuring components that are easy to maintain and repair. Compared to other lifting systems, such as overhead cranes or forklifts, gantry cranes typically have lower maintenance costs because they are less prone to breakdowns and require fewer repairs. The ability to control and monitor crane operations remotely also reduces the chances of wear and tear, as well as the risk of misuse by operators.
Design Considerations for Precasting Solid Wall Handling Gantry Cranes
Structural Design and Load Handling
Designing gantry cranes for precasting solid wall handling involves several key considerations to ensure the crane can safely and efficiently handle the heavy, large loads typically associated with precast panels.
- Load Distribution: The crane’s structure must be designed to handle the substantial weight of solid wall panels. This involves ensuring that the load is evenly distributed across the crane’s bridge and gantry legs. The lifting mechanism, including the hoist, trolley, and spreader bars, should be designed to manage the weight without compromising the crane’s stability.
- Reinforced Components: Heavy-duty cranes require reinforced components, such as thicker steel for the bridge and legs, to bear the weight of large panels. These reinforcements are critical for ensuring the crane operates safely under full load conditions and has the strength to withstand repeated use.
Span and Lift Height Considerations
- Wide Span: To accommodate the large size of precast solid wall panels, gantry cranes are designed with a wide span. This ensures that the crane can move the panels easily across a large production or storage area. The wider the span, the more space the crane can cover, allowing for efficient handling of multiple panels simultaneously.
- Lift Height: A gantry crane used in precast plants must have a sufficient lift height to clear the molds and transport vehicles, ensuring that wall panels can be lifted easily and safely. The lift height should be adjusted based on the typical height of the molds and the required lifting height for loading panels onto trucks.
Mobility and Flexibility
- Mobility Features: Gantry cranes used in precasting plants should have mobility features that allow them to move freely across the yard or facility. Rubber-tyred gantry cranes (RTGs) are often employed in outdoor environments due to their ability to move easily on uneven terrain. For indoor use, track-mounted gantry cranes provide the stability needed for precise lifting and transportation.
- Flexibility for Different Operations: The crane design should allow for flexibility in operation. This includes the ability to move panels to various areas of the yard, place panels on different trucks, and support different panel sizes. The crane must be adaptable to various production lines and storage areas, ensuring that it can handle both large and small panels efficiently.
Safety Features and Automation
- Safety Design Elements: Safety features like anti-sway systems, overload protection, and limit switches must be integrated into the crane’s design to prevent accidents and damage to both the crane and the precast panels. These features help to ensure smooth and safe lifting operations, even with very large or heavy loads.
- Automation for Precision: Many modern gantry cranes incorporate automation features to enhance precision and ease of use. Automation can include synchronization of lifting movements, real-time load monitoring, and automated positioning to ensure the panels are handled with maximum efficiency and minimal risk of error.
The design of gantry cranes for precasting solid wall handling is crucial to ensure that the crane meets the specific needs of the precast concrete industry, providing both operational efficiency and safety for handling large, heavy panels.
Case Studies and Real-World Applications
Precast Concrete Plant in Urban Development
Gantry cranes play a crucial role in the large-scale production and handling of solid wall panels for residential towers in urban development projects. The demand for high-rise buildings in cities requires the efficient manufacturing, transport, and installation of large precast concrete panels, which serve as the exterior walls of these towers.
- Facilitating Large-Scale Production: In a typical precast concrete plant dedicated to urban development, gantry cranes are used to manage the production of solid wall panels, which can be several meters tall and heavy. These panels are cast in molds on the plant floor and require precise handling to avoid damage. Gantry cranes with high load capacities and wide spans allow for the quick and safe movement of these panels from the production area to storage and loading zones, and eventually onto trucks for transport to the construction site.
- Handling Panels for Residential Towers: For residential towers, where construction timelines are tight, gantry cranes improve productivity by minimizing manual labor and reducing handling times. They enable the efficient lifting and placement of panels directly onto transport vehicles, reducing the risk of delays. The automation and control systems of the cranes ensure that panels are placed precisely where needed, preventing the costly rework and re-positioning of heavy panels.
By utilizing gantry cranes, precast concrete plants can meet the demands of large urban construction projects, ensuring the efficient delivery of high-quality panels for residential buildings while maintaining safety and precision.
Industrial Use for Precast Wall Panels
In industrial parks and commercial buildings, precast wall panels are often used for their durability, speed of installation, and cost-effectiveness. Gantry cranes are invaluable in these projects, helping manage the production, movement, and installation of the large panels used in the construction of warehouses, factories, and office buildings.
- Use in Industrial Parks: In a precast plant that serves industrial parks, gantry cranes are responsible for handling panels of various sizes, which are typically thicker and heavier than those used in residential buildings. These panels are produced in molds, then transported to storage or directly to loading docks for delivery to the construction site. Gantry cranes with high lifting capacities (often ranging from 20 to 50 tons) and large spans ensure that even the heaviest and most complex panels can be handled efficiently.
- Commercial Building Applications: For commercial buildings, where precast panels are commonly used for exterior facades, the speed and precision of gantry cranes are key. The use of automated crane systems minimizes handling times, streamlining the process from production to transportation. In addition to managing panel lifting, the cranes are also equipped with features such as anti-sway technology to ensure smooth and secure transport, particularly important when handling large, fragile panels.
This case exemplifies how gantry cranes improve the overall efficiency of precast concrete handling in industrial and commercial applications, reducing labor costs and increasing safety while maintaining high throughput.
Custom Gantry Crane Installation for a Specialized Project
Some precast concrete projects require tailored crane systems to meet unique customer needs, such as specialized wall panel shapes, sizes, or production processes. In such cases, a customized gantry crane system can be designed to accommodate specific requirements and ensure smooth operations.
- Tailored Systems for Unique Needs: In one such project, a precast concrete plant needed a gantry crane system designed to handle extremely large and irregularly shaped panels for a specialized construction project. The project involved the production of precast panels with unconventional dimensions, such as curved or angled walls, which required customized lifting equipment. The crane system was designed with adjustable spans and specialized lifting attachments, such as custom clamps and spreaders, to accommodate the diverse range of panel sizes and shapes.
- Precision Handling for Specialized Projects: For this project, the gantry crane was equipped with advanced automation systems for precise positioning and synchronized lifting. These features allowed for quick and accurate placement of irregular panels, ensuring they were moved and installed with minimal risk of damage. Custom features, such as enhanced anti-sway systems and load sensors, were also incorporated to handle the unique requirements of this high-stakes project.
This case demonstrates the flexibility of gantry cranes in adapting to specialized needs and how tailored systems can optimize the handling of complex precast solid wall panels, ensuring both efficiency and safety in non-standard applications.
Conclusion
Gantry cranes offer significant advantages in the handling of precast solid wall panels, enhancing safety, efficiency, and cost-effectiveness throughout the production and transportation processes. By automating the movement and placement of large, heavy panels, these cranes:
- Improve Safety: The use of gantry cranes minimizes human interaction with heavy loads, reducing the risk of workplace injuries. Integrated safety features such as overload protection, anti-sway systems, and limit switches further ensure safe operations.
- Increase Efficiency: Gantry cranes streamline operations by speeding up the handling and transportation of panels. With features such as precise control systems and automation, they reduce handling times, enabling faster turnaround from production to delivery.
- Enhance Cost-Effectiveness: By reducing labor costs and minimizing material damage, gantry cranes contribute to long-term savings. Their durability and lower maintenance requirements also make them a cost-effective investment in the precast concrete industry.
As the precast concrete industry continues to grow, investing in efficient, reliable handling equipment such as gantry cranes is becoming increasingly important. These cranes provide not only the necessary lifting power and flexibility for handling heavy solid wall panels but also contribute to safety, productivity, and cost savings. The long-term benefits of gantry cranes make them a vital asset for precast concrete manufacturers who aim to remain competitive and meet the growing demand for faster, safer, and more efficient construction solutions.
The continued integration of advanced technologies into gantry cranes will only enhance these benefits, making them an even more indispensable tool in the future of precast concrete manufacturing.