Buying Electromagnets: What You Need to Know to Make the Right Choice
Buying Electromagnets: Key Factors for Optimal Performance and Efficiency
What You Need to Know to Make the Right Choice
The Critical Role of Electromagnets in Various Industrial Applications
Electromagnets are essential in many industries. From lifting heavy metal scrap to moving parts on production lines, they help make tasks faster, safer, and more efficient. Their ability to create strong magnetic fields temporarily makes them perfect for jobs that require quick attachment and release of metal objects. Simply put, electromagnets are a key tool in modern industrial operations.
Importance of Choosing the Right Electromagnet
Choosing the right electromagnet is crucial for smooth and safe operations. The wrong one can cause problems like poor performance, wasted energy, or even accidents. For instance, if an electromagnet doesn’t have enough power to hold a load, it could lead to dangerous situations or damage. On the other hand, choosing one that’s too strong could waste energy and potentially harm materials. The right electromagnet helps save energy, reduces maintenance costs, and ensures safety for workers, improving the overall reliability of your equipment.
Overview of the Article
In this article, we’ll break down the key factors to consider when buying an electromagnet. You’ll learn what to look for, from load capacity to voltage requirements, so you can choose the one that’s best for your needs. Whether you're replacing an old electromagnet or buying one for a new project, this guide will help you make the right choice for performance, efficiency, and safety.
Electromagnets and Their Applications
What is an Electromagnet? Definition and Basic Operation
An electromagnet is a type of magnet where the magnetic field is produced by an electric current. Unlike permanent magnets, which always have a magnetic field, the strength of an electromagnet can be controlled by adjusting the current flowing through it. When the current is turned off, the magnetic field disappears.
The basic operation of an electromagnet relies on the principle of electromagnetism: when electricity flows through a coil of wire, it creates a magnetic field around the wire. By placing a magnetic core, usually made of iron or steel, inside the coil, the magnetic field becomes stronger and more focused, making it capable of lifting or attracting metal objects.
Key Components: Coil, Core, Power Source
- Coil: The coil, made of copper or other conductive wire, is where the electric current flows. The number of turns in the coil and the current’s strength affect the power of the magnetic field. The more turns in the coil and the higher the current, the stronger the magnet.
- Core: The core is typically made of ferromagnetic material like iron, which enhances the magnetic field created by the coil. The core helps concentrate the magnetic force, making the electromagnet much stronger than a simple coil of wire.
- Power Source: The power source provides the electricity that flows through the coil. This could be a direct current (DC) or alternating current (AC), depending on the specific requirements of the electromagnet and its application.
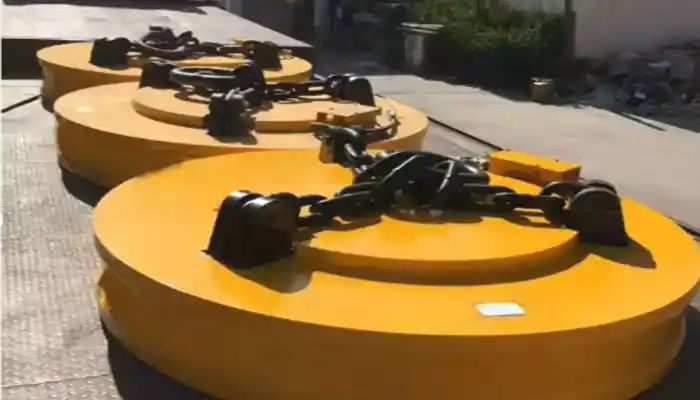
Common Applications
Manufacturing and Material Handling Electromagnets are widely used in manufacturing for handling materials like steel or scrap metal. In scrap yards, they help lift and move large pieces of metal, making it easy to sort and transport materials. In manufacturing plants, electromagnets are used to move metal parts efficiently through different stages of production.
Automotive Industry On automotive assembly lines, electromagnets are used to handle metal components such as engine parts, frames, or exhaust systems. They help lift, position, and move parts with precision, reducing manual labor and improving efficiency in the assembly process.
Construction Electromagnets are often used on construction sites to move heavy materials such as steel beams or rebar. Cranes equipped with electromagnets can lift and move large metal objects, reducing the need for cranes with mechanical hooks and providing more control and speed in material handling.
Other Industrial Uses Electromagnets are also used in various other industrial applications:
- Magnetic Separators: Used to separate metal contaminants from raw materials like ore or food products, electromagnets can attract and remove unwanted metals during processing.
- Cranes: Specialized cranes, often called "magnetic cranes," are fitted with electromagnets to lift and move ferrous metals in warehouses or shipping yards.
- Recycling: In recycling plants, electromagnets are essential for separating different types of metals from mixed waste materials.
These applications highlight the versatility of electromagnets, as they are used in everything from large-scale industrial processes to precision tasks in manufacturing and construction.
Key Factors to Consider When Buying Electromagnets
Load Capacity
When selecting an electromagnet, it’s essential to ensure that it can handle the weight and size of the materials you need to lift or move. The load capacity indicates the maximum weight the electromagnet can safely hold.
- Assessing Material Weight: Determine the weight and size of the objects you will be lifting. For heavy materials like steel beams or scrap metal, choose an electromagnet with a higher load capacity.
- Safety Considerations: An electromagnet that is too weak may cause materials to slip or fall, leading to accidents. On the other hand, choosing one that’s too strong can be inefficient and unnecessarily costly.
Selecting the right load capacity ensures the electromagnet operates safely and efficiently, without overloading or underperforming.
Electromagnetic Force (Holding Power)
Holding power is the force an electromagnet exerts to hold an object in place. It is crucial in determining whether the electromagnet will effectively lift and transport materials.
- How It’s Calculated: Holding power depends on the size of the electromagnet, the electrical current, and the core material used. A higher current or stronger core material will generally result in greater holding power.
- Choosing the Right Strength: Select an electromagnet with holding power suited to your task. If the force is too weak, the load may not stay in place, while excessive force can make lifting and handling more difficult.
Having the correct holding power ensures both performance and safety during material handling.
Voltage and Power Requirements
The voltage and power supplied to the electromagnet directly affect its performance and efficiency.
- Voltage Considerations: The electromagnet must match the available electrical supply in your facility. A mismatch can lead to inefficiency or damage.
- Power Consumption: Higher power demands typically result in stronger magnetic fields but can also increase energy consumption. Balancing power requirements with your existing electrical systems is crucial for optimal performance.
Ensure that the electromagnet’s voltage and power align with your system to avoid issues with operation and energy costs.
Duty Cycle
The duty cycle refers to the amount of time an electromagnet can operate continuously before needing to cool down.
- Explanation: A higher duty cycle means the electromagnet can operate for longer periods without overheating. For example, a 100% duty cycle allows continuous operation, while a 50% duty cycle requires breaks to cool down.
- Choosing the Right Duty Cycle: If your application involves continuous lifting, select an electromagnet with a higher duty cycle. If your tasks are intermittent, a lower duty cycle may be adequate.
Size and Weight
The size and weight of an electromagnet impact how it integrates with your equipment and the space it occupies.
- Installation Considerations: Larger electromagnets may be necessary for handling heavier loads, but they could also require more space and special mounting arrangements.
- Compatibility: Ensure the electromagnet is compatible with your existing machinery and can be easily installed in the available space.
Choosing the right size and weight is crucial for smooth installation and efficient operation.
Environmental Conditions
Electromagnets can be affected by environmental factors like temperature, humidity, and exposure to corrosive materials.
- Harsh Environments: Electromagnets used in extreme conditions, such as high temperatures or corrosive environments, need additional protection.
- Protective Features: Look for electromagnets with protective coatings or designs suited for high humidity, extreme temperatures, or exposure to chemicals.
Selecting an electromagnet designed for your specific environment ensures long-term reliability and durability.
Control Systems
Electromagnets come with a variety of control systems, including manual, automatic, and remote-controlled options.
- Manual Control: Basic systems that require an operator to turn the electromagnet on and off manually.
- Automatic Control: These systems automatically activate or deactivate the electromagnet based on preset conditions, improving efficiency.
- Remote Control: Allows operators to control the electromagnet from a distance, enhancing safety by reducing direct exposure to the lifting area.
Choosing the right control system improves both operational efficiency and worker safety. Automated or remote-controlled systems can streamline operations and reduce human error.
Material and Design Considerations
Material of the Core
The core material plays a significant role in the performance and efficiency of an electromagnet. The core is typically made from ferromagnetic materials such as steel or iron, which help concentrate and strengthen the magnetic field.
- Impact on Efficiency and Strength: Materials like iron have high magnetic permeability, which means they allow the magnetic field to pass through easily, creating a stronger force. Steel, on the other hand, is often used in heavy-duty applications due to its durability and strength.
- Selecting the Right Core Material: When choosing the right core material, consider both the strength of the material and its durability. For heavy-duty lifting tasks, steel may be the best choice due to its ability to withstand high stress and resist wear over time. For lighter applications, iron or a similar material may provide sufficient strength at a lower cost.
Choosing the proper core material ensures that the electromagnet can efficiently handle the required load without compromising on performance or longevity.
Coil Insulation and Construction
The coil is one of the most critical components of an electromagnet. Insulating the coil properly and ensuring its construction is designed for durability are key to avoiding damage and extending the electromagnet's lifespan.
- Importance of Coil Insulation: Coil insulation prevents the coil from overheating by providing an insulating barrier that protects the wire from heat buildup. Overheating can lead to reduced efficiency, damage to the coil, or even failure of the electromagnet.
- Design Considerations: Effective heat dissipation is essential for the electromagnet's performance, especially during continuous or high-duty-cycle operation. Look for electromagnets with high-quality insulation materials and efficient construction to ensure that the coil can handle prolonged use without overheating.
Coil insulation and efficient construction are necessary to maintain the electromagnet’s performance and ensure long-term reliability.
Safety Features
Electromagnets are powerful tools, and like all industrial equipment, they require built-in safety features to protect both the equipment and the workers handling it.
- Overload Protection: Overload protection prevents the electromagnet from being used beyond its maximum capacity. This feature helps avoid damage to the electromagnet and ensures safe operation by automatically disconnecting the power if the load exceeds the safe operating limit.
- Thermal Protection: Thermal protection sensors monitor the temperature of the electromagnet’s coil and activate cooling mechanisms or shut down the electromagnet if it reaches unsafe temperatures. This feature prevents overheating and reduces the risk of damage or fire.
- Other Safety Features: Many electromagnets come with additional safety features such as short-circuit protection, emergency stop buttons, and integrated alarms to alert operators if something goes wrong during operation.
Ensuring that the electromagnet includes these safety features will help meet industrial safety standards and provide a safer working environment for operators.
In summary, paying close attention to the core material, coil insulation, and safety features is crucial for ensuring that the electromagnet operates efficiently, lasts longer, and meets all safety requirements. Proper selection of these components will lead to improved performance, reduced maintenance costs, and safer operation
Cost vs. Quality: Making the Right Trade-Off
Factors Affecting the Cost of Electromagnets
The cost of an electromagnet can vary significantly depending on several key factors:
- Material Quality: High-quality materials, such as premium steel or specially designed alloys for the core and coil, can increase the initial cost. However, these materials offer better durability and performance over time, reducing the risk of premature failure and lowering replacement costs.
- Size: Larger electromagnets that can handle heavier loads generally cost more due to the increased materials and power required to operate them.
- Power Requirements: Electromagnets with higher voltage and power requirements tend to be more expensive. The stronger the magnetic field needed, the more energy is required to create and sustain it.
- Customization Options: Custom designs, such as electromagnets tailored to specific industrial needs or environments, can drive up costs. This may include modifications for extreme temperatures, corrosive conditions, or unusual lifting capacities.
- Advanced Features: Electromagnets with additional features like automated control systems, remote operation, or built-in safety mechanisms will cost more but offer added value in terms of performance, safety, and ease of use.
When evaluating electromagnets, consider what aspects are non-negotiable for your operation and what features can be scaled back to reduce costs without compromising performance.
Balancing Cost with Efficiency
While it may be tempting to choose a lower-cost electromagnet, it’s important to weigh cost against long-term benefits:
- Energy Efficiency: More energy-efficient electromagnets may cost more upfront but can lead to significant long-term savings in power consumption. Consider the electromagnet's efficiency in converting electrical energy into magnetic force and how this will affect your operating costs over time.
- Durability: Electromagnets made from high-quality materials or with superior design tend to last longer, meaning you may spend less on repairs, replacements, and downtime. A more expensive, durable electromagnet could provide better value in the long run.
- Maintenance Costs: Consider the cost of maintaining the electromagnet over its lifespan. Higher-quality models might require fewer repairs, reducing maintenance expenses and unplanned downtime. In contrast, cheaper models may need more frequent servicing, increasing operational costs.
- Lifespan: The longer the electromagnet lasts, the better the value it offers. Investing in a more durable electromagnet may initially strain your budget, but it could ultimately save money over its longer operational life.
Balancing upfront costs with these efficiency and durability considerations ensures that you’re making a wise investment that delivers long-term savings and value.
Budgeting for Your Electromagnet
Setting a budget for your electromagnet purchase involves carefully evaluating both your needs and the features you require:
- Assess Your Needs: Start by identifying your primary requirements—what kind of loads do you need to lift? What environmental conditions will the electromagnet be exposed to? How frequently will it be used? Knowing your exact requirements will help you avoid overspending on features you don’t need.
- Prioritize Essential Features: Focus on the most critical aspects, such as load capacity, holding power, and durability, which directly impact performance. If budget constraints are an issue, consider which advanced features are less essential for your specific application.
- Get Quotes and Compare: Reach out to suppliers for quotes and compare prices, but also consider the long-term cost of ownership, which includes maintenance, energy consumption, and potential downtime.
- Consider Total Cost of Ownership: Remember that the cheapest option isn’t always the most cost-effective in the long run. Weigh the upfront cost against the total cost of ownership, which includes initial purchase, operation, and maintenance costs.
By carefully assessing your needs and aligning them with your budget, you can find an electromagnet that offers the best balance of cost and quality, ensuring that your purchase provides both short-term affordability and long-term value.
In conclusion, when purchasing an electromagnet, it's important to focus on factors such as material quality, size, power requirements, and customization options, all while keeping a close eye on energy efficiency, durability, and long-term costs. Striking the right balance between cost and quality ensures that you make an informed decision that meets your operational needs without overspending.
Material and Design Considerations
Material of the Core
The core material plays a crucial role in determining the efficiency and strength of an electromagnet.
- Impact of Core Material: Electromagnets typically use ferromagnetic materials like steel or iron for the core, as these materials concentrate and strengthen the magnetic field. The choice of core material affects both the magnetic strength and energy efficiency of the electromagnet. Steel cores, for example, tend to offer better magnetic properties and strength compared to iron, making them ideal for heavy-duty applications.
- Selecting the Right Core Material: When choosing the core material, consider the durability and performance required for your application. If the electromagnet will be used in harsh environments (e.g., extreme temperatures or corrosive areas), selecting a core material resistant to wear and degradation will ensure long-term reliability and performance. Materials like laminated steel or silicon steel are often used for their high magnetic permeability and durability.
Choosing the right core material ensures that the electromagnet performs effectively while minimizing energy waste and maximizing its lifespan.
Coil Insulation and Construction
The coil is one of the most critical components of an electromagnet. Its insulation and construction significantly impact performance and durability.
- Importance of Coil Insulation: Proper coil insulation is essential for preventing overheating and ensuring the electromagnet’s longevity. When an electromagnet operates, it generates heat, and poor insulation can lead to short circuits or failure. Insulation materials such as varnish, epoxy, or enamel are commonly used to protect the coil and maintain its electrical integrity under heavy use.
- Design Considerations for Heat Dissipation: The coil design should also prioritize heat dissipation. An electromagnet with an optimized coil structure will dissipate heat more effectively, reducing the risk of overheating. Adequate spacing between coil windings and the use of materials with high thermal conductivity, such as copper, can improve the cooling process and enhance overall efficiency.
A well-insulated and well-constructed coil improves performance, reduces the need for frequent maintenance, and extends the electromagnet's operational life.
Safety Features
Safety is a critical concern when selecting an electromagnet for industrial use. Incorporating safety features ensures that the electromagnet operates reliably while protecting both the equipment and workers.
- Overload Protection: Overloading an electromagnet can lead to overheating or damage to the internal components. Overload protection mechanisms, such as thermal cutoffs or current limiters, automatically disengage the electromagnet if it exceeds a safe operating limit.
- Thermal Protection: Thermal protection features, such as built-in thermal switches, help prevent the electromagnet from reaching unsafe temperatures. These devices shut down the electromagnet when the internal temperature becomes too high, preventing damage and ensuring worker safety.
- Other Safety Features: Other common safety features include automatic shutdown in case of power failure, manual override for emergency situations, and warning lights or alarms that notify operators when the electromagnet is under stress.
Ensuring that the electromagnet has these built-in safety features helps comply with industrial safety standards and protects workers from potential hazards.
When choosing an electromagnet, the materials used for the core, the coil’s insulation and construction, and the safety features incorporated into the design all contribute to the electromagnet's performance, durability, and safety. By prioritizing these factors, you can select a high-quality electromagnet that operates efficiently and safely in your industrial applications.
Case Studies and Real-World Applications
Examples of Successful Electromagnet Use
Electromagnets have been successfully implemented across various industries, with businesses benefiting from their efficiency, strength, and safety. Here are some examples:
- Manufacturing and Material Handling: A steel manufacturer installed a high-load electromagnet to handle large steel beams during production. The company chose an electromagnet with a strong core material (steel) and a high holding power to ensure safe and efficient material handling. This improved their production speed and minimized worker injuries related to manual handling.
Key Benefits: Increased efficiency, reduced manual labor, and improved safety on the production floor. - Automotive Industry: An automotive parts supplier implemented an electromagnet for part handling on an assembly line. By selecting a magnet with the right voltage and power requirements, they ensured smooth and reliable operation. The electromagnet’s automatic control system also enabled precision handling, reducing part misplacement and boosting assembly line speed.
Key Benefits: Enhanced operational efficiency, reduced errors, and streamlined production flow. - Construction and Demolition: In the construction industry, a demolition company used a powerful electromagnet to lift and move heavy scrap metal from site to recycling facilities. The electromagnet’s design incorporated thermal protection, allowing for extended use without overheating in high-demand conditions.
Key Benefits: Safe handling of heavy materials, reduced downtime due to overheating, and enhanced scrap metal recovery.
These case studies highlight the effectiveness of well-chosen electromagnets in increasing operational efficiency, safety, and overall productivity.
Lessons Learned from Incorrect Electromagnet Choices
While electromagnets provide significant benefits, poor selection can lead to costly mistakes. Below are some examples of the consequences when businesses did not choose the right electromagnet for their needs:
- Overloading and Equipment Damage: A warehouse used an electromagnet with insufficient load capacity to handle heavy metal parts. The result was frequent breakdowns and eventual damage to the electromagnet, leading to high repair costs and downtime.
Lesson Learned: Always ensure that the electromagnet’s load capacity matches the weight and size of the materials being lifted. - Inefficient Power Consumption: A recycling plant selected an electromagnet that was underpowered for its high-load tasks. Although the magnet could lift the materials, it consumed far more energy than necessary, leading to higher operational costs.
Lesson Learned: Matching the electromagnet’s power requirements to the facility’s electrical system is essential to prevent wasted energy and reduce costs. - Safety Incidents Due to Lack of Protection: A construction company faced safety issues when the electromagnet they used lacked proper thermal protection. Over time, the electromagnet overheated, causing it to malfunction and resulting in a near-miss accident.
Lesson Learned: Ensure that electromagnets have built-in thermal protection and overload protection to maintain safety and prevent equipment failure.
These examples underline the importance of selecting the right electromagnet based on specific operational needs, as poor choices can lead to higher costs, inefficiencies, and safety hazards.
Customer Testimonials
Insights from businesses that have successfully implemented electromagnets show the significant impact these tools can have on operations.
- Automotive Parts Supplier: "We recently upgraded to a new electromagnet with a higher holding power and automatic controls for our assembly line. The difference has been remarkable. Our line runs smoother, there’s less risk of parts being misaligned, and we’ve seen a noticeable increase in production speed. The electromagnet was an investment, but it’s paid off in improved efficiency and fewer mistakes." – Operations Manager, Automotive Supplier.
- Steel Manufacturer: "Choosing the right electromagnet for lifting steel beams made a huge difference in our factory. The new magnet handles the weight without issue, and we no longer face the safety risks we had before. The reduced downtime from maintenance and breakdowns alone has made it a worthwhile purchase." – Production Supervisor, Steel Manufacturing Plant.
- Demolition Company: "In demolition, you never know what kind of materials you’ll be lifting, and things can get heavy quickly. Our electromagnet is built to withstand the conditions, and the added thermal protection has been essential. It’s one of the best investments we’ve made for our heavy equipment." – Field Manager, Demolition Company.
These testimonials reflect how careful selection of electromagnets can lead to significant improvements in operational efficiency, safety, and productivity. Customers across industries have found that investing in the right electromagnet yields long-term benefits, from reducing operational costs to improving safety and efficiency.
By studying real-world examples and customer experiences, businesses can gain valuable insights into the importance of selecting the right electromagnet for their needs. Whether it’s to handle heavy materials, ensure safety, or improve overall performance, a well-chosen electromagnet can make a significant difference in industrial operations.
Conclusion
Summary of Key Considerations
Selecting the right electromagnet involves considering several critical factors that influence its performance, efficiency, and longevity. These include:
- Load Capacity: Ensuring the electromagnet can safely handle the weight and size of the materials you plan to move.
- Electromagnetic Force (Holding Power): Choosing an electromagnet with the appropriate strength to lift and hold materials securely.
- Voltage and Power Requirements: Matching the electromagnet’s power needs with your available electrical systems.
- Duty Cycle: Understanding how long the electromagnet can operate continuously before needing to cool down.
- Size and Weight: Ensuring the electromagnet fits within your space and integrates well with existing equipment.
- Environmental Conditions: Selecting an electromagnet designed to withstand temperature extremes, humidity, and corrosive environments.
- Safety Features: Prioritizing features like overload protection, thermal cutoffs, and automatic shutdown systems to ensure safe operation.
Each of these considerations plays a vital role in ensuring that the electromagnet will perform effectively and safely in your specific application.
Final Tips for Making the Right Choice
Making the right choice when purchasing an electromagnet requires a balanced evaluation of performance, cost, and longevity. Here are some tips for evaluating your options:
- Understand Your Needs: Clearly define the tasks you want the electromagnet to perform. Consider the materials you will lift, the operating environment, and the expected workload.
- Compare Specifications: Look at the load capacity, holding power, and duty cycle of various electromagnets. Compare them with your operational requirements to ensure you choose one that aligns with your goals.
- Balance Cost and Longevity: While it might be tempting to opt for a lower-cost option, ensure it meets your needs for durability and long-term performance. A more expensive electromagnet might save you money in the long run by reducing maintenance costs and improving efficiency.
- Consult with Suppliers: Speak with electromagnet suppliers to get expert advice on the best solutions for your specific use case. Suppliers can help clarify technical details and offer recommendations based on their experience.
Now that you’ve gained an understanding of the essential factors in choosing an electromagnet, take the next step to optimize your operations. Assess your specific needs, considering the materials you handle, your operational environment, and your safety requirements. Consult with trusted suppliers who can guide you toward the best electromagnet for your application. By selecting the right electromagnet, you can enhance efficiency, reduce costs, and ensure safety in your workplace.
FAQs (Frequently Asked Questions)
What is the difference between a permanent magnet and an electromagnet?
- Permanent Magnet: A permanent magnet is a material that produces a magnetic field without the need for electrical power. It retains its magnetism over time and is generally used for applications where a constant magnetic field is required.
- Electromagnet: An electromagnet, on the other hand, is a temporary magnet that requires an electrical current to generate a magnetic field. When the current is turned off, the magnetic field disappears. Electromagnets are typically used in applications that require adjustable or temporary magnetic force, such as lifting and handling materials in industrial settings.
How can I tell if my electromagnet is powerful enough for the job?
To ensure that your electromagnet is powerful enough for the job, you need to evaluate the load capacity and holding power. Consider the following:
- Load Capacity: Ensure the electromagnet can handle the weight of the materials you intend to lift or move.
- Holding Power: Check the electromagnetic force (measured in gauss or tesla) to verify that the electromagnet can securely hold the material in place.
- Safety Margin: It’s also a good practice to choose an electromagnet with a slightly higher capacity than required to account for factors such as material composition or environmental conditions.
Can I use an electromagnet in extreme environmental conditions?
Yes, but you must ensure the electromagnet is designed for such conditions. Here are some considerations:
- High Temperatures: Look for electromagnets with thermal protection or made with materials that can withstand high temperatures without losing magnetic strength.
- Corrosive Environments: Electromagnets used in chemical or marine environments should be equipped with anti-corrosion coatings and made from materials resistant to rust and degradation.
- Humidity: Choose electromagnets with sealed coils and insulation designed to protect against moisture, preventing short circuits and operational failures.
What are the common problems that electromagnets face during operation?
Several issues can arise during the operation of electromagnets:
- Overheating: Prolonged use without sufficient cooling can cause the electromagnet to overheat, potentially damaging the coil or internal components.
- Power Failures: Inconsistent or insufficient power supply can lead to reduced holding power or complete failure to activate the electromagnet.
- Wear and Tear on Components: Over time, the coil insulation can degrade, causing electrical shorts or failures in the electromagnet's performance.
- Magnetic Field Degradation: If the electromagnet is not properly maintained, it may lose its magnetic strength, particularly in harsh environments or with poor-quality materials.
How do I maintain my electromagnet for maximum efficiency?
Proper maintenance is essential to ensure the electromagnet operates at its best:
- Regular Inspections: Periodically check the coil insulation, core, and wiring for signs of wear or damage. Look for signs of overheating or burn marks.
- Clean the Magnet: Dust and debris can affect performance. Regularly clean the electromagnet to remove contaminants that may interfere with the magnetic field.
- Check Power Supply: Ensure that the electromagnet is connected to a stable power supply, and monitor for fluctuations or issues that might affect performance.
- Lubrication and Cooling: For electromagnets with moving parts, ensure proper lubrication. If your electromagnet operates in a high-demand environment, make sure it has sufficient cooling to prevent overheating.
- Follow Manufacturer’s Guidelines: Always follow the manufacturer’s maintenance schedule and instructions for inspections, repairs, and replacement of worn components.